8 tips to machine titanium alloys
Learn how to machine titanium alloysOnce titanium alloys were exclusively used in the aerospace industry for components exposed to a combination of high dynamic loads and high operating temperatures. Titanium alloys are now a mainstream material, used in many applications such as jewellery, sporting equipment, surgical tools, motorsport components, and other high-performance products.
Titanium alloys are best known for their high melting temperature point, high strength and low-density properties, making them a particularly “difficult-to-machine” material. The main reasons for this are:
- Low thermal conductivity – Their low thermal conductivity increases the temperatures at the cutting edge of the tool, which causes rapid wear of the cutting tool and can cause plastic deformation of the cutting edge.
- Chemical reactivity - Their high reactivity results in chemical interaction with the cutting tool, and crater wear is a typical problem.
- Strain hardening - Another challenge when machining titanium alloys is that they work-harden, forming a hardened surface during machining, which causes notch wear at the depth-of-cut line.
- Hot hardness - Finally, the low modulus of elasticity of titanium alloys and high strength at elevated temperatures further impair their machinability.
Listen to the on-demand Titanium Webinar
- Due to the extremely low thermal conductivity, the use of high-pressure emulsion is advised.
- Cutting speeds depend on strategy but are typically relatively low and vary from 50 m/min (conventional) to 150 m/min (high-speed or advanced roughing).
- Positive geometries with tough cutting edges are highly recommended due to the material’s ductility and high chemical reactivity. AlTiN and AlCrN PVD coatings are both suitable for titanium applications and have proven successful in this area.
- Use the largest nose radius possible as this tool feature will spread the cutting forces and heat generated during the