Five Tips on Steel Milling
Steel milling is certainly one of the processes that requires precision and experience if you want to produce a quality productSteel is the most widely used material in the world and its production chain generates 8.3 trillion dollars of added value annually (10% of global GDP) and employs 259 million people.
Steel is an alloy composed of Iron and Carbon and is one of the most resistant and versatile materials that exist on the market. Its uniqueness derives from the fact that, by varying the carbon content and adding binding elements, it is possible to obtain different mechanical characteristics that can be adapted to the most extreme needs.
The multiple types of steel that can be found make its processing complex. Steel milling is therefore certainly one of the processes that requires precision and experience if you want to produce a quality product.
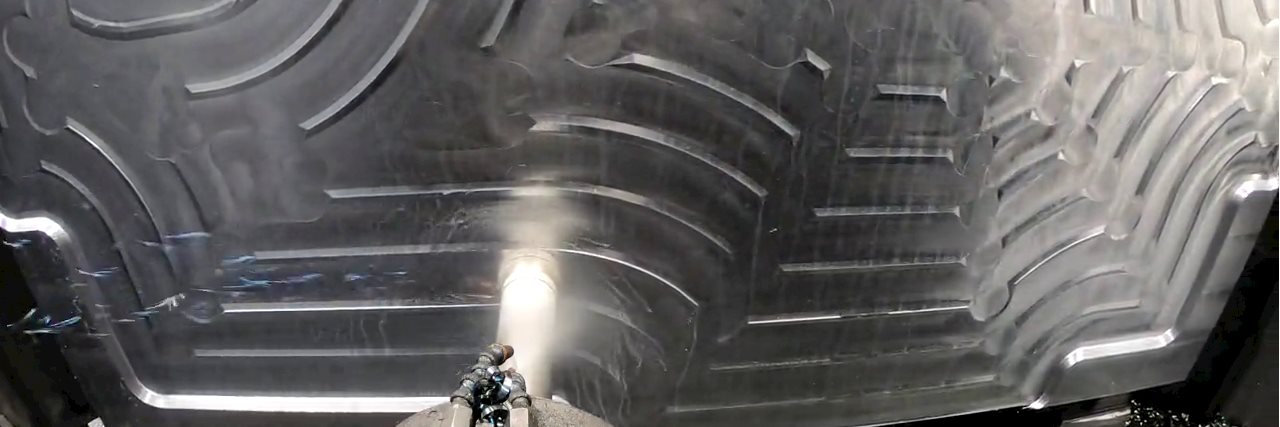
Below we have listed five simple tips, thanks to which you can tackle the milling of all types of steel without incurring unpleasant surprises:
- Know your steel. Although steel is basically composed of only two elements (Fe and C), there are many types based on the carbon content or alloying elements used. These two parameters combined with the heat treatments and manufacturing processes chosen determine the machinability of your steel and the problems you may encounter during milling. For example: a low-carbon steel facilitates the formation of burrs and built-up edges that can damage the cutter, while a hard steel can give chipping problems to the component and the tool. Tip: Identify the steel you are milling and use the parameters that the tool manufacturer recommends for that specific material.
- Distinguish the processing phase. The steel milling process requires more than one step to achieve the desired quality result, and each requires different cutting parameters and tools. In the roughing phase, where a large amount of material is removed, it is essential to use the right cutting speed and dry milling to avoid thermal micro-cracking problems. If you're finishing steel, use a cutting fluid to improve the surface finish and avoid excessively low feeds to allow the tool to work properly
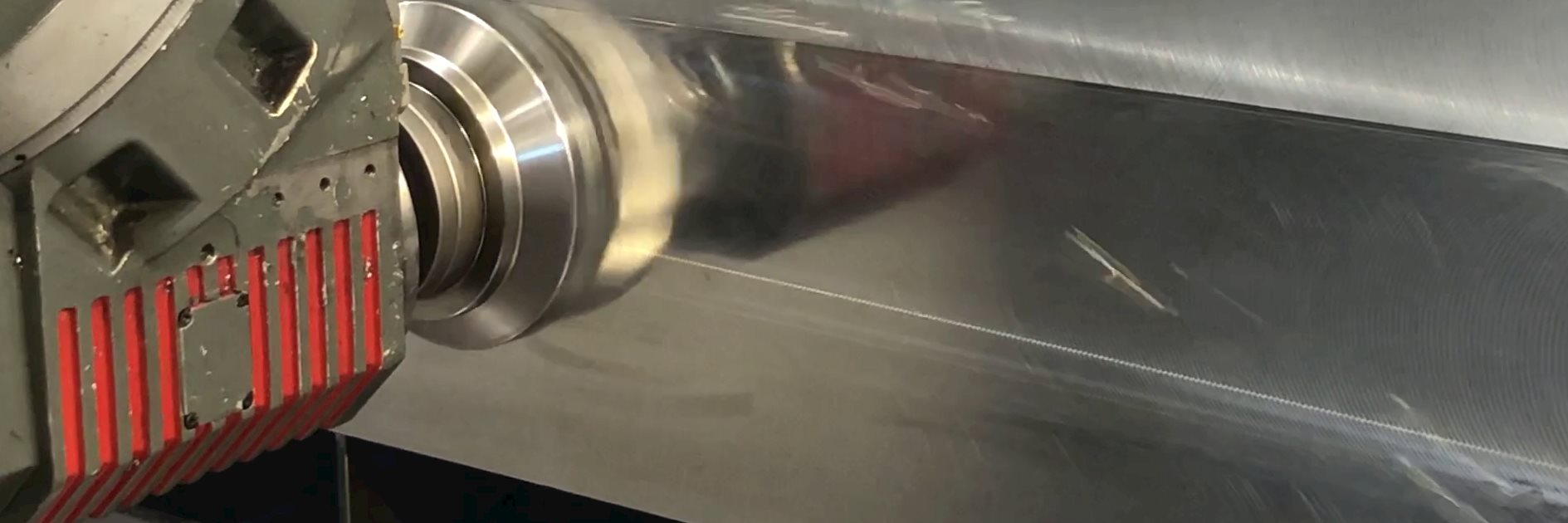
- Keep the heat down. The steel milling operation is an interrupted cutting process that generates temperature changes near the work area. As a result, the cutting edge is subject to thermal shock and cyclic stresses, which can generate micro-cracks and lead to a reduction in the effective tool life. Always use the most suitable cutting parameters listed in the tool manufacturer's catalog to prevent excessive heat generated from ruining the material and the tool. Where this is not enough, you can use a generous and constant flow of coolant that keeps the temperature low and promotes chip evacuation.
- Control vibrations: The hardness of the steel and the rotational speeds required of the cutter can cause vibration. They have a negative effect on the surface finish and damage the tool. To minimize this problem, use strong, rigid, and short tools so you can increase your cutting parameters and improve your throughput. Keep the workpiece securely in place with the right clamping and minimize tool overhang. You can also try using cutters with a small cutting radius.
