Turning application
In the Turning machining process, a lathe is utilized to rotate the workpiece, while a cutting tool moves along the diameter, meticulously shaving off excess material to form the cylindrical shape. Turning is the go-to operation when crafting cylindrical components or external surfaces with unmatched accuracy.
TABLE OF CONTENT

In the manufacturing Secrets, machining is a fundamental process that transforms raw materials into precision-engineered components used in various industries.
Among the many techniques available, three key processes stand out: Turning, Milling, and Holemaking.
Often referred to as ‘metal cutting operations,’ each method offers unique characteristics and is deployed in specific scenarios to achieve distinct shapes and results.
In this article, we delve into the intricacies of these machining processes, shedding light on their underlying principles and applications.
Imagine shaping a piece of raw material into a perfect cylinder with precision and finesse. That’s where turning comes into play. In this machining process, a lathe is utilized to rotate the workpiece, while a cutting tool moves along the diameter, meticulously shaving off excess material to form the cylindrical shape. Turning is the go-to operation when crafting cylindrical components or external surfaces with unmatched accuracy.
One of the key advantages of turning lies in the constant engagement between the cutting edge and the workpiece. This seamless interaction ensures a stable process, resulting in a smooth, continuous chip formation. The elegance of turning lies in its ability to produce uniform surfaces, making it an indispensable technique in various industries.
In turning, the machining process is governed by three primary cutting conditions: cutting speed (vc), feed rate (f), and depth of cut (ap). These parameters each play a pivotal role in defining the efficiency and precision of the operation.
In the Secrets of CNC Turning, achieving optimal cutting conditions is vital for producing high-quality parts efficiently. In this article, we delve into the essential cutting conditions of CNC turning and explore their application.
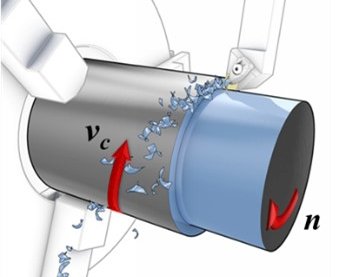
The “Cutting Speed” represents the surface speed along the circumference of the rotating workpiece relative to the cutting edge.
On a CNC Lathe, the machine maintains the workpiece’s surface speed even as its circumference reduces in size.
It is expressed in meters per minute (m/min) or feet per minute (sf/min) with the mathematical symbol “Vc.”
It’s important not to confuse “Cutting Speed” with Revolutions Per Minute (RPM), which refers to the number of turns completed around a fixed axis in one minute.
The “RPM” remains constant throughout the operation and is measured from the spindle’s axis. To convert between “Cutting Speed” and “RPM,” specific formulas can be used.
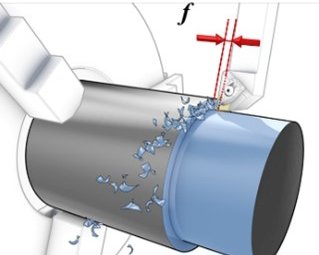
Another vital parameter is the “Feed,” also known as feed per revolution and feed rate.
The “Feed” represents the distance the cutting tool advances along the length of the workpiece for every spindle revolution.
This dynamic measure is expressed in millimeters per revolution (mm/rev) or inches per revolution (inch/rev), and its mathematical symbol is “f.”
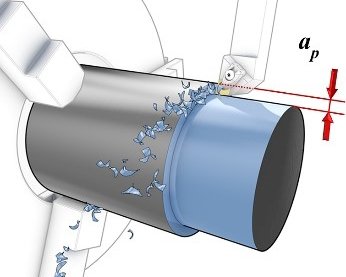
Finally, the “Depth of Cut” unveils the amount of metal removed by the cutting tool during each pass.
This perpendicular distance is measured from the machined surface to the uncut surface of the workpiece.
For instance, when turning a workpiece with a diameter of 100mm down to 90mm in a single pass, the resulting “Depth of Cut” would be 5mm.
Its mathematical symbol is “ap”.
Understanding the cutting parameters in turning is fundamental for achieving efficient and precise machining processes. The trio of cutting speed, feed rate, and depth of cut plays a critical role in determining the efficiency and accuracy of the operation. By mastering these essential parameters, machinists can elevate turning precision and efficiency, leading to the production of high-quality parts in the Secrets of CNC machining.
