A digital portal helps customers select the right cutting tool
Our expert Mr. Rajesh Gupta shares his views on the latest developments in cutting tools with Efficient Manufacturing Magazine.A digital portal helps customers select the right cutting tool
Our expert Mr. Rajesh Gupta shares his views on the latest developments in cutting tools with Efficient Manufacturing Magazine.
The complete know-how of the component material and machine to employ the best tool and the strategies to be used are key when considering process optimisation. Performance, reliability and consistency are the factors to be taken into consideration while selecting the cutting tool. The selected tool should deliver its best in a more predictable and defined way; it should be application-specific and according to the workpiece material. The right cutting parameters (cutting speed, feed and depth-of-cut) with the right strategy not only helps increase productivity but also minimise the machine down time and tool failures, thus reducing the cost per operation. The proper discipline to be maintained for the tool changes when it is worn-out rather than running it further, which results in tool breakage and increases the down time and tool cost. Anti-vibration system (steadyline), high coolant pressure (JET Stream) and the latest available coated grades and geometries also help in trouble-free machining and boost the productivity. Advance cutting tool materials, like PCBN and PCD multi-fold the production outputs and reduce the operation cost. The right selection of cutting parameters, grades and geometries not only does the efficient machining, but also helps to maintain the geometrical tolerances of workpiece, improves productivity and maintains the cost per component ratio. As the right selection of cutting tool and cutting parameters are the key for successful implementation, digitalization is now playing an important role as well. A digital portal helps the customer in selecting the right cutting tool and the parameter based on the workpiece material and strategy. Each day, the cutting tool industry is facing new challenges in terms of new workpiece material, more complex shapes, productivity