Milling Application
Explore the fundamental principles of milling applications in the machining industry with our comprehensive guide. Elevate your knowledge and stay ahead in the ever-evolving world of machining. Start your milling journey today!
TABLE OF CONTENT
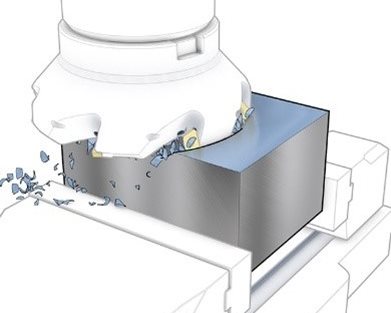
Milling takes center stage when intricate designs and complex shapes are on the agenda.
In this machining process, the workpiece remains stationary, while the milling tool rotates and moves in linear motions, gradually removing excess material to reveal the desired geometry. Milling excels at crafting cubicle shapes, flats, and intricate contours that demand unparalleled precision and detail.
The interaction between the rotating milling tool and the workpiece creates a distinctive characteristic. The cutting edges enter and exit the cut repeatedly, resulting in the formation of broken chip segments.
Despite its intermittent chip formation, milling offers outstanding versatility and is widely adopted in the manufacturing realm for its ability to craft intricate and aesthetically pleasing components.
In milling, four cutting conditions govern the process:
- revolutions per minute (RPM),
- feed speed (mm/min),
- axial depth of cut (ap),
- radial depth of cut (ae).
Milling, with its multiple cutting teeth in motion, requires a more involved understanding of these parameters than turning.
Unlike turning, milling is a machining process where the workpiece remains stationary, and the milling tool rotates. Therefore, CNC milling machines utilize “RPM” and “Feed Speed” (table feed) as the primary cutting parameters.
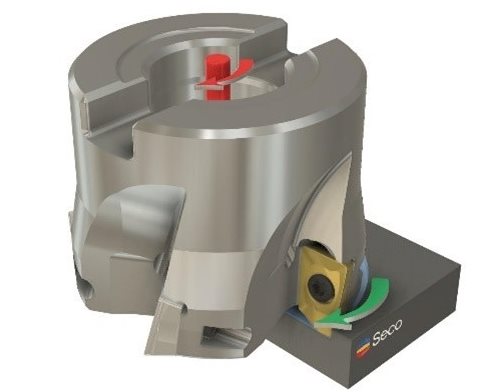
Distinguishing between “RPM” and “Cutting Speed” in milling is crucial. While “RPM” denotes the number of turns completed by the milling tool in one minute, “Cutting Speed” measures the relative velocity between the milling tool and the workpiece surface. Accurate translation between these two parameters is essential for successful milling operations.
“Milling Feed” is a multifaceted term, including “feed per tooth,” “feed per revolution,” and “feed speed.”
Understanding each definition is vital for achieving precise and efficient milling.
“Feed per tooth” refers to the theoretical length of material fed into one cutting edge at the tool’s centerline as it moves through the material.
“Feed per revolution” represents the actual length the cutting tool advances along the centerline after one complete spindle revolution. Finally, “feed speed” is the linear velocity of the milling cutter relative to the workpiece and is calculated by multiplying the feed per tooth, number of teeth, and revolutions per minute.
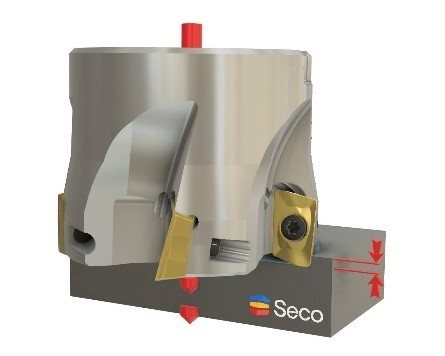
In milling, the “axial depth of cut” (ap) refers to the distance a tool engages the workpiece along its centerline. It determines how deeply the tool cuts into the material, affecting the efficiency and accuracy of the operation.
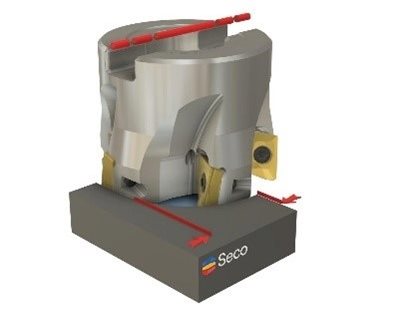
The “radial depth of cut” (ae) in milling is the distance the tool steps over into the workpiece. It measures the depth of the tool along its radius as it cuts. The choice of radial depth of cut influences the tool engagement and the type of cut made, be it peripheral or slot cutting.
