SECO TOOLS OPTIMIZES THE MANAGEMENT OF ITS PRODUCTION UNITS WITH TDM SYSTEMS’ SOLUTION
In 2018, Seco Tools launched a pilot project at its Bourges site. This aimed to optimize production processes, using TDM Systems‘ software - specialized in the management of cutting tools, gauges, calibration equipment and fixtures. Through the collaboration with TDM Systems, part of the same group, Seco Tools has reaped many benefits: productivity gains, increased reliability, and optimization of consumable stocks.Seco Tools, part of the Sandvik Group, is a global player in complete cutting tool solutions for industry. In 2018, as part of a group-wide digital transformation project, Seco Tools launched a pilot project at its Bourges site. This aimed to optimize production processes, using TDM Systems‘ software - specialized in the management of cutting tools, gauges, calibration equipment and fixtures. Through the collaboration with TDM Systems, part of the same group, Seco Tools has reaped many benefits: productivity gains, increased reliability, and optimization of consumable stocks. This solution, centralized on a server at Seco Tools‘ headquarters in Fagersta, Sweden, is now being deployed at the production sites in Pune (India) and others worldwide.
- Productivity & quality gains due to excellent tool data and its continuous use
- Increased reliability single, centralized, and always up-to-date tool data base
- Optimization of consumables visualization of the location of each tool
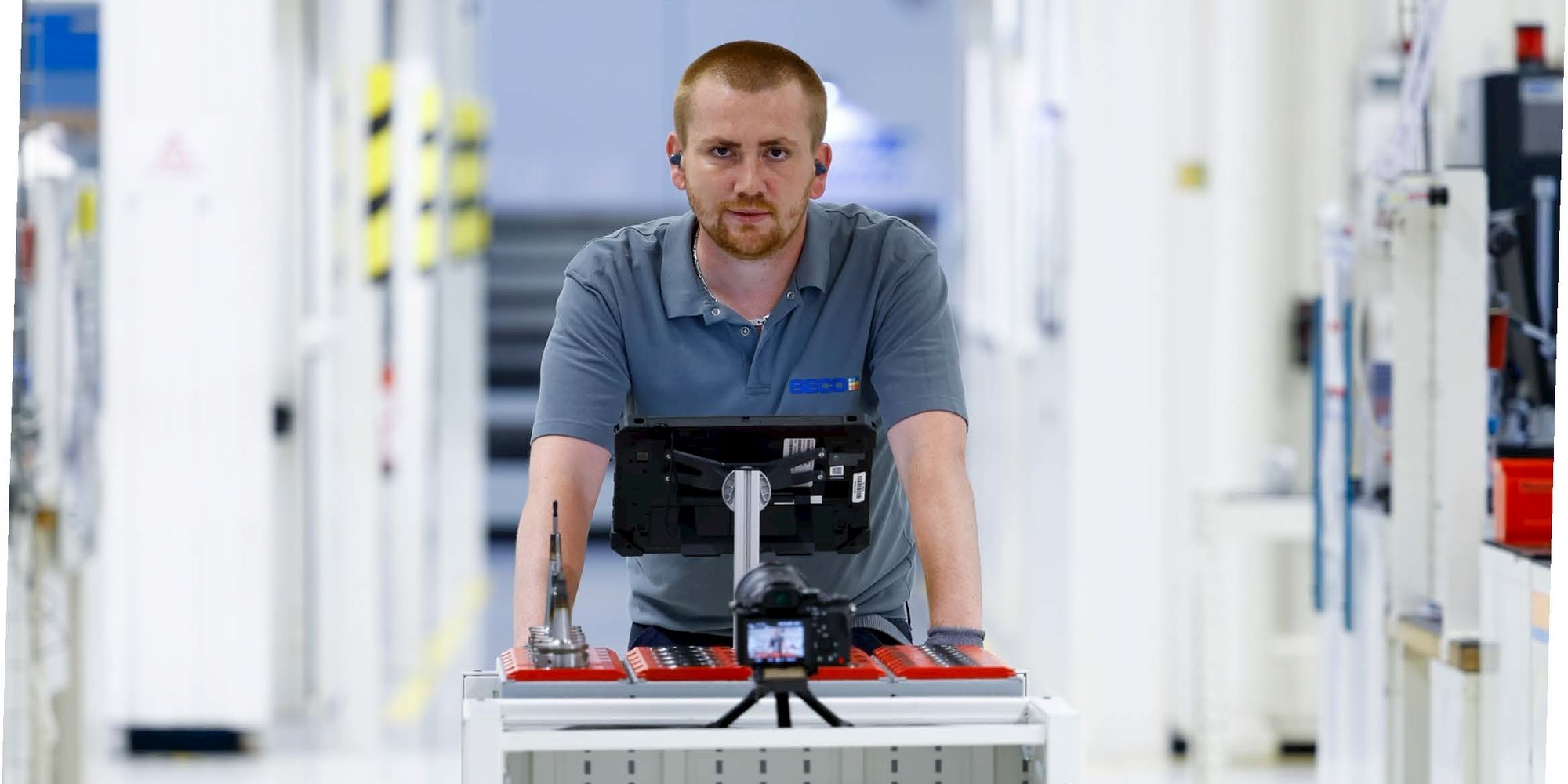
In 2015, Seco Tools launched an extensive digital transformation project. The goal was to implement an Industry 4.0- like approach, capitalizing on innovative solutions to lower production costs. Launched in 2018 on the Bourges pilot site, the collaboration with TDM Systems, is part of this project. It aimed to leverage modules of the TDM Global Line solution to optimize production processes and streamline tool data, to maximize machine utilization and operator execution speed.
The objective was to move away from the predominantly manual management of tool data and make the complete list and characteristics of each tool available centrally and digitally.
This data is essential to allow ad hoc programming of the machine before each production cycle. The machine must be perfectly adapted to each tool, otherwise it will not function properly. At the same time, these same tools must be physically available, within the operator‘s reach, with the right assembly, to be quickly mounted on the machines. The downtime of the latter is thus minimized.
Prior to the collaboration with TDM Systems, Seco did not have a solution for managing tool data within a production unit. Each operator manually listed the tool data on his own Excel spreadsheet, copying it from existing and not necessarily up-to-date files. These data files were scattered, heterogeneous and did not communicate with each other. The good continuity of the operations thus often depended on the knowledge of the people who knew where the tools were and how to program their use by the machines. The process was therefore time-consuming, potentially error-prone, and problematic during vacation periods. It also did not encourage the optimization of each machine.
To implement effective data management and governance, Seco Tools wanted to streamline this process. Since TDM Systems is also part of the Sandvik Group and specializes in tool management solutions, collaboration was a natural fit. With TDM Systems, Seco Tools was able to have an application that was seen as a single source of information and that would allow anyone in the production unit to access the necessary tool data, according to each need, at the right time and in the right place.
