Axle Shaft
Typically made from carbon steel, axle shafts involve multiple turning and grooving operations. Chip control must be maintained during machining operations within fully automated production lines.
YOUR MANUFACTURING CHALLENGES
- Maintaining effective chipbreaking while copy turning the flange diameter, chamfers and back face.
- Ensuring high productivity during turning of the outer diameter and face.
- Optimising productivity while turning the undercut groove.
- Minimising cycle times while reliably turning the circlip grooves.
- Drilling numerous holes with low cycle times, high quality and reliability.
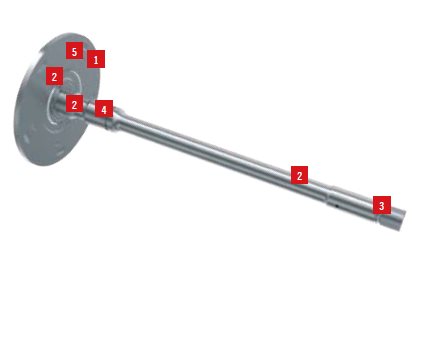
1 - Effective chipbreaking
Your Challenge: | | Maintaining effective chipbreaking while copy turning the flange diameter, chamfers and back face. |
Our Solution: | | With a top clamp and serrated contact surfaces between the insert and toolholder, Secoloc insert clamping provides the MDT system with superb stability, which is then further enhanced through the use of long inserts. The Seco-Capto interface adds tremendous flexibility, and the ability to move to full automation by adding electronic data chips to the toolholders. MDT coated carbide inserts optimize chip removal rates in this application. Your benefits include robust performance, high process security and shorter cycle times. |
Product: | | Seco-Capto™ MDT Grooving Tool |
2 - Turning of the outer diameter and face
Your Challenge: | | Ensuring high productivity during turning of the outer diameter and face. |
Our Solution: | | The flexible Seco-Capto quick change turning head system reduces tool change times and can be error-proof modified for mass production applications. Offering highly rigid and accurate performance, the system also enables full automation of presetting by adding electronic data chips to the toolholders. Additionally, using ISO/ANSI Duratomic® inserts maximizes chip removal rate for this application. The wide variety of available geometries guarantees optimal chipbreaking efficiency. Your benefits include reliable accuracy and increased efficiency. |
Product: | | Seco-Capto™ Turning Tool |
| 3 - Turning the undercut groove |
Your Challenge: | | Optimising productivity while turning the undercut groove. |
Our Solution: | | Dedicated to machining shallow grooves, Snap-Tap tools use a strong clamping system and rigid body to ensure stable, reliable and productive performance. Seco-Capto systems can be error-proof modified for mass production applications, and allow for full automation by adding electronic data chips to the toolholders. Your benefits include increasing throughput with a secure process. |
Product: | | Seco-Capto™ Snap-Tap® Grooving Tool |
4 - Turning the circlip grooves
Your Challenge: | | Minimising cycle times while reliably turning the circlip grooves. |
Our Solution: | | With a top clamp and serrated contact surfaces between the insert and toolholder, Secoloc insert clamping provides the MDT system with superb stability, which is then further enhanced through the use of long inserts. The Seco-Capto interface adds tremendous flexibility, and the ability to move to full automation by adding electronic data chips to the toolholders. MDT coated carbide inserts optimize chip removal rates in this application. Your benefits include robust performance, high process security and shorter cycle times. |
Product: | | Seco-Capto™ Turning Tool |
| 5 - Drilling numerous holes |
Your Challenge: | | Drilling numerous holes with low cycle times, high quality and reliability. |
Our Solution: | | Providing high performance the Seco Feedmax Chamfer Drill utilises the light-cutting geometry and a special edge preparation to increase process security and tool life. The tool also incorporates a low-friction coating. Your benefits include maintaining productivity in challenging, high-tolerance holes. |
Product: | | Seco FeedmaxTM Chamfer Drill |