- Watch out for surface work hardening. When milling different types of steel, it is easy to run into work hardening problems. This phenomenon occurs when the heat generated by the tool is transferred to the component instead of the chip, causing the material to deform plastically. The result will be drastically reduced tool life and an unsatisfactory surface finish. To avoid this, check that the cutting edges of your cutter never show excessive wear and replace them regularly when their condition is no longer optimal. Also try to avoid interruptions along the milling path and to maintain a feed rate as constant as possible, this will reduce points of excessive heat and reduce the likelihood of work hardening.
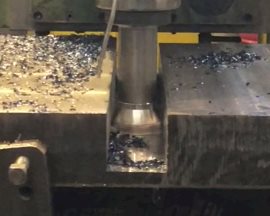
With our classroom and online training programs, you will learn about and use the latest techniques and technologies for machining, turning, milling, boring, drilling and boring.
If you would like to get in touch with us to find out about our training courses and tools, you can contact us
Inline Content - Gridded Links
Tags: 'contact'
Max links: 1
HOMERelated content
How to recycle your used carbide tools?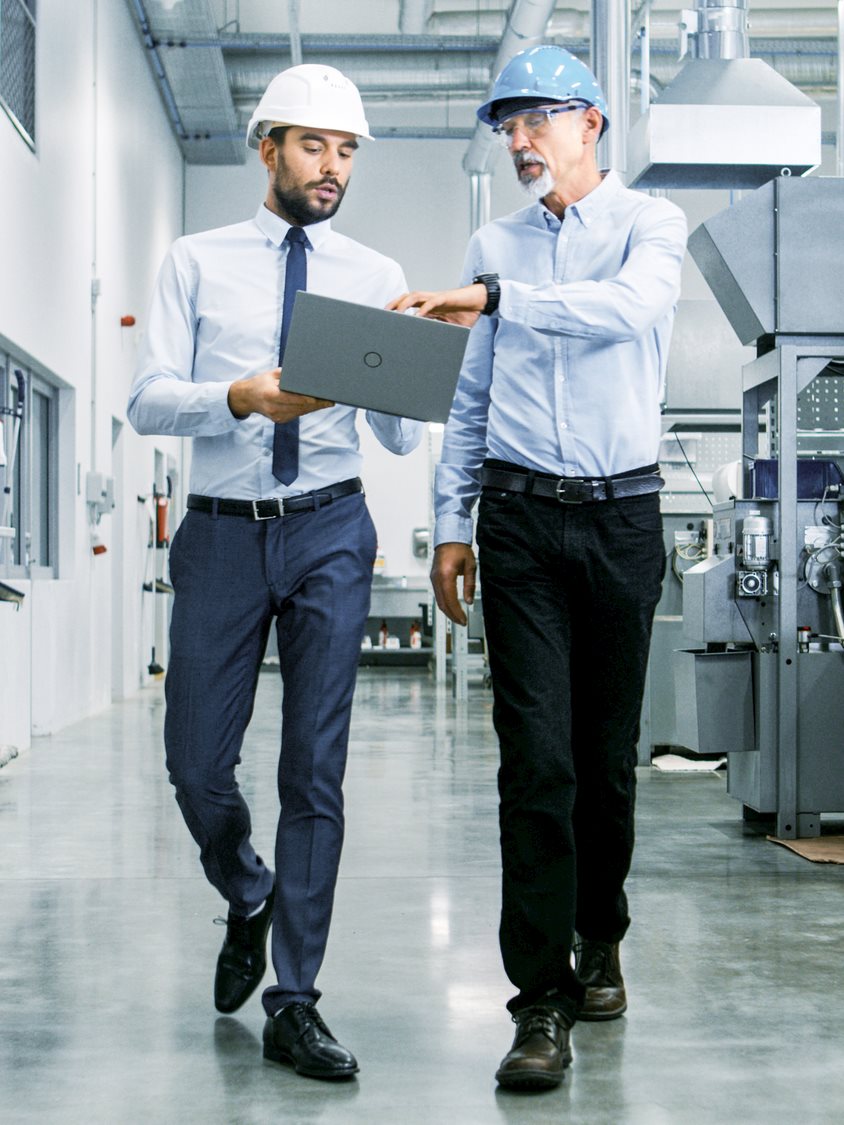
Recycling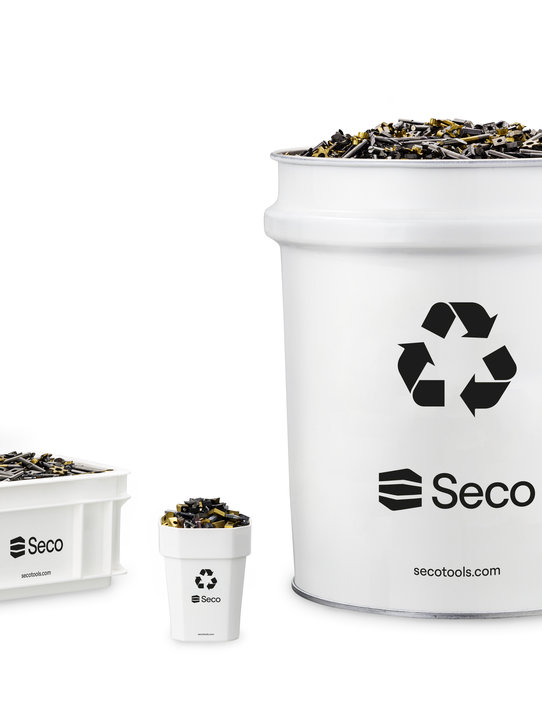
