Machining Science & Tool Technology = Maximum Output
New developments in machining technology can provide maximum economic benefits if the machining process is described as one consistent model. It is of vital importance to compare different possible technological scenarios in the light of overall or global production economics.Fagersta, March 2022 — New developments in machining technology can provide maximum economic benefits if the machining process is described as one consistent model. It is of vital importance to compare different possible technological scenarios in the light of overall or global production economics. A pragmatic definition of global production economics is: “Assuring maximum security in, and predictability of, the machining process, while maintaining highest productivity and lowest production costs.” Before performing detailed 1:1 optimisation of individual operations, the productivity and cost efficiency picture of the process overall must be balanced and optimised on a macro basis. Once this step is taken, further improvements can be achieved by careful investigation into situations where a 1:1 optimisation can be beneficial.
The traditional approach to achieving maximum machining results involves a narrow-perspective micro model based on 1:1 optimisation of one tool in one operation. Macro models, on the other hand, consider manufacturing from a broader perspective. With these macro or global models, the total time required to produce a given workpiece plays a more decided role.
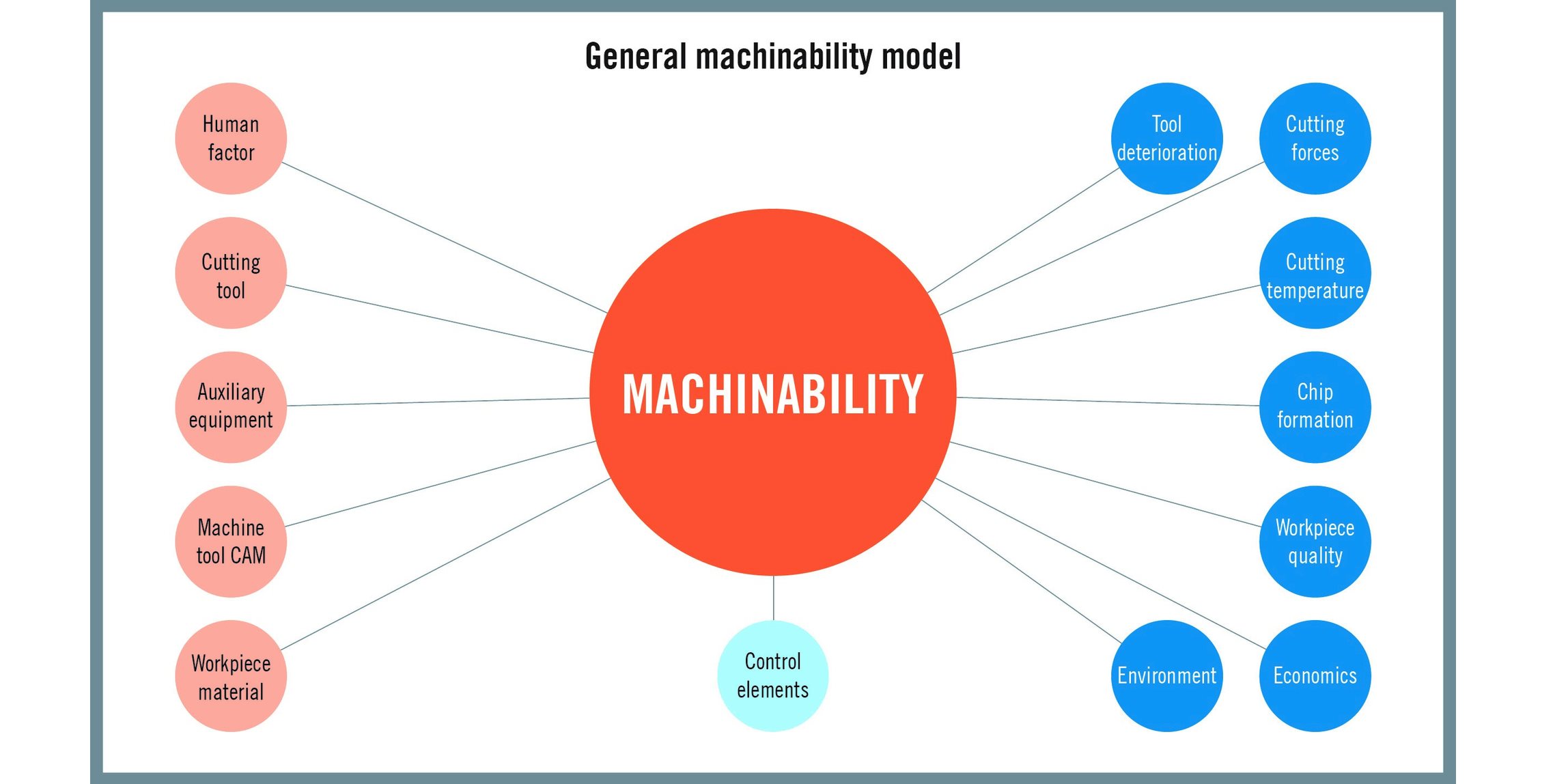
A simplified example of global optimisation involves two machines employed in series to produce a component. There is no use in optimising cutting times and boosting output on machine tool “A” if similar improvements are not possible on machine tool “B.” The increased output would only produce extra costs in semi-finished workpiece inventory waiting to be processed on the second machine. Much better in this example would be to optimise cutting costs on machine tool A. Doing so might limit productivity on machine tool A, but it would reduce overall costs while maintaining output.