Milling, with its multiple cutting teeth in motion, demands a more comprehensive understanding of cutting parameters compared to turning. The four key cutting conditions: revolutions per minute (RPM), feed speed, axial depth of cut, and radial depth of cut, govern the milling process. By mastering these cutting parameters, machinists can optimize productivity and produce high-quality parts, advancing the CNC machining industry to new heights of reliability and effectiveness.
Beginners Guide to CNC Milling Operations and Strategies
In the fast-paced Secrets of manufacturing, achieving precise and efficient results is essential. Milling operations play a crucial role in shaping materials with unmatched accuracy. Among the different cutting tools available, milling tools stand out as versatile and effective choices. In this guide, we’ll explore various milling operations you can accomplish with these tools, highlighting their transformative impact on the manufacturing industry.
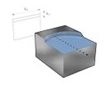
Face milling is a common operation used to create flat surfaces on a workpiece.
With milling tools equipped with multiple cutting edges, you can efficiently remove material in a single pass.
This process is vital for achieving plane surfaces, refining rough cuts, and getting high-quality finishes.
Manufacturers across industries love face milling for its versatility and precision, making it the ‘go-to’ choice for flawless results.
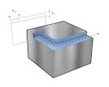
In side milling (known as peripheral milling), the milling tool removes material from the outer edges of the workpiece.
This operation is perfect for contouring, profiling, and slotting.
Thanks to the tool’s multiple cutting edges, you can quickly remove material, making it ideal for roughing.
Industries benefit from the efficiency and reliability of peripheral milling, allowing them to craft intricate shapes and meet strict design specifications.
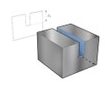
Slot milling involves cutting narrow channels or slots into the workpiece.
The design of milling tools allows for precise slot milling due to their sharp cutting edges and stable construction.
This operation is widely used in manufacturing keyways, grooves, and other similar features.
Milling tools deliver exceptional performance in slot milling, ensuring industries achieve the precision necessary for critical components.
Chamfering and Beveling: Mastering Angles

Chamfering and beveling involve cutting angles on the edges of a workpiece.
Milling tools with specialized chamfering or beveling geometries accomplish these tasks accurately and efficiently, providing consistent edge finishes and ensuring precise dimensions.
Manufacturers can achieve impeccable bevels and chamfers, enhancing both aesthetics and functionality.
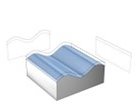
Copy milling, also known as contouring, is a milling operation used to create complex shapes on the workpiece’s surface.
Milling tools with ball nose or corner radius designs are ideal for contouring, as they can smoothly follow the contours of the workpiece, producing intricate shapes with excellent surface finish and detail.
This operation allows manufacturers to unleash their creativity, delivering innovative and eye-catching designs.
Some milling tools transcend their traditional role and embrace the art of drilling with remarkable precision.
With the right design, these versatile milling tools effectively perform drilling operations, making them a game-changer in machining.
Solid carbide end mills, often at the forefront of this revolution, prove their worth in drilling tasks.
Still, a select few indexable milling cutters also join the league, thanks to their unique point geometry designs that enable them to drill holes skillfully.
This ingenuity positions these milling tools as viable alternatives to traditional twist drills, particularly in specific applications where their capabilities shine.
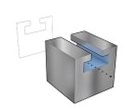
T-slot milling is the operation of producing T-slots on the workpiece using a T-slot milling cutter.
This versatile process enables the creation of slots that can accommodate various fixtures and components, making it essential for many manufacturing applications.
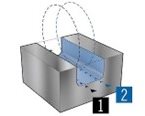
It is the operation of producing the groove on the surface of the workpiece by using a saw-milling cutter or end milling cutter.
The workpiece is fixed firmly on a milling machine, and fixing the end milling cutter on an arbor, by adjusting the depth of cut, the work is fed against the cutter to cut the groove on the work surface.
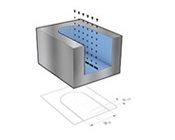
Plunge milling is a technique where the milling tool is fed directly into the workpiece, creating pockets or cavities.
Milling tools excel in plunge milling due to their rigidity, reducing the risk of deflection and ensuring accurate results.