Tool Reconditioning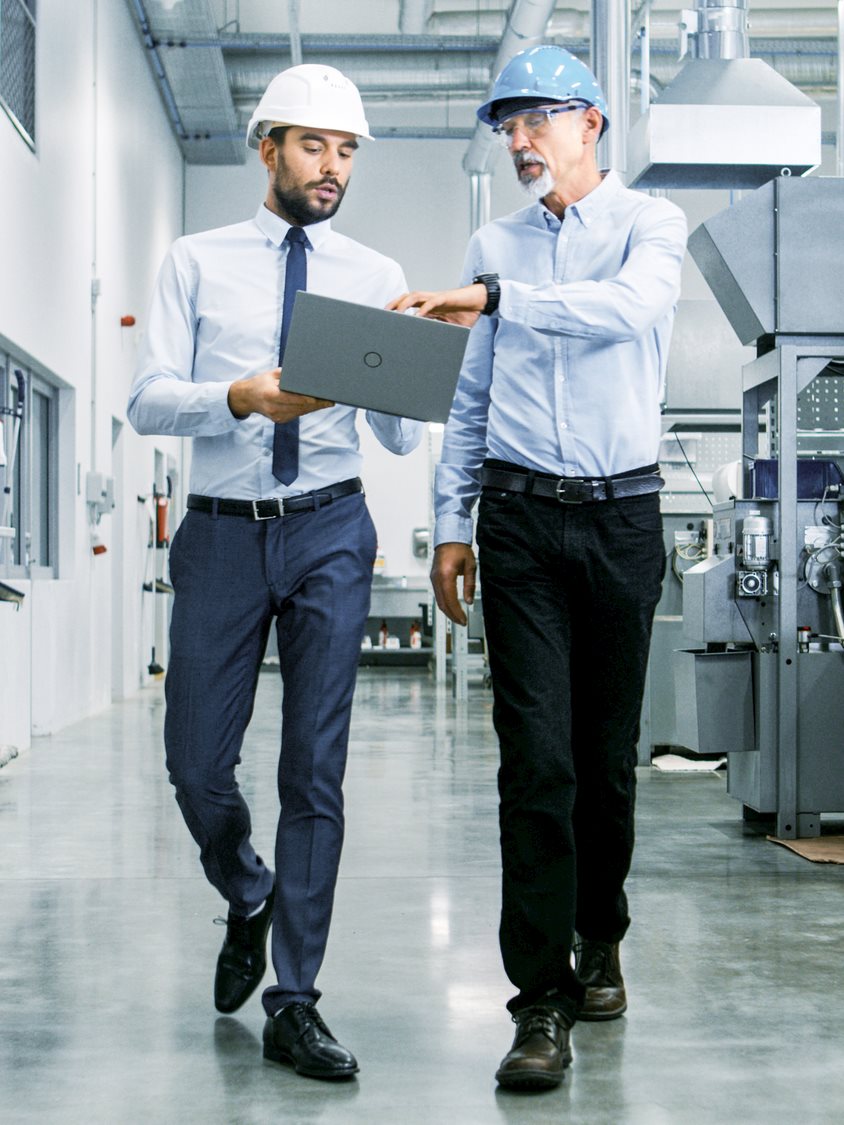
Video: The process of Recycling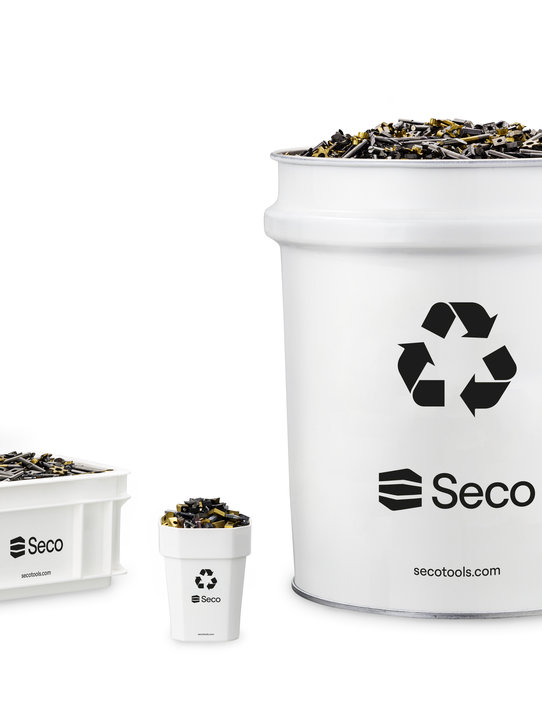
Used carbide Recycling Program | Seco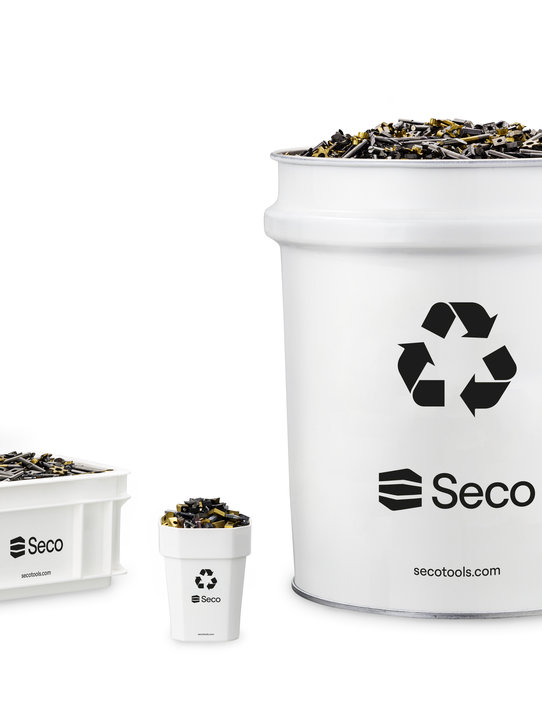
How to Handle Recycling Packaging? | Seco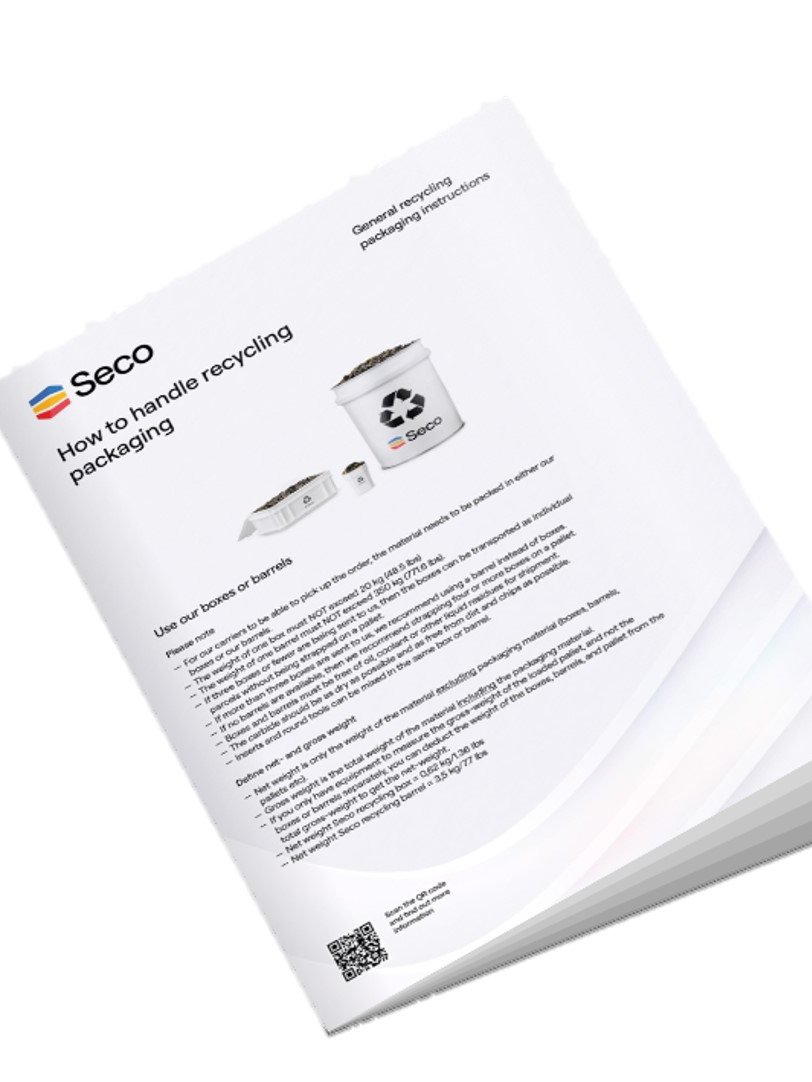
Seco Tool Reconditioning Service Grows by Over 30% And Continues to Increase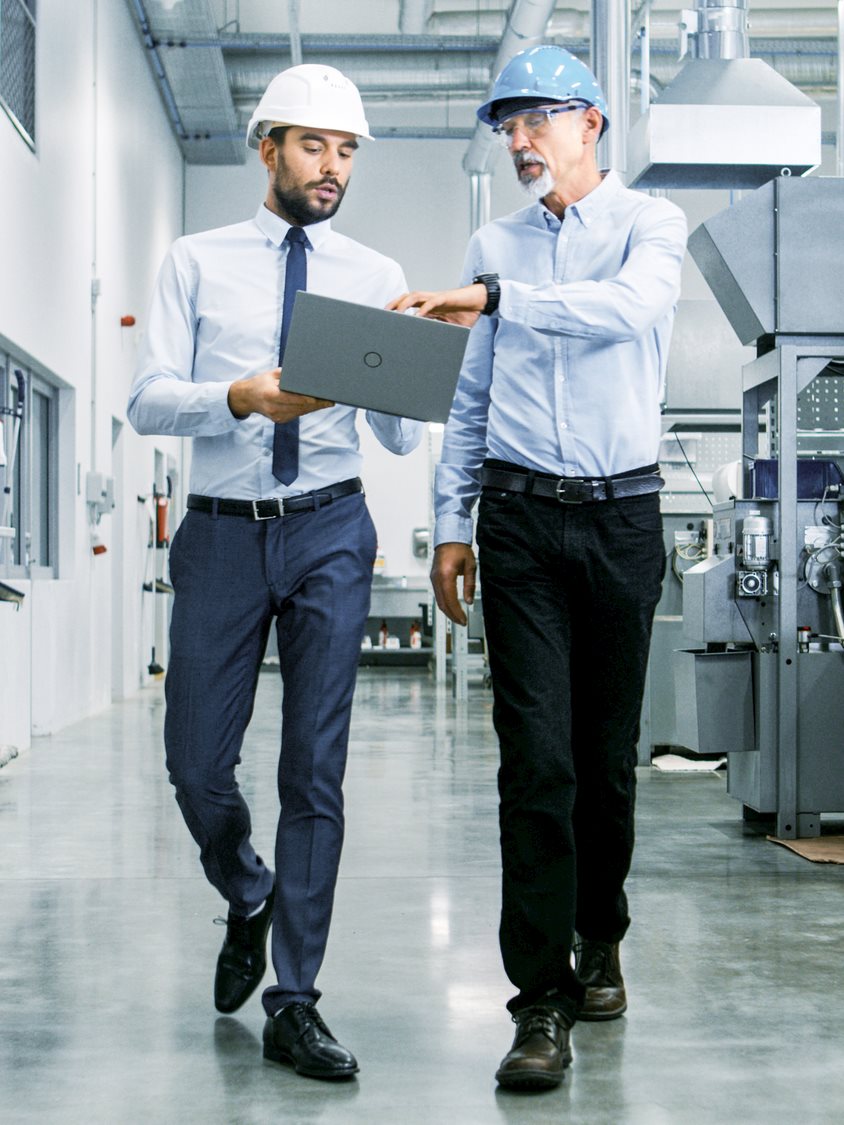
