How to Select the right Turning Grades according to Materials and Solutions
Whether you’re involved with general ISO turning, hard part turning, grooving, parting or threading, choosing the turning grade for the material and application can be essential to obtain your desired outcomes. Proper grade selection also provides opportunities to optimize machining efficiency, sustainability and productivity.
Seco turning grades and geometries cover all material groups, allowing you to achieve improved removal rates, tool life and surface finishes regardless of the application.
Seco offers turning grades to support inserts of different shapes, sizes and thicknesses. Each of our grade solutions is designed to achieve the desired removal rates, tool life and surface finish for productive, sustainable machining.
Carbide – Tungsten carbide is nearly twice as dense as steel and provides excellent wear resistance at high cutting speeds and feeds and high thermal temperatures. With a relatively low initial investment, specially coated carbide tooling is a cost-effective option for sustainable manufacturing and an effective solution for most materials, including steel, stainless steel, heat resistant superalloys (HRSA) and some hardened steel applications.
PCD – Polycrystalline diamond is produced by sintering diamond particles under high heat and pressure to form tools that combine the hardness, abrasion resistance and thermal conductivity of diamond with the toughness of tungsten carbide. PCD coated inserts are suitable for machining non-ferrous metals and alloys such as aluminum, copper, brass and bronze. They can also be used for titanium alloys, ceramics, graphite, reinforced plastics and composites.
PCBN – Polycrystalline cubic boron nitride is sintered at extremely high pressure and temperature into a highly wear-resistant material with properties similar to diamond. Due to its hot hardness, oxidation resistance and fracture toughness, PCBN inserts provide excellent edge strength and long tool life. PCBN is suited for machining hardened steel, pearlitic grey cast iron, chilled and white cast iron, manganese steel, cemented carbide, powder metallurgy alloys and nickel-based superalloys (InconelÒ 718).
Ceramic – Ceramics include a range of products that are die-pressed and sintered to provide high thermal shock resistance and excellent wear properties for advanced manufacturing. Seco ceramic inserts are designed for stable, high-speed rough machining of nickel-based HRSAs such as InconelÒ 718 or similar materials as Hastalloy and Udimet.
Cermets – Cermets is an abbreviation of “Ceramic-Metals” and a cutting material category of cemented tungsten carbide that provides exquisite surface-finishes with inherent wear-resistance due to the chemical resistance of predominately hard-carbide mixes with other crystallography.
Understanding the diversity of Seco turning grades’ strengths and alignments will help guide you to the best choice for the material you are machining.
Our General Grade Mapping chart below will help optimize your application with the appropriate combination of grade and geometry.
This chart provides an overview of most turning grades in the context of workpiece material. The chart also shows basic grade toughness, as well as geometric characteristics for sharpness and strength. Based on workpiece material, you can identify suitable grade/geometry combinations as a first orientation. You can also see the various types of materials a grade can machine as well as suitable geometry matches.
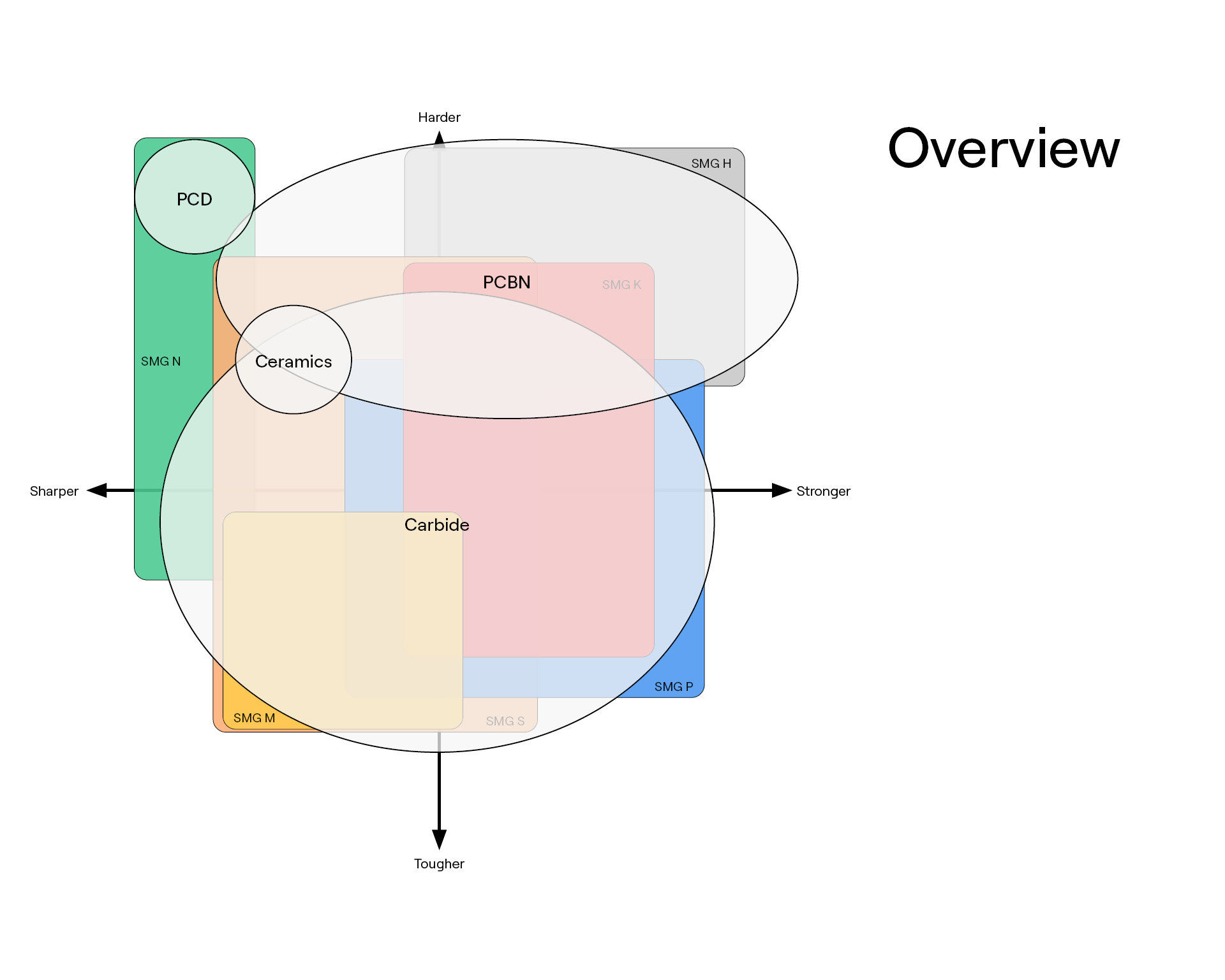
From top to bottom, the chart arranges grades by increasing toughness, with the toughest grades indicated at the bottom. Tougher grades can handle higher chip loads and enable the use of sharper geometries, work with interrupted cuts or vibrations, heterogenous workpiece conditions, and machine in inclusions with less edge chipping and disruption. Tougher grades also have fewer issues with the thermal cracking and notch wear that can be challenges in turning. The drawback with tough grades is that they tend toward higher flank, crater wear and plastic deformation, which require an adjustment toward the harder, more wear-resistant grades shown at the top of the chart.
Find out more about tool wear patterns
Insert geometry significantly impacts the way a turning grade behaves and wears. A hard grade paired with an overly sharp geometry will easily chip and fracture during extreme interrupted cuts or when encountering inclusions. Conversely, an insert with a tough grade and heavily protected geometry can sustain excessive tool wear due to extreme thermal and abrasive conditions.