This operation is often used in roughing and finishing processes, providing manufacturers with the means to achieve intricate designs and perfect contours.
High-Feed Milling: Need for Speed and Productivity
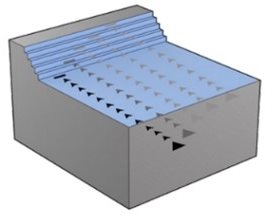
High-feed milling allows significantly higher feed rates compared to conventional methods.
Specialized milling tools equipped with high-feed geometries are ideal for this process, rapidly evacuating chips and maximizing material removal rates.
As a beginner, adopting high-feed milling will help you accomplish quicker roughing operations and boost overall productivity.
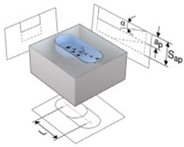
Ramping in a linear motion emerges as the go-to method for approaching workpieces, especially when dealing with closed slots, pockets, and cavities.
This efficient approach eliminates the need for a drill, streamlining the machining process and maximizing productivity.
Ramping intertwines in a mesmerizing two-axis ramping dance by simultaneously feeding in the axial (Z) and one radial direction (X or Y).
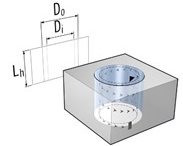
Circular interpolation, specifically circular milling in a 2-axis approach, is a highly effective technique for machining large holes.
Usually, starting with a pre-drilled hole in the workpiece, we follow up with a square shoulder milling or a long-edged milling cutter.
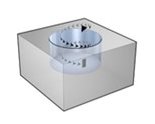
Discover the art of, also known as circular ramping and spiral interpolation.
This advanced technique boasts simultaneous circular motion in the X and Y directions, perfectly synchronized with an axial feed in the Z direction at a defined pitch.
Embracing circular ramping offers an exceptional alternative to traditional drilling methods, empowering your machining endeavors with unparalleled efficiency and finesse.
Helical interpolation reigns supreme over linear ramping (full slotting) and circular interpolation for many reasons.
Trochoidal Milling: Optimize Efficiency and Reduce Wear
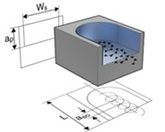
Trochoidal milling is a high-performance strategy that optimizes material removal using circular tool paths.
Milling tools with multiple cutting edges work wonders in trochoidal milling, reducing tool wear, cutting forces, and vibrations.
This technique leads to exceptional surface quality and extends tool life, making it a perfect choice for precise and efficient machining.
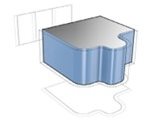
2D Advanced milling (also known as Adaptive 2D Milling and dynamic milling) is the epitome of efficient roughing with well-defined tool paths that maintain a constant arc of contact, ensuring reliable machining of simple and intricate shapes.
Embrace the advantages of large axial depths (ap) and small radial depths (ae) of cut, complemented by remarkably high feeds per tooth (fz) and cutting speeds (Vc).
This powerful combination enhances productivity and showcases the utmost precision in your machining endeavors.
Barrel milling is a specialized machining process using barrel solid end mills and a 5-axis machine. With innovative circle-segment end mill geometries, you can finish parts up to 80% faster than conventional ball-nose end mills, as these circle-segment end mills have a unique contour with a considerably larger radius, allowing for increased step-over distance during finish milling.
Barrel end mills demonstrate exceptional proficiency in handling finishing and semi-finishing machining tasks for 3D surfaces with minimal stock removal. This is made possible by their unique toroidal cutting geometry, which enables them to operate at high feed rates, leveraging the chip thinning effect for enhanced efficiency.
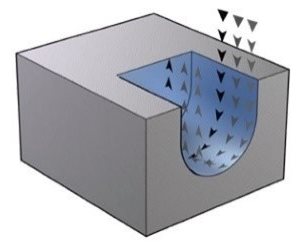
Push-Pull milling is a sophisticated 3D machining method that involves executing a synchronized down and up copying movement, meticulously following the profile of the desired form.
This innovative approach delivers enhanced precision and efficiency, making it a favored choice in modern machining practices.
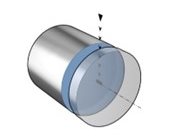
Cutoff blades, mounted on a shank or arbor and held in a milling machine spindle, are perfect for streamlined cutoff tasks. With 3+2-axis or 5-axis machine movement, these blades offer precise cuts from optimal angles, boosting productivity and accuracy. Integrating cutoff blades into your 5-axis workflow unlocks multifunctional capabilities, optimizing efficiency and simplifying setups. Embrace this dynamic duo and elevate your precision machining to new levels.
