Medical Shoulder
See details here
We machined a titanium shoulder joint utilizing advanced five-axis milling and simultaneous turning to achieve precision and efficiency.
To watch the demo, fill in this form now and instantly get 5 additional machining demos
Inline Content - Sugar Form
Sugar Form url - https://info.secotools.com/acton/fs/blocks/showLandingPage/a/45194/p/p-00dc/t/page/fm/0
Frame height - 650 px
An aging population and advances in medical and material technologies are driving the demand for orthopedic joint replacement components. Shoulder replacements and reverse shoulder replacement procedures are anticipated to increase substantially by 2040. This, in turn, will present market entry and economic growth opportunities for medical manufacturers. However, the sheer number of required shoulder arthroplasty components also presents unique manufacturing challenges that must be addressed to meet the ever-increasing demand.
From a manufacturing standpoint, orthopedic implants require extremely tight tolerances and exceptional surface finishes. The success of a shoulder replacement depends not only on the medical procedure but the quality of the orthopedic components as well. Manufacturing defects, however small, can result in a negative outcome for the patient. In addition to machining with a high degree of precision, the growing demand for shoulder components will also spur the need for unmanned, lights-out production to make the necessary quantity of components in a manner that is sustainable and cost-effective for the manufacturer.
Also, modern shoulder implant components have moved away from cobalt-chrome to titanium. Titanium material is more readily accepted by the body for bone ingrowth. However, when we talk machining, turning and milling titanium can be challenging if the incorrect approach is taken.
The humeral stem connects the arm to the ball and socket joint and requires processing difficult-to-machine titanium while maintaining high accuracy and exceptional surface finishes. Historically, humeral stems were forged then machined to shape. That process, however, presented production challenges such as multiple setups on multiple machines, downtime and inefficiency, decreased accuracy and unacceptable surface finishes. The current trend, however, is to use a single 5-axis, dual-spindle mill/turn machine with B-axis capability to rough round titanium bar stock into concentric shape then perform necessary finishing operations.
Seco has developed an entire process including design and programming strategies, machining, tooling and workholding solutions based on this single-multitasking machine processing strategy for unmanned production. Using this strategy, manufacturers overcome several industry challenges, such as reducing the need for skilled labor, to meet the production challenges while improving accuracy, maintaining required surface finishes and ensuring quality control for regulatory compliance. Advanced multitasking machine technology also streamlines production of these complex parts and enables manufacturers to keep pace with advances in material technology.
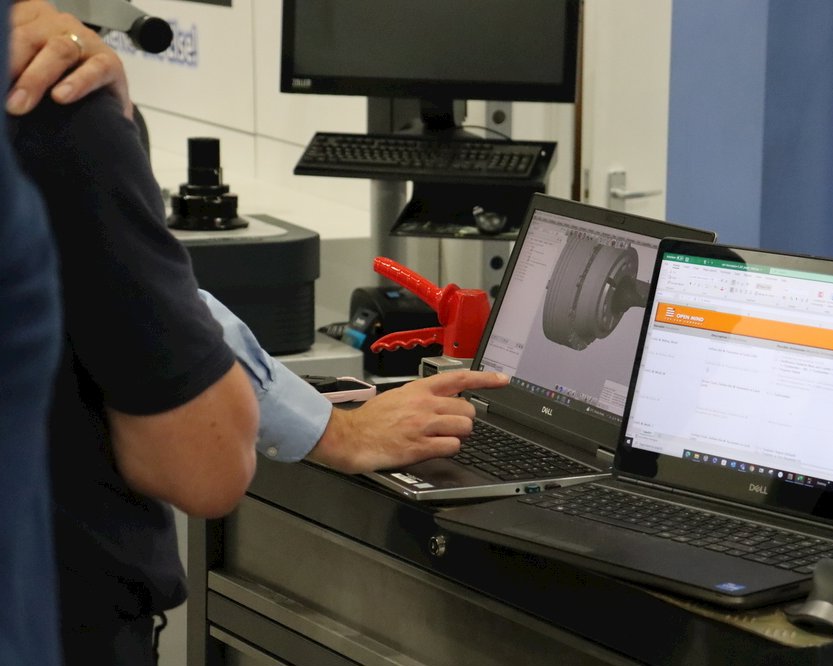
Due to the complexity of the shoulder implant shape, high tolerance and critical surface finish are required.
Therefore, bespoke workpiece holding was introduced with partners allowing advanced roughing strategies to be implemented for both milling and turning on a 5 axis Millturn.
Incorrect machining of titanium will cause a factor of things: Stringy, tangled nests of chips/swarf wrap around the workpiece and tooling, marring surface finishes and reducing tool life. Work hardening can cause component brittleness and other adverse characteristics, vibration and chatter that impact surface finish and increase cutting forces, which all leads to inconsistent and reduced tool life.
