10 tips on machining heat-resistant superalloys (HRSA)
Learn how to machine heat resistant superalloys.Heat-resistant superalloys (HRSAs) are well known to be “difficult-to-machine” alloys. The HRSA family has sub-categories:
- nickel
- iron and
- cobalt base alloys.
They were developed specifically for applications that demand exceptional mechanical and chemical properties at elevated temperatures. The classic use of these alloys is in the hot end of aircraft engines and land-based turbines. Over the past decade, these materials have seen their way into other applications such as chemical, medical, mining and structural design, where high-temperature properties or corrosion and oxidation resistance are in high demand.
Every metallurgical change to improve the material’s properties to make them ‘super’ makes it more difficult for us machinists. Typical failure modes observed when machining superalloys are abrasive wear at the nose radius, chipping at the cutting edge, and notch wear at the depth-of-cut line. The difficulty of machining superalloys mainly resolves itself into short tool-life and poor surface finish of the machined part. The main reasons for this are:
- Low thermal conductivity - superalloys constrict the heat flow into the chips and generate high cutting temperatures on the cutting edge. This can cause deformation of the cutting edge.
- Strain hardening - Most superalloys work-harden rapidly, which means that a hardened surface is formed during machining. Notch wear occurs at the depth-of-cut line, mainly due to the hardening of the material during machining.
- Hot hardness - The high mechanical strength of superalloys at elevated temperatures – such as when machining – appears in the