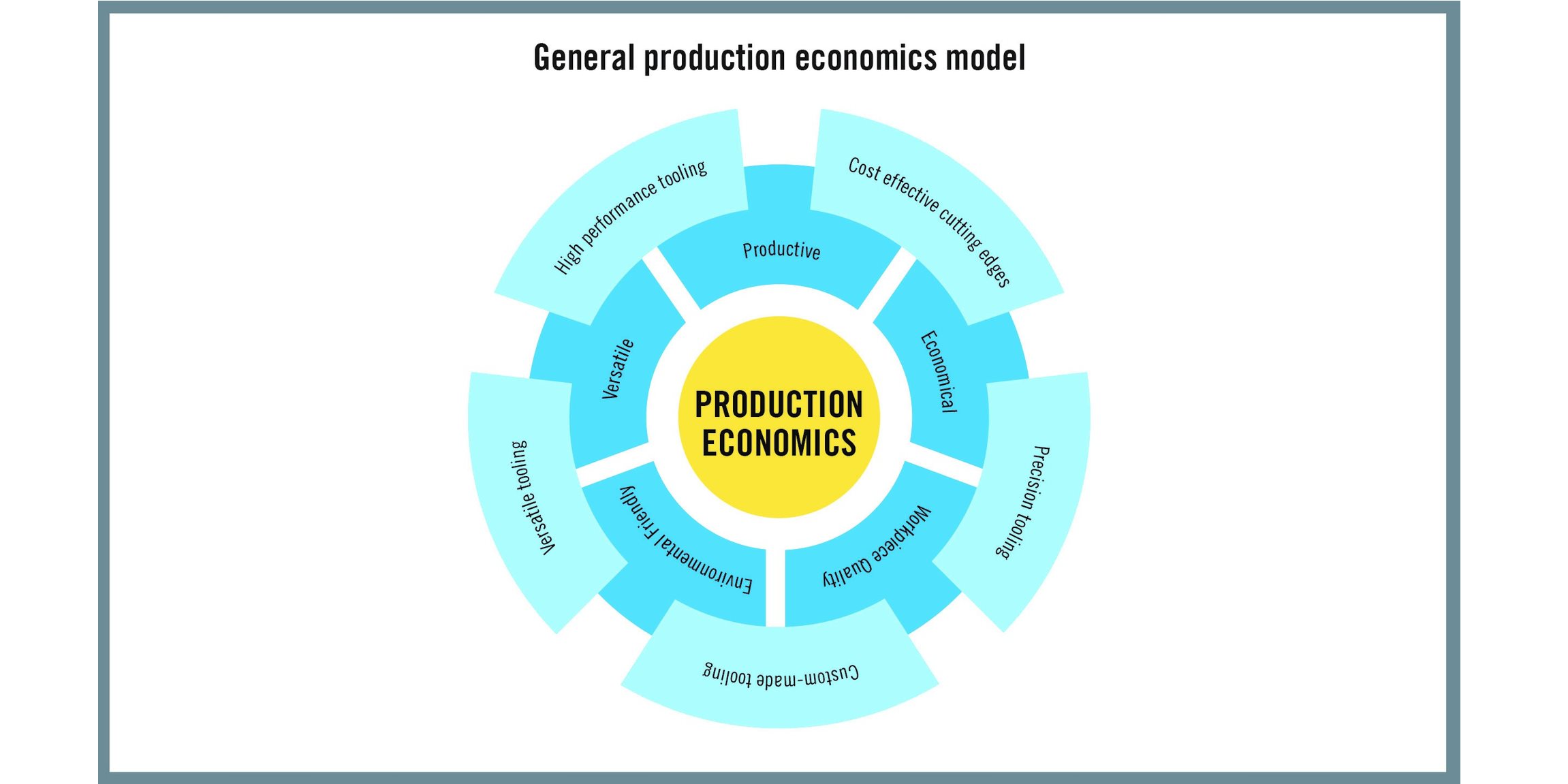
On the other hand, in a situation where machine tool B stands idle waiting to process parts produced by machine tool A, increasing the output of machine A will boost total output. Much depends on how the shop organises its production operations: whether it is a line, batch or parallel organisation. There is no single truth, but these examples indicate the need for a broader view and illustrate that micro model optimisation needs to be carried out very carefully.
The requirement to take a broader view can apply to machine tools themselves. A typical situation could involve a shop running a milling machine fully loaded 40 hours a week and deciding to replace it with a high-speed machine. When the new machine is up and running, however, it spends half the time standing idle. Then the shop faces the challenge and expense of finding more work to keep the new machine busy and justify the investment in it. The better path would have been to first examine the bigger picture and anticipate what would result from the new machine’s greater output.
A 1:1 optimisation focuses on one application and one cutting tool and is intended to create high metal removal rates at the lowest cost possible. The process involves selecting tooling best suited to machine the part and employing the largest depth of cut and highest feed rate possible. Of course, maximum depths of cut and feed rates are subject to constraints regarding available machine power and torque, stability of workpiece fixturing and security of tool clamping.