To avoid these issues, advanced roughing, which can be termed as high feed turning, was implemented with careful selection of grade, edge preparation and coating for this challenging material. The addition of Jetstream toolholders allowed us to increase data while maintaining part quality, effectively enhancing chip formation, preventing stringy swarf and controlling heat generation.
As a result, cutting is improved by lifting chips away from the rake face and reducing the heat load. In addition to producing a better finish, tool life is extended, allowing manufacturers to maintain a stable, sustainable and predictable process. Predictability and stability also improve automated, unmanned part processing as tool changes can be anticipated and scheduled for uninterrupted machining.
Milling the humeral stem’s connection face requires precision milling with extremely tight surface finish tolerance control. An advanced roughing strategy was chosen utilizing the JS750 series high-performance solid carbide square shoulder end mills and ball nose cutters.
This range is optimized for challenging materials with proven geometries and coatings, often improving tool life by 25 to 40%. An advanced roughing strategy will also reduce the tool inventory list for these components. Reconditioning of these tools is also available, allowing the manufacturer to amortize costs and reduce the Cost Per Part further.
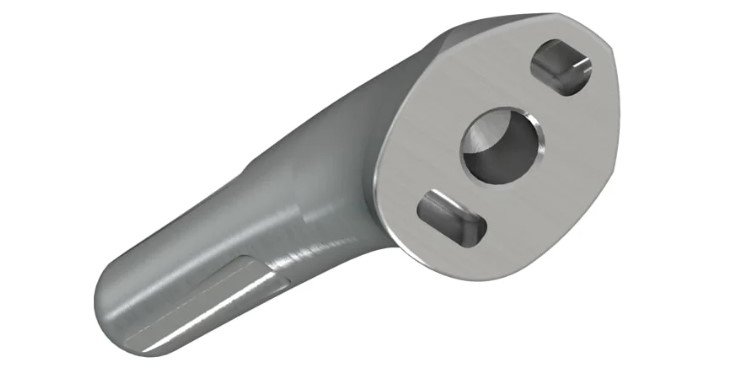
For decades, Seco has collaborated with industry leaders, partners, leading universities and research institutes throughout the world allowing us to build a strong foundation of insight and expertise in the medical manufacturing sector. Seco understands the challenges and demands medical manufacturers face, and we have developed standard and customized tools, technologies, strategies and component processes that will help improve and stabilize your processes around the new concepts and technologies of the ever-evolving medical field.
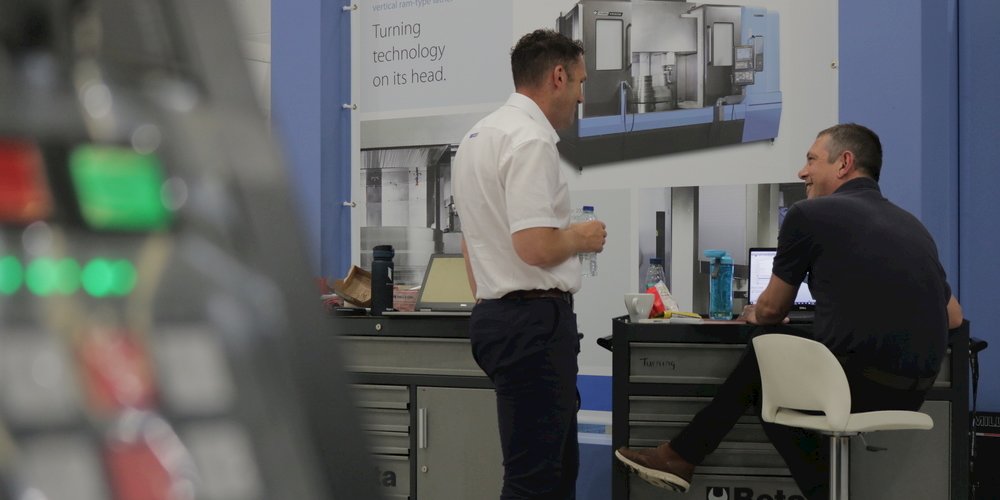
Customers rely on us to supply world-class tooling, but Seco offers so much more. We provide support and expertise that will maximize your productivity and sustainability. Tool reconditioning and inventory management solutions improve profitability and eliminate waste. Our knowledge databases and Innovation Hubs explore and develop new trends and technology, offering end-to-end solutions in the whole manufacturing process from component design to machining and verification.
And who knows what the future holds – fully robotic processes? Let’s find out and shape it together.

- Hainbuch
- Mills CNC
- Openmind
If you would like to reach out to one of our medical experts
Contact our experts here