Seco's Experts Answer your Drilling Questions
Choosing the right drill for your application is essential for sustainable, cost-effective drilling. Whether you have questions about drill geometry and composition, coatings or coolant, Seco experts have the answers you need that will minimize your cost per hole.
TABLE OF CONTENT
What kind of materials are drills made of and what can they machine?
Choosing a drill’s composition will vary depending on its use. Generally, drill bit materials are available in three categories.
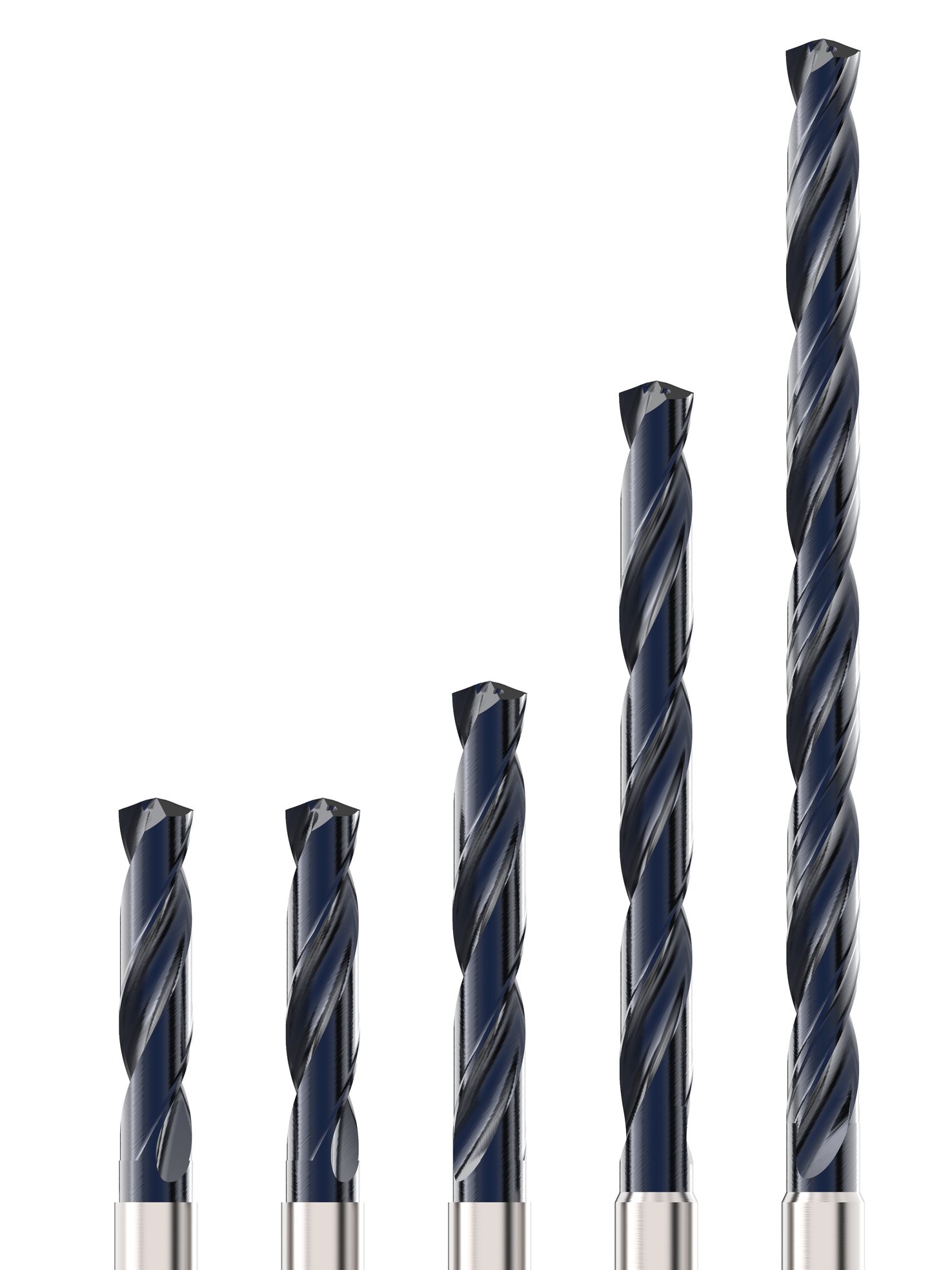
HSS drills are a good choice for drilling soft steels and plastic. They are economical and adaptable for many drilling applications.