improvement, the un-manned machining, with geometrical tolerances getting closer. For efficient machining, these materials require the latest and special carbide grades, coating and geometries; new advanced materials, like PCBN, PCD and ceramics are becoming the best alternates for improving productivity and machine efficiency.

DGM – Milling & Advance Material, India
HOMERelated content
PCBN General Turning - ISO Inserts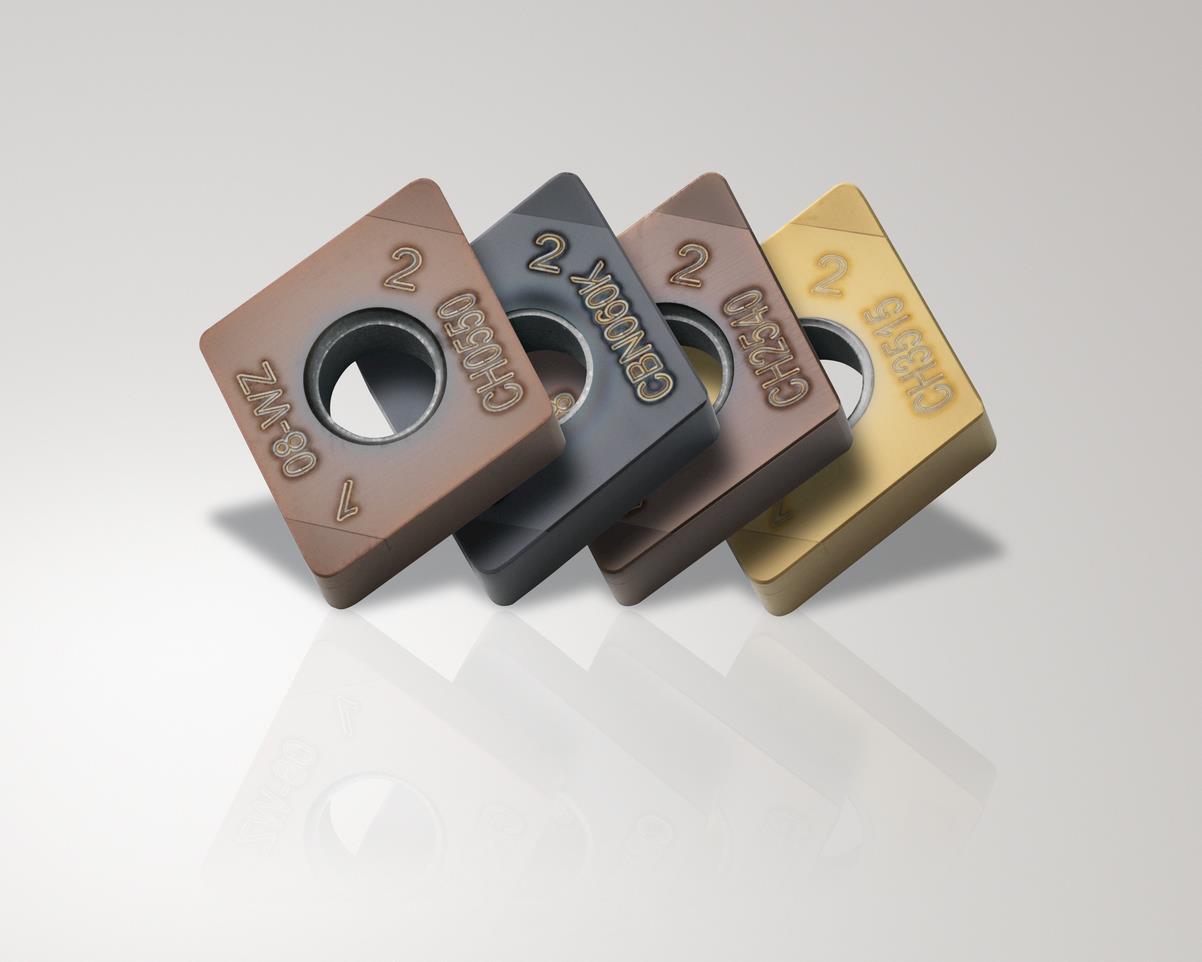
Seco expands solutions for hard turning with new PCBN grades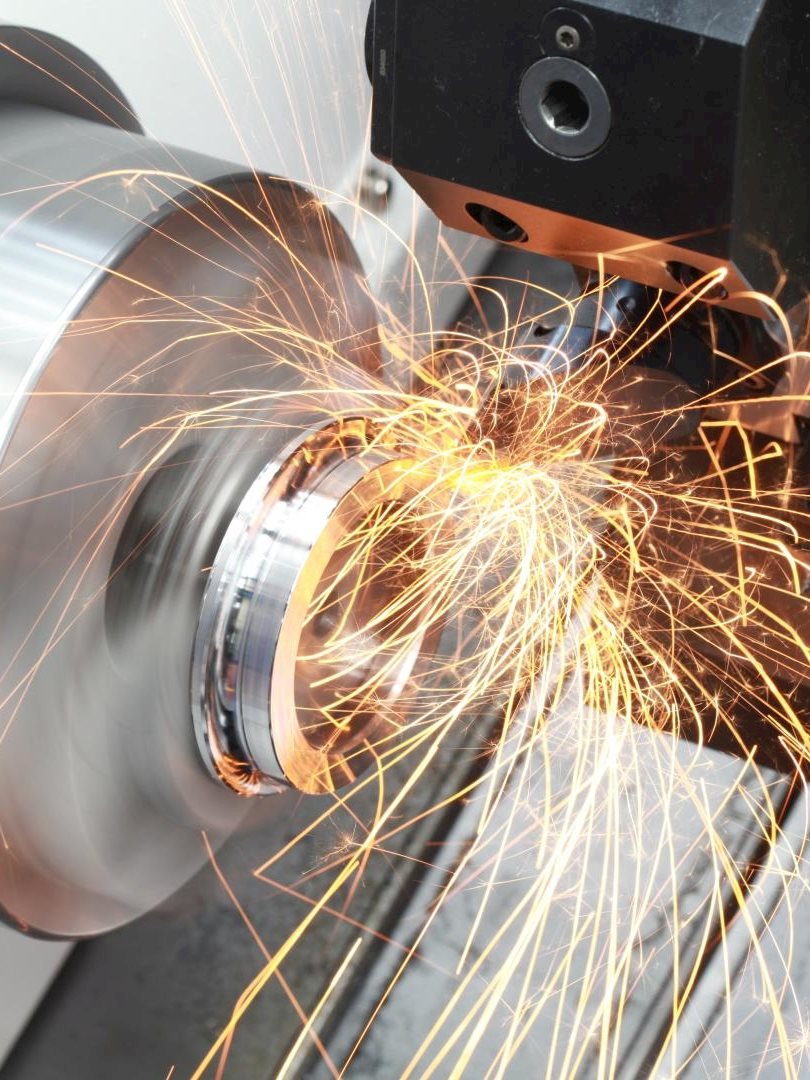