Seco is moving towards a sustainable future and switching to recyclable packages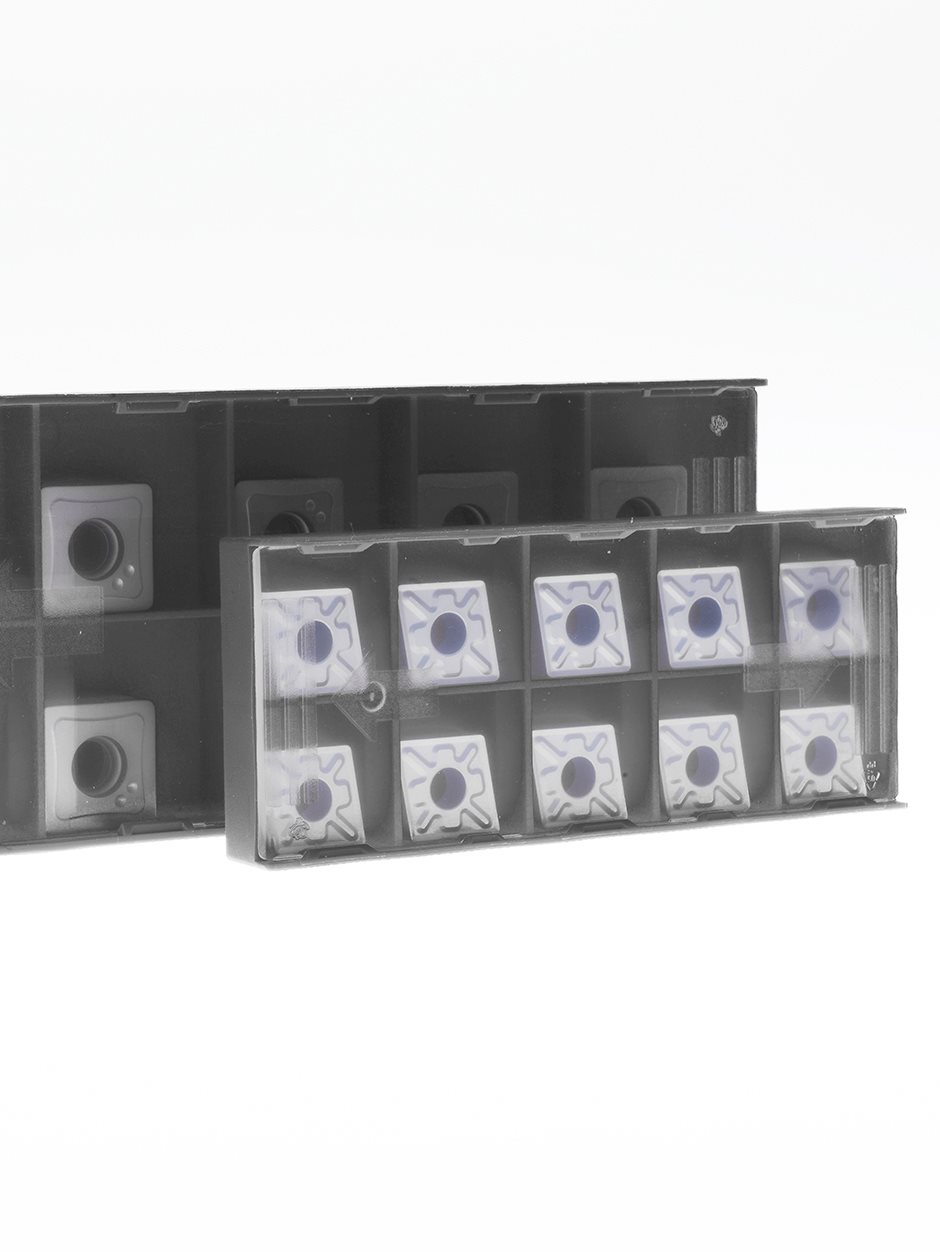
Responsible sourcing of minerals and metals at Seco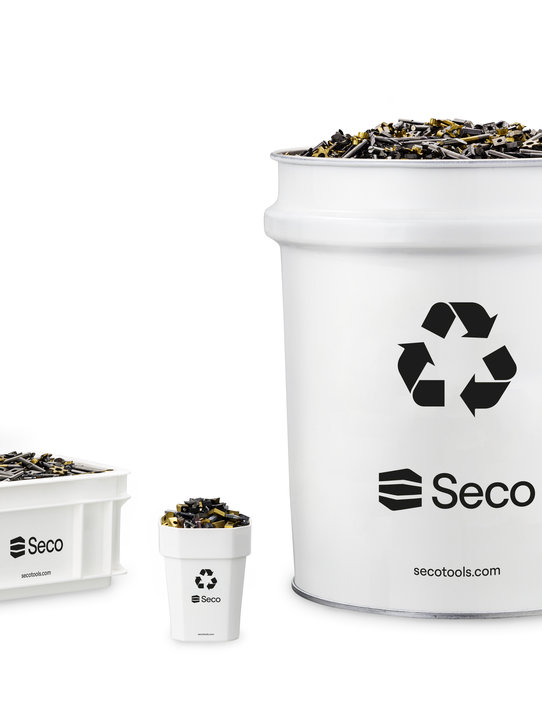
Tool life maximisation through smart tool life cycle management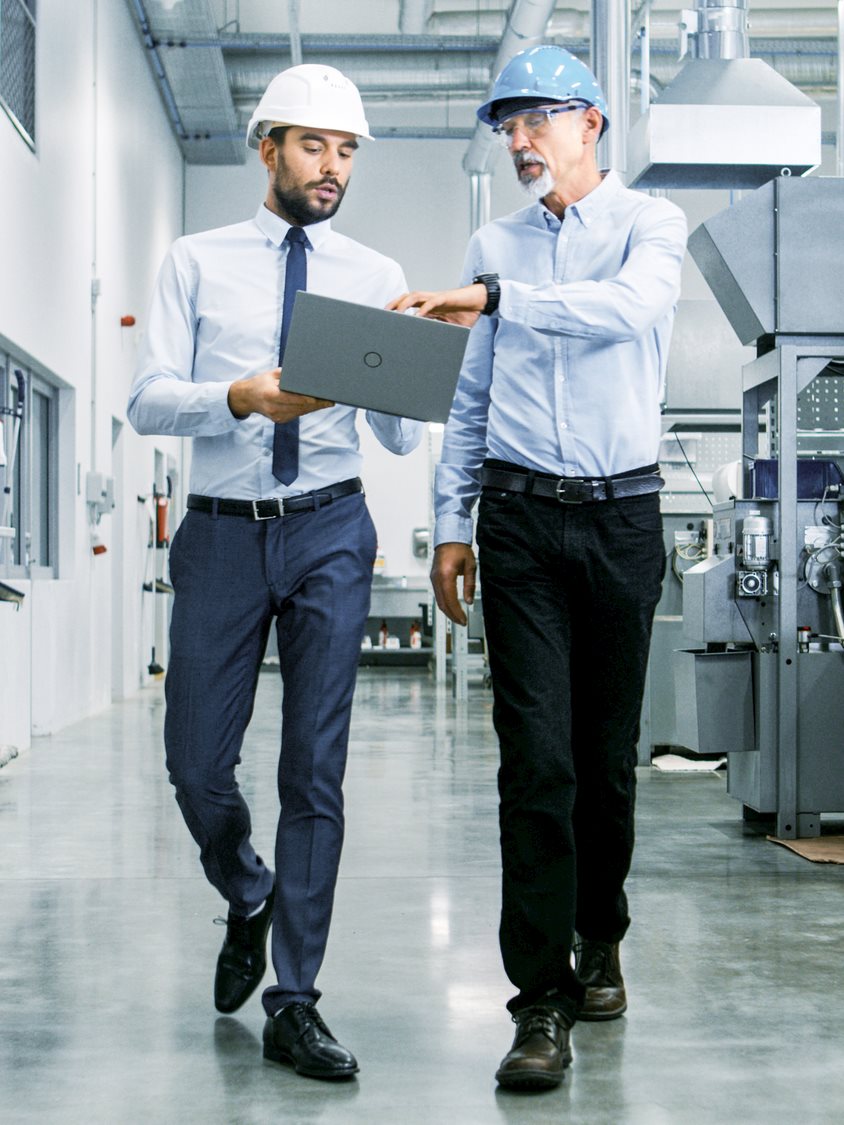
Recycling is key as Seco Tools sets ambitious target for circular economy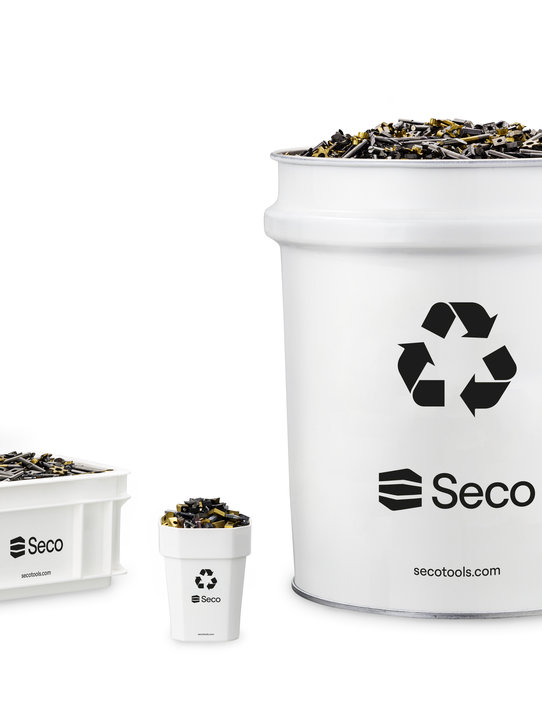