With the addition of 5-8% of cobalt, HCSCO drills provide improved hardness and wear properties and are suitable for drilling steel, cast steel, titanium and other hard materials.
Carbide drills maintain sharpness more than any other drill material and are best for the hardest materials, including ceramics, glass, stainless steel and cast iron. While outperforming all other drill materials, carbide drills are brittle and more expensive.
Drills can be custom made to virtually any size, depending upon the application. However, industry standards have set defined drill sizes that are most commonly produced by drill manufacturers.
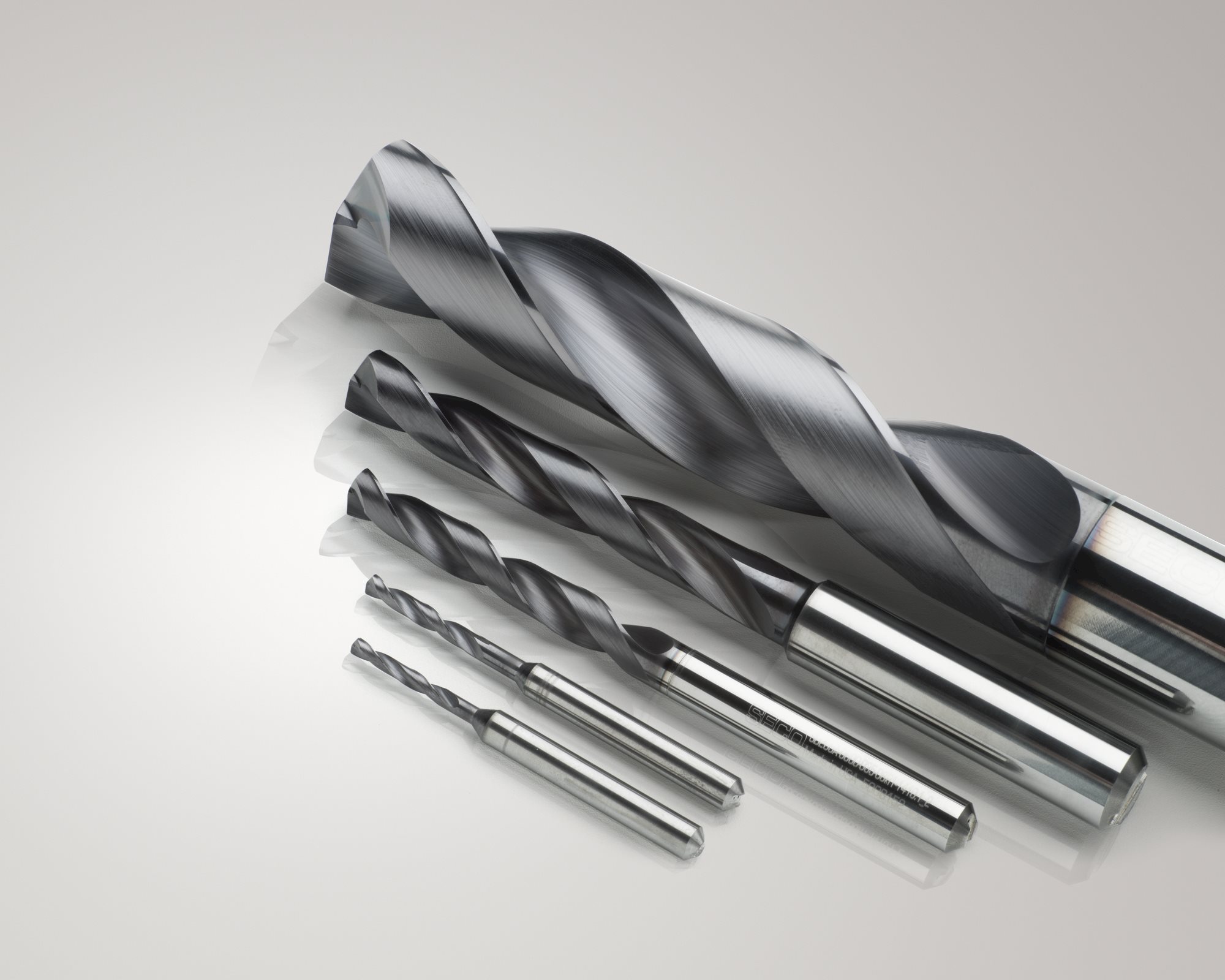
Drill lengths are also variable, however, there are defined types:
- Jobber length – The most common type of general-purpose drill made for a wide variety of jobs, combining strength and accuracy.