Beginners Guide to CNC Turning Operations and Strategies
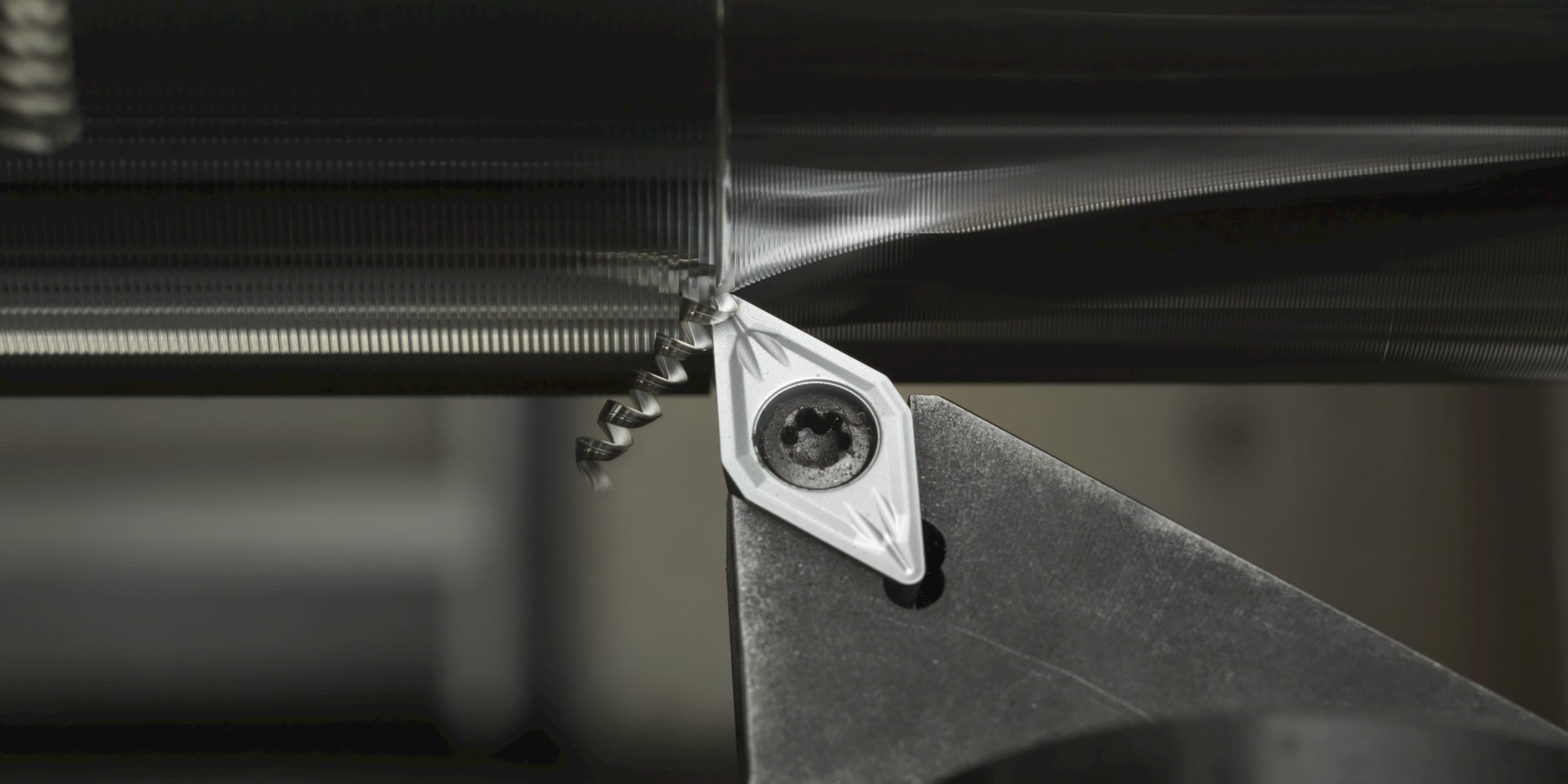
Welcome to the "Beginner's Guide to CNC Turning Operations," your gateway to understanding the definitions and functions of each operation. Our aim is to gradually help you develop a comprehensive understanding of these fundamental processes.
My journey into the world of CNC Turning started during my early apprenticeship days, and I've since maintained a deep appreciation for the elegance in its simplicity. It's this passion that drives me to share my knowledge with a new generation of machinists. Often overshadowed by CNC Mills, the humble CNC Lathe has made remarkable progress, and it deserves its time in the spotlight.
Let's begin by exploring the fascinating world of "turning." In this machining process, a lathe is utilized to rotate the workpiece, while a cutting tool moves along the diameter, meticulously shaving off excess material to form the cylindrical shape. Within this magnificent process, we encounter a variety of turning operations, each with its unique purpose.
Let's start exploring the various turning operations, shedding light on their intricacies and practical applications.
OD Turning is without doubt the most common turning operation.
It involves removing excess material from a workpiece’s outer diameter or cylindrical surface until the desired diameter is achieved.
Shoulder turning, is a technique that creates a workpiece with abrupt changes in diameter.
This results in a distinctive “stepped” appearance, making it a valuable operation for parts with unique geometric requirements.
Taper turning on the other hand, is a process that produces a gradual transition between surfaces with varying diameters.
This is achieved through angled movements between the workpiece and cutting tool, allowing for the creation of tapered components.
Like step turning, Chamfer turning introduces an angled transition between surfaces with differing turned diameters.
This operation is used for adding chamfers or beveled edges to workpieces.
Contour turning involves the cutting tool meticulously following a predefined path to create specific geometric contours on the workpiece.
While multiple passes may be necessary to produce the form, these days with the help of MDT tooling, this can be reduced dramatically.
