Seco Tools AOB - Dur comme du diamant
A Mortagne-sur-Sèvre, Seco-AOB est un centre de compétences et une unité de production pour la conception et la fabrication d’outils PCD. Des produits qui permettent d’augmenter la productivité dans l’usinage de tous les matériaux composites.Retrouvez cet article sur le n°1081 de MACHINES PRODUCTION
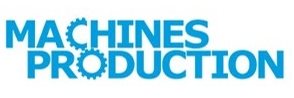
Le groupe Seco Tools est une entreprise internationale, originaire de Fagersta, en Suède, où se trouve encore aujourd’hui son siège social. En France, ce groupe compte quatre sites : Seco Tools Tooling Systems dans l’est de la France pour la fabrication de systèmes d’attachement, un site en Isère, Seco Reaming, qui fabrique des alésoirs, Seco-AOB, à Mortagne-sur-Sèvre, spécialisée dans la production d’outils PCD (où nous nous sommes rendus) et Seco Tools, à Bourges (Cher), siège social France et site de production de fraises à plaquettes. Ce centre technologique intègre également le service de recherche et de développement, la direction de Seco Tools France, et l’ensemble des services supports pour le marché français. Nolwenn Nivet, la directrice de
Seco-AOB, présente le site de Mortagne-sur-Sèvre (Vendée) : « Notre entité, ici en Vendée, compte une quarantaine de personnes. Notre raison d’être réside dans l’expertise de l’usinage de matériaux non ferreux, tels que les composites et l’aluminium fortement silicé, avec des outils en polycristallin diamant PCD. Nous nous positionnons en tant que support technique auprès de nos clients pour développer et améliorer leurs procédés d’usinage. On va répondre à une demande spécifique et relever le challenge du client, ce qui nous fait évoluer et avancer. » Le site de Mortagne-sur-Sèvre est un centre de compétences et une unité de production d’outils PCD brasés utilisés pour l’usinage de matériaux composites et métaux non ferreux. Seco-AOB apporte au groupe des solutions et un savoir-faire complémentaires aux autres sites Seco.
Applications
Des composites en bois sont beaucoup utilisés pour l’agencement de cuisines et l’ameublement en général ; d’autres composites en fibre de carbone sont destinés, par exemple, à l’industrie aéronautique et les éoliennes ; la fibre de verre est utilisée notamment dans la fabrication de bateaux. Enfin, on trouve de nombreux cas d’applications du PCD dans d’autres matériaux non ferreux, tels que l’aluminium silicé. Les champs d’applications sont extrêmement vastes donc nombreux. Seco-AOB conçoit et produit des solutions sur mesure, représentant 95 % de son chiffre d’affaires. Nolwenn Nivet poursuit : « Notre souhait est de résoudre une problématique client, peu importe son domaine d’activité. Néanmoins, nous nous orientons de plus en plus
dans l’aéronautique où les potentiels en composite et en aluminium sont de plus en plus importants. Ce marché est très porteur et en plein développement. Notre part de marché est encore
relativement faible et les opportunités d’amélioration dans l’usinage de ces matériaux sont nombreuses (qualité, temps de cycle, durée de vie). »
L’histoire d’AOB
L’entreprise AOB, fondée en 1982, s’est implantée en Vendée, en raison de la forte représentation de l’industrie du bois. Son fondateur, Alain Le Bris, a commencé son activité de reconditionnement d’outils à plaquettes carbure. Puis, en suivant la demande de ses clients qui utilisaient de plus en plus de matériaux composites, mélaminés, agglomérés, qui sont plus abrasifs – il est arrivé à la limite de l’utilisation du carbure dans ces matériaux. Pour améliorer la qualité de coupe, l’état de surface, et pour résoudre certains problèmes, tels que les bavures, il a fallu rechercher une matière plus résistante : le polycristallin diamant (PCD) répondait parfaitement à ces problématiques, avec un pouvoir de coupe supérieur, un plus faible facteur d’usure, et offrait donc une meilleure durée de vie. Ceci a permis à AOB de s’orienter vers les marchés de l’automobile et aéronautique. En l’an 2010, l’ancien dirigeant Alain Le Bris a souhaité arrêter son activité, tandis que le groupe Seco recherchait des compétences dans l’usinage de matériaux composites. C’est à partir de ce moment que AOB a intégré le groupe Seco.