cutting zone resulting in high cutting forces on the cutting edge. This can cause edge chipping or edge deformation.
- Abrasiveness – HRSA’s are heat treated before machining to modify their properties, in which abrasive carbide precipitates or other second phase particles often form. These hard particles cause rapid abrasive nose wear and flank wear.
- Use relatively large depths of cut with a reduced cutting distance or constantly varying depths of cut to minimise notch wear caused by strain hardening.
- Use positive geometries with PVD coatings, as this reduces pressure and breakage.
- Use relatively low cutting speeds with large feed rates to reduce heat generation and lower temperatures on the cutting edge.
- Use high-pressure directed emulsion to control the temperature even more.
- Use an oil-based emulsion with approx. 12-15% concentration level to help with lubrication at the cutting edge, which will increase tool life.
- Use the largest nose radius possible as this tool feature will spread the cutting forces and heat generated during the cutting process to a larger portion of the insert, decreasing point wear and increasing tool life.
- Also, use a “Button” insert or a tool with the biggest approach angle to spread the cutting forces over a larger area.
- Don’t try and generate spring cuts, as this will cause the tool to rub, causing premature wear and increased heat generation, leading to Strain Hardening.
- When milling on older machines, maintain a width-of-cut no greater than 30% of your tool diameter to control heat generation and tool wear.
- When machining on newer machines, use advanced Dynamic turning and Dynamic milling strategies to minimise heat generation and tool wear.