Seco provides a starting point for grade and geometry based on material groups. Once the starting point is determined, further optimization can be achieved. Seco’s digital catalog and the Seco Suggest online application provide this information.
Click on the workpiece material to find the most suitable Seco turning grade and geometry combinations for your application.
Inline Content - Gridded Links
Tags: 'turning_grade_iso_p', 'turning_grade_iso_s', 'turning_grade_iso_m'
Max links: 3
Inline Content - Gridded Links
Tags: 'turning_grade_iso_h', 'turning_grade_iso_k', 'turning_grade_iso_n'
Max links: 3
Seco grades are designed for a wide range of uses, but no grade is suitable for every application or every purpose. The proper turning grade depends upon workpiece materials; part size and shape; application and machining conditions; and the desired outcome. High tolerances and exacting results will require deeper analysis of those considerations.
Learn more about the Nomenclature
Grades are more suited to one material than others, and the first step in selecting a turning grade is considering the material to be machined. For example, coated cemented carbide is a suitable choice for most steels and stainless steels. However, there are no hard and fast rules for grade selection. In some cases, wear patterns and results may require you to optimize to an alternative. Though PCBN might be a first choice for heat-resistant super alloys and hardened steels, cemented carbide might be more suitable for those materials under certain circumstances.
Similarly, while non-ferrous metals and plastics are generally easy to turn, the addition of specific requirements and desired outcomes could make them a challenging application that ultimately require diamond based cutting materials such as a PCD grade.
To make the process easier, The Seco Materials Group v2 provides a quick, comprehensive reference guide for materials and cutting data. You can also contact a Seco expert for advice.
Once component material is analyzed, machined part size, shape and features is the next consideration for grade selection. A large, rigid part, for example, will generally require long in-cut times to remove large amounts of material relative to small, thin components that may need fast, one-hit cuts.
Depending upon machining conditions, the optimal grade selection for turning small and large parts may be the same. The choice will lie at a point along the tool wear-to-toughness spectrum that balances desired outcome with sustainability.
The characteristics and capabilities of the machines on your shop floor influence your turning grade choices. All-round, general-purpose machining will determine a different grade selection than that for a very particular application. Similarly, grade selection will be different for close-tolerance features with high-quality surface finishes under difficult machining conditions for aerospace applications than that used for less critical applications. Discussing the right choice for various applications and machining conditions with a Seco expert will make selecting the right turning grade easier.
Finally, you must consider the desired outcome of the process. For instance, does a specific step in the machining process involve finishing, roughing or medium cuts? In many cases, this analysis involves considering several competing factors: required surface finish, material removal rate, reliability, process security, machine capability and overall shop production strategy. A Seco expert can help you balance the variety of factors necessary to selecting the proper turning grade for your application.
Finish turning aerospace turbine blade discs made from titanium or Inconel® require high-quality precision tools specifically designed for those materials to achieve tight part tolerances and required surface finishes. Using Seco PCBN or carbide inserts optimize the process in terms of time and cost while ensuring tolerance and surface finish requirements are met.
Inline Content - Gridded Links
Tags: 'suggest', 'secoassistantoptimizer', 'secoassistantcompare'
Max links: 3
Specific tool and grade recommendations can also be found on Seco Suggest, a comprehensive online resource that will help optimize your machining process. Cutting strategies, tool selections based on material, features and desired results as well as alternative solutions for specific requirements can be found here.
Inline Content - Survey
Current code - 5fce8e61489f3034e74adc64