Seco CH1050/CH2581 PCBN Hard Part Turning Inserts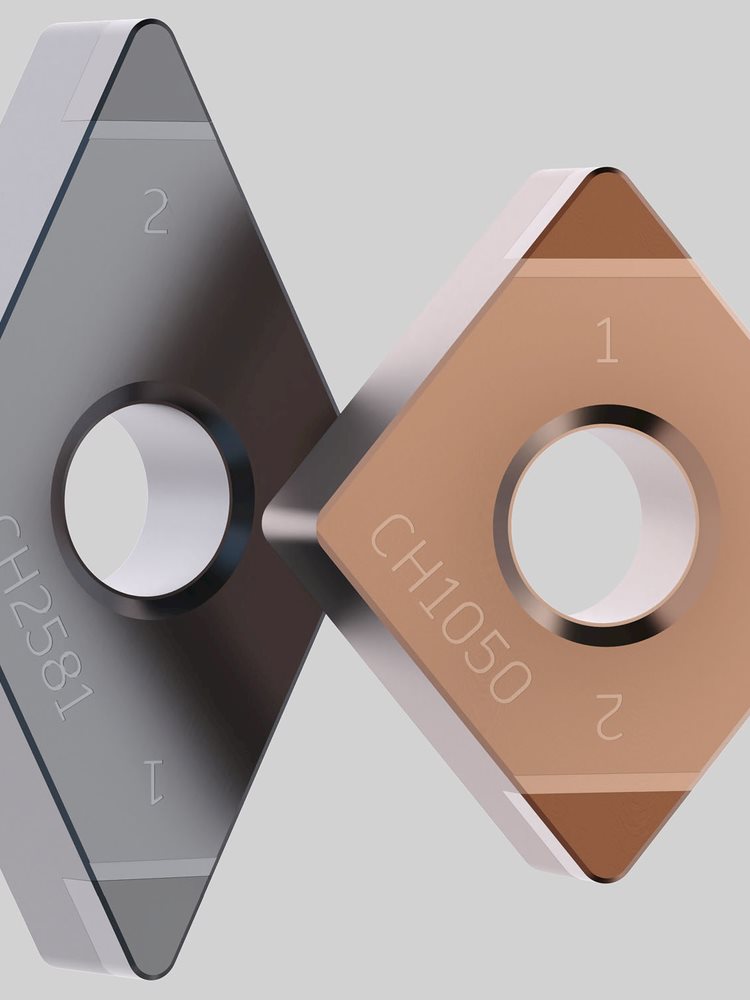
Comparing the popular types of inserts for heat resistant superalloys - Ceramics, Carbide and PCBN
Sustainable Business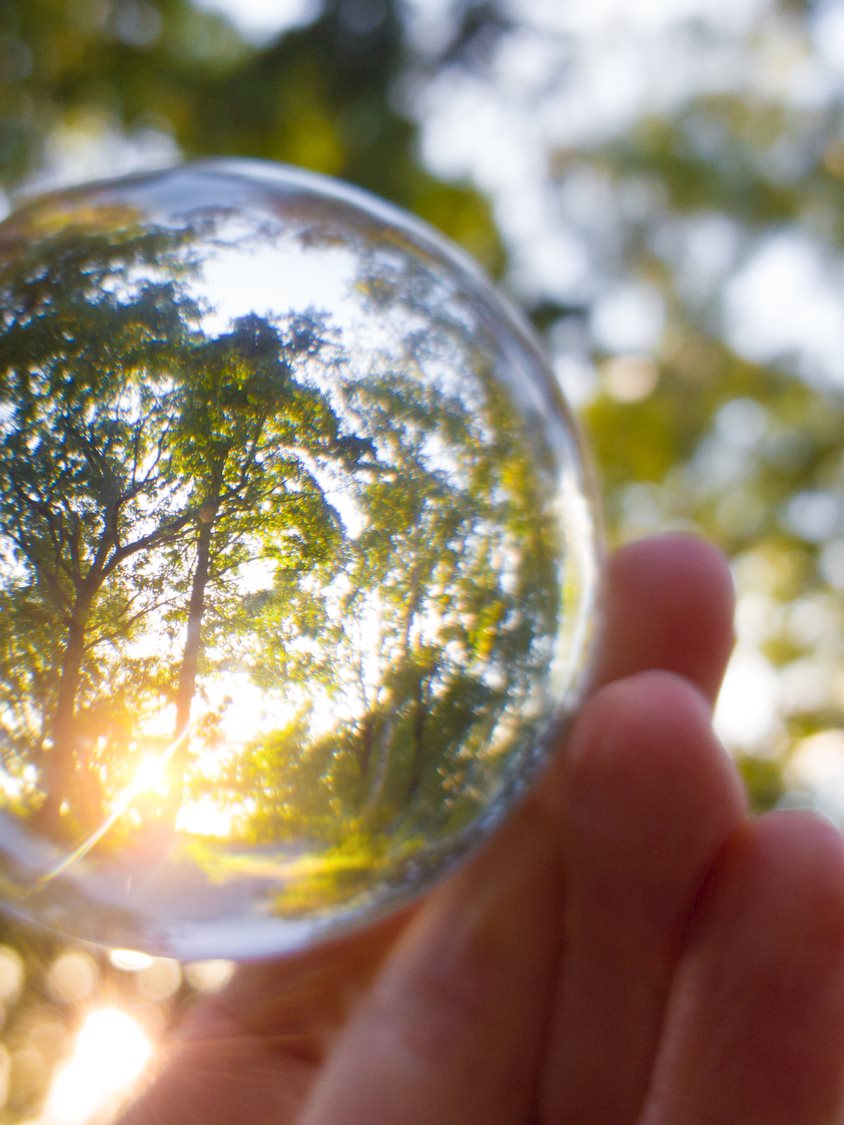
Seco Octomill™ 06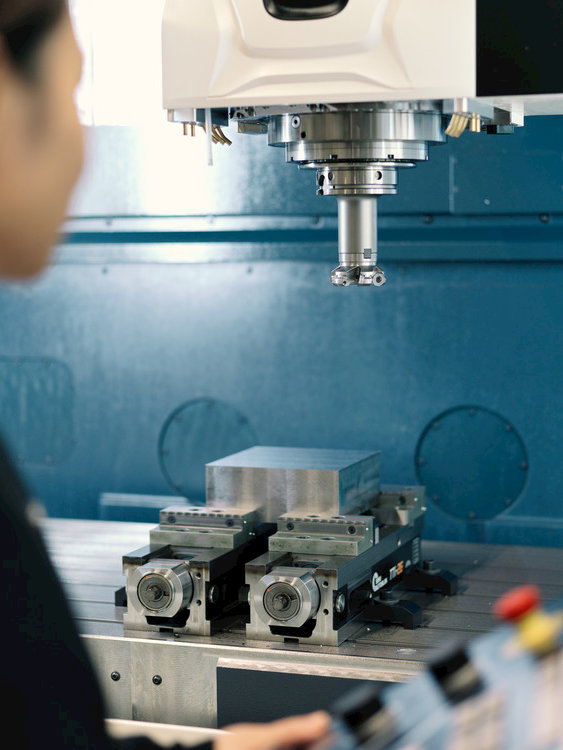
Seco Stabilizer™ Series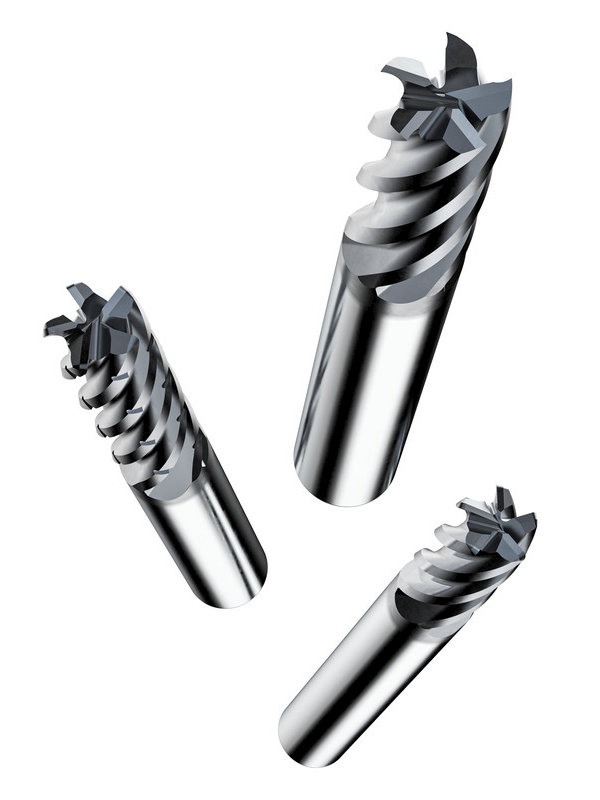
Seco enhances life cycle assessments with pilot project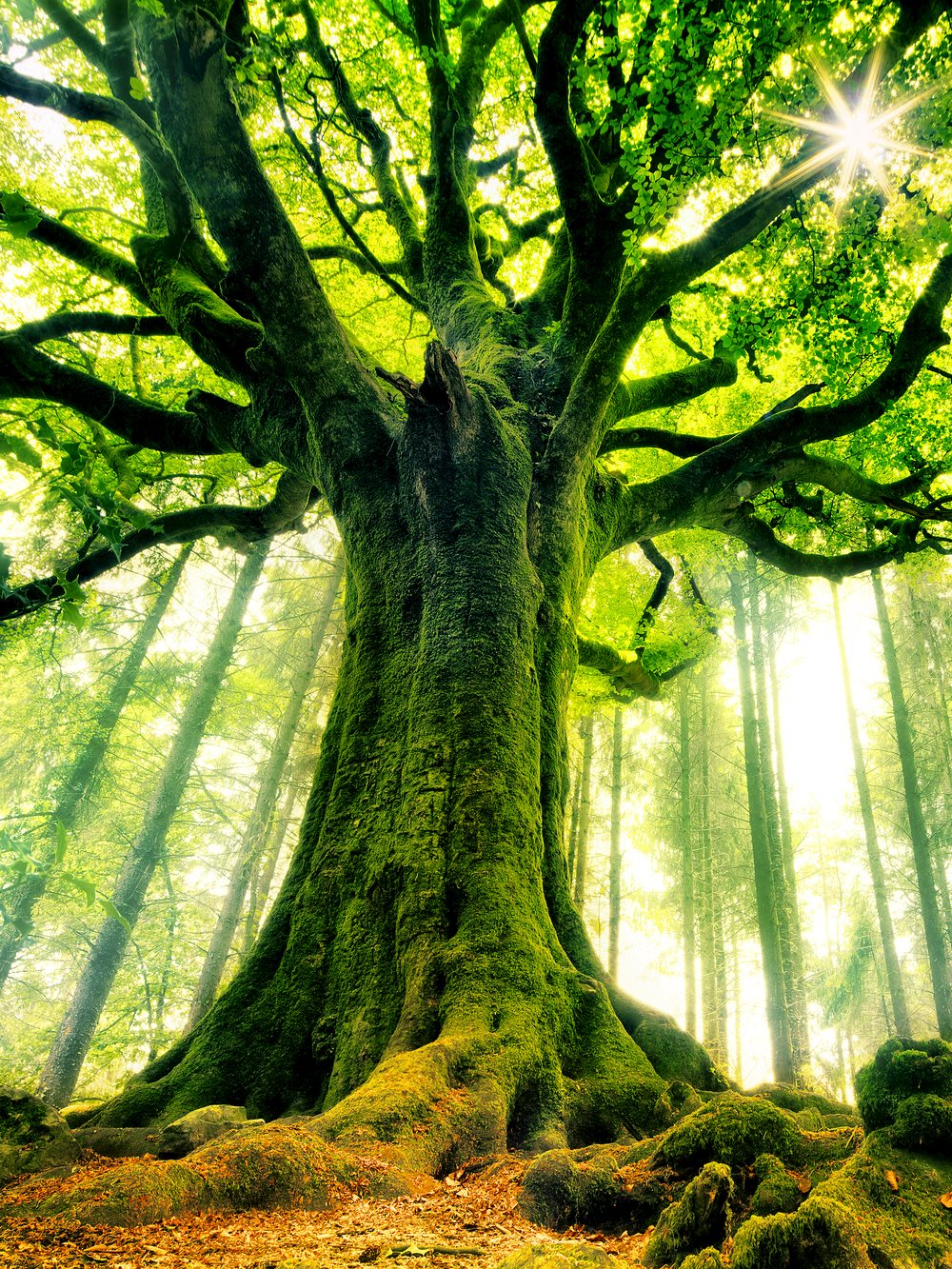
How to find the best alternative for your application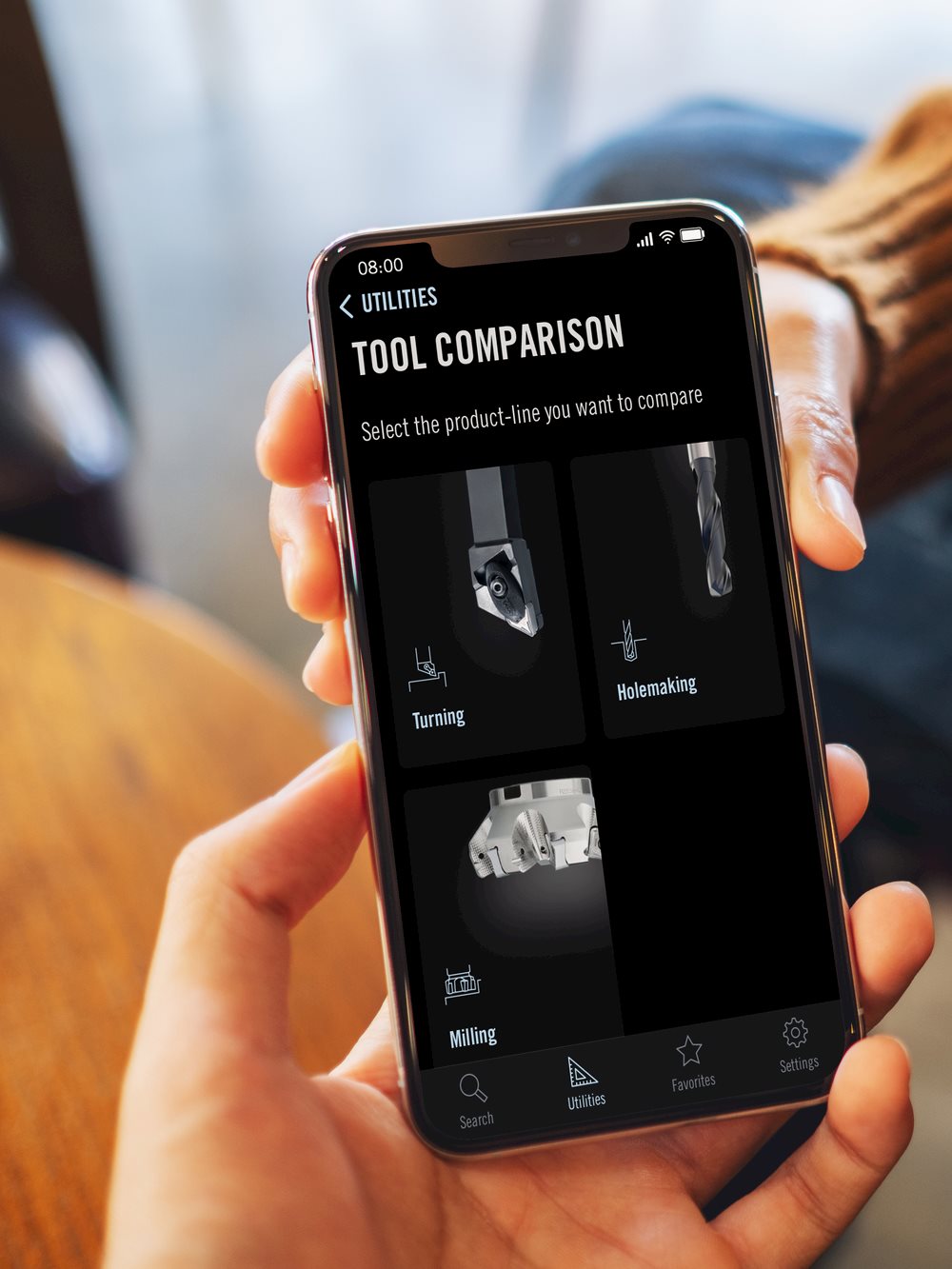