- Mechanics length – These drills have shorter flutes than jobber lengths, providing more strength and rigidity.
- Screw machine length – These are the shortest of the standard drill bits with more rigidity that reduces deflection.
- Extended length – Designed to drill deep holes, extended length drills incorporate long shafts and flutes.
- Taper length – These drills fall between the jobber and extended length bits in terms of dimension.
Drill geometry is the complex relationship between the various angles and aspects of the drill. The length and bore of the drill along with the configuration of its cutting edges, flute profile and point angle impact performance, accuracy and tool life.
Optimizing these relationships to the application, production goals and workpiece is essential to efficient, cost-effective drilling.
Components of drill geometry to be considered are:
- Point angle – Located at the head of the drill bit, the point angle determines wandering, ease of centering, heat conduction and chip flow.
- Main cutting edges – Connected by the chisel edge, cutting edges perform the actual drilling process.
- Chisel edge – Located in the middle of the drill tip, the chisel edge length determines drill sharpness.
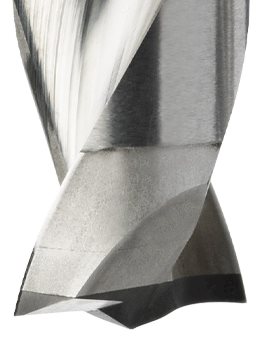
- Flute profile – Facilitates chip removal and coolant flow.
- Guide lands – Guide the drill as it works through the hole.
A drill’s rake or helix angle is the angle between the drill’s leading edge and its axis. Rake angles are generally available between 18 and 45 degrees with 30 degrees being the typical value. Higher rake angles form tightly rolled chips. Lower rake angles tend to form chips that are more loosely rolled. Rake angles also affect cutting temperature and tool life.
Large rake angles are generally employed when drilling softer materials, while smaller angles are used when drilling hard materials that produce smaller, shorter chips.
DIN 1836 addresses helix angles with three groups:
- Type N – Normal helix for materials with normal hardness such as non-ferrous metals and cast iron. Type N helixes are not suitable for softer materials.
- Type H – Longer drawn helixes for brittle material such as steel, hard plastics and laminates.
- Type W – Tightly spiraled helix that produces long, curling chips in soft plastics and metals.
A drill’s cutting edges are connected by the chisel edge and are responsible for the actual drilling process. Long cutting edges provide better performance in the drilling process.
Find the Right Drill with our guide/whitepaper The goal of metal cutting applications, including holemaking, is to keep tooling and operational costs low and output high. While many manufacturers carefully consider the tools they use for milling and turning, they may not treat the selection of holemaking tools as an equally critical decision, but they are. Tips and tricks are always welcome. Learn more here |
What drill coatings are available, and which are best for a given application?
There are a variety of coatings available for drills, each with specific advantages and more appropriate than others for specific applications. As in most tool selection questions, the answer to which is best is primarily driven by the operation and workpiece. Drill coatings also extend tool life, thereby reducing the overall cost per hole.
Coatings are generally applied to drill cutting edges via a process called Physical Vapor Deposition (PVD). PVD uses a physical process such as heating or sputtering to produce a vapor of material that is then deposited on the object being coated.
The most common drill coatings are:
- TiN, or titanium nitride, composed of titanium and nitrogen that has been shown to double and even quadruple tool life for general purpose drilling.
- TiAIN, or titanium aluminum nitride, which can extend tool life up to 10 times and offers excellent heat and oxidation resistance. Suitable for alloyed and stainless steels at medium to high cutting speeds.
- TiCN, or titanium carbonitride, provides very high hardness and wear resistance and can extend tool life up to five times that of uncoated tools. Works best on bronze and copper alloys as well as aluminum bronze and nickel alloys.
- ALTiN, or aluminum titanium nitride offers superior hardness for high-temperature applications when drilling very hard or abrasive workpieces.
The primary disadvantage of coated drills, however, is that they sometimes cannot be resharpened.
What type of coolants are available and how should I use them?
Coolant and lubrication during the drilling process significantly improves tool life, chip evacuation and hole quality, especially in tough workpieces such as alloyed or stainless steels. Heat reduction is even more important in drilling operations because most of the energy is transformed into heat. In drills with multiple land margins there is more contact between the hole surface and the tool, making heat control even more important.