For more information or help contact us or visit the Aerospace Industry Segment Solution page.
Follow David Morr for more articles.
Inline Content - Survey
Current code - 5fce8e61489f3034e74adc64
HOMERelated content
How to deal with "difficult-to-machine' materials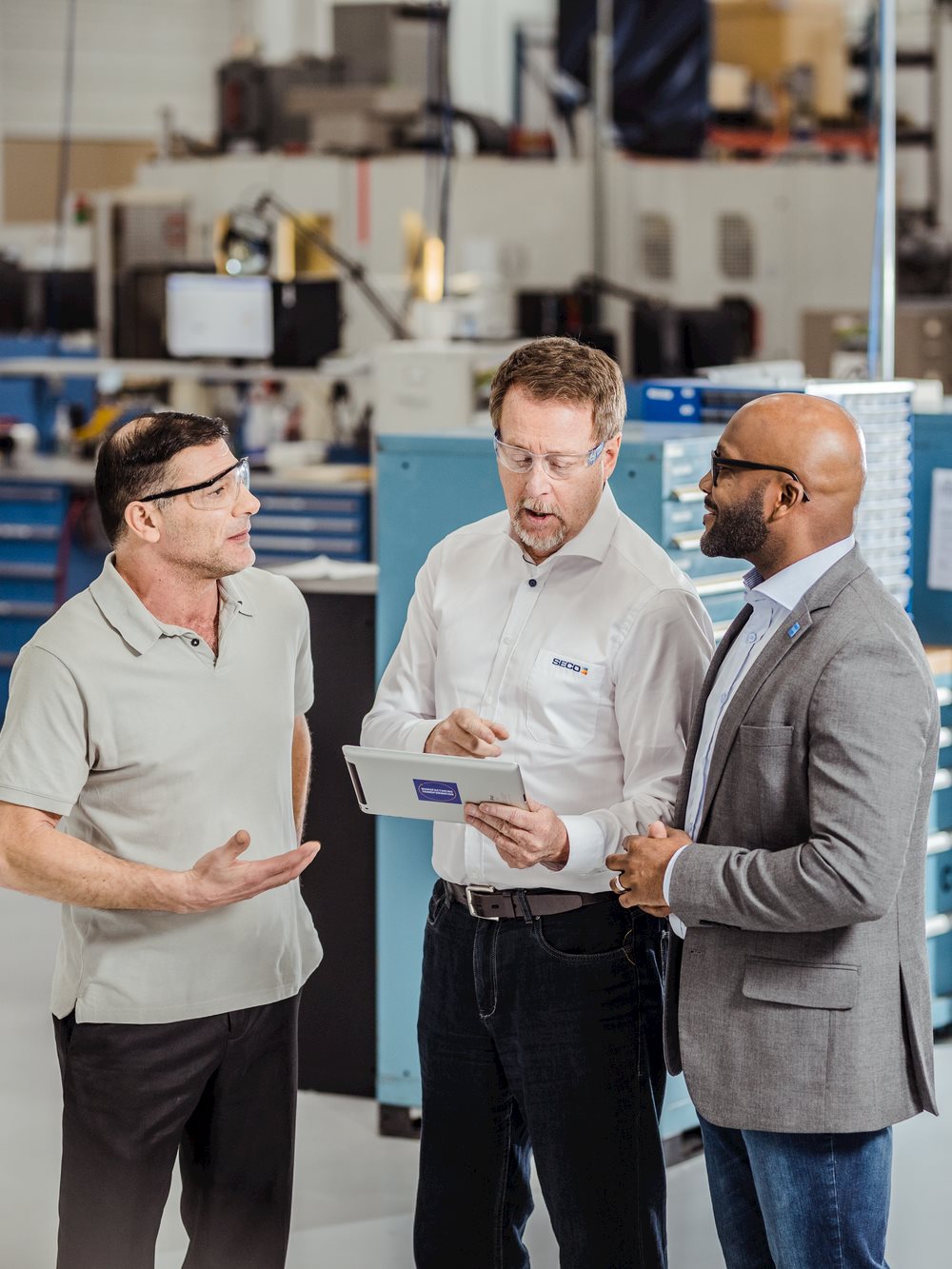
Advances in superalloy machinability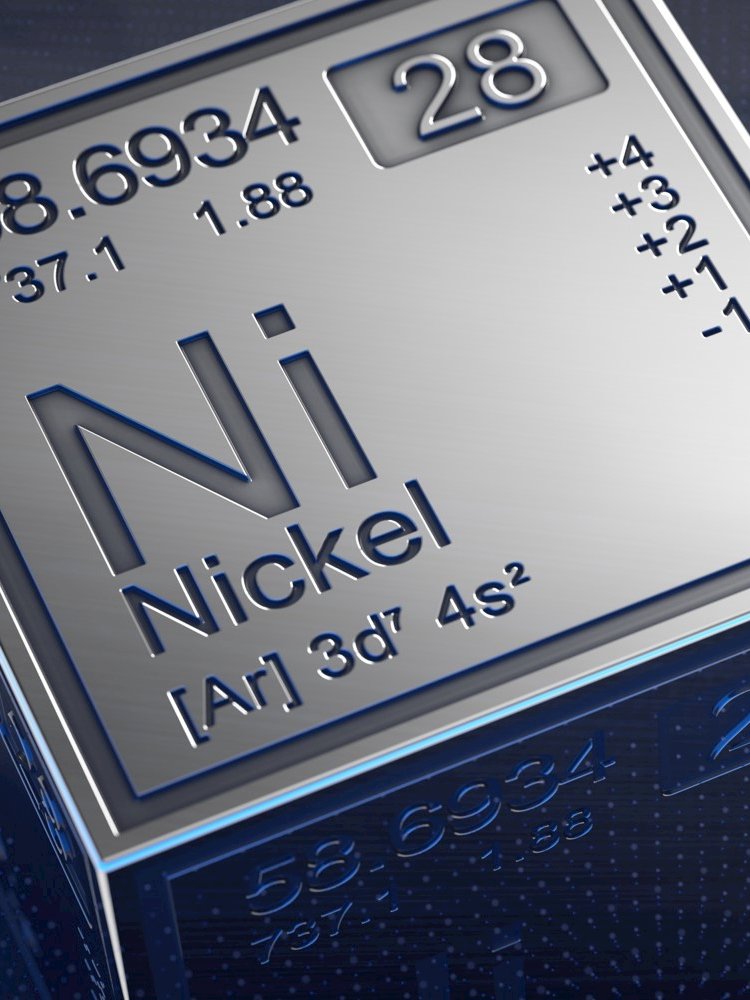
Material and machining trends in aerospace manufacturing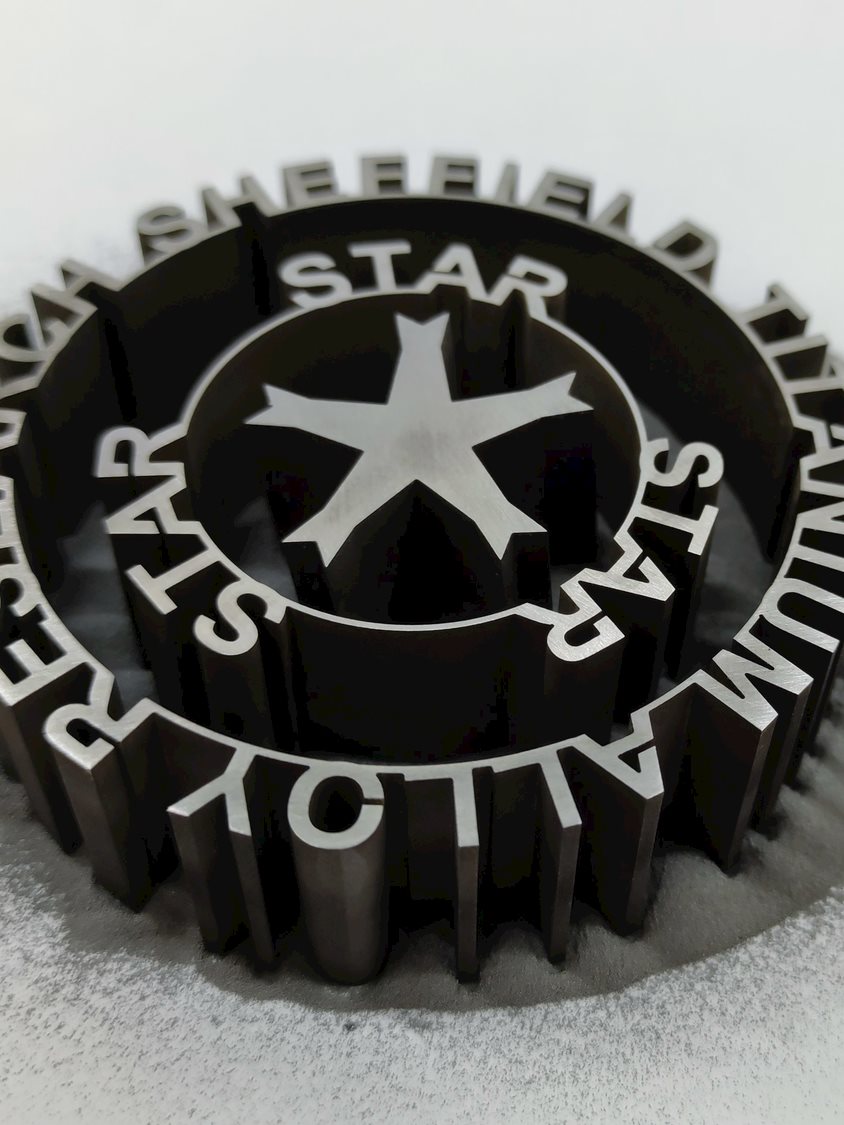
The Ethics of A.I.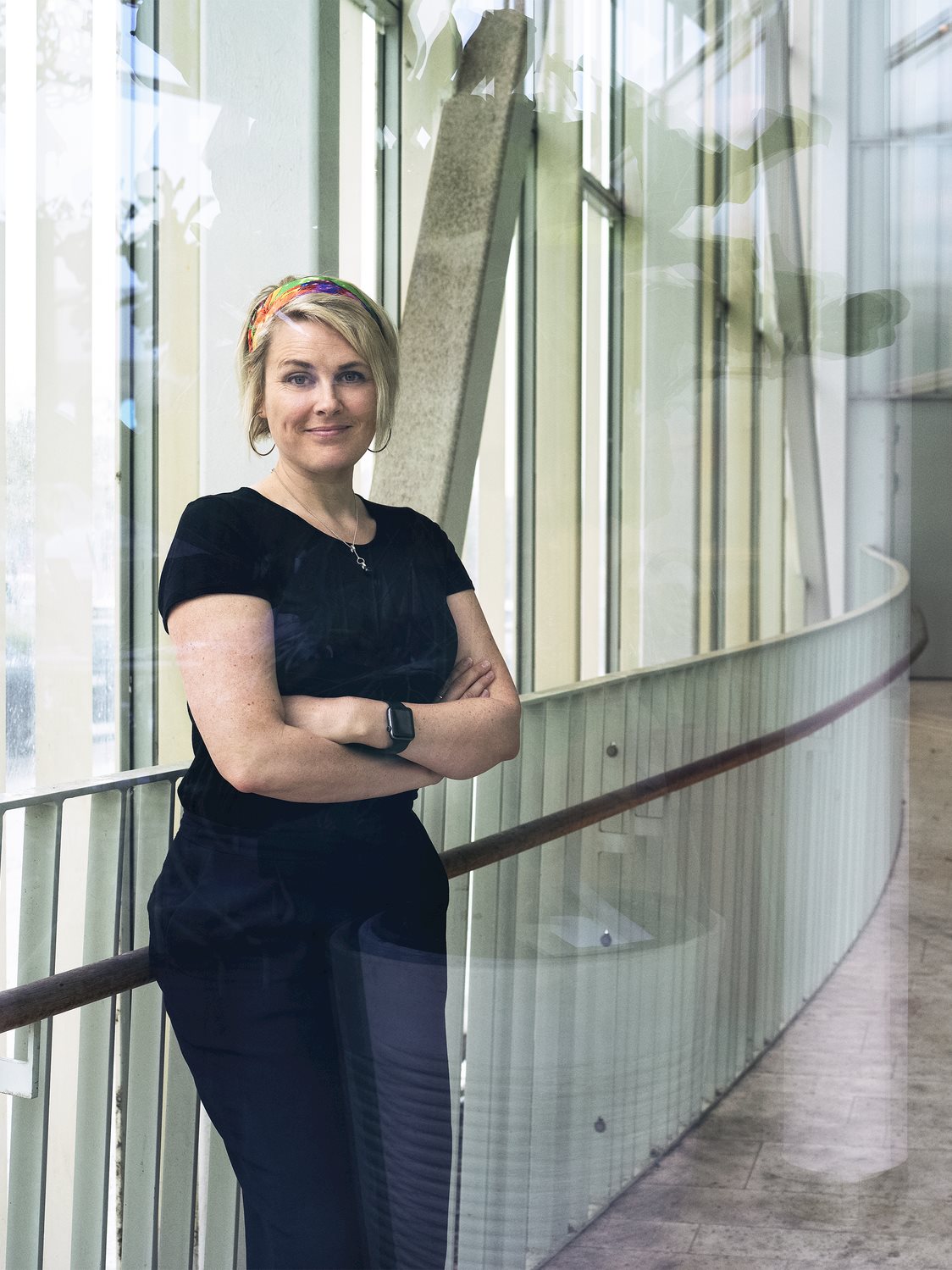
Seco Innovation Hubs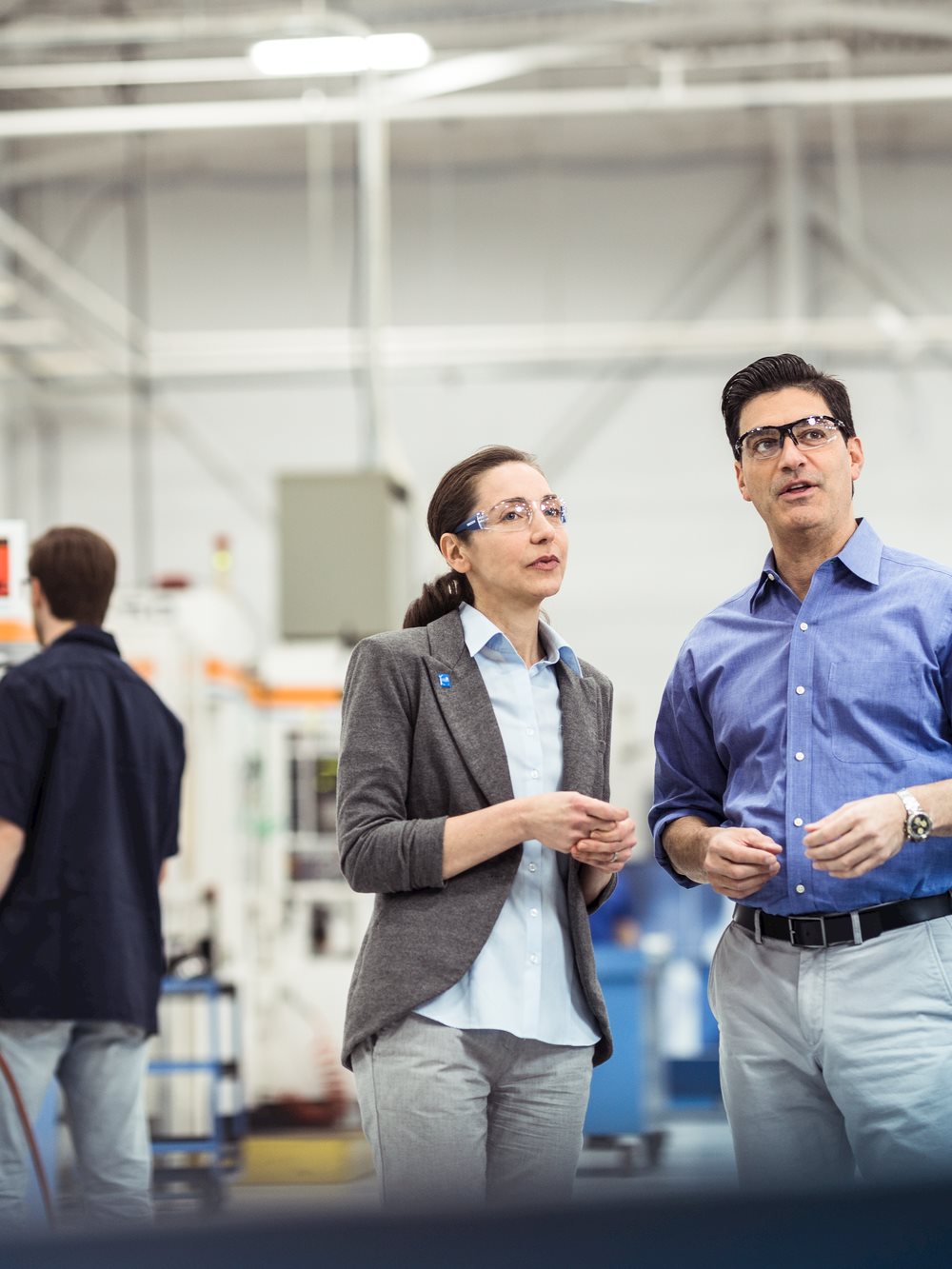
