Rejecting second best
With customers expecting costs to be kept in check, high-precision manufacturers are striving to get things right the irst time.0NE OF THE PARADOXES of the machining process is that to add value to the end component you first need to take material away. This is particularly true when it comes to highly complex and critical parts destined for high-precision uses – such as in the medical equipment, semiconductor, aerospace and defense sectors – where parts take on significant value after machining. Increasingly, producers are aiming to take away as little material as possible by using the most efficient techniques.
The development of advanced machining processes has made it easier to produce parts that were once difficult to create. There is also a trend for increased complexity in the form of combining several parts into one component. This is placing pressure on manufacturers to optimize their machining strategies to ensure accurate dimensions and tolerances as well as repeatability in the manufacturing process.
Jan Bruurs is Technical Specialist for Tooling at KMWE Group, a company that specializes in high-mix/low-volume and high-complexity machining for high-precision industries. He explains, “This trend means that greater numbers of long tools [with protruding length ≥ 5× Dc] are needed to machine these parts. To use these long tools efficiently, the tool cutter frequency must be harmonized with the dominant natural frequency of the system. The system consists of the combination of the machine tool spindle, the tool holder, and the cutting tool. Using this approach, we can achieve a first-time-right percentage for long tools of approximately 90–95 percent.”
Bruurs says it’s important for a components manufacturer like KMWE Group to work closely with tooling makers to both optimize tooling and to create tailor-made tooling solutions to achieve desired outcomes, such as producing smaller chips.
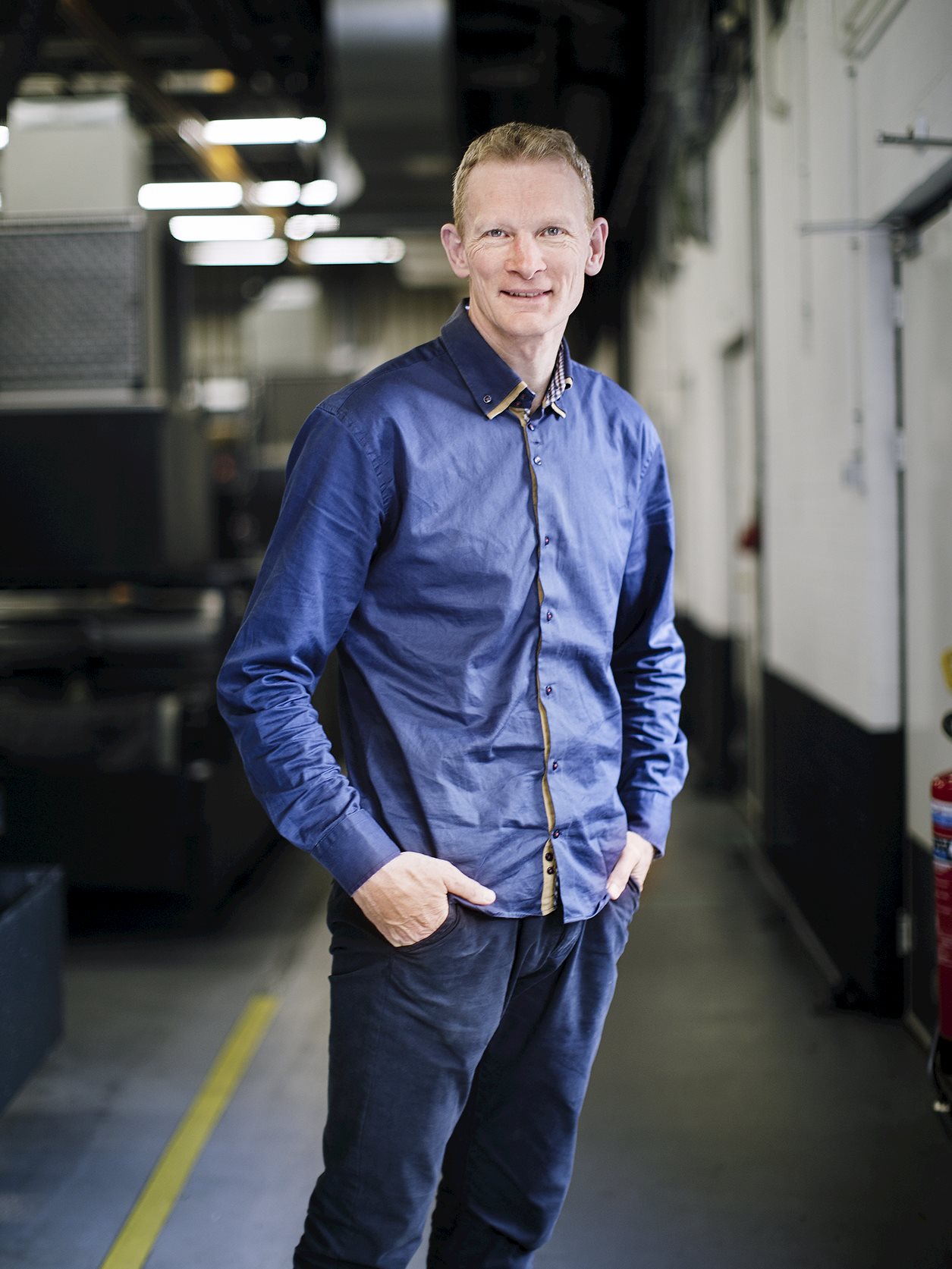
AS WELL AS the trend towards complexity, there is a push towards the increased use of lighter materials, such as titanium and its alloys, alongside the use of more familiar materials such as aluminium, stainless steel and heat-resistant steel alloys.
Bruurs explains there is also demand from customers to control and reduce costs, a factor that has led to the development of the first-time-right concept. KMWE uses dedicated software like Vericut and CutPro to simulate machining processes prior to setting up on the machining centers. “When you strive for a first-time-right approach, the better solutions aren’t always at your fingertips,” Bruurs says. “As part of our permanent quest for the better solutions, we must continually expand our knowledge of machining processes.”
Bruurs says another trend is the rise of machining of so-called ‘near-net-shaped’ components where the initial production of the item is very close to the final shape. “This is unstoppable and will become a larger part of our activities in the future,” he says. “Because these components are already close to their final shape, there’s a limited choice of appropriate machining strategies. It will be a challenge to approach these products in ways that allow them to be machined efficiently.”
Despite the challenges, Bruurs is adamant that ‘second best’ is never acceptable. “Good is the greatest enemy of better,” he says. “But that doesn’t mean you have to give up on best. You can’t change the principles of machining, but by learning to understand them, you can develop better solutions. I personally have developed an allergy to trial-and-error approaches. You should avoid this approach as far as possible. Machining is not an exact science, but when you try to approach it in a scientific way, you will most likely achieve better results.”