There are several different types of coolant available, and selection is dependent upon the application. Among them are:
- Straight cutting oils – Also known as neat oils, cutting oils are 100% petroleum or mineral oil used in broaching, tapping and deep-hole drilling. They are especially suited to drilling super alloys and stainless steel.
- Water-soluble cutting oil – Though it lacks the lubricity of neat oils, soluble oil is more versatile and can be used in a wide variety of light- to medium-range applications.
- Synthetic and semi-synthetic fluids – Provide cooling and lubrication for high-speed drilling in moderate to heavy applications.
Internal coolant is always recommended for drilling and is the best option for tough work materials such as super alloys and stainless steel. For effective internal cooling, through-cooling tools have cooling channels that direct coolant directly to the cutting zone.
If external coolant is used, it is important to ensure the coolant flow is directed as parallel as possible to the drill as it reaches the cutting area. For acceptable chip evacuation, the maximum recommended drilling depth using external coolant should be no more than 3X diameter and reduce cutting speed by 20% as compared to operations using internal coolant.
What are common drilling issues and solutions?
Though there can be any number of issues that arise, by far the most concerning is drill breakage. Broken tools obviously have to be replaced at the expense of time and money, but they also increase the risk of scrapped parts and waste.
Some causes of drill breakage are:
- Improper speed – Large-diameter drills operate at lower speeds than small-diameter drills. Drilling too fast or too slow may cause drills to bind and break. Workpiece hardness also determines drilling speed. Consult manufacturer tables for proper speed.
- Excessive pressure at the bottom of a blind hole – Chip buildup at the bottom of a blind hole due to insufficient removal can cause breakage. Reduce pressure when nearing the bottom.
- Clogged flutes – When flutes become clogged with chips, they are not evacuated properly, causing the bit to bind in the hole and break. Opt for a drill with wider flutes and/or withdraw the drill at regular intervals.
- Improper drill point for the application – Different point angles are required depending on the hardness of the workpiece. Consult manufacturing tables for the correct point angle for your application.
- Excessive feed rate – Exceeding recommended feed rates break down cutting edges and the drill point, resulting in splitting or breakage. Reduce feed rate to relieve drilling pressure.
Efficient drilling requires minimizing cost per hole. Drills that wear too fast require downtime for changing tools, and that increases cost per hole. To avoid changing tools too often:
- Check the coolant to make sure it’s reaching the cutting point.
- Review speed and feed parameters.
- Use the right tool for the job – the appropriate drill and point geometry for your specific application can make all the difference.
Chipped cutting edges will not drill a quality hole. Chips on the cutting edge can be caused by:
- Excessive runout/loose chuck.
- Excessive/improper speeds and feeds.
- Failure to use or inadequate use of cutting fluid.
Chips that fail to break become long and stringy requiring work interruptions to unwind them from the tool. To keep chips in check:
- Increase feed rate.
- Examine the drill to make sure it’s sharp.
- Consider changing to a different drill point geometry.
What are some common drilling tips and tricks?
Follow these general guidelines for cost-effective, sustainable drilling.
Shorter drill bits decrease the drill’s ability to wander or stray from its starting point during the drilling process. As a result, shorter drill bits provide more accuracy. Because they are more rigid, they are less likely to break and are easier to use in confined areas.
A self-centering drill geometry allows for precise and accurate hole placement, eliminating the need for additional alignment tools or excessive adjustment. The drill automatically centers itself within the starting point, ensuring the hole is perfectly positioned to part requirements. Self-centering drills save time, simplify setups and reduce cost per hole.
Use drills engineered to prioritize secure drilling and maintain position throughout the drilling process to minimize unintended movement or deviations. Stability is critical for achieving accurate, consistent results, particularly when working on delicate, complex parts where precision is paramount.
Efficient chip evacuation and preventing chip buildup is essential for smooth drilling and maximizing productivity. Proper chip evacuation reduces downtime, enhances drilling performance and promotes overall productivity in the machining process.
For deep hole drilling and long drills exceeding 16XD, a pilot drill will be necessary. Drilling a pilot hole first will remove some of the material from the workpiece and reduce the force necessary to produce the final hole. Pilot holes decrease hole runout and assure maximum accuracy.