Advances in superalloy machinability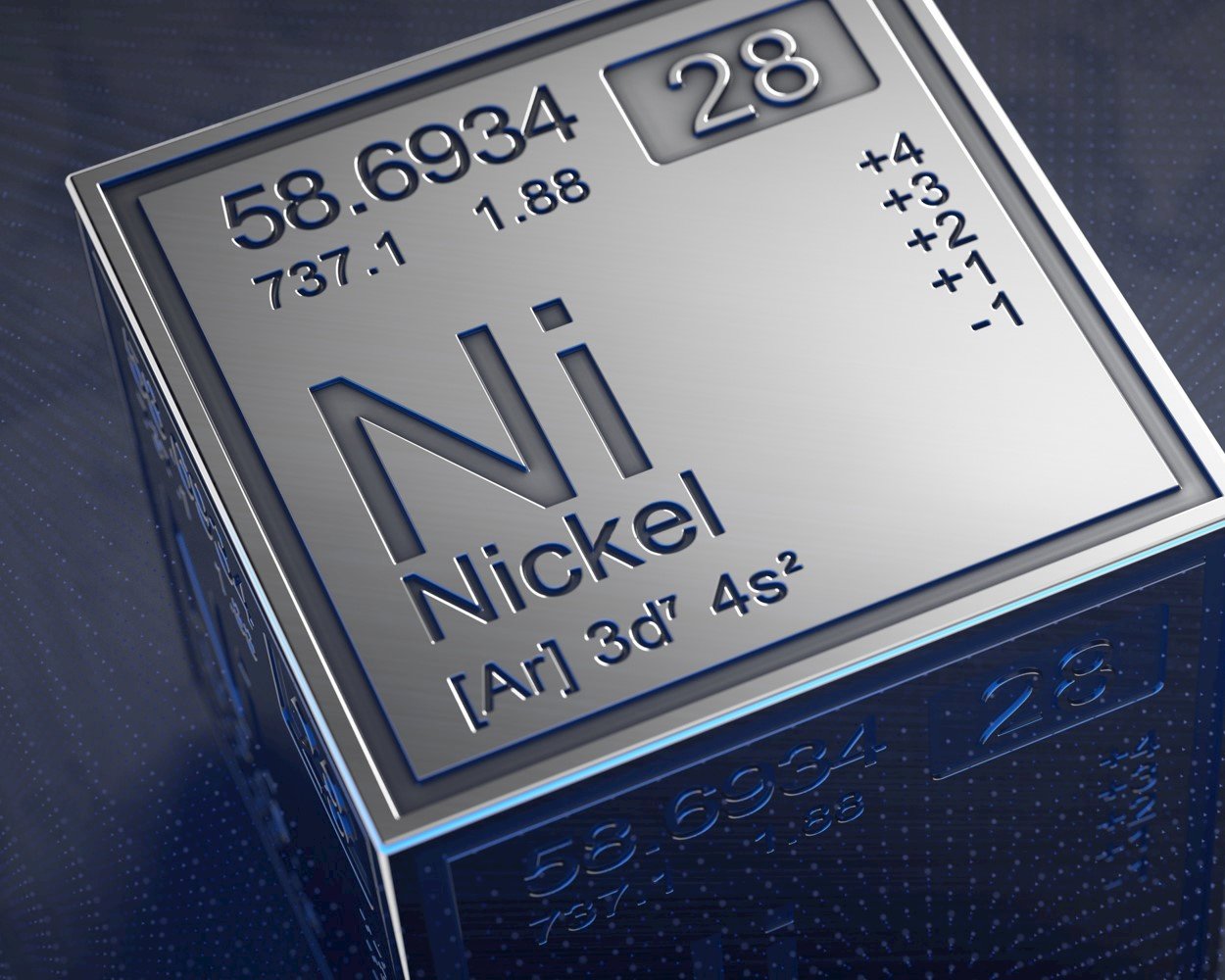
Inspiration Through Innovation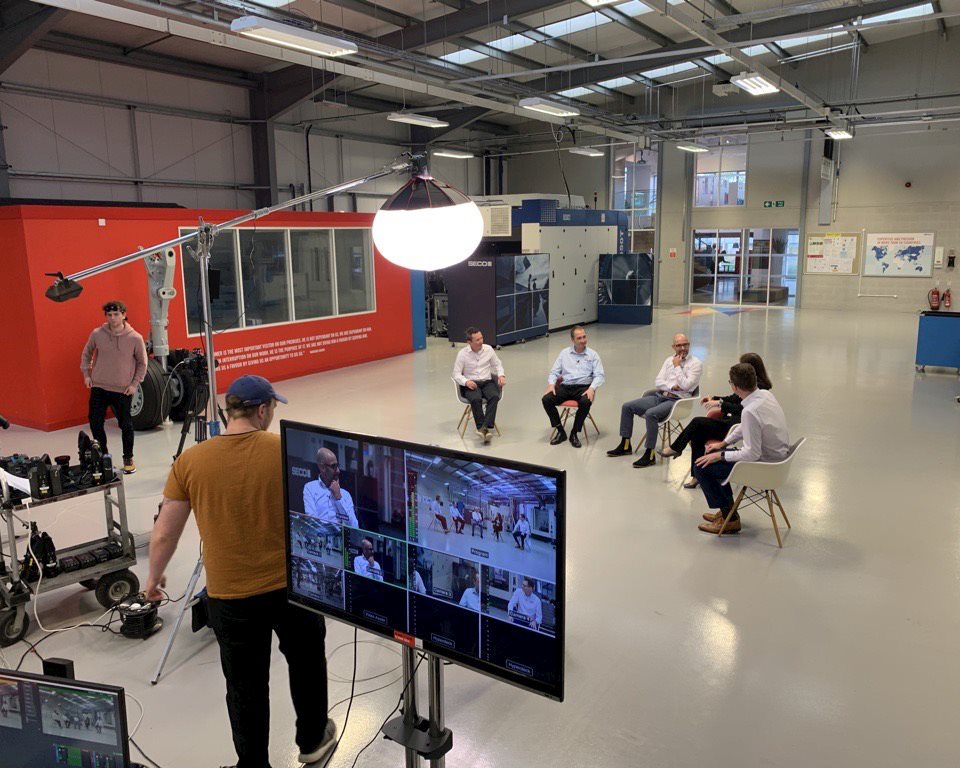
Seco R&D delivers for Scania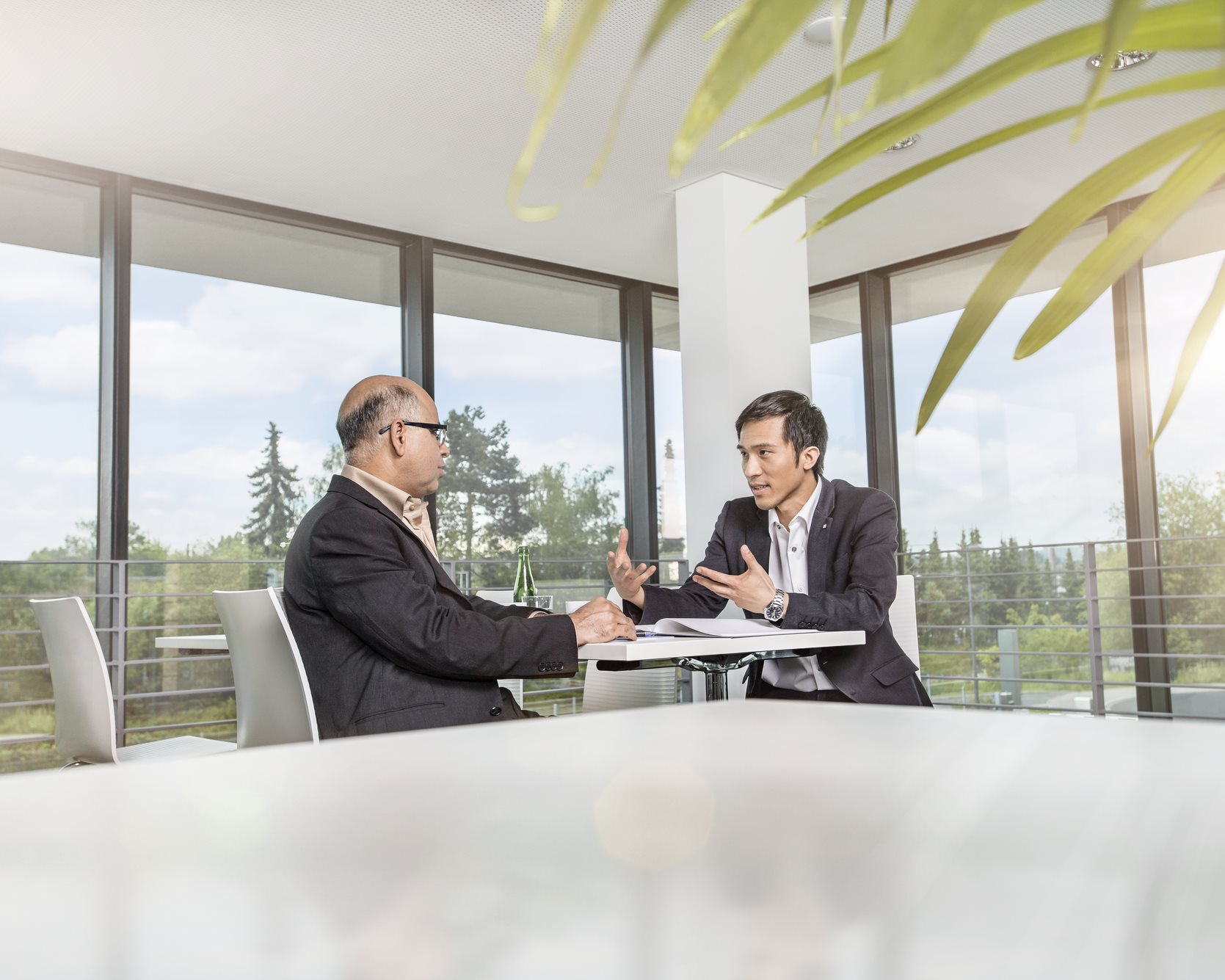
Seco Tools 3D Manufacturing creates New Opportunities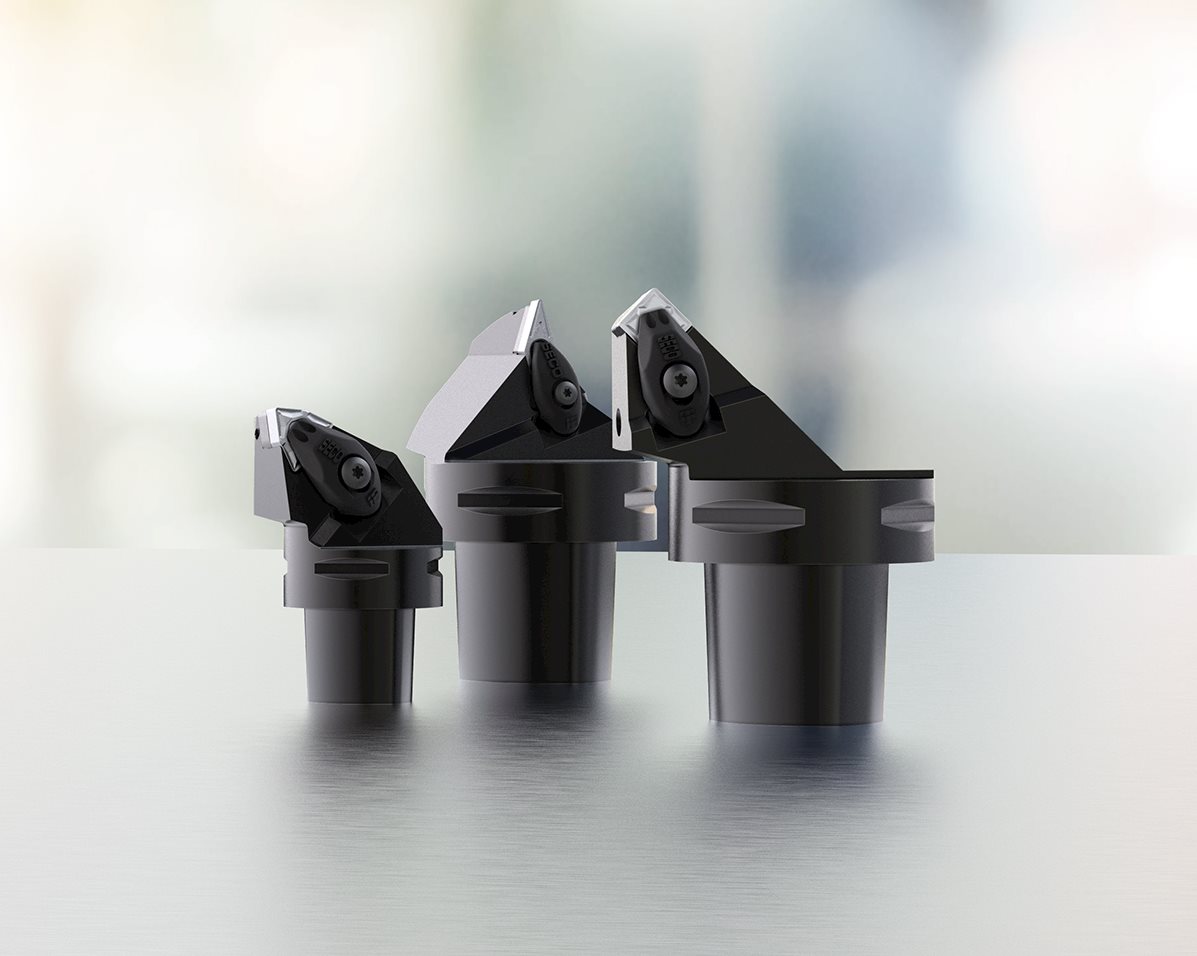
Seco launches innovative solutions for optimized part processing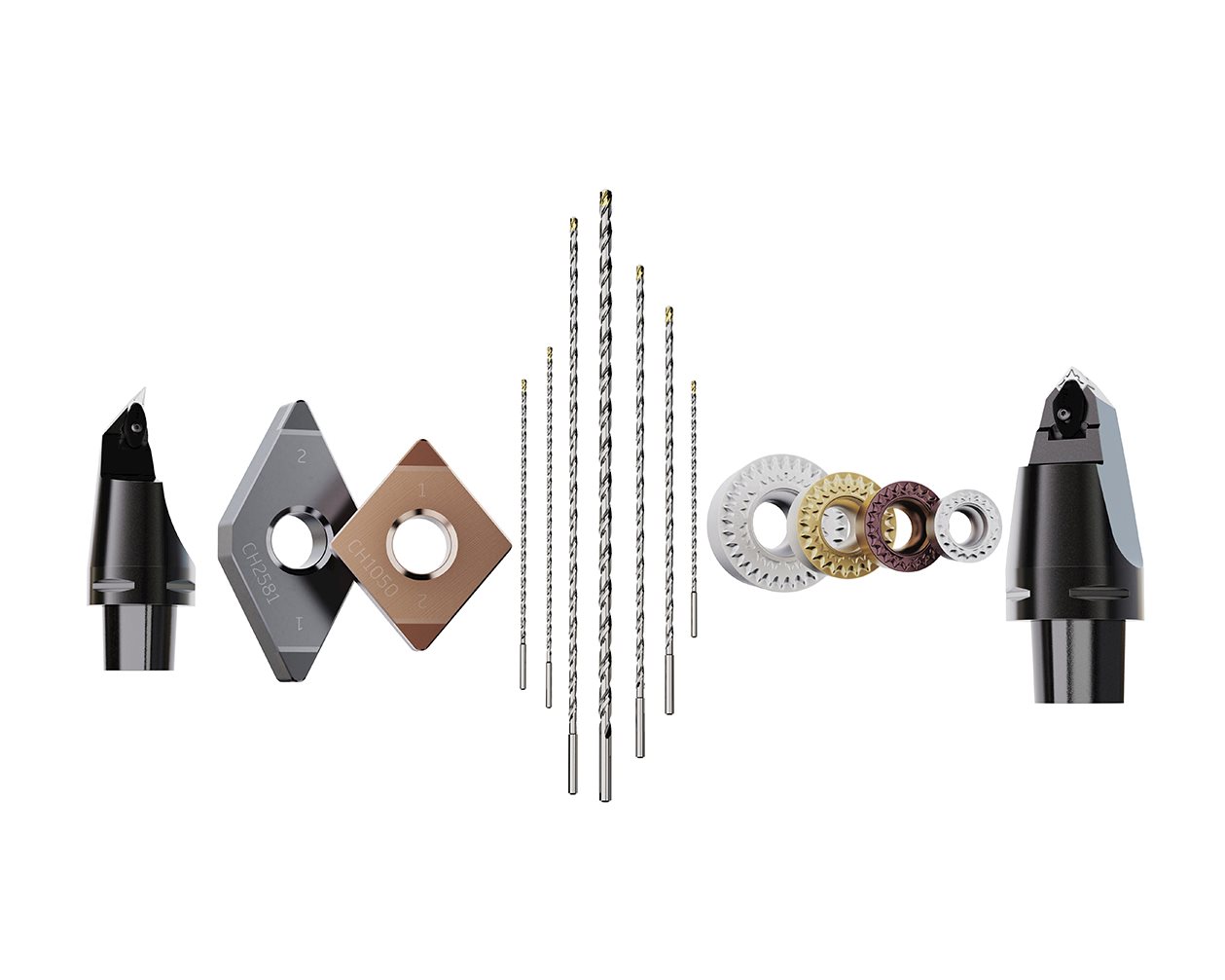
Inspiration Through Innovation 2024: Championing collaboration in the pursuit of manufacturing excellence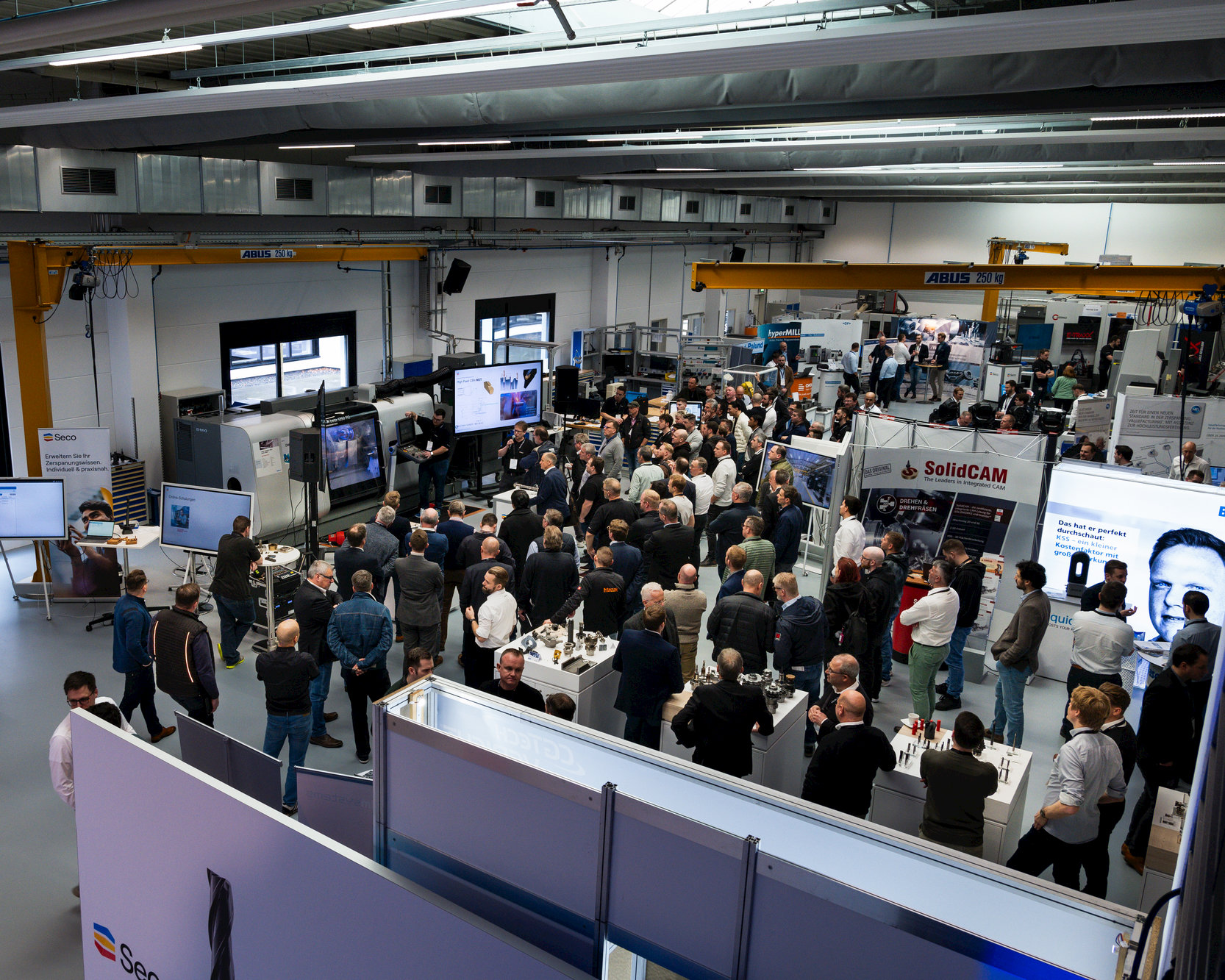