General machining is a versatile strategy suitable for various applications, where the ae-ap ratio can be adjusted based on the operation. The best part is that there are no special machine requirements needed, making it accessible with basic CNC technology. While not suitable for highly advanced methods, it consistently delivers satisfactory results, achieving average metal removal rates. Its application area often includes small batch sizes and a wide range of materials.
While no special requirements exist for an indexable milling cutter, solid carbide endmill characteristics include long cutting lengths and thin core diameters, providing excellent performance and chip evacuation.
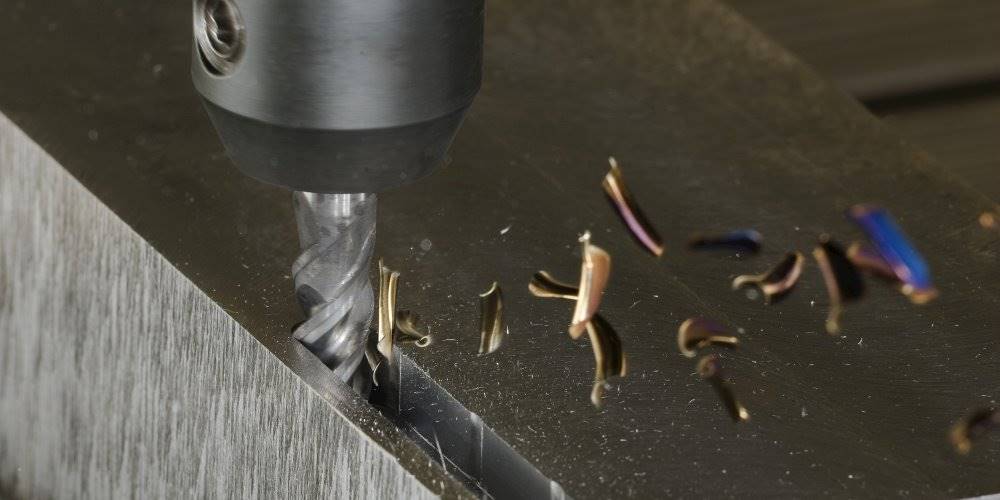
HPM strategy allows you to achieve remarkably high metal removal rates. You can maximize productivity by utilizing a significantly higher chip load compared to general machining. High stability, power, CNC