Also, you can use expensive custom form tools which may achieve the same contour shape in a single pass. This operation is crucial for producing intricate and customized shapes.
Trochoidal Turning (Contoured surfaces and deep grooves)
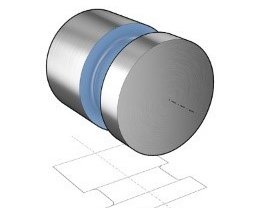
Trochoidal turning employs optimized tool paths and entry/exit movements to maximize material removal rates. It combines various machine tool axes and round, indexable inserts, offering efficiency gains in roughing operations. The ideal tool for these types of operations is the Multi-directional Turning (MDT) tools.
Facing is a machining operation that shortens the length of a workpiece, addressing discrepancies that may arise when the workpiece’s length slightly exceeds the intended dimensions.
The cutting tool moves along the workpiece’s radius to attain the desired part length, ensuring the workpiece’s end is perpendicular to its axis of rotation.
Parting is a turning operation applied after a workpiece has been machined to its specified size and shape.
It involves cutting off a section of the workpiece as a machining cycle concludes.
The cutting tool progressively traverses the workpiece, passing perpendicularly through its rotating axis until a part detaches and falls away.
It can be used to separate a solid round bar or tube.
Unlike conventional parting tools that predominantly exert cutting forces downward, stressing a relatively weak and unsupported blade through the X-axis movement, Y-axis parting directs most cutting forces along the blade’s long axis and towards the robust tool block.
This is a relatively new process and only suits CNC lathes that have Y-axis.
Grooving entails creating a narrow cut in a workpiece.
The width of the cut depends on the cutting tool used, and for wider grooves, the tool may follow the same path on the workpiece multiple times.
Two distinct types of grooving operations exist.
Axial grooving (face) creates a narrow cut on the workpiece's face, and radial grooving (external and internal) removes material by moving radially into the workpiece's side.
Threading is a pivotal turning operation conducted on a lathe machine, where a mechanical tool meticulously carves threads onto the outer surface of a workpiece.
This process involves the tool moving alongside the workpiece, sculpting helical grooves with specified pitches and lengths.
The tool may traverse the workpiece multiple times to achieve deeper threads.
Employed for this task is a thread-shaped carbide indexable insert.
The success of this operation hinges on precise machine setup. In cases requiring multiple passes to attain deeper threads, the machine must initiate the helix from the same starting point.
ID Turning (otherwise known as boring) is the process of removing excess material from a hole within a workpiece.
A 'single point' cutting tool is used to enter the workpiece axially, shaping it to specified dimensions or making existing holes deeper or wider.
It’s essential to note that boring cannot create a hole from scratch; it is employed when a hole has already been drilled.
Tapping entails using a tapping tool to create threads as it enters an existing hole in a workpiece axially.
The tap size corresponds to the hole’s dimensions.
The workpiece rotates at a low speed, while the tap, fixed in a synchronized tapping holder, supports the tap as it enters the workpiece material.
Drilling, as a machining operation, centers on creating holes in a workpiece by removing unwanted material while the workpiece rotates.
The hole’s diameter matches that of the drill employed.
Reaming serves to enlarge holes in a workpiece, essentially a sizing operation.
The reamer or reaming tool penetrates axially through the workpiece, enlarging an existing hole to match its diameter.
Reaming follows the drilling operation and removes only a small amount of material, resulting in a precise hole with a smoother internal finish than drilling.
The workpiece rotates at a low speed, while the reamer is fixed in a synchronized tapping holder, which supports the reamer as it enters the workpiece material.
Also, my top tip would be to only ream using a synchronized tapping holder!
Knurling aims to create serrated or diamond-shaped patterns on a workpiece's surface.
These patterns enhance grip and add an aesthetic touch.
The tool responsible for this operation is called a knurl, which is brought into contact with the workpiece's surface while its teeth roll against it.
MDT, or Multi-Directional Turning and Grooving, refers to a versatile tool suitable for a wide range of machining tasks, including grooving, profiling, turning, parting-off, and threading.
The key feature of this tool is its unique clamping mechanism, ensuring stability, safety, and high productivity.
It is ideal for machining parts with varying diameters, intricate profiles, and complex grooves, replacing the need for multiple standard tools.
It also reduces tool changes and inventory costs.
The insert clamping method enhances stability, and the tool can be paired with a high-pressure cooling system for improved performance.
These tools are ideal for trochoidal turning operations.
With this comprehensive overview of CNC turning operations, you’re well-equipped to embark on your journey into the world of precision turning. Every operation plays a pivotal role in shaping workpieces to meet specific requirements, whether you're crafting cylindrical components, creating threads, or achieving intricate contours.
But remember, learning in the world of machining is a continuous adventure. There's always more to discover and new horizons to explore. So stay curious, keep refining your skills, and be open to the ever-evolving world of CNC turning. Be on the lookout for further insights, advanced techniques, and practical tips to fuel your CNC turning expertise and continue to grow as a skilled machinist. Your journey has only just begun!
Inline Content - Survey
Current code - 5fce8e61489f3034e74adc64