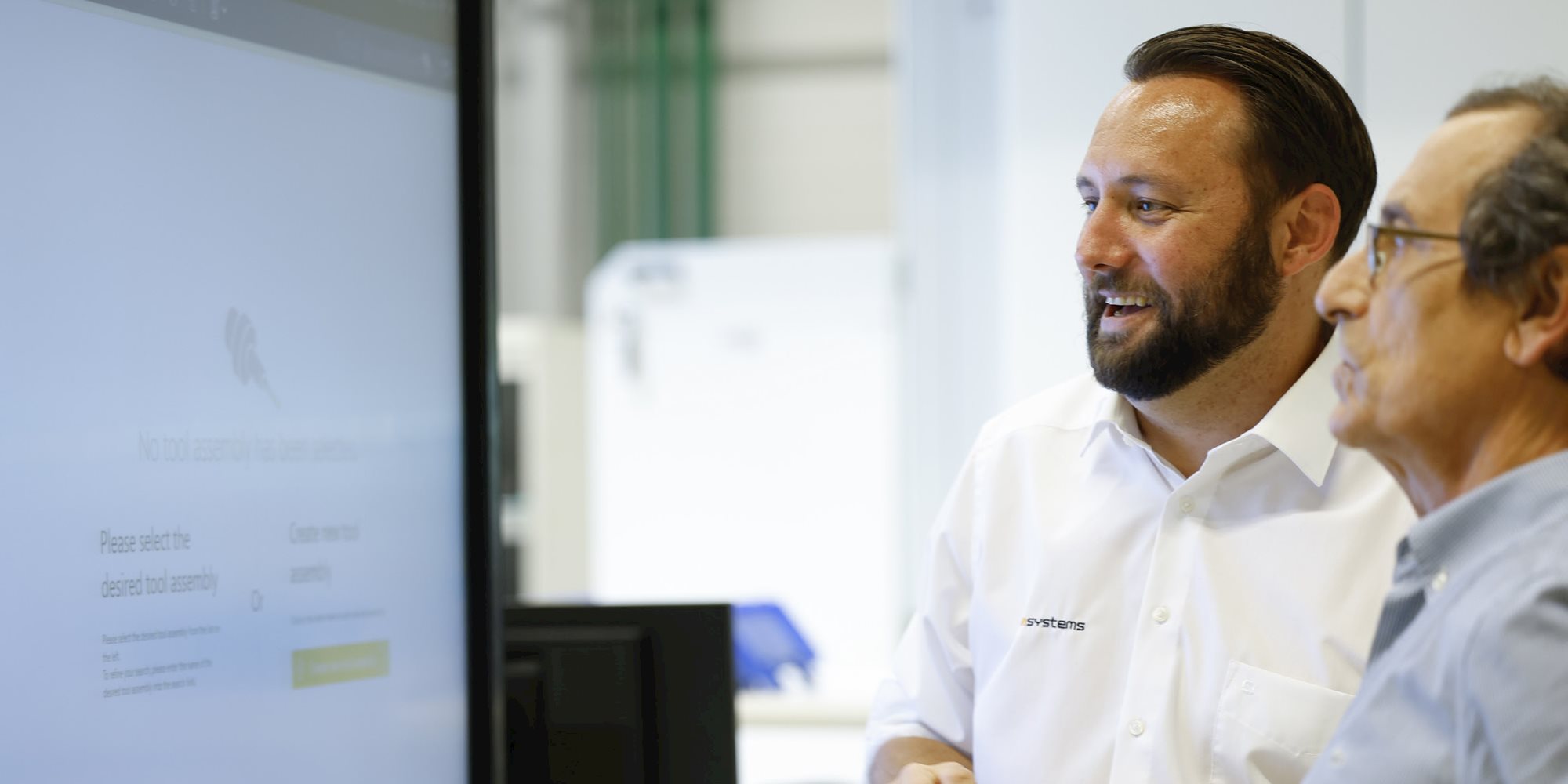
The partnership between the two entities was envisaged from the outset as a win-win cooperation. It would allow Seco to benefit from TDM Systems‘ expertise and support. In return, the Bourges site would be a showcase for TDM Systems‘ solutions to customers and other Sandvik group entities.
Seco Tools has opted for modules that are now combined in the TDM Global Line solution. These modules offer different interfaces, adapted to each need, which allow the management of all technical data used in a production unit. A project team, led by a Seco Tools production manager and a TDM System expert, was set up. To initiate the transformation process and become familiar with the tool, the team decided to start with the cutting tools and tool holders for machining assemblies.
As a first step, a database of more than 1,200 references was created, integrating all the information and characteristics related to the cutting tools and completed by a digital catalog composed of 2D and 3D graphics. Information such as videos or photos could also be added to the tool, if needed, to better guide the operators. Once the database was created, for each NC machine programming, it is then sufficient to transfer this complete tool data via an interface from the TDM tool to the CAM system NX at the touch of a button. After finalizing the NC program, all machining information such as tool lists, necessary equipment and the machining program goes back to the TDM system.