control, and a rigid clamping system are essential CNC machine requirements. HPM excels in mass production environments where production time is critical or in applications requiring a high metal removal rate (Q cm3/min) for individual products.
Special tool features, such as chip formers in the flute, tip protection, smooth-formed chip space, and various coatings, enhance the performance.
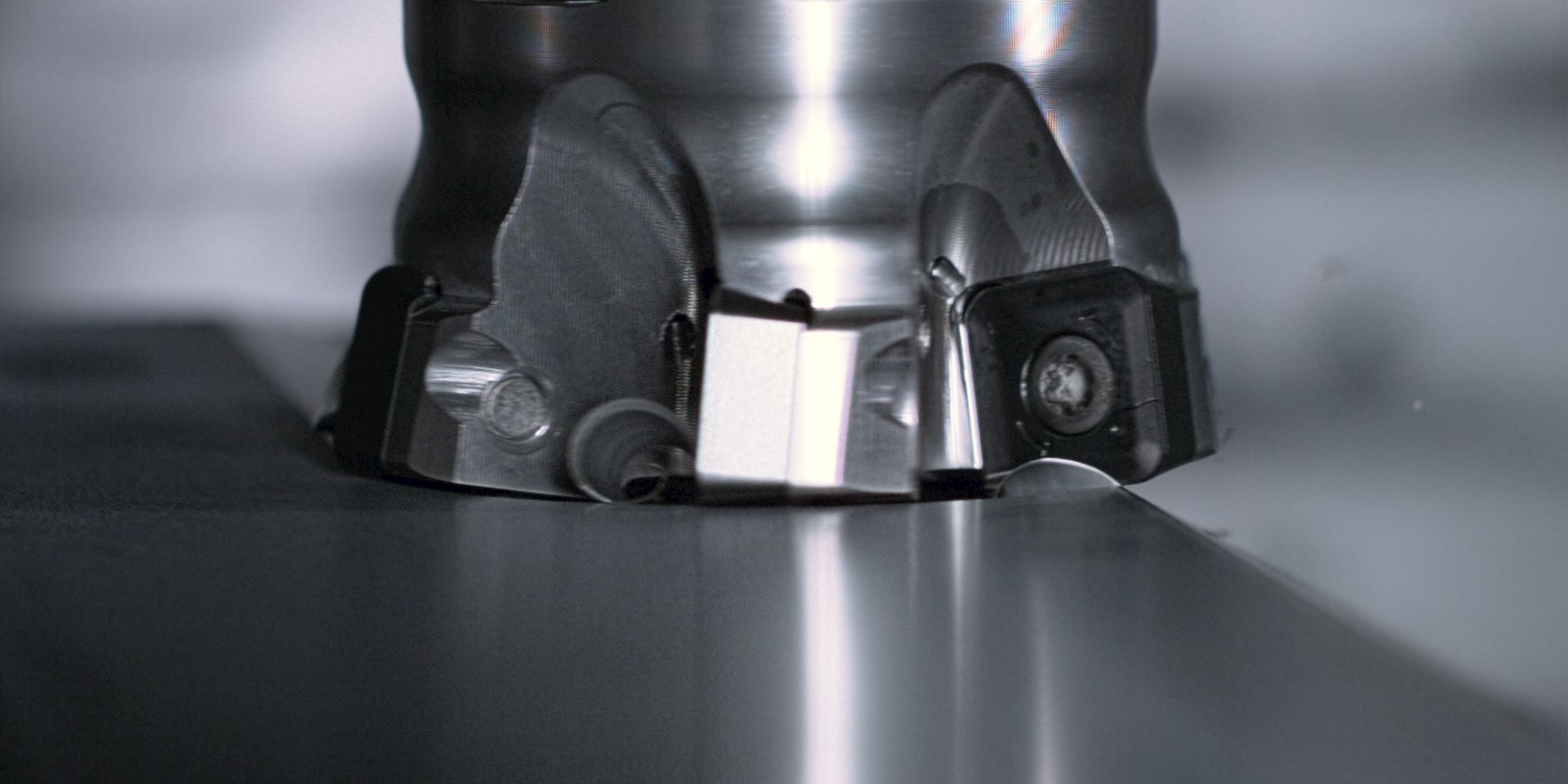
High Feed Machining (HFM): “Surge Ahead with Rapid Feed Rates and Flawless Finishes!”
When it comes to high feed rates with large radial engagements and small axial depths, HFM is the go-to strategy. Compared to general machining, this technique allows for high metal removal rates and superior surface finishes, thanks to its increased table feed. The advantages of HFM extend to user-friendliness, ease of programming in CAM, and safety. Even without extensive programming experience, complex forms