Reduce waste. Improve sustainability.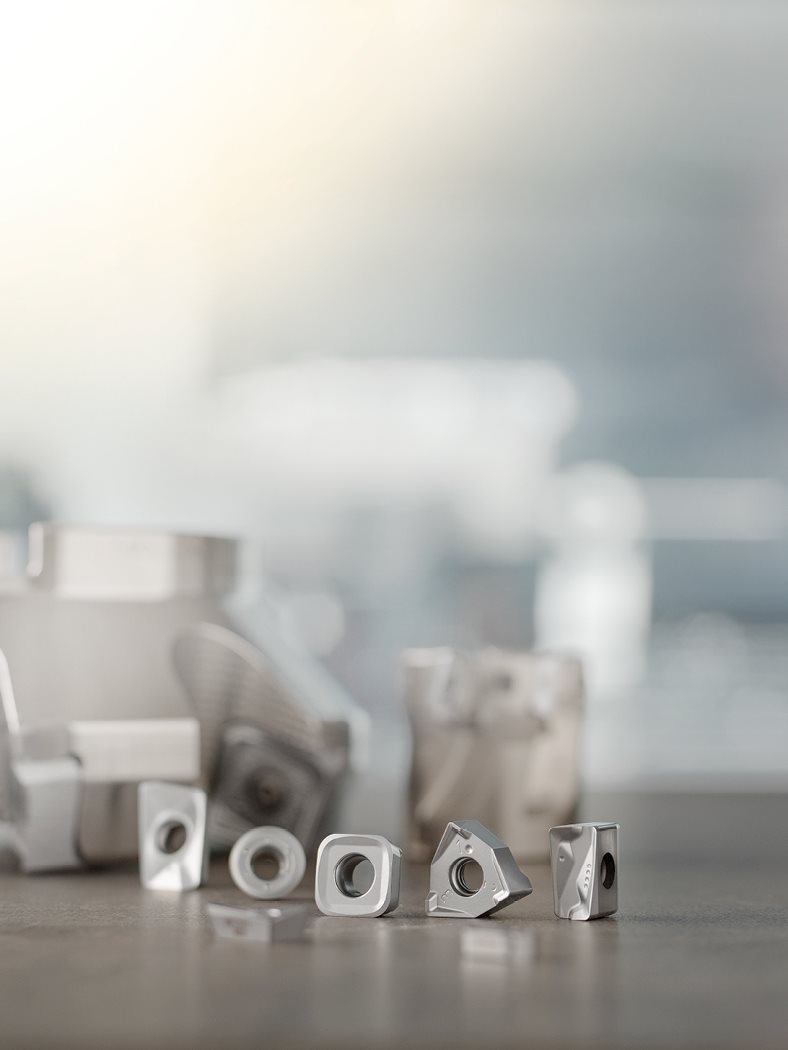
Download Centre India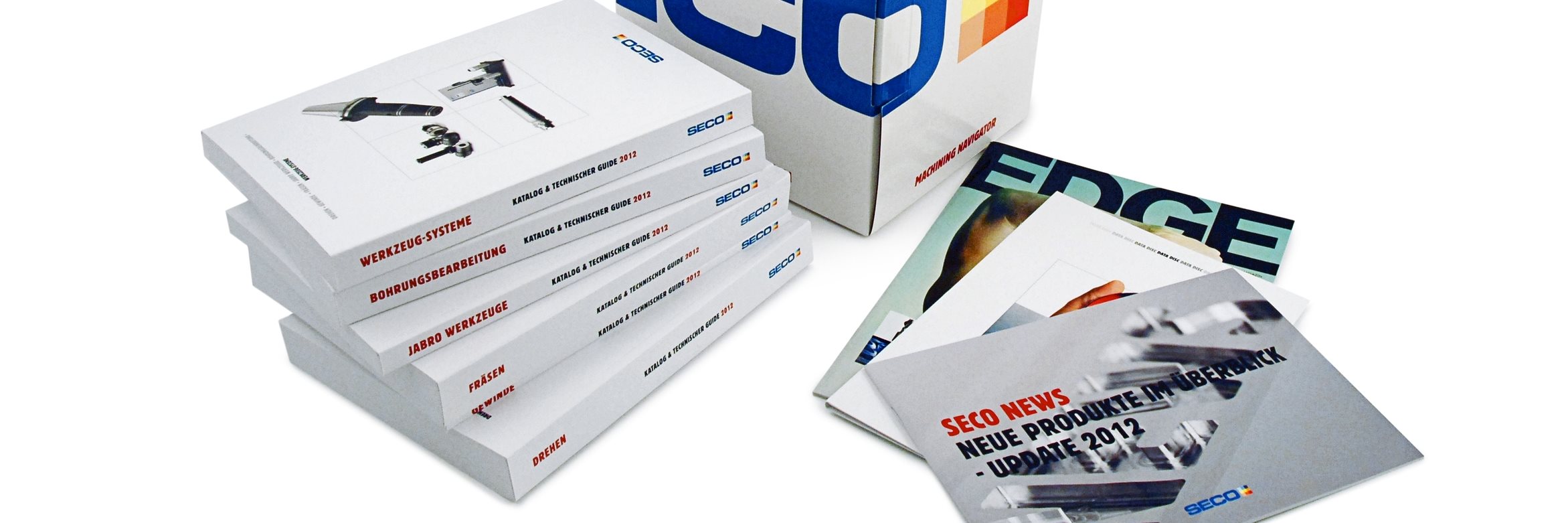
7 benefits of versatile metal cutting tools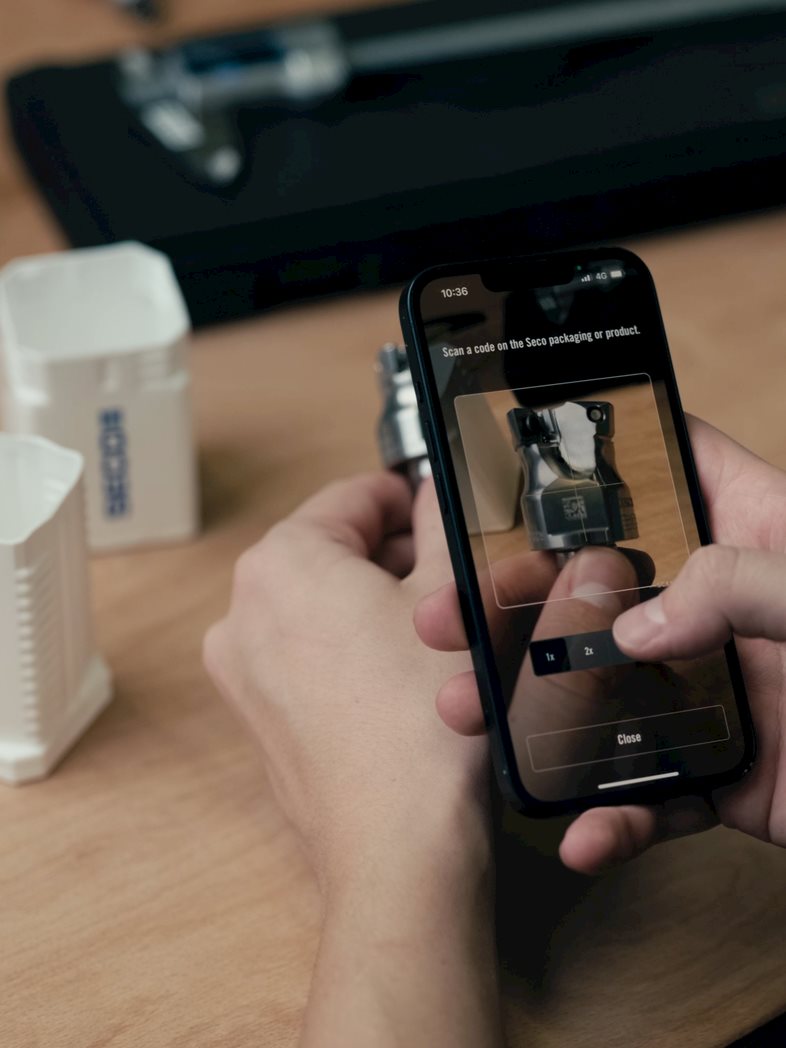
Seco News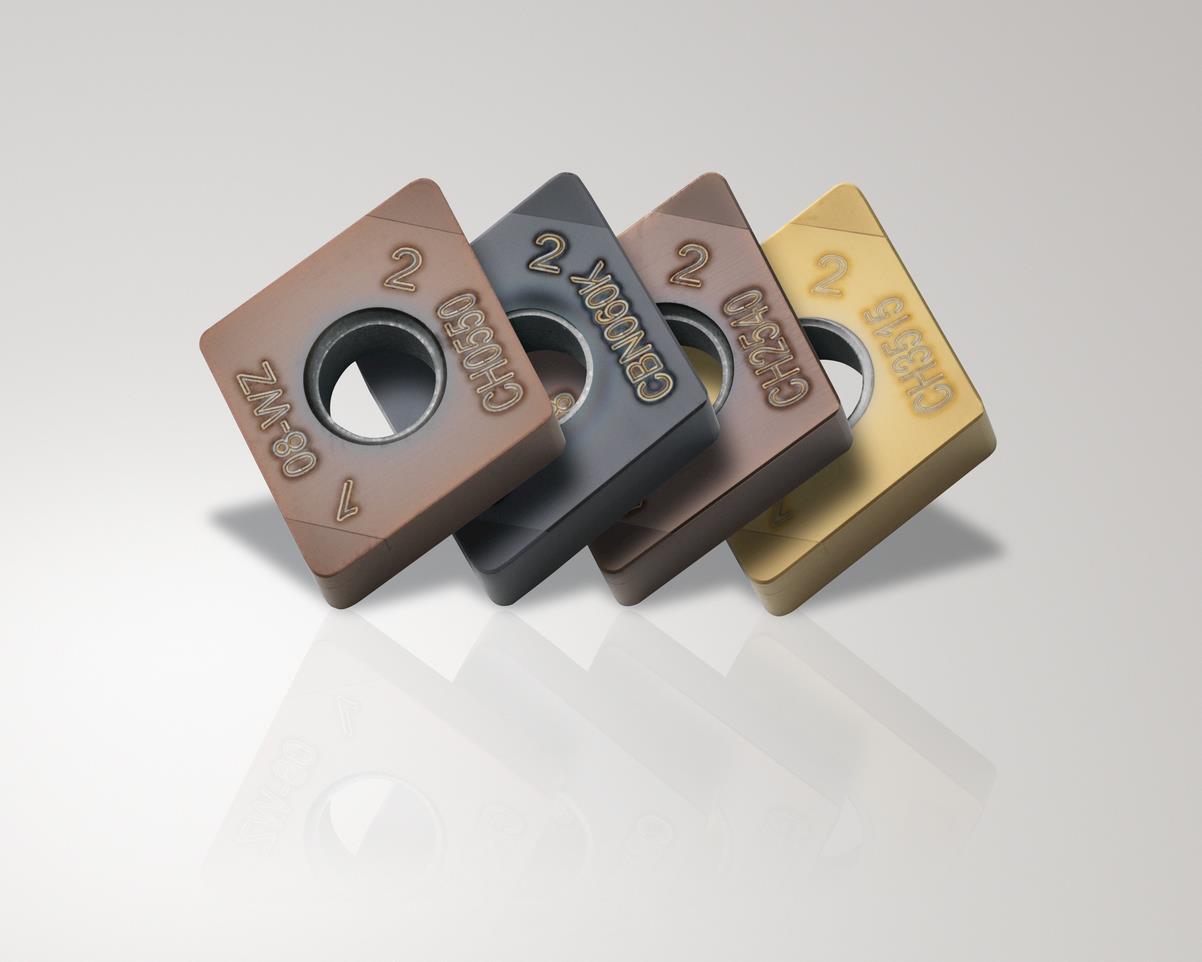
Technical Guide - Solid Carbide End Mills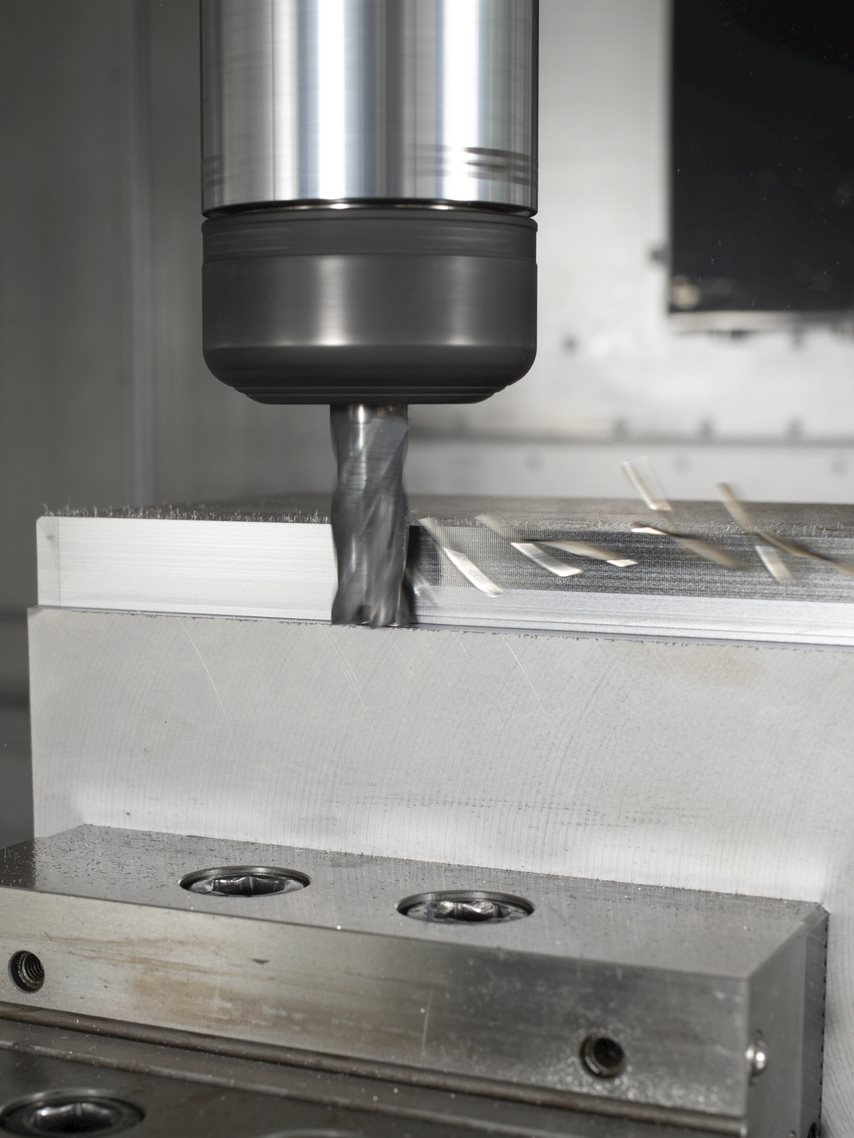
Seco Tools signs MoU with Lila Poonawalla Foundation, pledges support for 70 girls from junior college!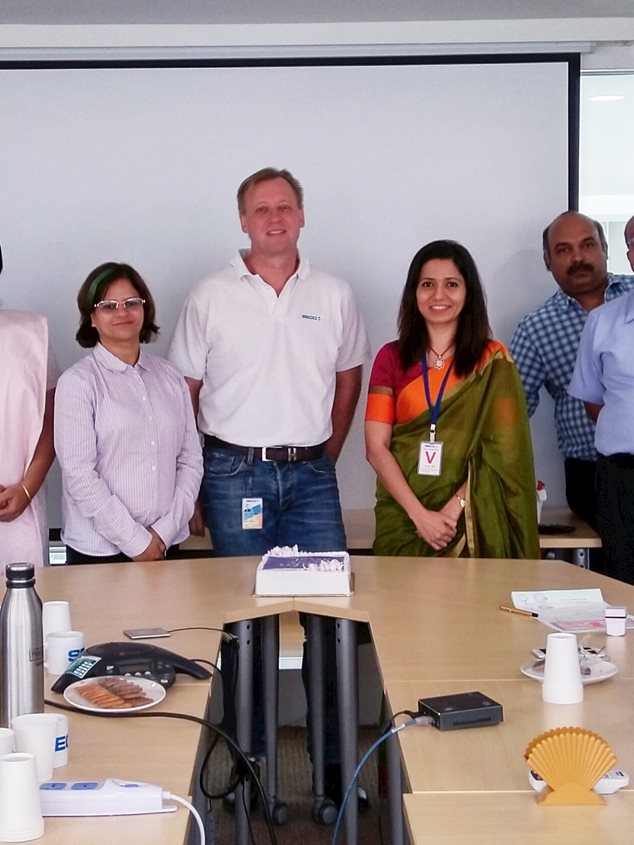
