Understanding the risks of tool wear and how to improve tool life are essential for sustainability and profitability. In fact, the way a cutting tool edge interacts with the workpiece is directly connected to overall profitability. While a well-maintained tool can boost performance, tool life deterioration and/or tool failure on the shop floor can adversely impact business in a variety of ways. Understanding why tool failure occurs, as well as the related risks and how to avoid them, allows shops to optimize production time and improve operations.
Wear-related and non-wear-related tool failure represent two distinct issues that can affect the performance and lifespan of tools.
Wear-related tool failure occurs when tools gradually deteriorate over time due to repetitive use and frictional forces. Cutting edges may wear down or become dull after prolonged use, leading to decreased cutting efficiency and precision. Wear-related failure is a natural consequence of tool usage and can be mitigated through training, proper maintenance, lubrication, and periodic replacement.
Non-wear-related tool failure occurs when tools break or malfunction due to factors unrelated to normal use, which can result from inadequate material strength or exposure to excessive forces or temperatures beyond tool tolerance. Non-wear-related failures often happen suddenly and unexpectedly, resulting in tool breakage, fracture, or complete loss of functionality.
- Quality Issues – Tool failure can result in poor precision, incorrect dimensions, surface defects, or other quality-related problems in the produced parts. Inconsistent parts may not meet customer specifications. Damaged parts often require additional rework or correction, ultimately contributing to an increase in scrap.
- Downtime – Tool failure often leads to unplanned downtime, which adds time and cost to a project. Production disruptions can also result in inconsistent or incomplete parts, as well as inconsistencies in material feed or other parameters. The same inconsistencies can lead to defective parts, which are likely to be scrapped, resulting in longer lead times.
- Rework and scrap material – When a tool fails during a production run, it may damage the workpiece or material being processed. This can result in complete rejection of the affected parts, also leading to an increase in scrap. Additionally, any rework or corrective measures required to salvage defective parts will also contribute to scrap generation and increased energy consumption.
- Resource waste – Tool failure not only leads to the generation of scrap parts but also wastes other resources such as raw materials, energy, and labor. Worn or improperly maintained tools tend to generate additional friction, requiring higher energy input to achieve desired results. Inefficient tools can cause excessive heat, vibration, and resistance during operation, leading to increased energy consumption.
- Excess inventory – When tool failure causes downtime, it can also create a buildup of unfinished goods or work-in-progress inventory, which ties up working capital and increases costs.
Put these tips to work for your shop today:
- Use the right tool
Using the right tool for your application reduces wear, avoids scrap and gets results. For any application, consider tool length, carbide grade, cutting geometry, rake face and coating. If you know your application but are looking for the right tool, use the online service Suggest. - Use proper cutting parameters
The correct cutting depth, spindle speed, feed rate and machining method (ratio time in cut/time out of cut) must be aligned to avoid waste and wear. Start with the safe cutting data provided with each tool and then finetune the parameters. - Use high-quality tools
High-quality, high-performance tools last longer for increased productivity and provide more accuracy and better surface finishes. - Maintain tools properly
Improper storage can damage cutting edges. Tools should be stored in a clean, organized manner. To learn more, see Seco Tools’ Preventive Tool Maintenance document. - Monitor tool wear
Noticing and tracking tool wear patterns establishes baselines and average expected tool lives for given applications. Changes in noise level, surface roughness, excessive vibration/chatter and increased power consumption are also tool wear indicators. - Implement an inventory management system
Inventory management systems track tool location, usage and availability. In addition to ensuring the right tool is available for an application, shop managers can monitor usage and consumption for preventive maintenance to avoid failures. - Train your employees
Tools, systems and processes are only as good as the people using them. Workforce training is essential for tool life optimization. Knowing how to identify and address wear patterns requires experience and proper training.
As mentioned in tip #7, workforce education plays a vital role in identifying and addressing tool wear. Fortunately, employee training resources are expanding and becoming easier to access. Seco maintains an extensive catalogue of online courses, including a comprehensive overview of tool deterioration and wear for shop owners and operators that helps shops interpret their tool wear history.
To help shops diagnose tool wear issues, the Tool Optimization feature of the Seco Assistant app provides a fast, easy source of information. The app allows users to troubleshoot the various causes of tool wear and eliminate them before they cause issues.
Most importantly:
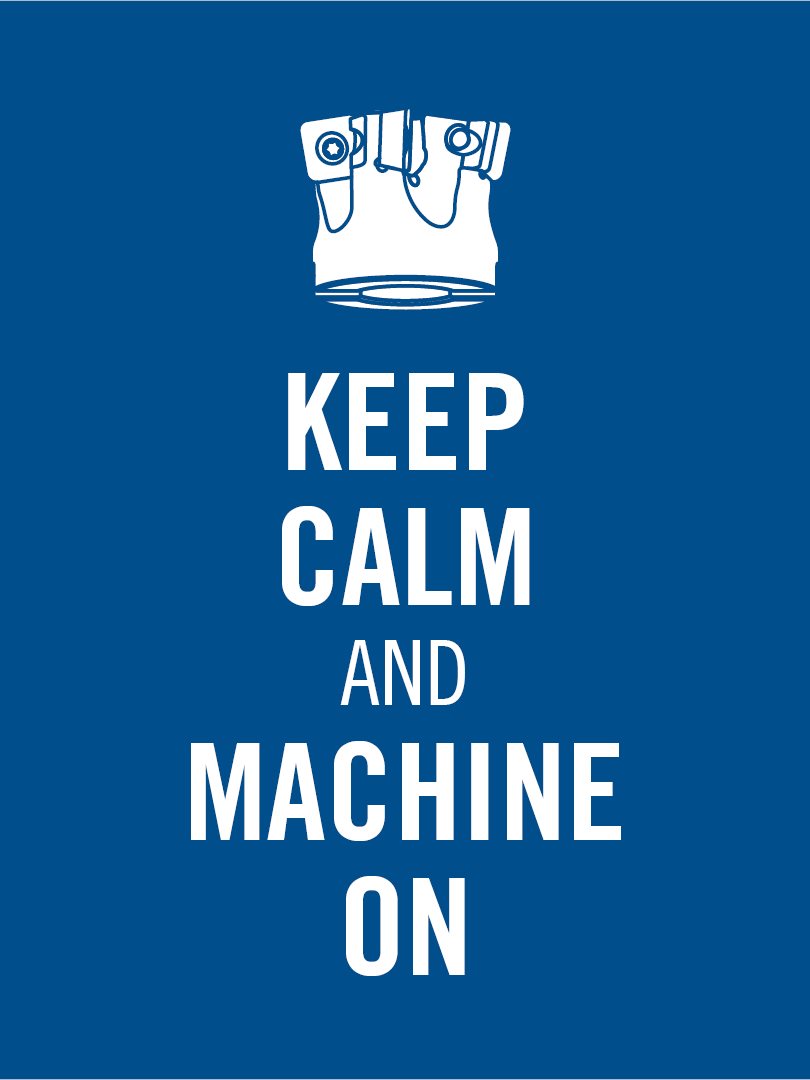