can be relatively easily programmed. It is an ideal roughing operation for most materials and finds applications in deep pocket machining.
These tools have specially developed front teeth, giving these cutters a very short cutting length.
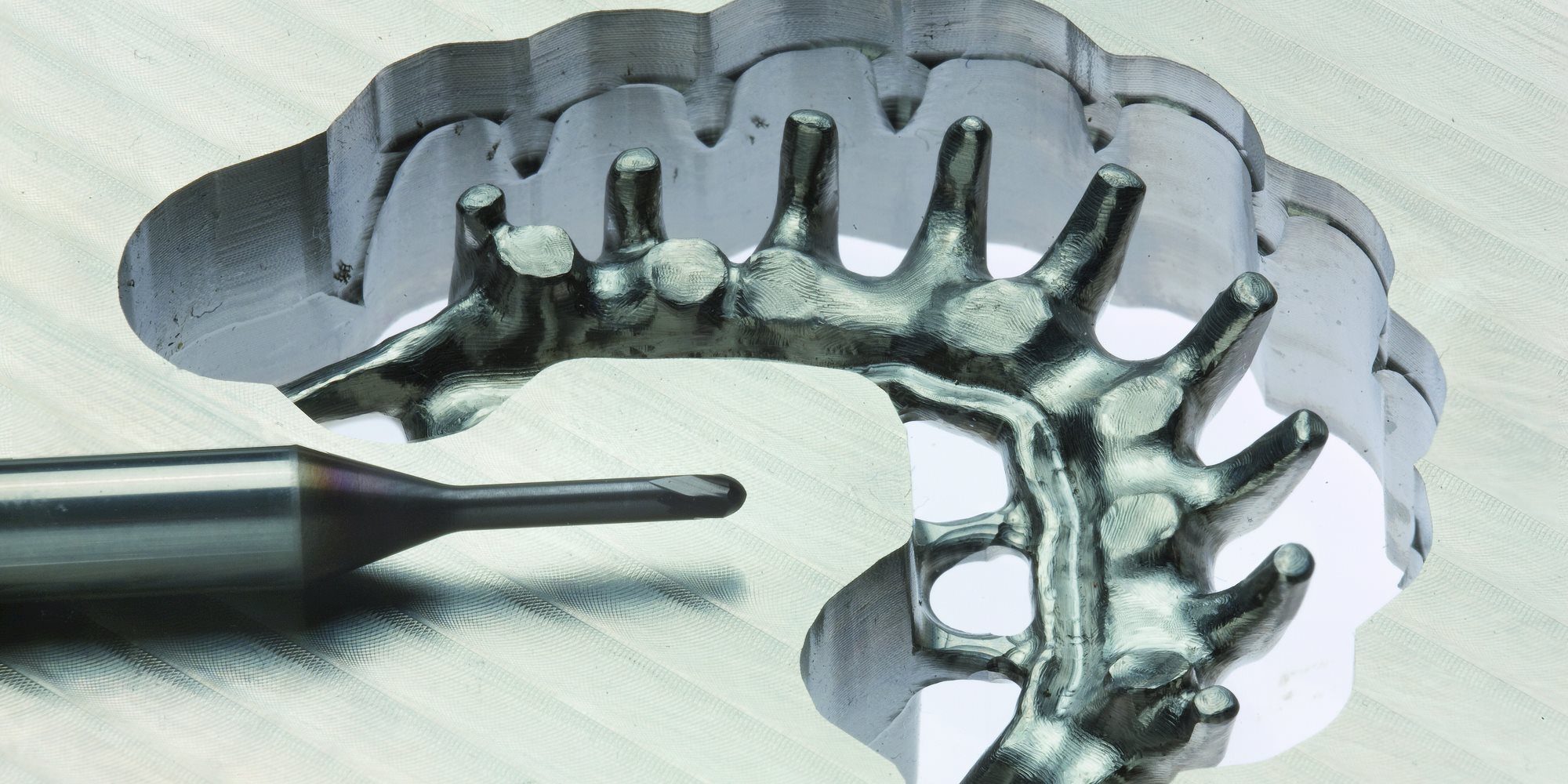
Micro-machining is the unsung hero of CNC, using tiny tool diameters (Ø 0.1 to 2.0 mm) for precision-critical applications. With meticulous craftsmanship, it creates intricate cavities in various materials. Precision and stability are crucial, requiring high spindle accuracy, RPM control, and thermal stability. From medical to electronics, micro machining plays a vital role in modern technology.
The tools used in this specialized strategy involve using incredibly small tool diameters ranging from Ø 0.1 to 2.0 mm. Despite their diminutive size, these tiny tools wield mighty precision, crafting intricate components with immaculate detail.