Tool life maximisation through smart tool life cycle management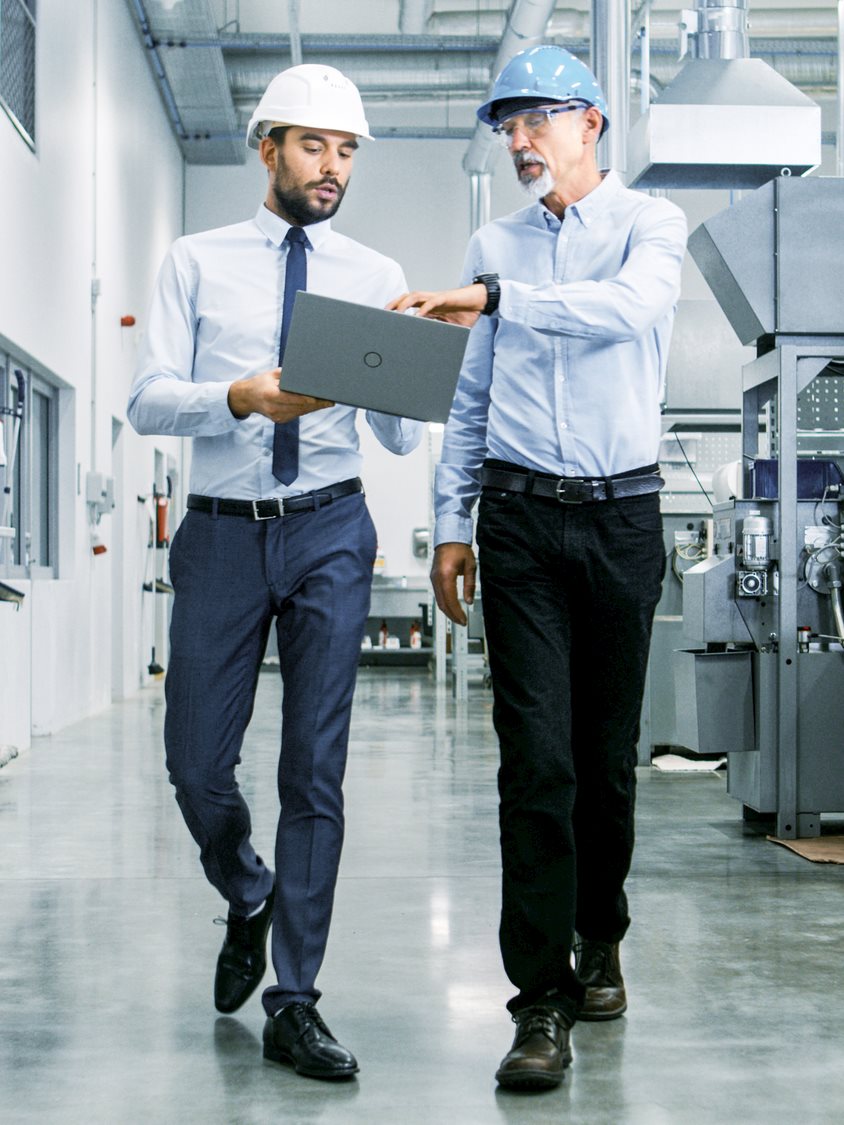
Seco leads the way with Life Cycle Assessment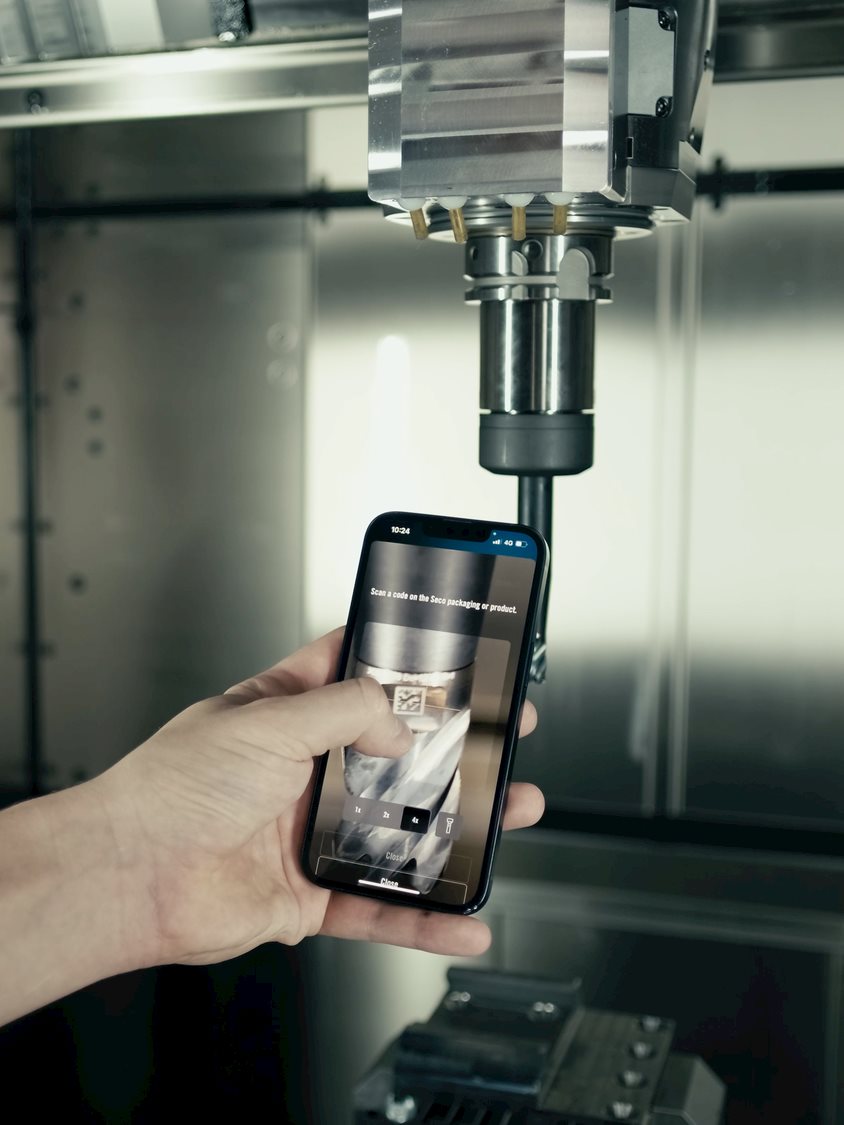
Seco Green Fund Achieves Sustainability Goals for Over a Decade
Video: How to recycle scrap? - You Asked - We Answer #7 by Manufacturing Transformation I Seco Tools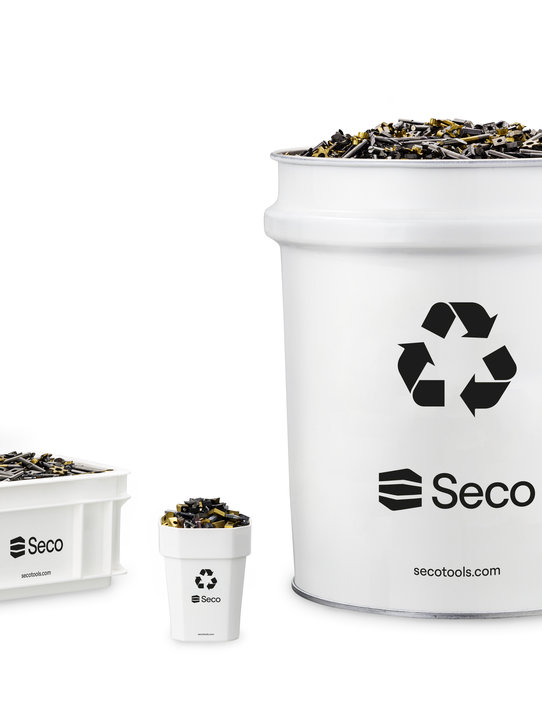
Green energy helps Seco hit emissions target nine years ahead of schedule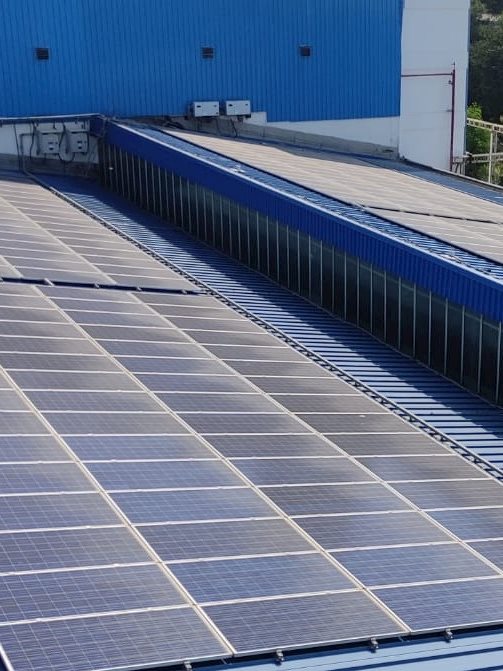