If drilling into an angled surface, machine a flat using a solid end mill via the interpolation method. If milling is not possible, reduce the drilling feed by 50% until the drill has reached full cut. Use a drill with multiple land margins and reduce feed rate by 30 to 50% during exit.
To drill cross holes, reduce feed by 50% 3mm before the crossing and maintain that low feed rate up to 3mm after passing the crossing hole. If possible, use a multiple land margins drill to improve guiding.
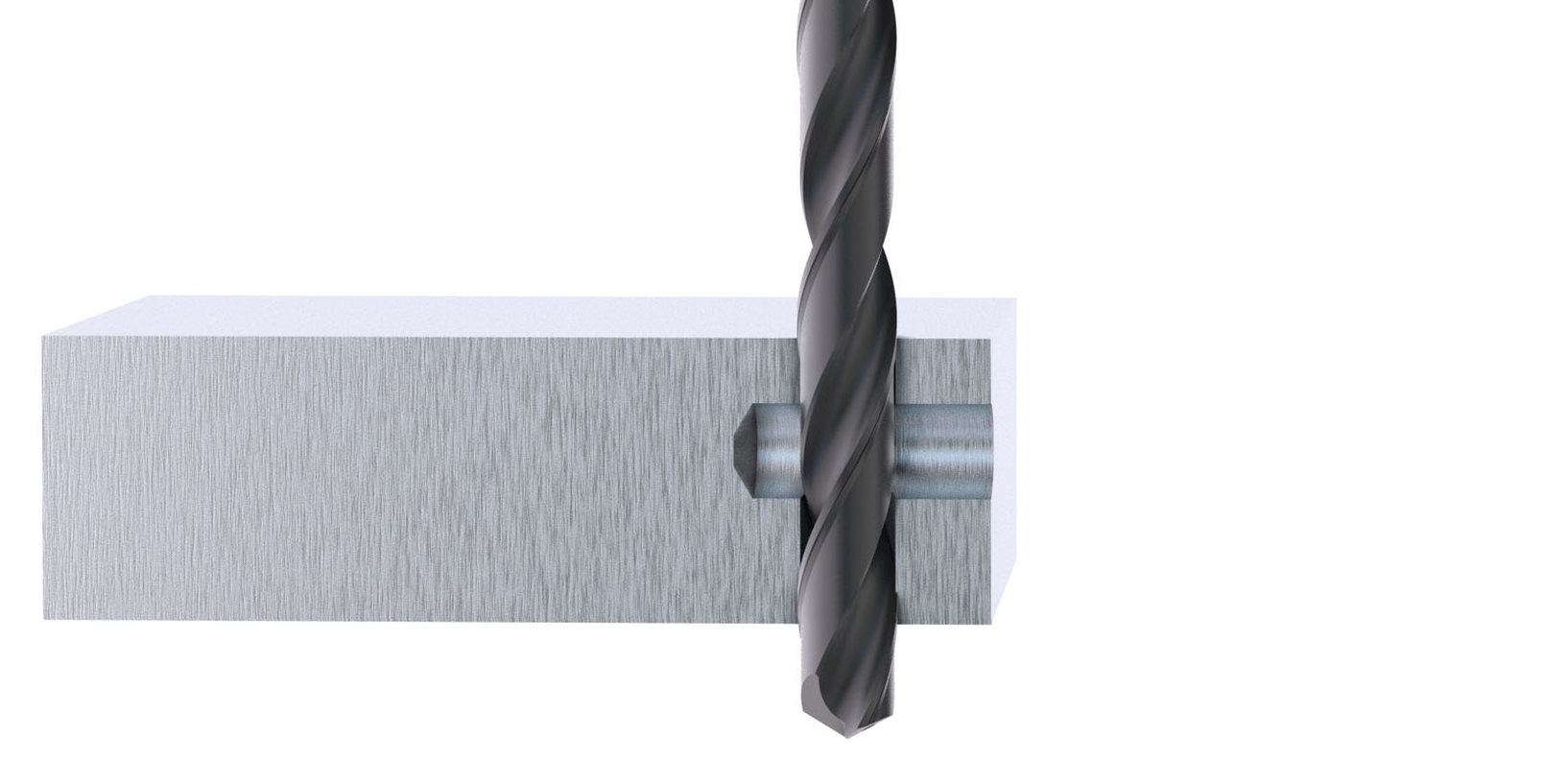
Stacked materials can be drilled effectively as long as the workpieces are clamped securely so that there are no air gaps between them. Air gaps have a detrimental effect on chip evacuation and cause drill damage.