The final step in 1:1 optimisation is selecting an appropriate criterion in terms of minimum cost or maximum productivity and using cutting speed to fine-tune achievement of that criterion. It is important to remember the Taylor model for tool life determination. This model demonstrates that for a given combination of depth of cut and feed, there is a certain window for cutting speeds where tool deterioration is safe, predictable and controllable. When working in that window, it is possible to qualify and quantify the relation between cutting speed, tool wear and tool life.
Initially, machining time drops, and productivity rises with increasing cutting speeds. But after a certain point cost again start to rise. Above a certain cutting speed, tool life becomes so short that the cutting edge requires frequent replacement. In the total picture, the decrease of the machining time cost has a smaller effect than the fast-increasing tool cost. Somewhere there is a cutting speed where the sum of the two costs balances to result in a minimum total cost.
In the quest for productivity, shops have to be careful not to give too much attention to details and not enough consideration to the total picture, namely the total floor-to-floor time to produce the workpiece.
The levels of part quality required today are seriously higher than in the past. However, achieving top levels of quality sometimes is overdone. High quality is good but excessively high-quality wastes money. A simple, theoretical question that sums up the situation is: “How can we produce the worst workpiece possible that is still acceptable from a functional point of view?” Cost can be reduced drastically, and productivity can be increased dramatically by just fulfilling the minimal requirements.
Similarly, when focused entirely on maximum productivity in terms of lower cycle times, the reliability of a metalworking process can deteriorate. When a process is run constantly at the limits of possibilities and those limits are exceeded, the cost is rejected or scrapped workpieces and lost time.