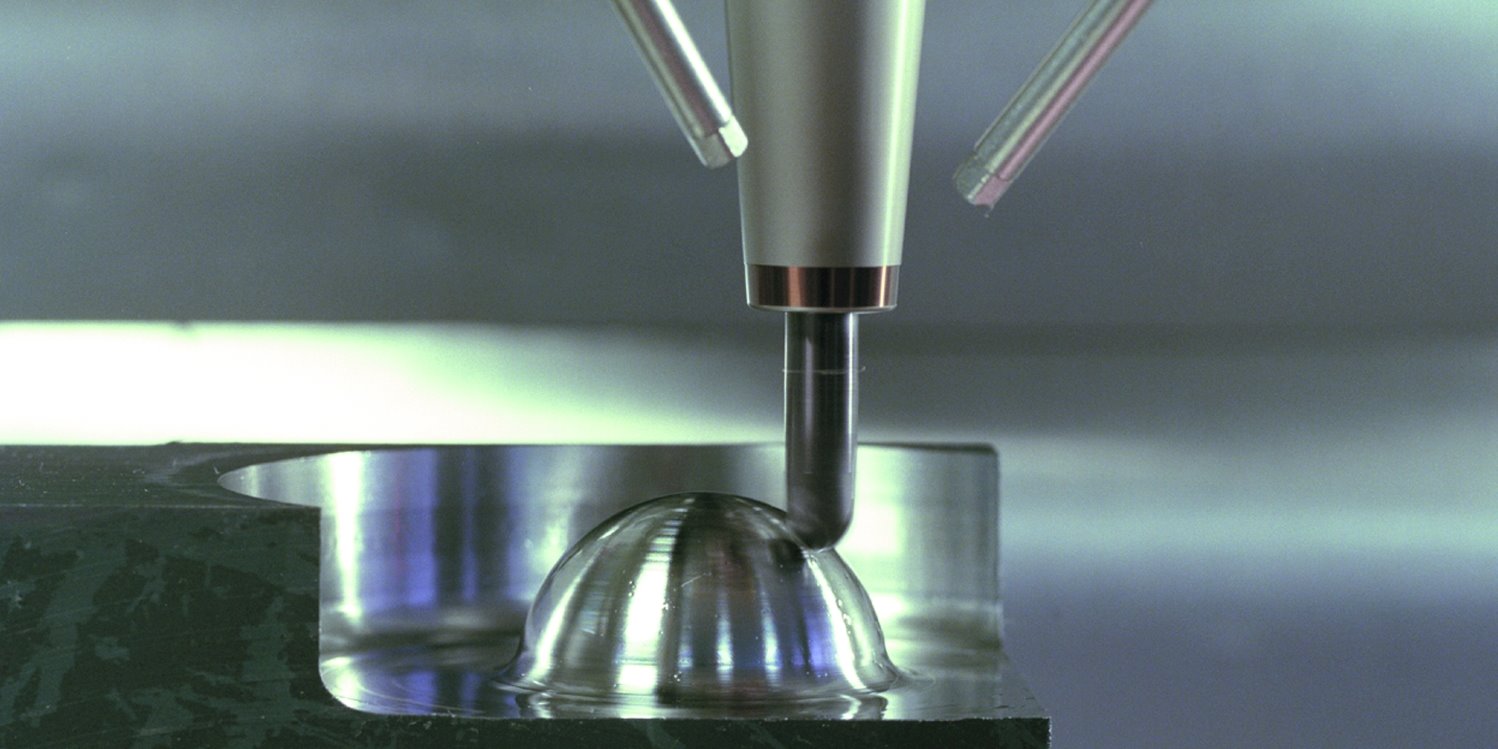
High-Speed Machining (HSM): “Swift and Precise - Where Speed Meets Perfection!”
HSM strategy combines a small radial depth of cut with high cutting speeds and table feeds. The result is remarkable metal removal rates and superior surface finishes compared to general machining. The hallmarks of HSM are the comparably low cutting forces, reduced heat buildup in both tool and workpiece, minimal burr formation, and high dimensional accuracy. Quick CNC control, high RPM, and rapid transmission to the axis are necessary CNC machine requirements. HSM shines in the Mold & Die industry for pre-finishing and finishing operations on hardened steel (48-62 HRc) with short lead times. Additionally, it can be applied effectively to most other materials with the right tool and advanced machining method.
Stable tools with well-formed chip space and coatings are recommended to fully leverage this technique.