Today, the employees of the production units at the Bourges plant have access to a common application and methods that provide them with more services, without completely changing the way they work. They have moved from paper Excel files, produced manually and laboriously, to a digital
format with connected tablets that give them access to reliable and centralized data, where and when they need it. Programmers gain speed of execution, reduce the risk of errors, and maximize machine uptime. Thanks to the 3D visualization, it is even possible to locate each tooling within the workshop, to know if it is used and by which operator. Consumable expenses have thus been reduced.
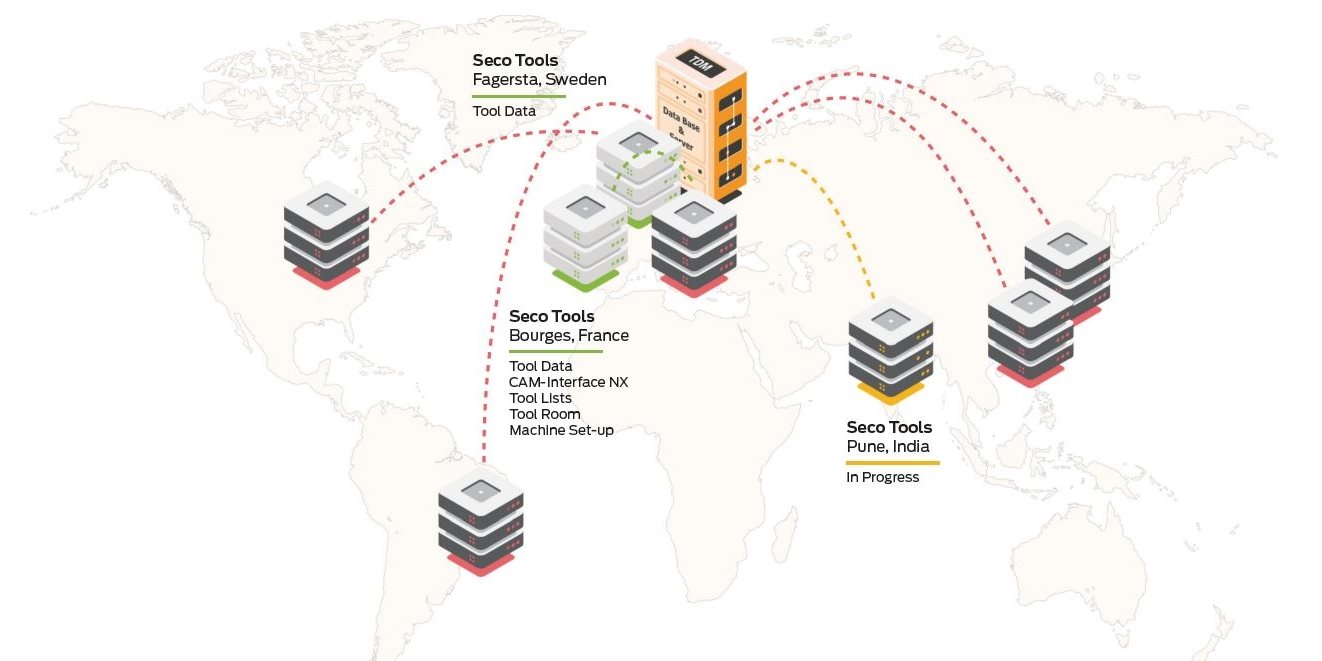
Once the process was mature in Bourges, the project began to be deployed in Pune (India) and Arboga (Sweden ), from servers hosted at Seco‘ s parent company in Fagersta (Sweden). Since the database was already created and centralized on these same servers, both sites were able to use it immediately. In addition to optimizing IT costs, this centralization was very useful during the lock down period because the project could continue to be deployed and controlled remotely. Roch Rivière, TDM Administrator at Seco Tools, comments on the project: „We are very satisfied with the collaboration with TDM Systems. Seco Tools, a global group, now has a solution that forms a common backbone for harmonizing the management of its production units. With unified working methods and data, it is possible to increase our flexibility by transferring the production of certain parts to different
factories if necessary. This allows us to serve our customers with the same quality and responsiveness no matter where they are located”.