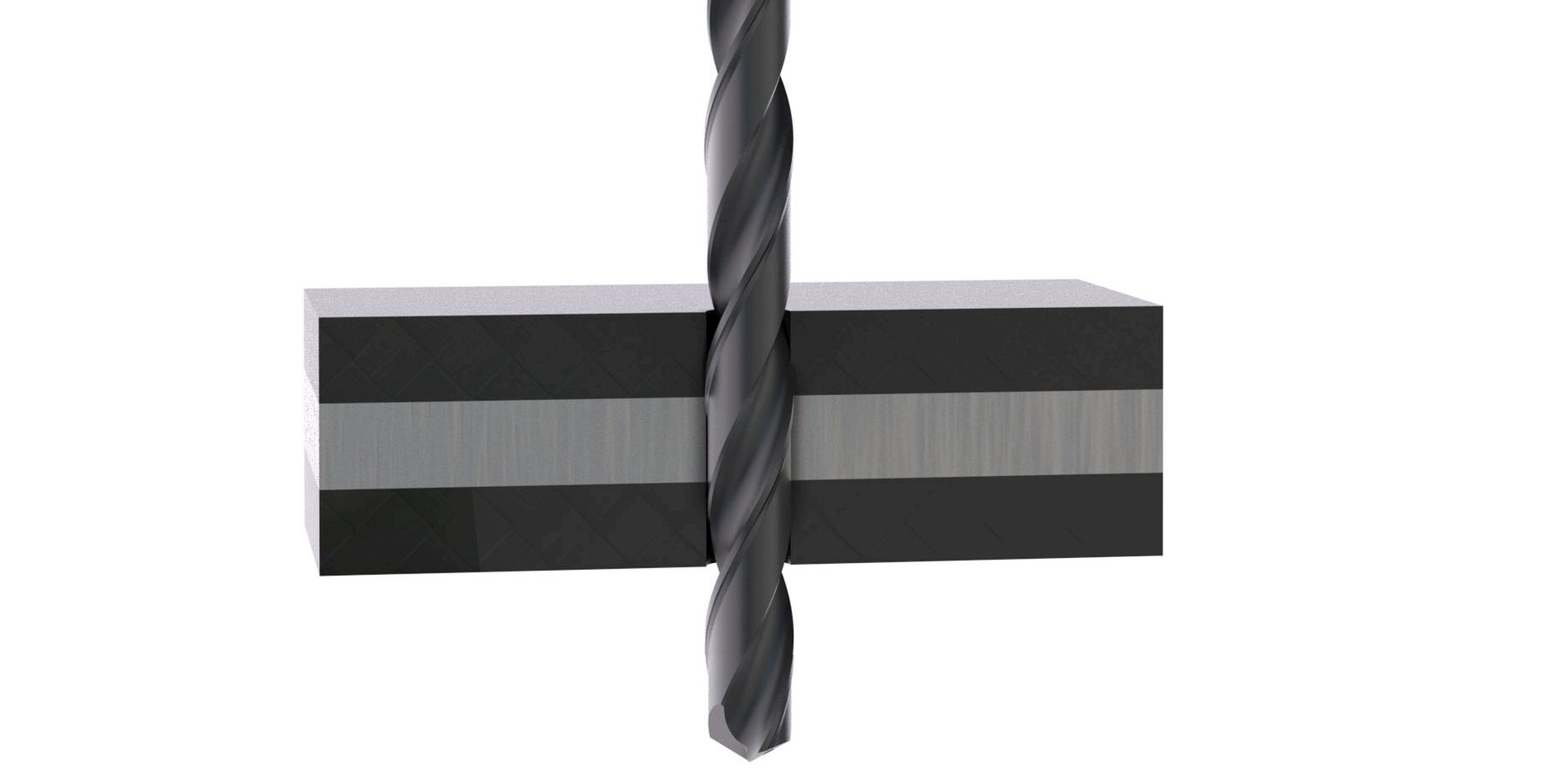
Choosing the best tool for a given application involves a broad range of considerations. Apart from universal drill geometries that are versatile and adaptable to changing applications and production needs, selecting a drill with the right features, dimensions, coatings and cutting characteristics will directly impact your performance.
For sustainable drilling at the most efficient cost per hole, contact a Seco expert to find the right tool for your job or try Suggest.