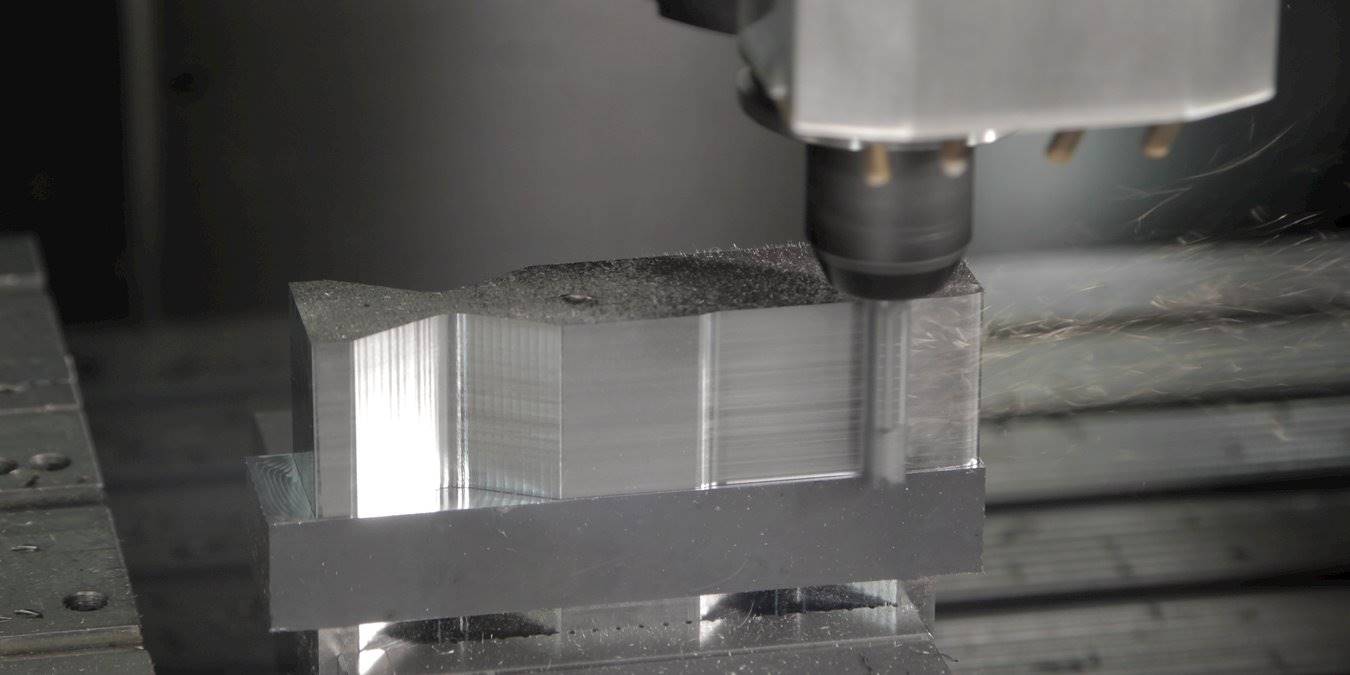
With so many names for this advanced roughing strategy, such as Optirough, Dynamic Milling, Adaptive Roughing, and many more, this strategy is designed with precision and productivity in mind. By employing well-defined tool paths with constant arc of contact, we ensure reliable roughing of both simple and complex shapes. The combination of large axial depths (ap), small radial depths (ae) of cut, high feeds per tooth (fz), and cutting speeds (Vc) leads to exceptional productivity. Reducing the arc of contact minimizes heat generation during roughing operations, allowing for higher cutting speeds and shorter cycle times. Our CAM-based rough-machining approaches center on the cutting tool’s arc of contact and its average chip load, resulting in impressive performance and efficiency.
Although most people generally use solid carbide endmills with this strategy, the truth is you can use an indexable milling cutter too! That’s because this strategy is all about utilizing your CAM software to maximize your milling tool’s full potential.
In this article, you’ve explored a variety of advanced milling operations and learned about cutting-edge techniques that can elevate your machining skills. By incorporating these methods into your repertoire and gaining hands-on experience, you’ll unlock the true potential of milling tools.
As we conclude this three-part series, “Unveiling the Secrets of Machining: Beginners Guide to CNC Milling Operations and Strategies”, we hope you have gained invaluable insights into the Secrets of precision metalworking. From general machining to micro-machining, HSM, and advanced roughing, each strategy offers unique advantages and applications.
Remember that practice, patience, and attention to detail are key to becoming a skilled machinist. Armed with this knowledge, you are well on your way to mastering the art of precision metalworking.
Roughing and Finishing: Your Power Duo
Milling tools are excellent for both roughing and finishing operations. Their combination of strength and sharp cutting edges allows for rapid material removal during roughing, while their ability to maintain high precision ensures superior surface finish during finishing passes. This versatility makes milling tools indispensable in machining, enabling manufacturers to optimize productivity and achieve impeccable results.
As we conclude the first part of our three-part series, “Unveiling the Secrets of Machining: Beginners Guide to CNC Milling Operations and Strategies,” we have witnessed the incredible potential of milling tools and their indispensable role in shaping the manufacturing industry. From face milling and peripheral milling to drilling and contouring, the versatility of milling operations has proven unmatched in delivering precise and efficient results.
Stay tuned for the second part of the three-part series, where we will delve further into advanced milling operations and cutting-edge innovations that continue to push the boundaries of milling capabilities. Join us as we pave the way to an even brighter and more innovative future for manufacturing. The power of milling tools awaits, ready to unlock new possibilities and elevate your machining endeavors to unparalleled heights!
Inline Content - Survey
Current code - 5fce8e61489f3034e74adc64