Production efficiency involves three factors: quality, production time and cost. Environmental factors such as energy consumption and disposal or recycling of worn tools and machining waste must also be considered as well as safety factors regarding the wellbeing of employees.
Many individual technical factors affect production efficiency. For machining processes, it is not at all unusual for one or more of 50 - 70 individual factors to have an appreciable effect on efficiency. Typical factors include tools/tooling systems, workpiece configuration and materials, equipment process capabilities and data, human factors, peripheral equipment and maintenance issues.
One of the most influential factors is the result of the interaction of the tool and workpiece. Understanding of tool wear and failure modes is essential for control of the machining process. Wear-related phenomena generally are gradual and predictable, while other failure modes, such as tool breakage, lack the predictability required to maintain a reliable cutting process.
Balancing productivity, reliability and tool cost considerations requires tooling that offers versatility and flexibility over a broad application window. Versatile or universal tooling (see sidebar below) also is an answer for manufacturing’s clear trend towards smaller batch sizes. The move to smaller machining batch sizes results from increased utilisation of just-in-time production strategies and the growth of outsourcing.
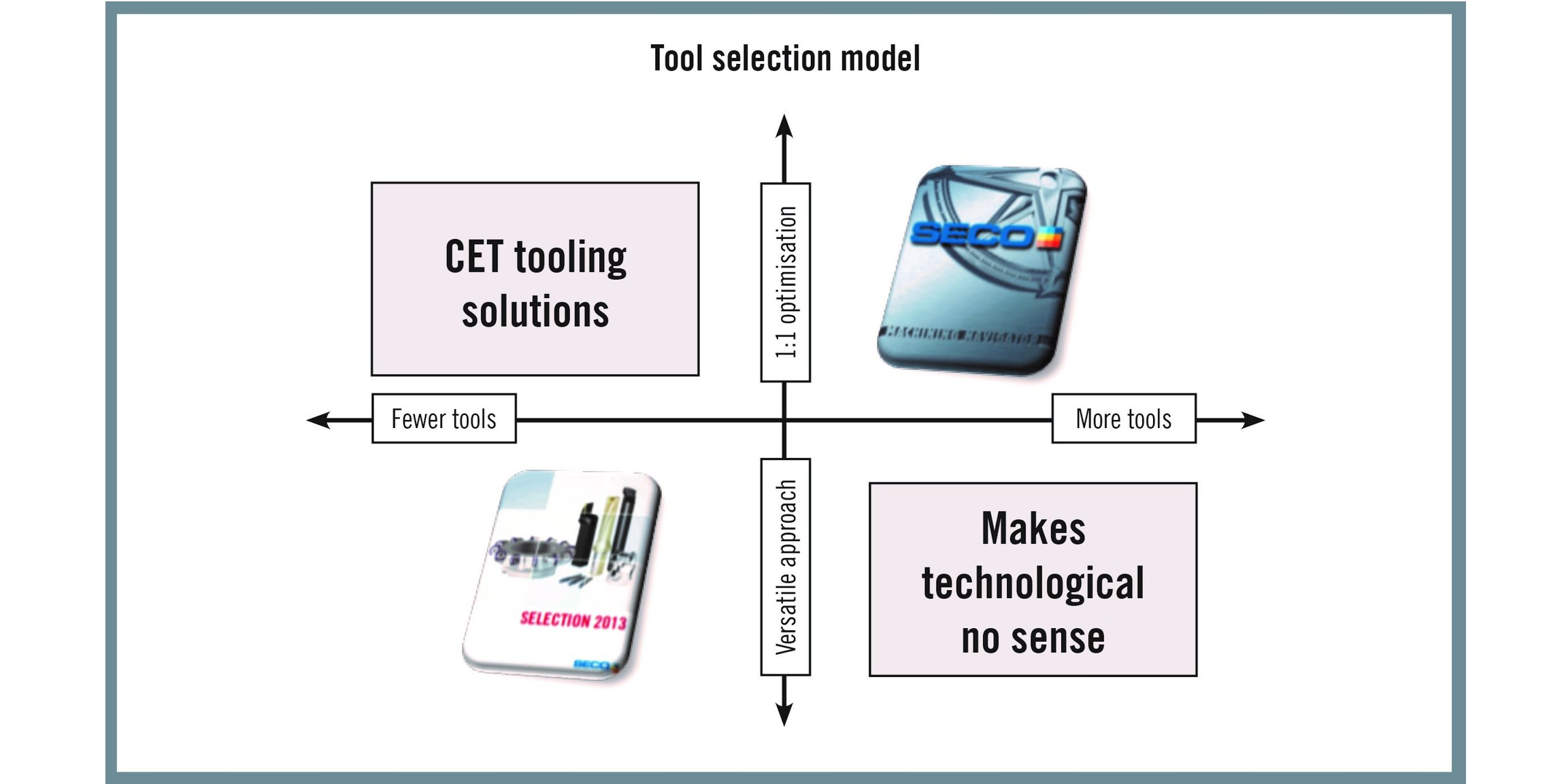
Subcontractors are confronted with smaller batch sizes that need to be produced regularly but not continuously. In the past, automatic toolchangers helped reduce toolchanging downtime, and the use of pallet changers reduced downtime resulting from workpiece manipulations. Universal tools can reduce downtime by minimising the time to switch in a new tool when the workpiece changes, as well as eliminating the need to set up and test run a new tool. Minimising the number of different tools in the workshop reduces tool-handling time and increases the time available for machining operations.
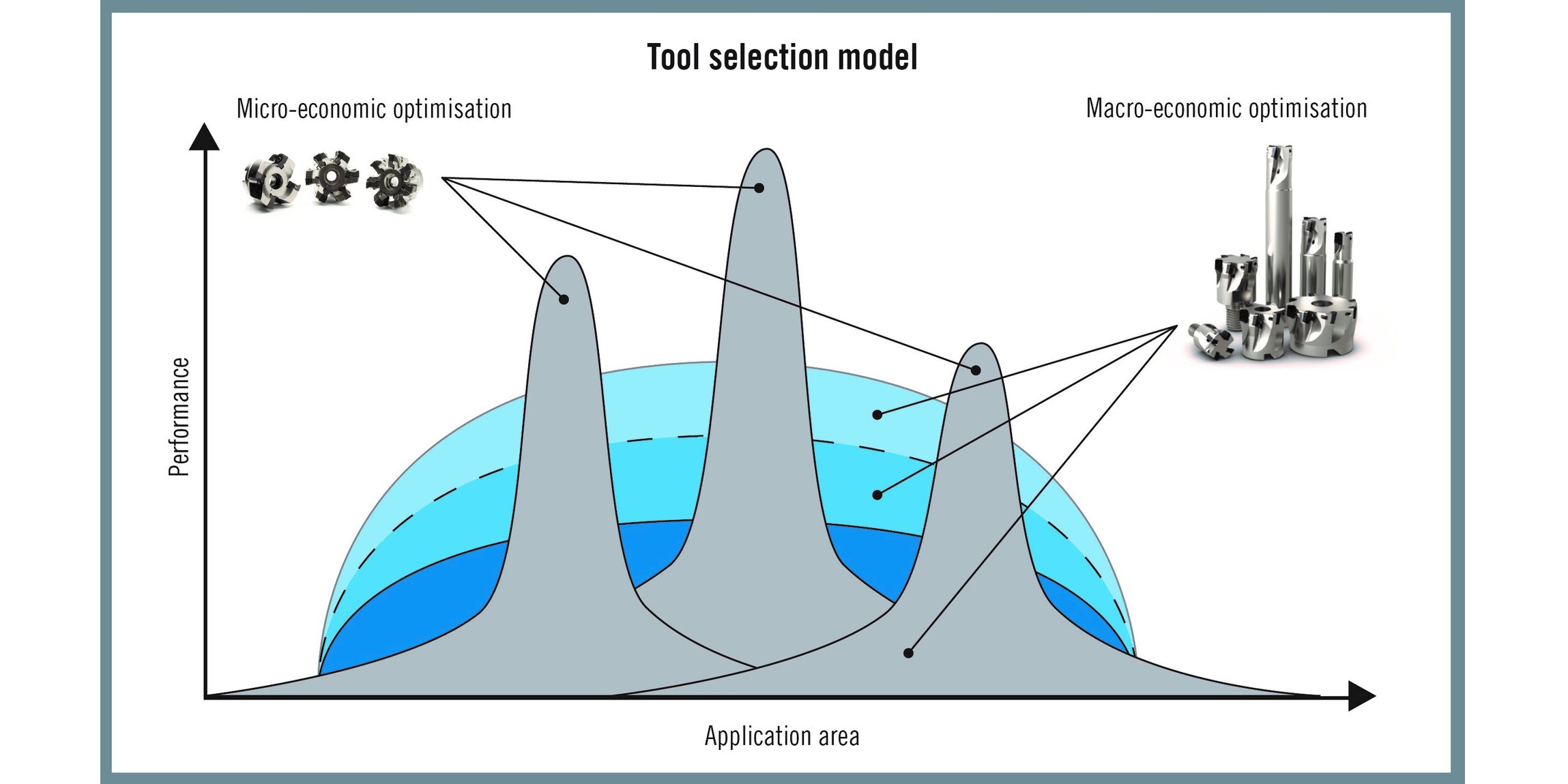
