Trochoidal Slot Milling
Trochoidal milling has become a popular method of dynamic machining across a variety of applications for milling pockets, slots and hard materials. Using a spiral tool path with a low radial depth of cut and high axial trochoidal milling cuts slots wider than the tool’s diameter. Trochoidal milling offers several advantages over conventional milling, including radial chip thinning, faster feed rates, improved accuracy and longer tool life.With its origins in mold and die making, trochoidal milling has become a popular method of dynamic machining across a variety of applications for milling pockets, slots and hard materials. Instead of attacking the workpiece head on, trochoidal milling uses a spiral tool path that allows it to machine slots wider than the tool’s diameter. By using a low radial depth of cut (DOC), trochoidal milling enables a high axial DOC and feed rate that keeps the cutting tool in continuous movement using low cutting forces.
The low radial DOCs produce chips that are extremely thin. As a result of this radial chip thinning, a radial chip thinning formula can be used to calculate increased feed rates that will generate a normal-sized chip and improve production.
Trochoidal milling offers several advantages over conventional milling. Even though it is essentially a roughing strategy, trochoidal milling improves accuracy and finishes over hard slotting.
Utilizing a lower radial DOC and higher axial DOC also improves tool wear and tool life. With a higher axial DOC, heat is distributed along the entire length of the cutting edge and not just at the bottom of the tool. Improved tool life translates to more sustainable, cost-effective machining and less downtime attributed to tool changeovers.
Additionally, job shops engaged in high-mix production can machine multiple slot and pocket dimensions with just one tool.
To capitalize on the advantages of trochoidal milling over conventional milling, tool rigidity is paramount. Due to the quick movement and radial forces on the tool, shops must use the best toolholding available in terms of stability and clamping force. Shrink fit, hydraulic and other proprietary toolholding systems that maximize security are recommended.
As a result of the thin chips produced by radial chip thinning that occurs during trochoidal milling, tools can have more and shallower flutes for better surface finishes and faster feed rates. Shallower flutes also provide a tool with a stronger core to withstand the radial forces exerted. The use of multi-flute tools and small radial DOCs result in significant gains in efficiency.
Trochoidal milling also requires a machine tool that is fast with sufficient torque and acceleration to accommodate the many small movements of the trochoidal milling tool path. Similarly, shops should thoroughly research a robust CAM software package that is capable of programming and controlling the application.
In this #SecoTechTalk installment, Seco Product Manager Jay Ball shows you how to use radial chip thinning formulae to calculate the recommended slot width for trochoidal slot milling. To allow the machine time to strike an arc and for proper chip evacuation, the slot must be 60% larger than the tool diameter. Check out more of Jay’s #SecoTechTalk for more on the trochoidal milling calculator.
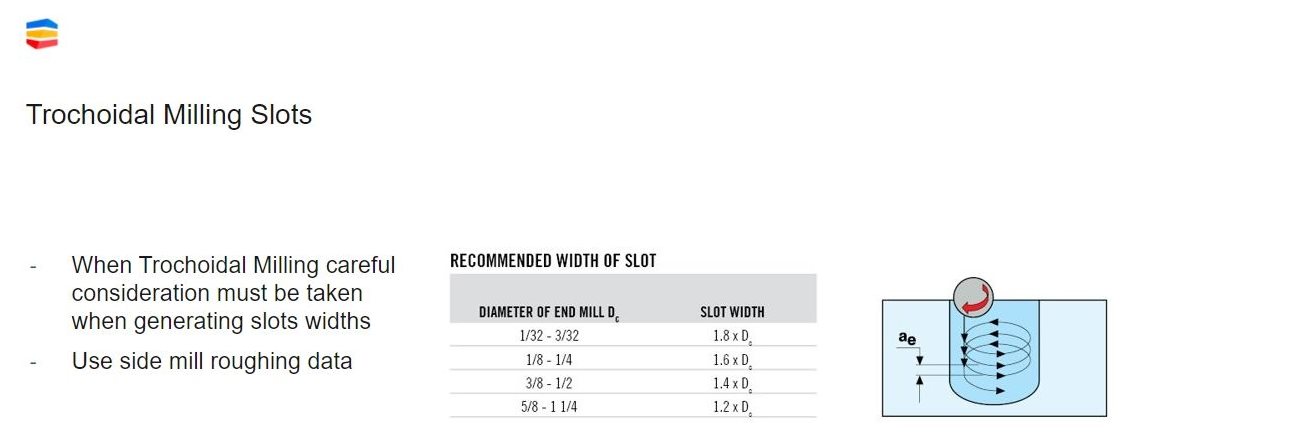
For tips on getting the most from your machining operations, catch more episodes of Jay’s #SecoTechTalk on Seco’s Instagram. You’ll find practical advice that makes your machining more efficient and sustainable. Leave a comment to let him know what you want to hear about next.
Inline Content - Survey
Current code - 5fce8e61489f3034e74adc64