He adds: „Our customers are very interested in the technology showcase that Seco Tools provides. We regularly discuss with them all the innovations that the TDM Systems solution has enabled us to implement and the benefits it brings us in terms of productivity gains and speed of execution”.
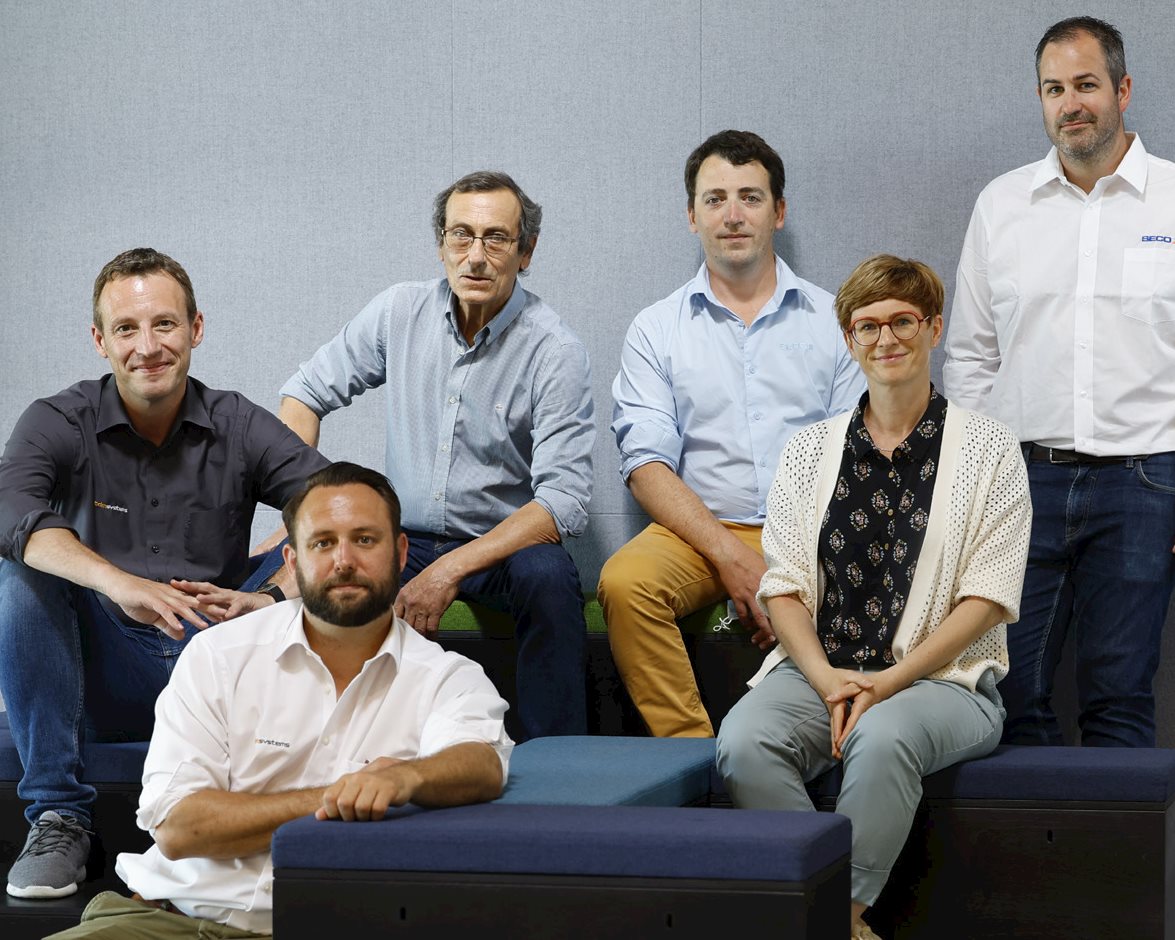
This was collaboration at its finest. Working with a great, motivated team, we were able make the shift from a local tool data management system to a scalable, global manufacturing knowledge platform. Thank you Vincent Bataille Roch Rivière, Geoffrey Chalivoy and also Daniela Steinhart for the project and video making.