Traditional tool selection thinking tends to be application-oriented: seeking a tool specifically for steel, for stainless steel or for roughing or milling, for example. What is of more importance than choosing tooling for a single operation is how that operation fits into the total picture. The choice should be biased toward what is desired in terms of productivity, cost efficiency or reliability, and what best fits a broad view of the production process.
Taking the broad view to process optimisation need not be complex; it can involve very basic, simple actions and analysis. Examination of used tools is a key example. Correct interpretation of what the tools show can provide a broad view of what is going on in the workshop. For example, if a shop generally uses inserts with 12 mm-long cutting edges and wear patterns on the tools only reach 2 mm or 2.5 mm, that shop is probably using inserts that are much too big for what they do. Tools with 6 mm cutting edges would be more than sufficient, and a tool with 6 mm-long cutting edges is significantly cheaper than a tool with a 10 mm cutting edge. Such a simple observation can reduce tool costs by 50 percent without losing productivity.
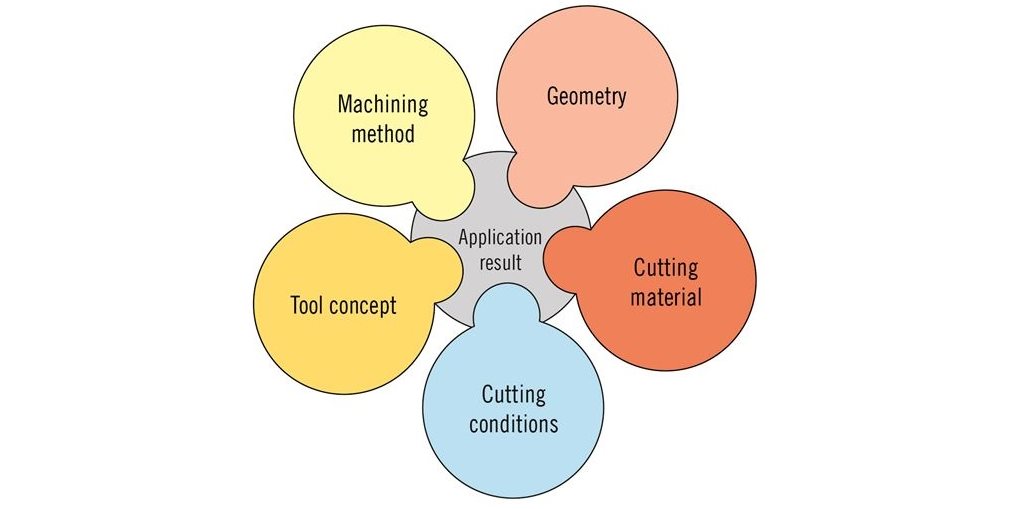
Inline Content - Survey
Current code - 5fce8e61489f3034e74adc64