Effective approach to high-speed machining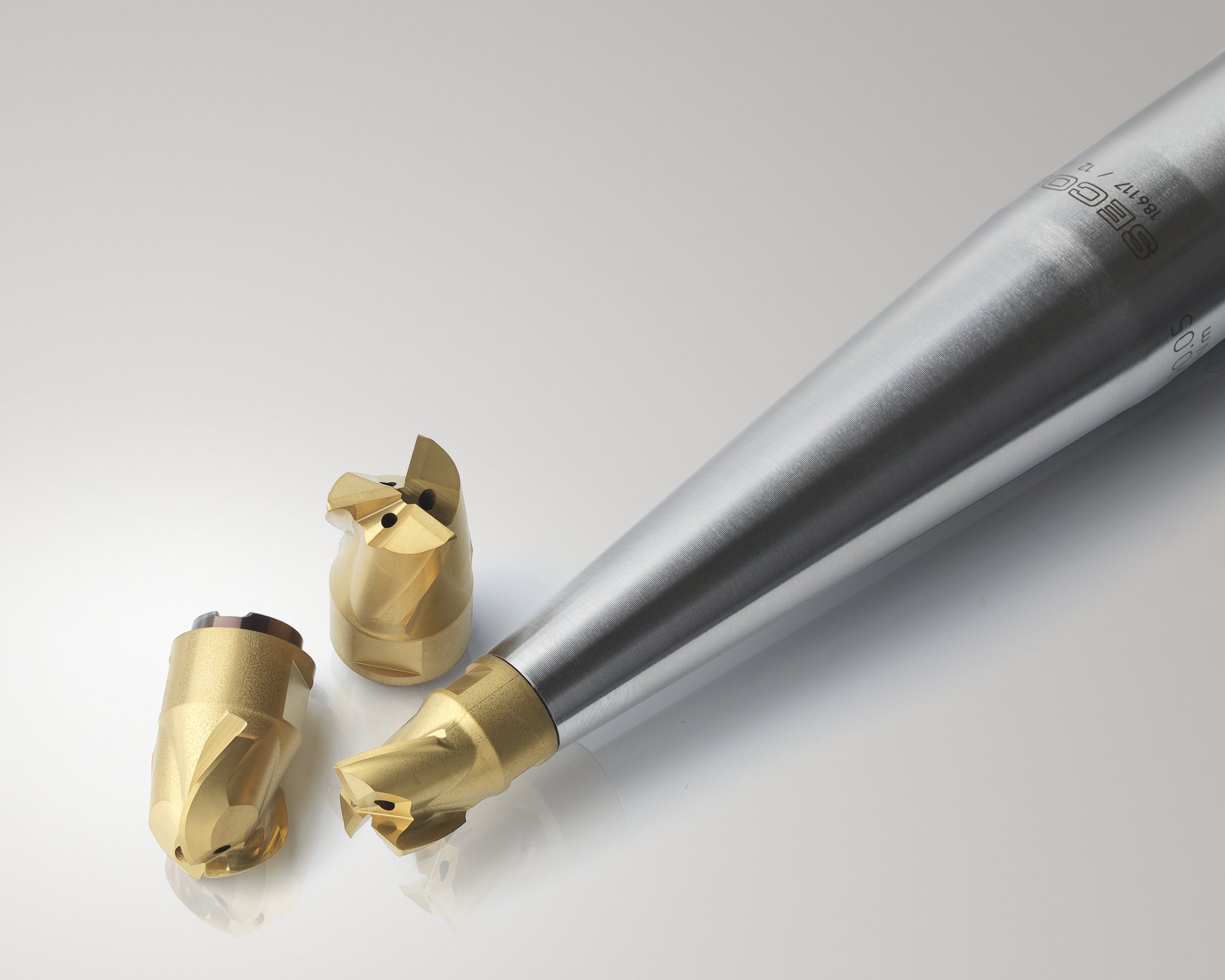
Seco X2 System for Small Part Machining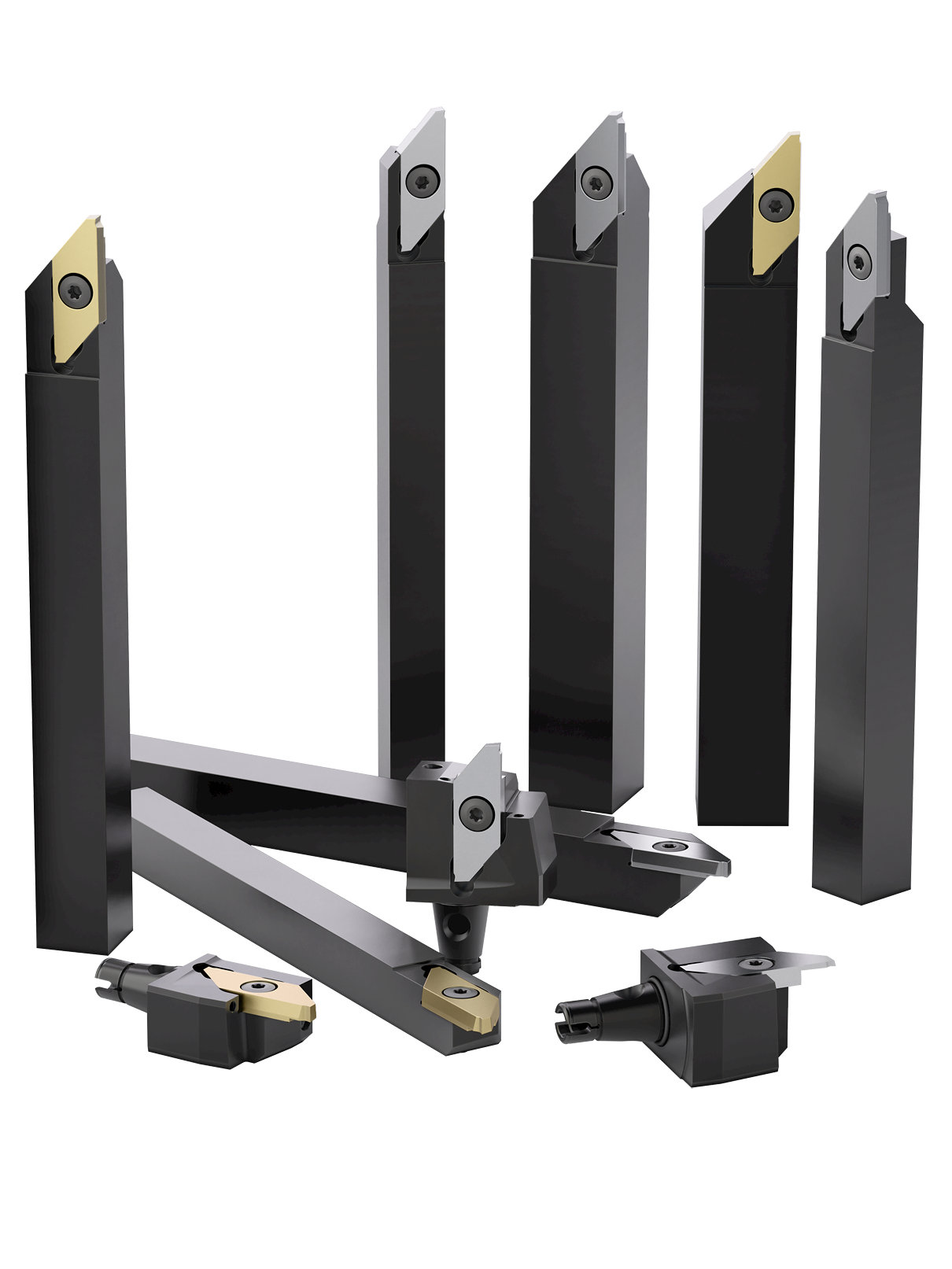
Seco Machine Library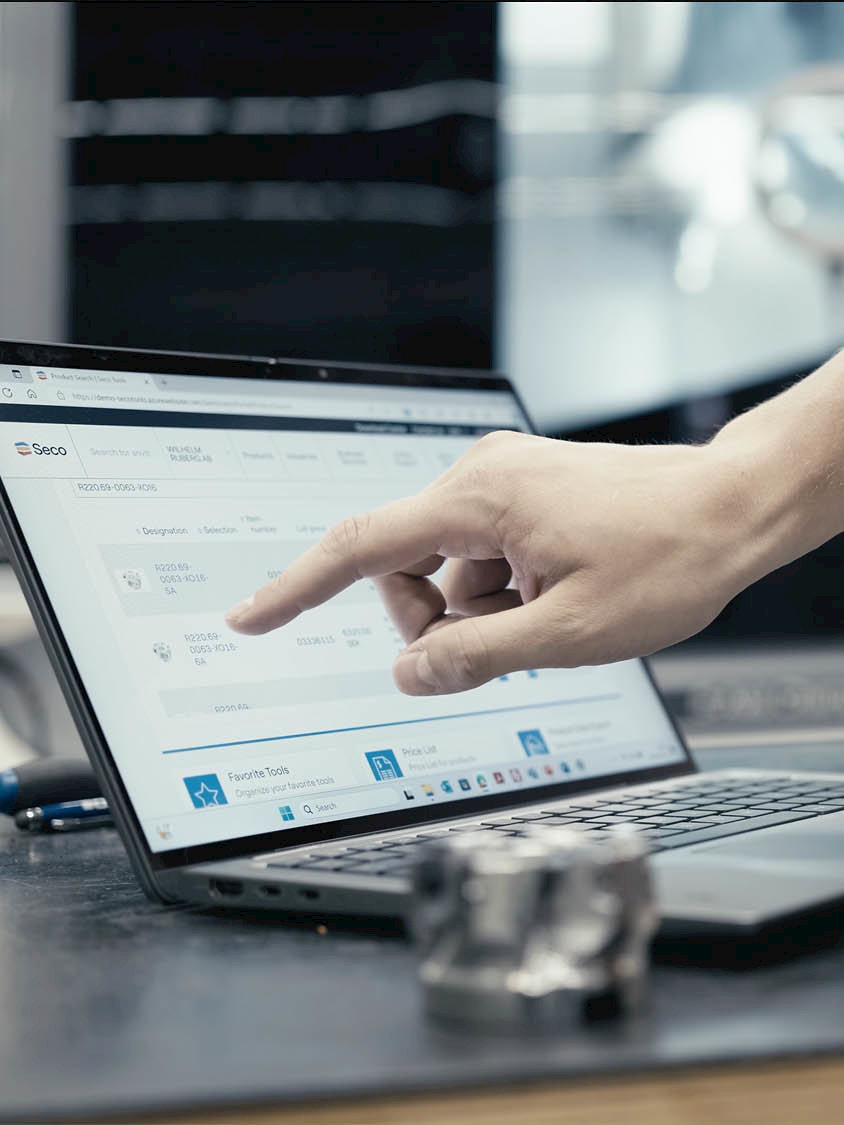
Seco-Capto MTM JETI toolholders for general ISO Turning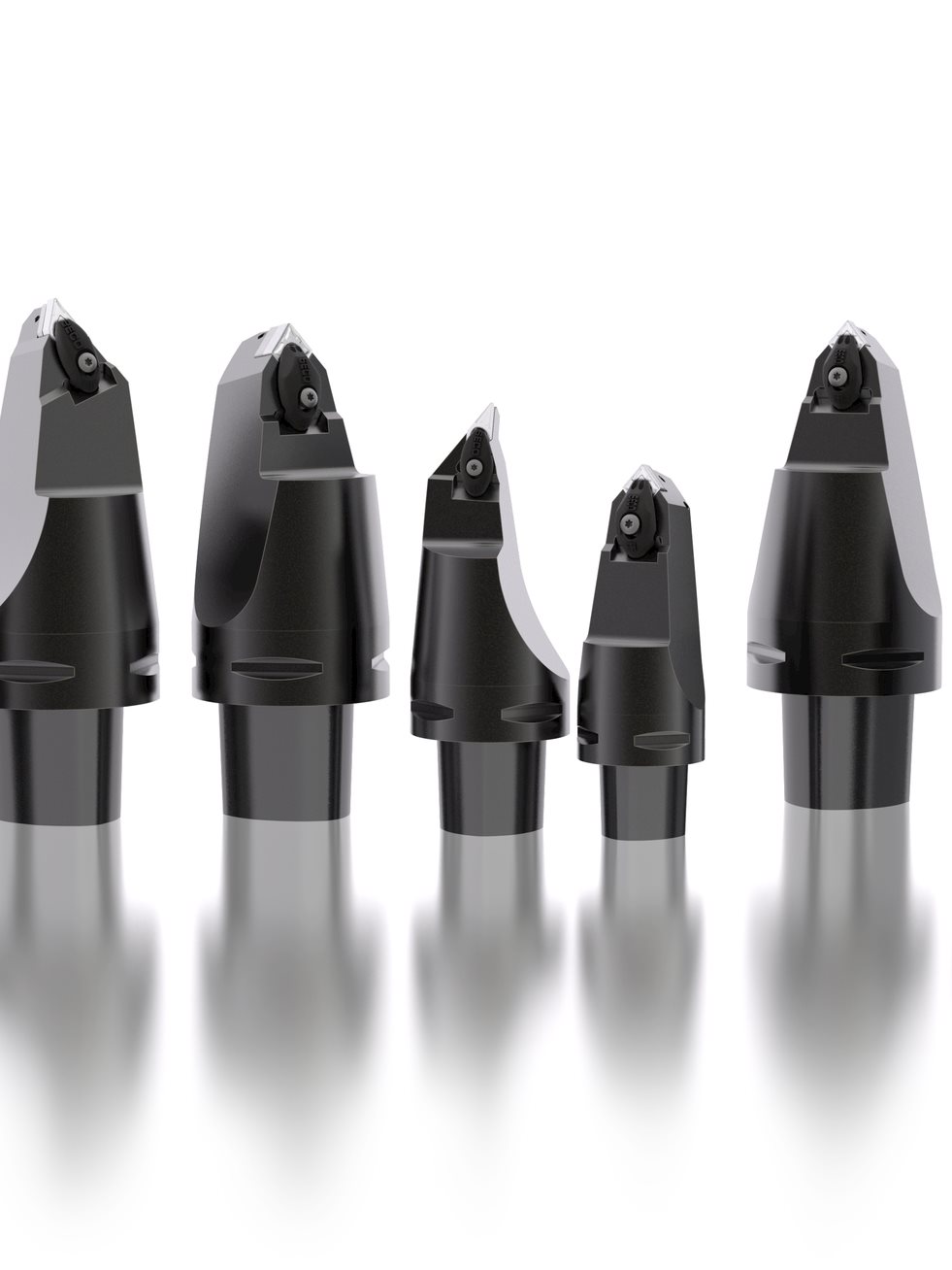
Control Tooling Inventory Costs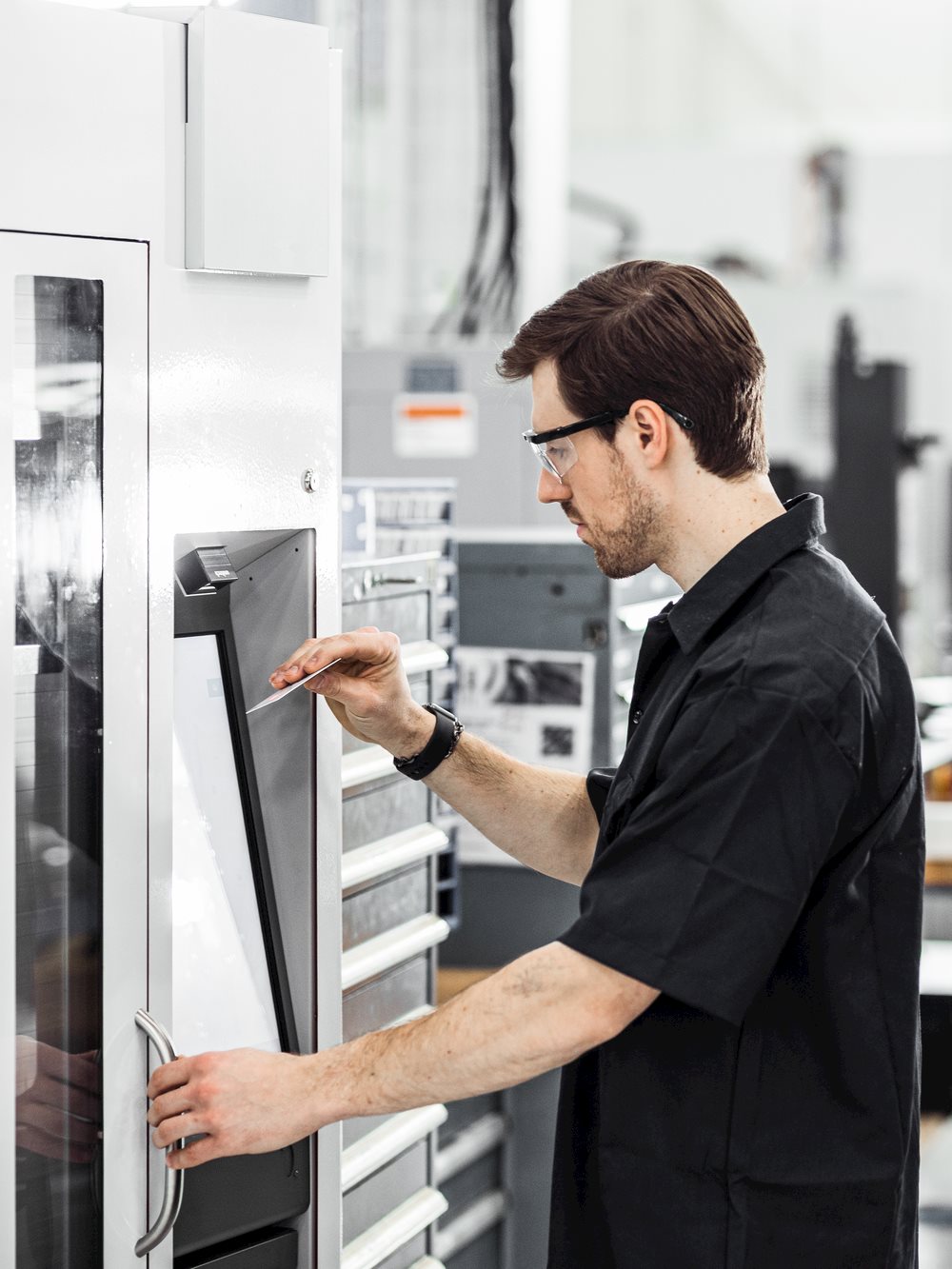
Seco X-Tra Long Solid Carbide Drills – 40xD-60xD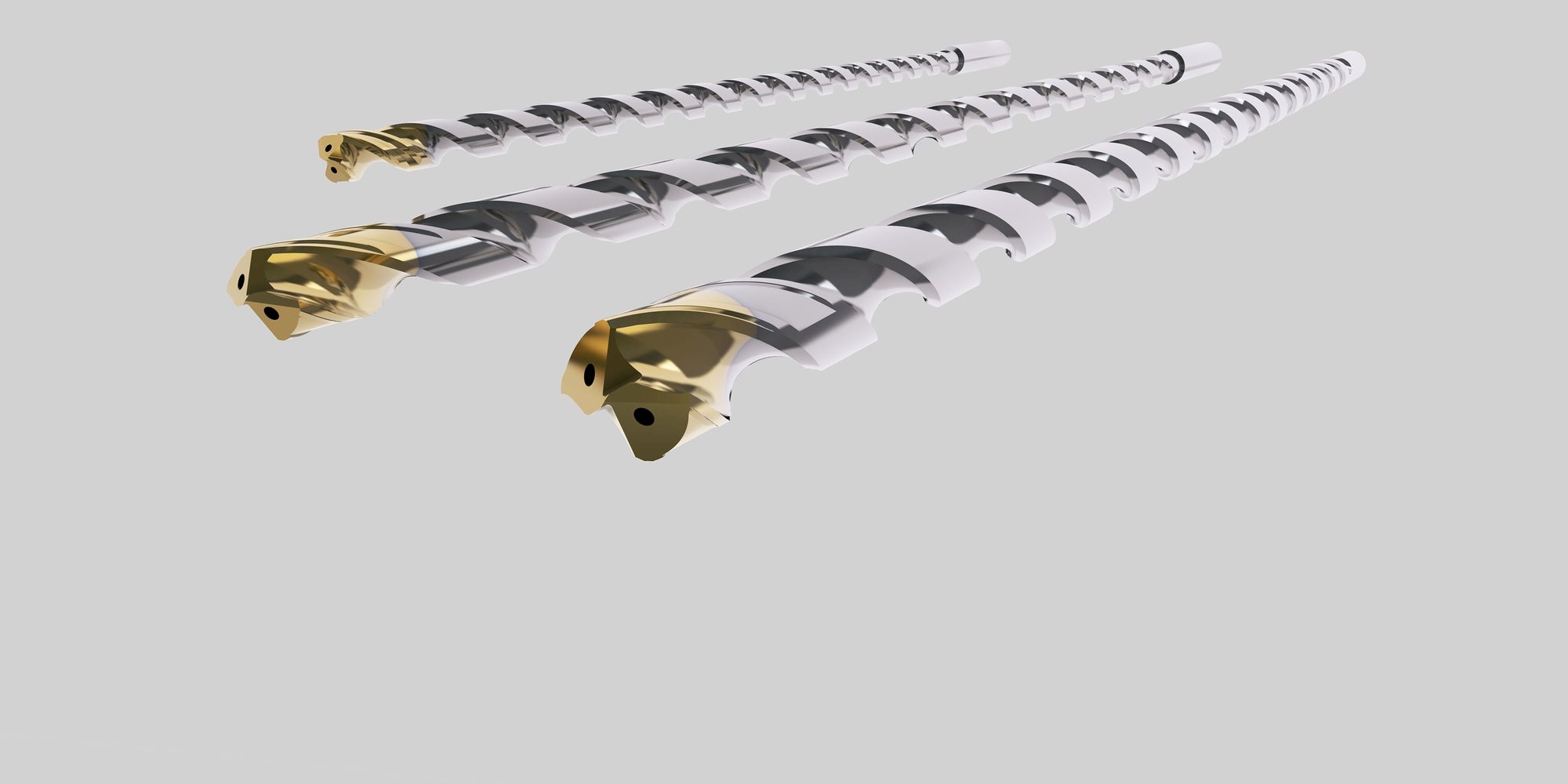
Seco Assistant - Get the new Seco mobile app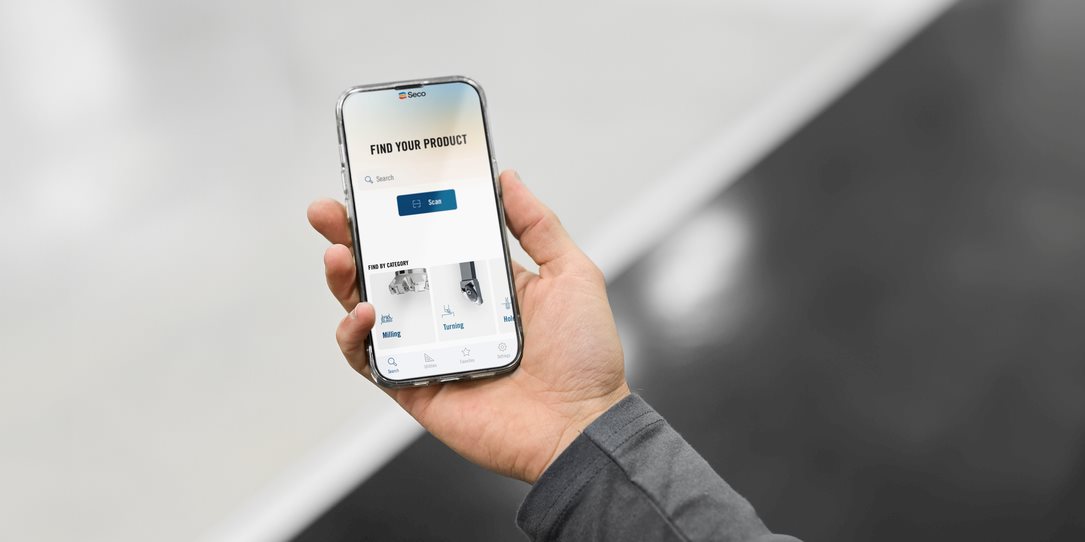