cutting process to a larger portion of the insert, decreasing point wear and increasing tool life.
- When milling on older machines, maintain a width-of-cut no greater than 30% of your tool diameter to control heat generation and tool wear.
- When roughing in milling applications, high torque machines are generally recommended when high metal removal rates are required.
- Ensure not to generate high temperatures in the cutting zone (above 600°C) as this will cause “Alpha Casing” on the material’s surface and could cause poor service life of the component. Only introduce high cutting speeds when the use of High-Pressure Coolant is being used.
- When machining on newer machines, use advanced Dynamic turning and Dynamic milling strategies to minimise heat generation and tool wear.
For more information or help contact us or visit the industry segment pages: Aerospace Industry Segment Solution or Medical Industry Segment Solution.
Follow David Morr for more articles.
Inline Content - Survey
Current code - 5fce8e61489f3034e74adc64
HOMERelated content
Challenges in titanium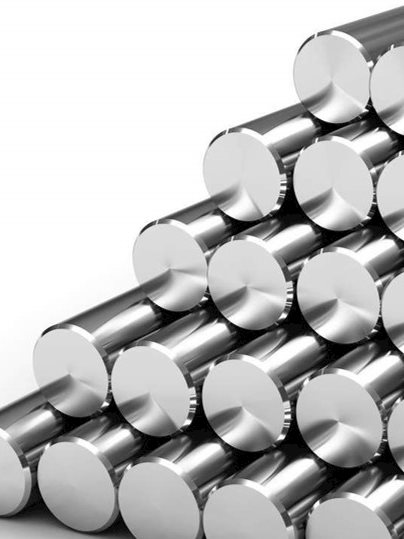
Aerospace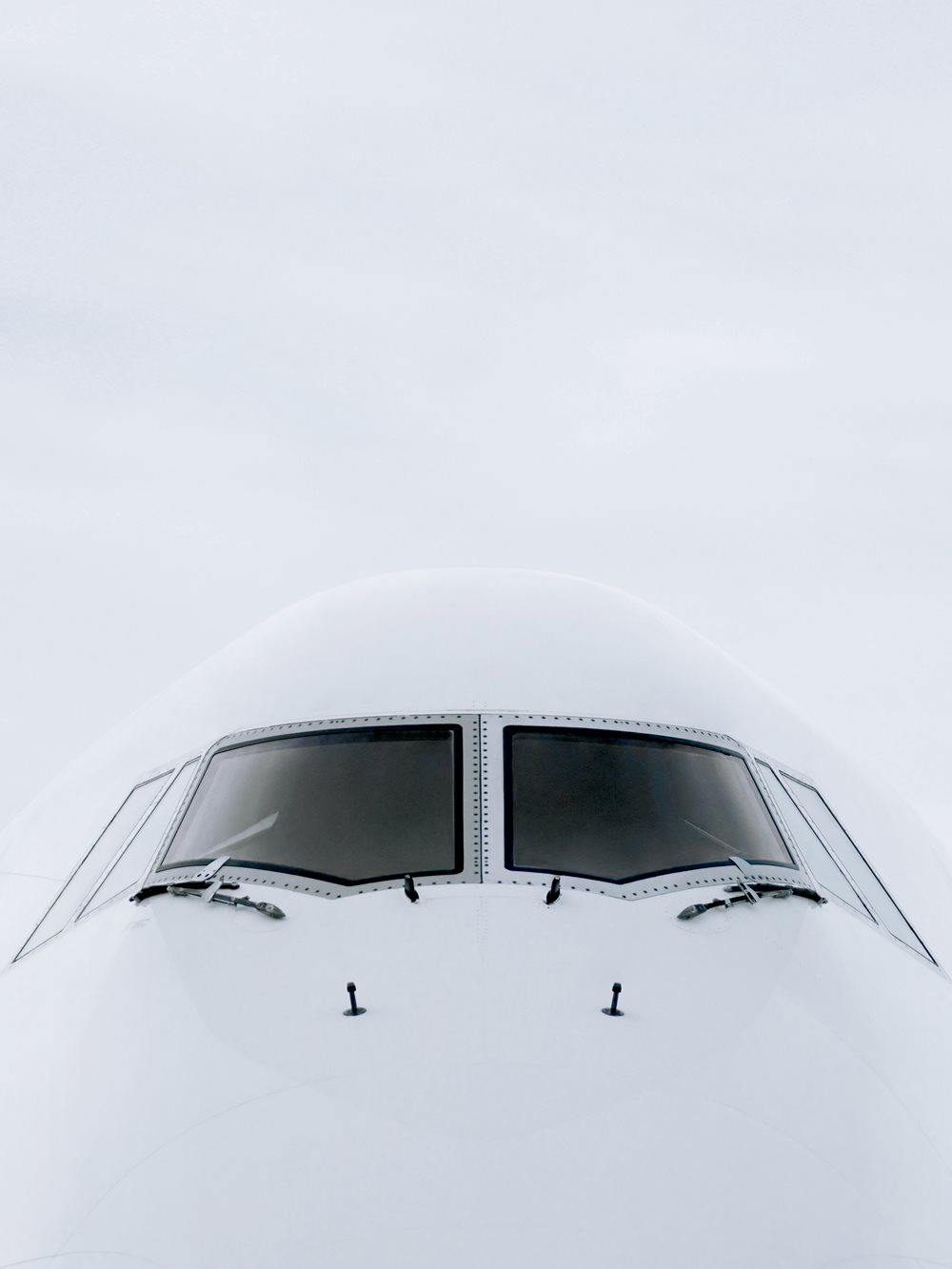
Medical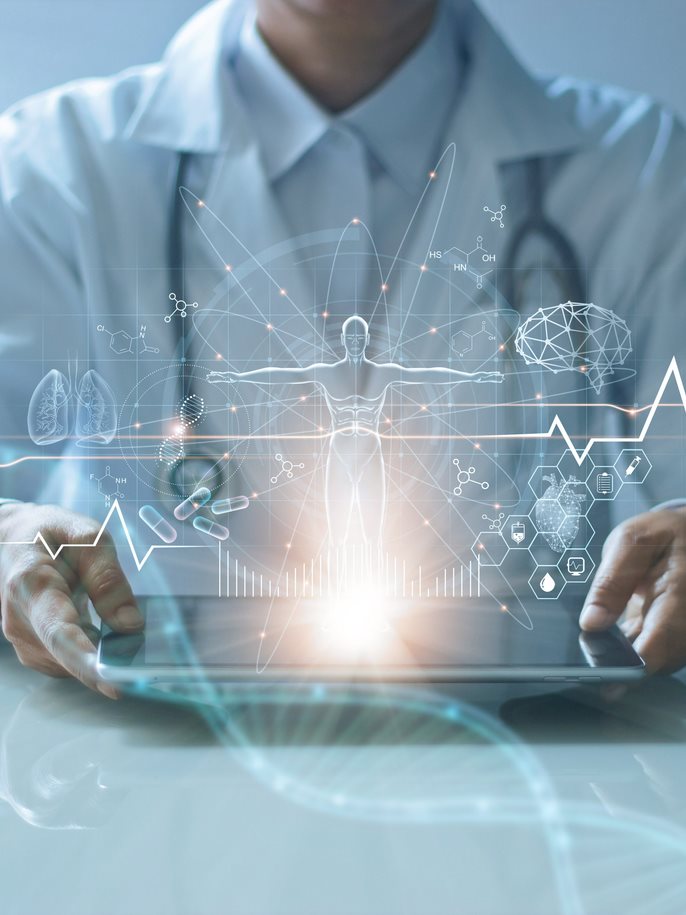
Titanium: Mastering Today’s Challenges, Shaping Tomorrow’s Trends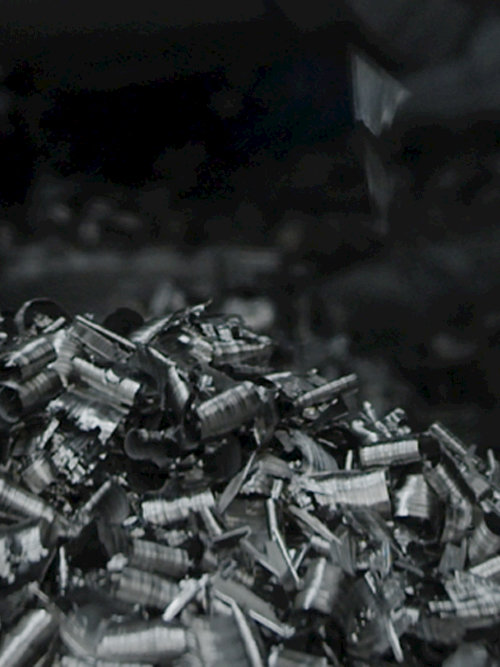
AM Titanium Blisk Demonstration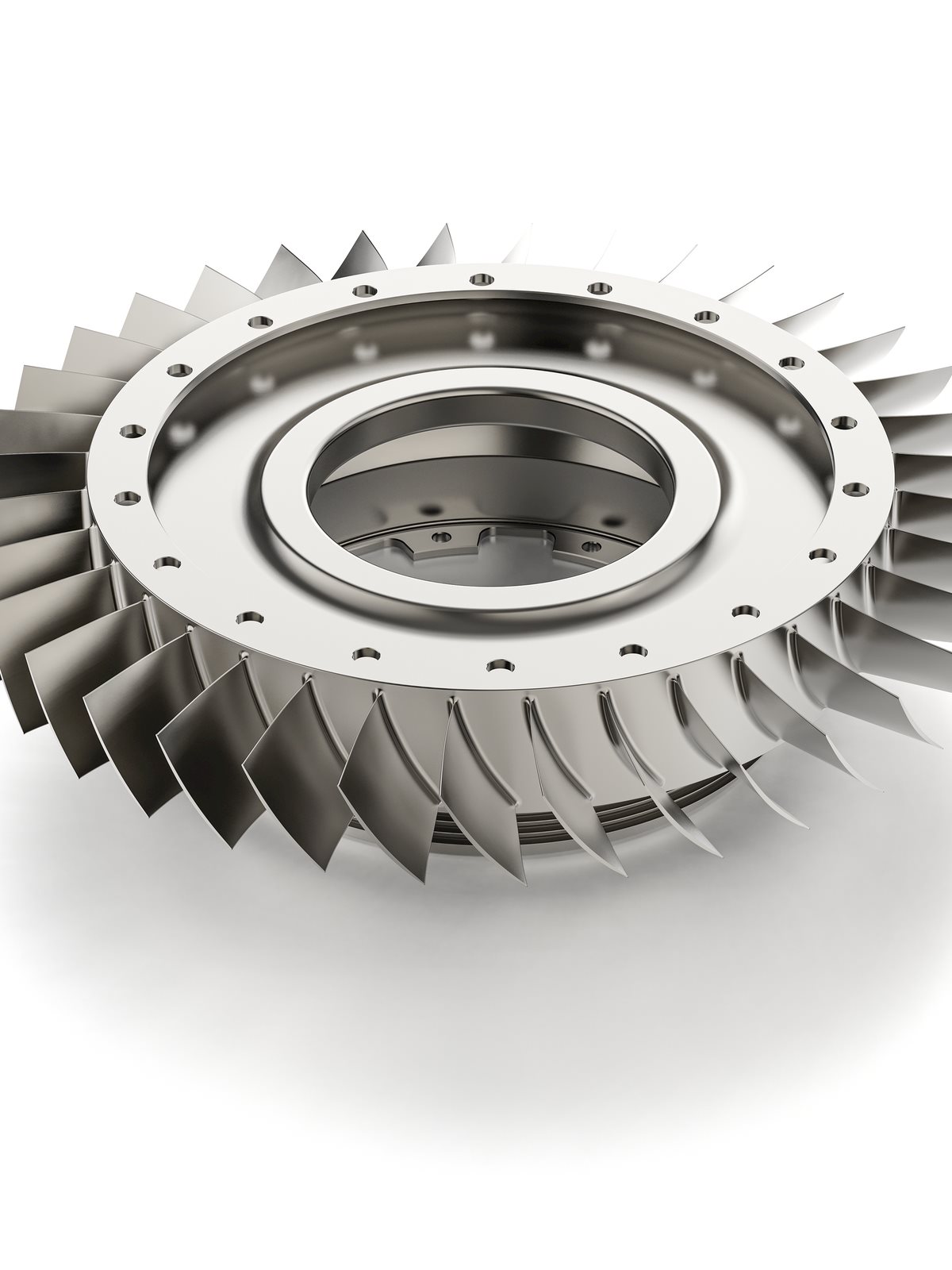
Finishing a Titanium Pylon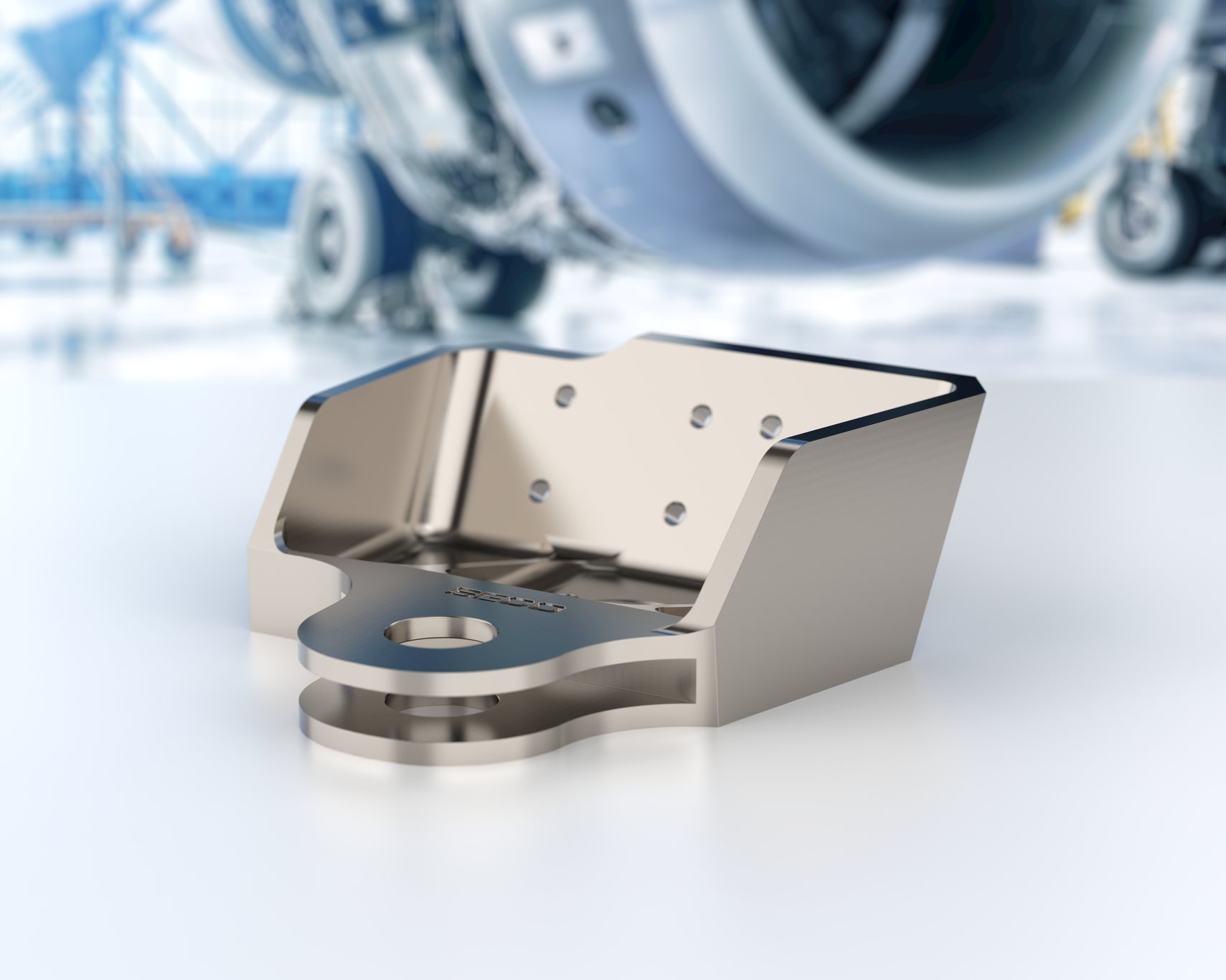