Nolwenn Nivet explique ce choix : « On s’appuie sur notre compétence et notre savoir-faire qui s’est développé au fil de notre histoire et de nos expériences clients. Nous avons 35 ans d’expérience et nous avons su nous adapter et évoluer en même temps que la demande de nos clients. Nous avons constamment investi dans des nouvelles technologies et des machines de plus en plus performantes avec de plus en plus d’autonomie, en érosion en particulier, pour l’affûtage des outils mais aussi pour la découpe des plaquettes, en taillage des corps en carbure et en fraisage des corps acier, qui sont des machines avec chargeurs automatisés qui tournent 24 heures sur 24, 7 jours sur 7. »
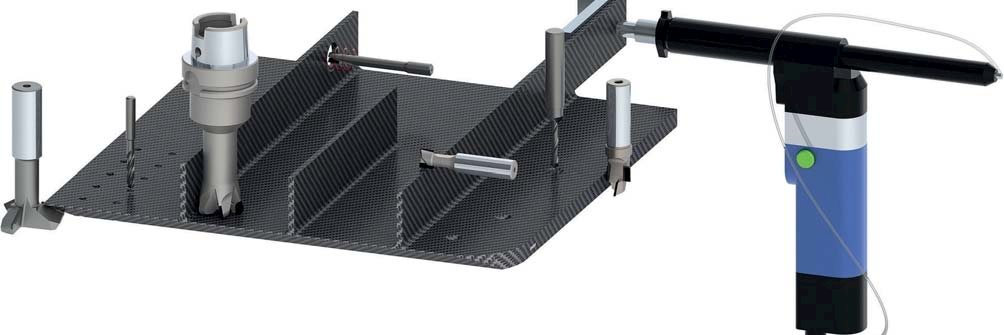
Des marchés en pleine mutation
Aujourd’hui, Seco-AOB travaille principalement sur trois secteurs d’activité : l’automobile, l’aéronautique et l’ameublement composite. Pour ces trois activités, cette société propose des solutions en fraisage, perçage et alésage. Le marché français représente 60 % de leur chiffre d’affaires et 70 % en Europe. Elle a deux marchés en forte croissance depuis 3 ans : le marché américain et asiatique. Outre la fabrication de ces outils performants, Seco-AOB a également une forte activité dans le domaine de la réparation des outils, qui représente 35 % du chiffre d’affaires. Nolwenn Nivet poursuit : « Quand nous recevons les outils de la part de nos clients, nous procédons à une expertise complète et en fonction de l’usure on va définir les différentes opérations à prévoir pour remettre le produit à neuf. Cela va du simple retaillage des dents par érosion ou un reconditionnement complet de l’outil. Dans ce cas-là, on va débraser les plaquettes et rebraser une plaquette neuve. Ainsi, le client reçoit un outil pratiquement neuf. » Un grand nombre d’opérations est nécessaire pour fabriquer de tels outils : l’usinage acier (débit/tournage, fraisage) pour la fabrication du corps de l’outil, ou le débit et taillage du corps carbure, la découpe des plaquettes PCD, l’assemblage du corps et des plaquettes en brasage avec deux types d’opération : brasage par induction ou brasage par chalumeau. Ensuite, vient le nettoyage de l’outil, sablage et brunissage. Par la suite, les produits vont en érosion où se définit la géométrie de l’outil conformément au besoin du client final. La finition au micron près se fait ensuite par meulage. Pour un outil plus complexe, par exemple un alésoir pour l’industrie automobile, on peut atteindre plus de vingt opérations différentes. Tous les corps de métiers sont réunis sur place, permettant ainsi un haut degré de réactivité.
Frédéric Auvinet, responsable produits PCD, intervient : « Si nous n’avons que peu de produits standard, c’est parce que nous recherchons toujours la solution la plus adéquate par rapport à une application donnée en tenant compte de la durée de vie et de la qualité du produits recherchées. La solution que nous proposons est issue d’un développement d’un produit standard. Le produit final en PCD a une durée de vie nettement plus élevée que les produits en carbure (deux à dix fois plus longue). Il est certain qu’un produit en PCD est plus cher à l’achat, mais il s’usera moins vite et il peut être reconditionné plusieurs fois, ce qui représente une solution intéressante du point de vue économique. »
Nolwenn Nivet conclut : « L’utilisation de ces produits PCD est également intéressante par rapport à la productivité du client, parce que le PCD permet de rentrer beaucoup plus vite dans la matière, ce qui permet à l’utilisateur de gagner en temps machine, en adaptant sa méthodologie de programmation et ses paramètres machine. »