Video: For a Low Carbon Future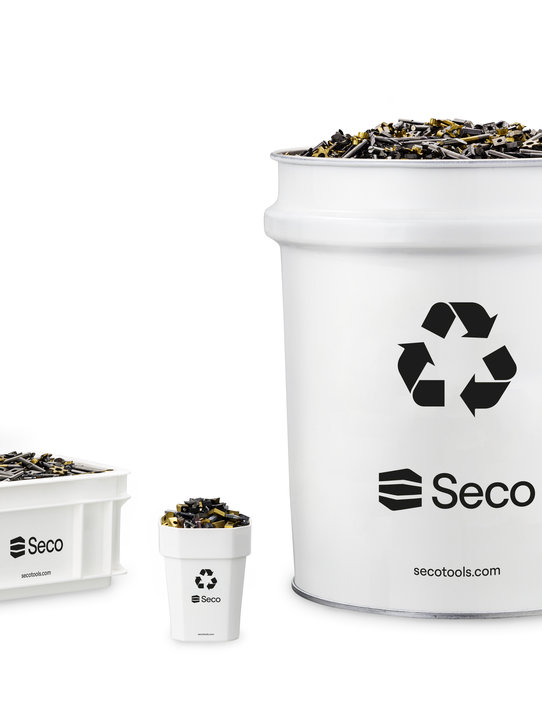
Video: Zero Waste - Recycle with Seco: Both At Work As Well As At Home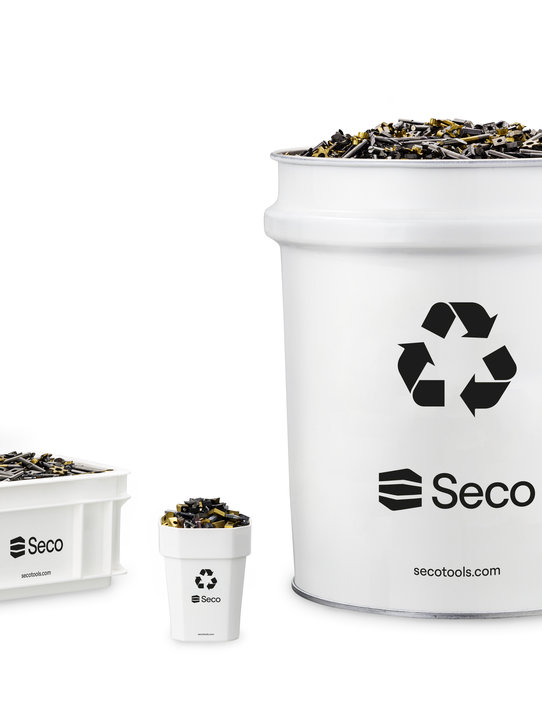
Download Recycling brochure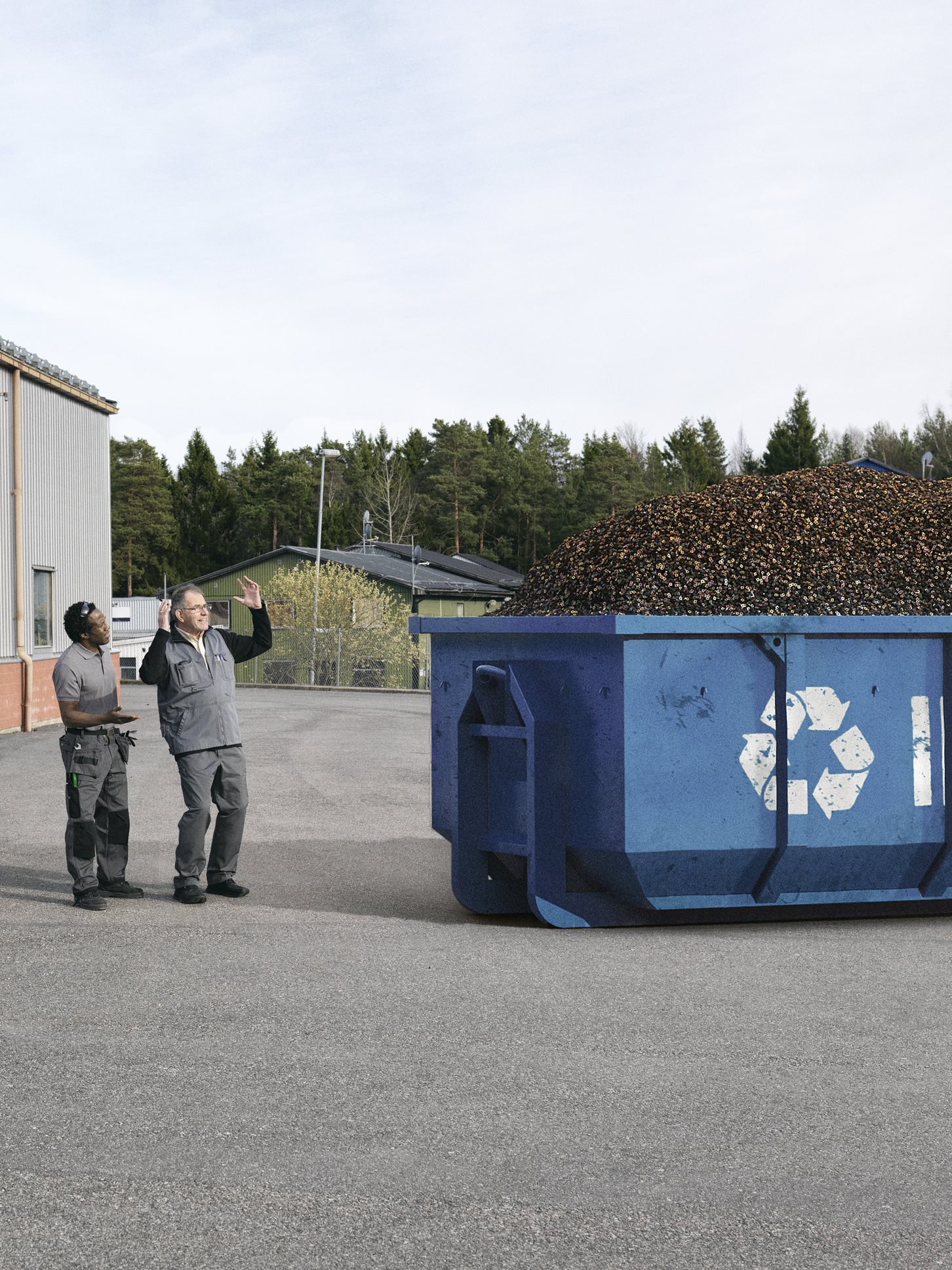
Sustainable Business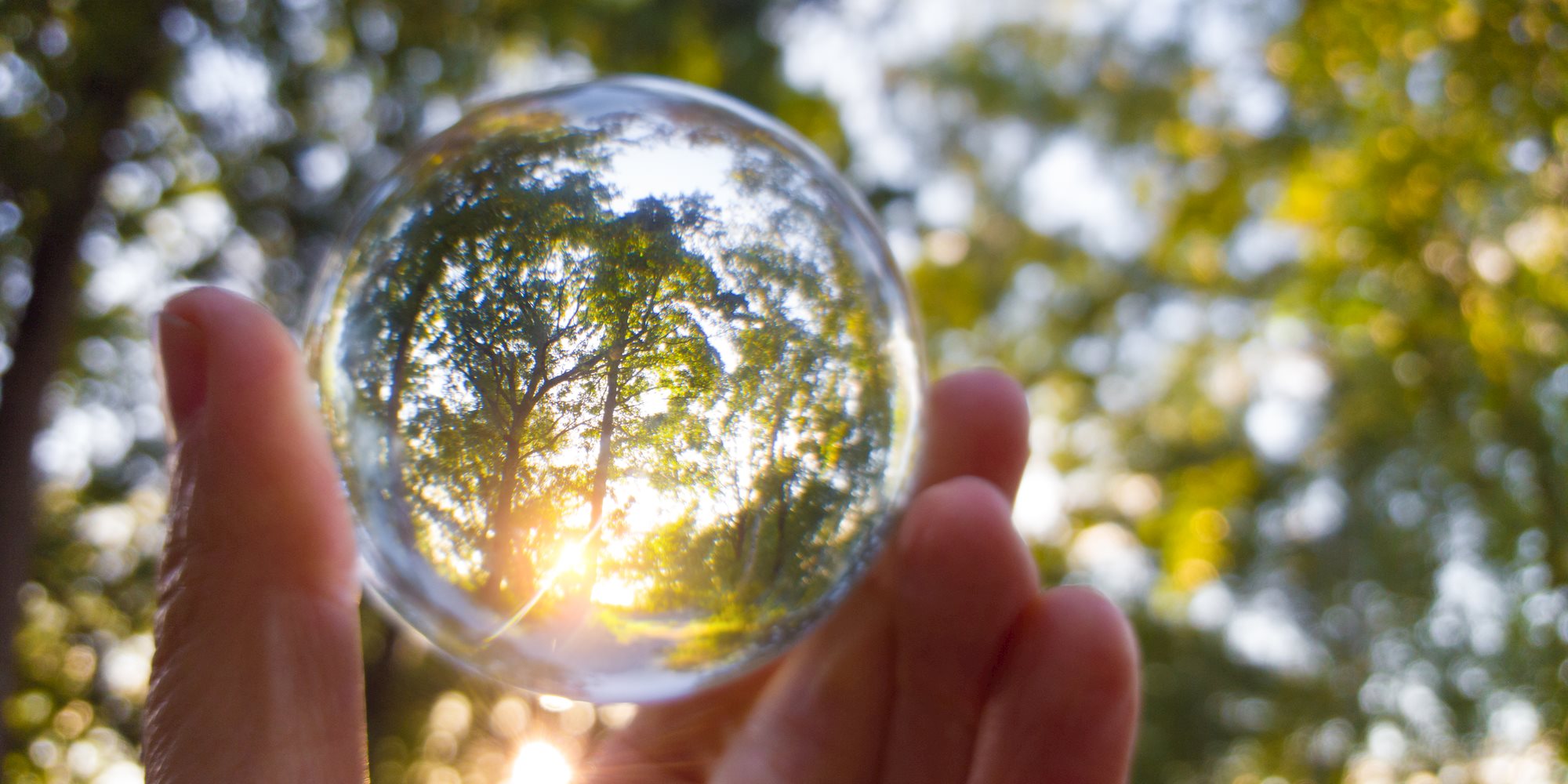
Seco® Octomill™ 06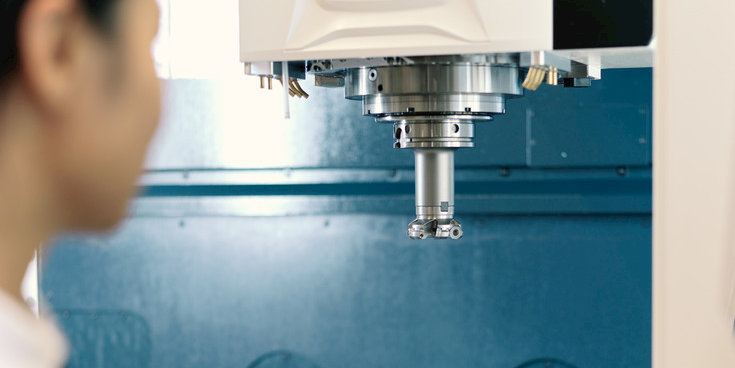