Challenges and benefits of Additive Manufacturing in the medical segment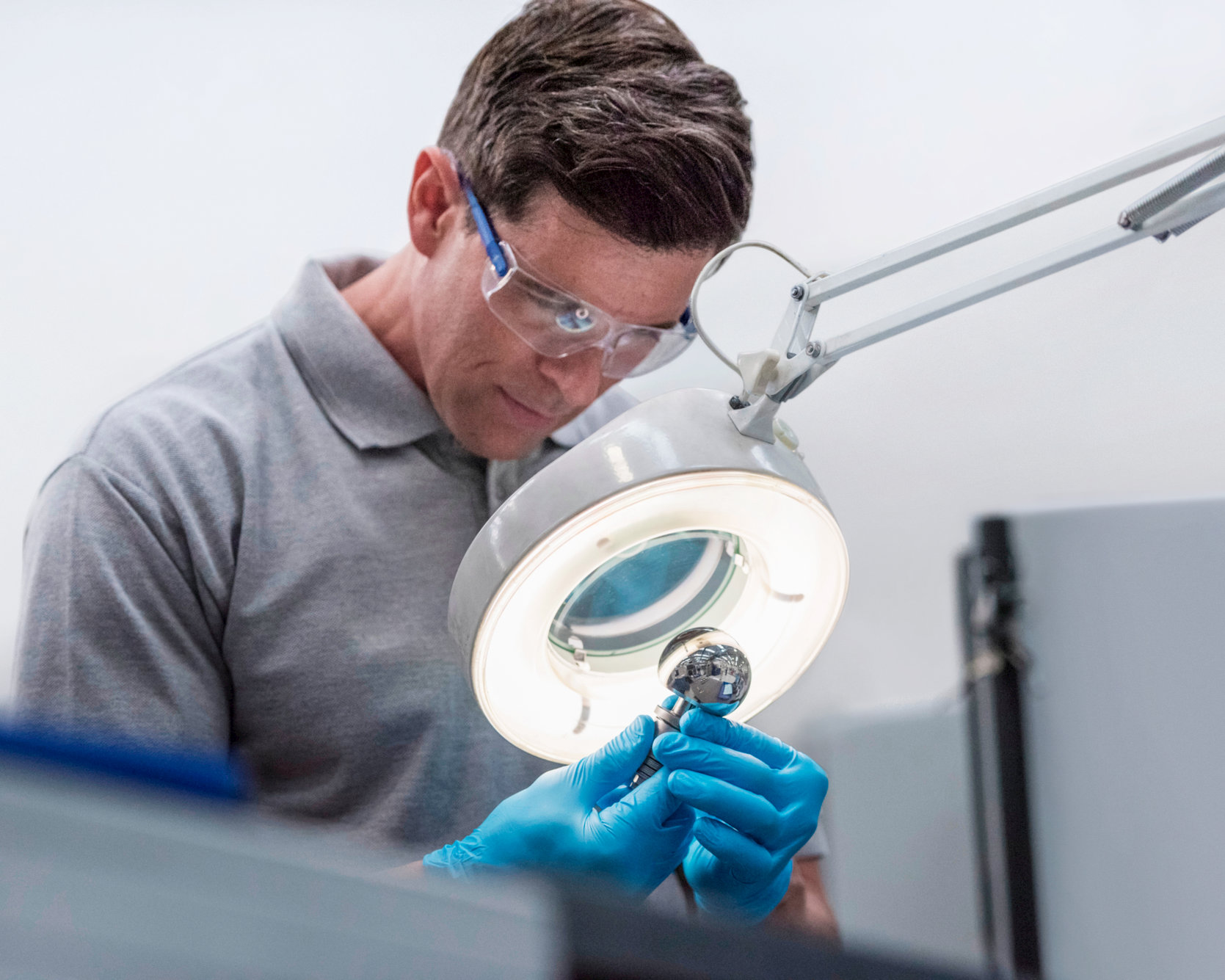
Why making an aeroplane pylon is a true collaborative process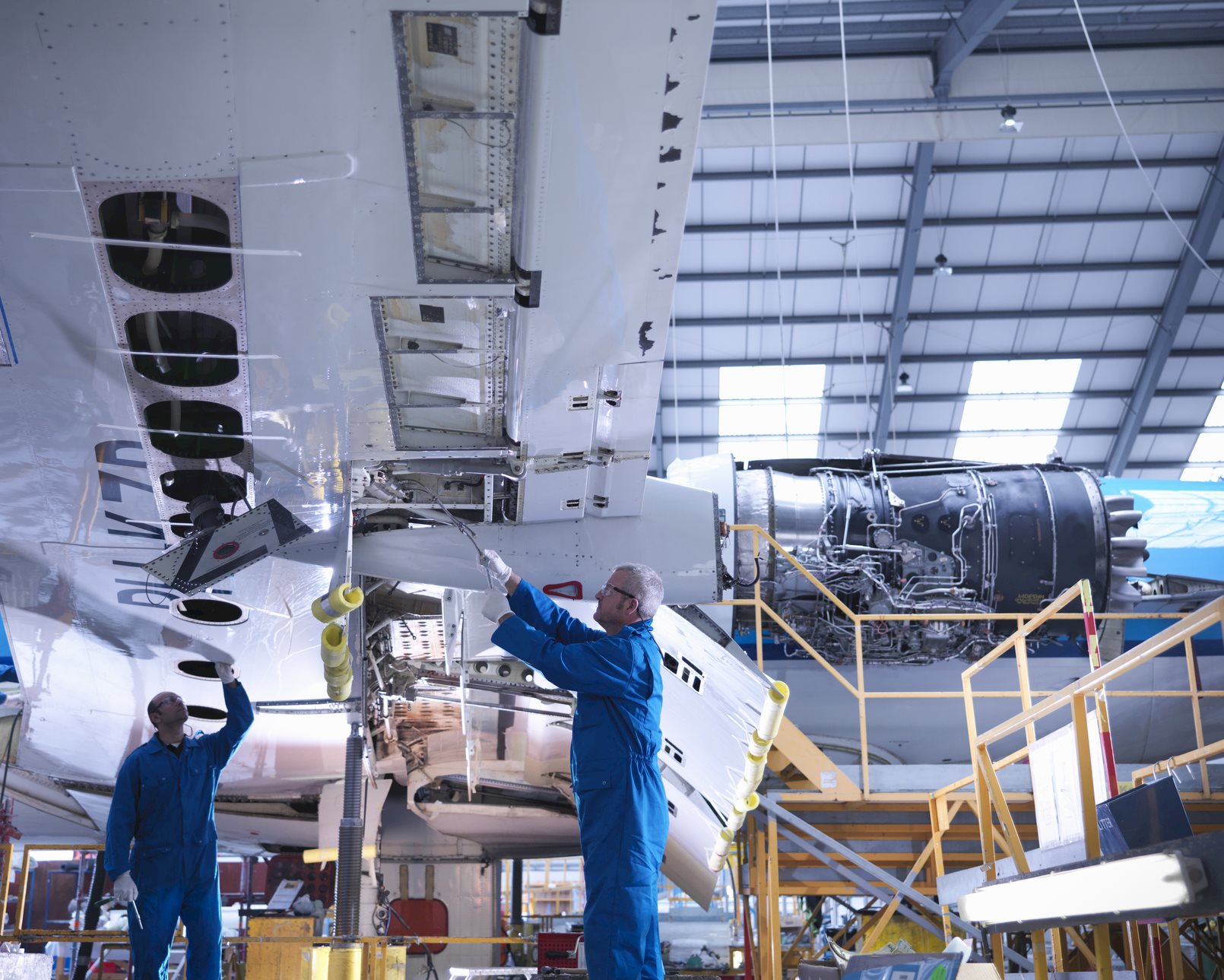
ActOn’s ‘secret weapon’ is transforming medical implants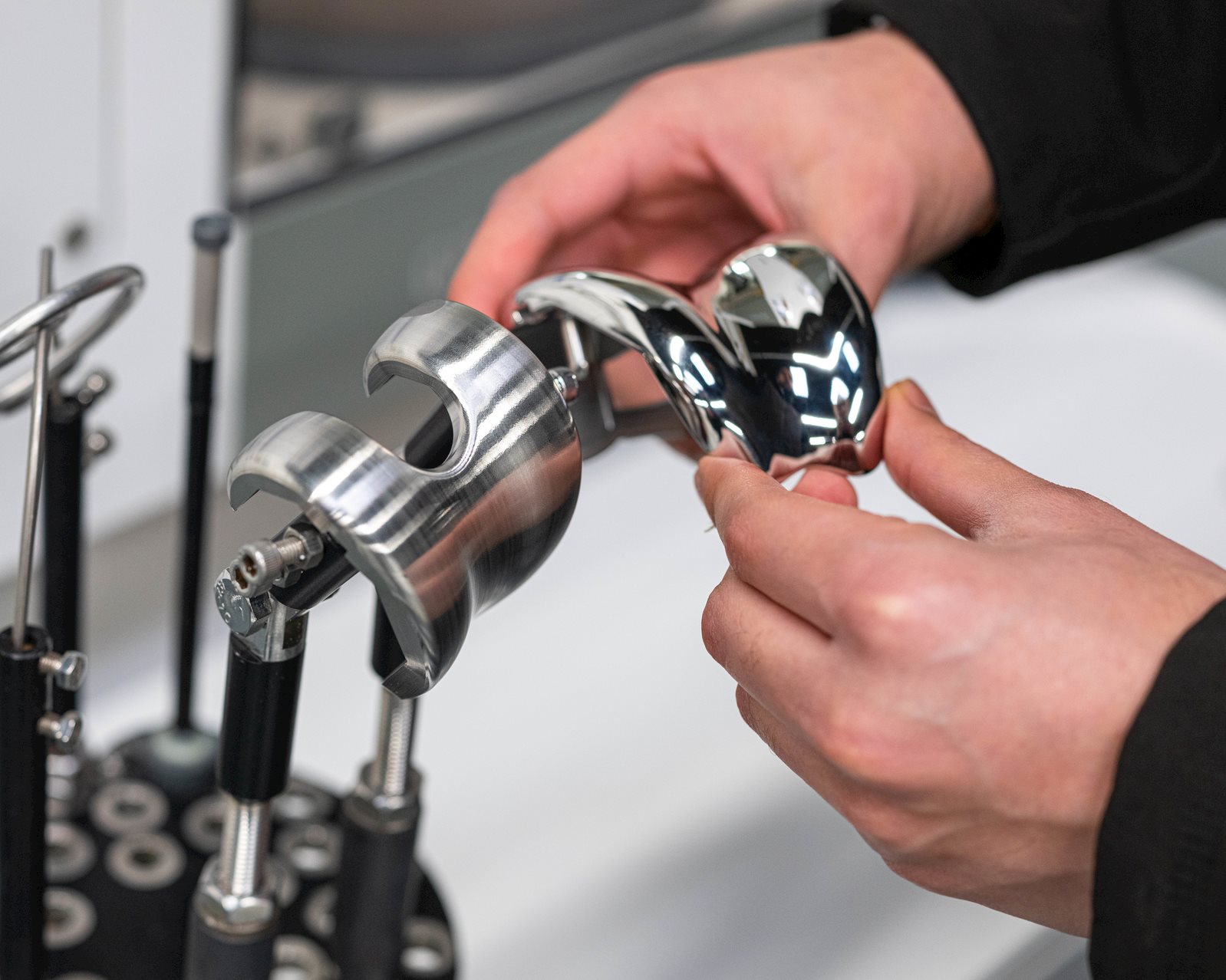
Advances in Titanium Alloy machinability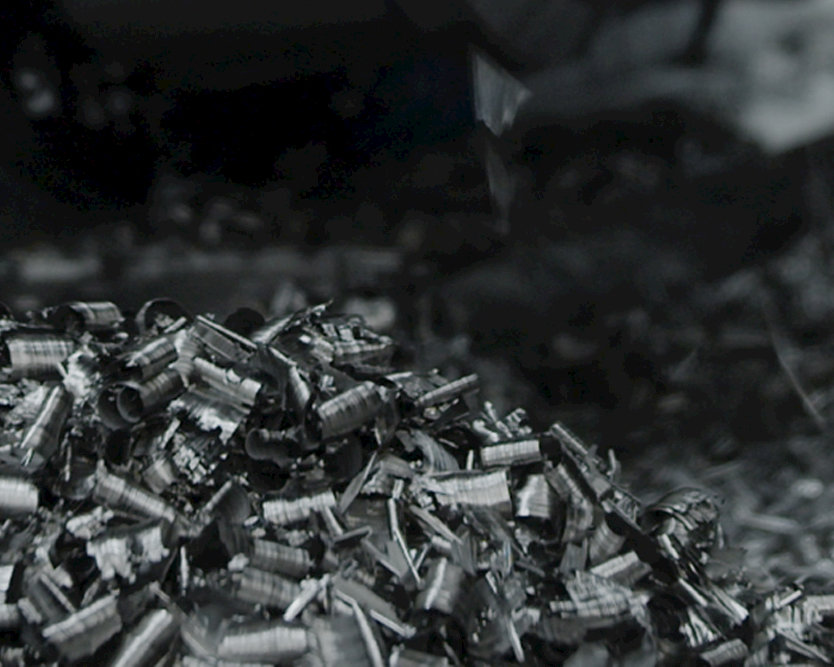
Seco and Mastercam: How Accelerated Finishing Tools Enhance Surface Finishes and Save Time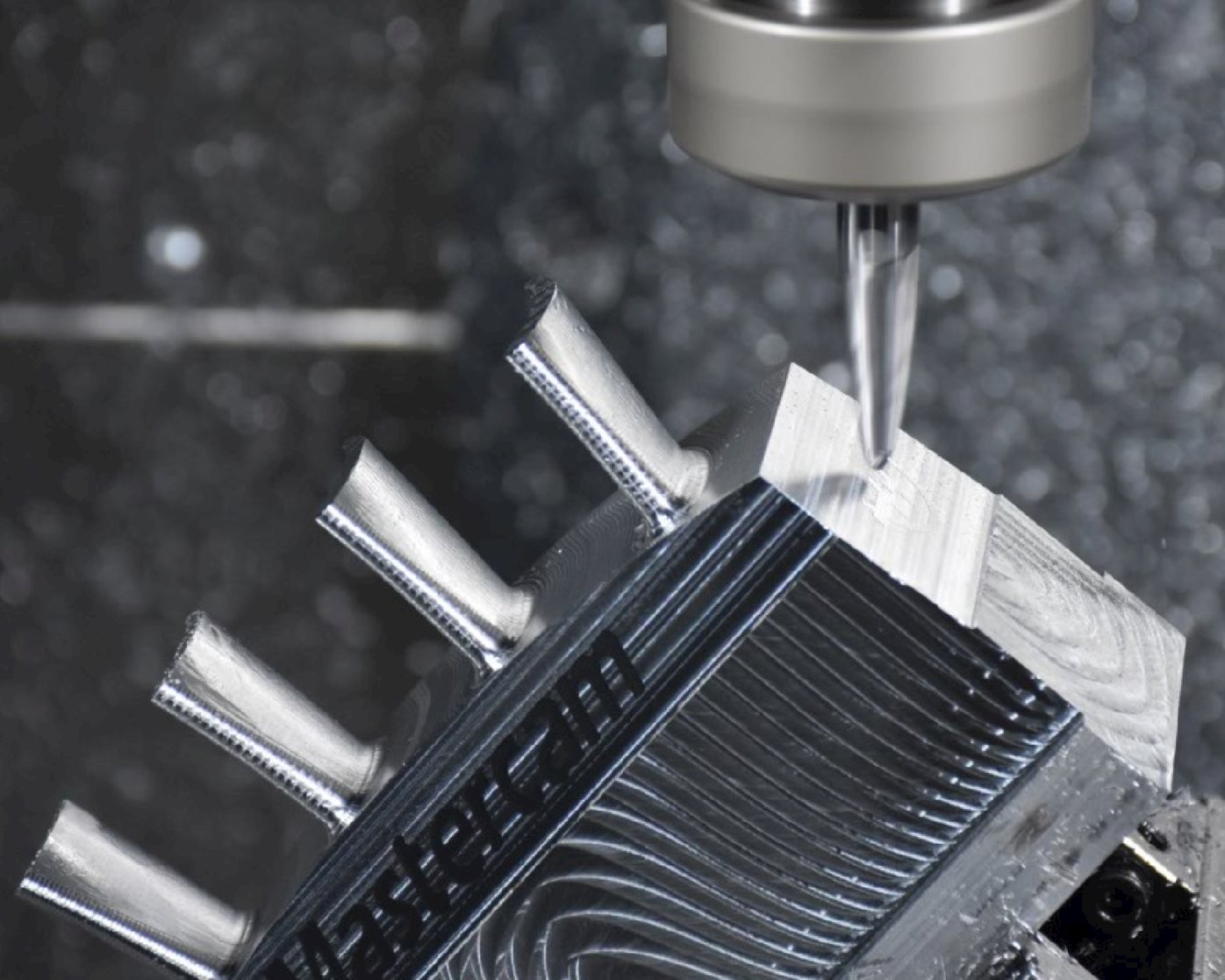