Bearing Cap
Bearing caps contain the main bearings of an engine’s crankshaft. As part of their required processing, bearing caps must undergo a tough splitting operation, requiring strong and stable operations. Tooling for bearing cap machining is highly complex and often custom in nature.
YOUR MANUFACTURING CHALLENGES
- Creating an efficient and secure process for chamfering bearings before splitting.
- Reliably roughing crank bores with minimum cycle time.
- Maintaining productivity and reliability while face milling irregular stock, cast skin and impure surfaces.
- Meeting surface finish and flatness requirements while productively finishing main faces.
- Maximising productivity by combining seal location and chamfer into one operation.
- Reducing cycle times for roughing the outer diameter.
- Producing spot faces with maximum productivity and reliability.
- Drilling numerous holes with low cycle times, high quality and reliability.
- Minimising setting and adjusting time in bearing splitting operations.
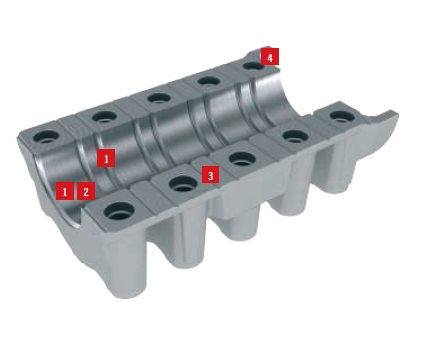
1 - Chamfering bearings before splitting
Your Challenge: | | Creating an efficient and secure process for chamfering bearings before splitting. |
Our Solution: | | To optimise productivity, this custom tool was designed to allow all chamfers on the bearing cap to be machined in a single pass. A guide bushing supports the front end of the cutter body during the contouring operation to ensure reliable performance. Your benefits include minimising cycle times with an economical solution. |
Product: | | Chamfer Milling Cutter |
2 - Reliably roughing crank bores
Your Challenge: | | Reliably roughing crank bores with minimum cycle time. |
Our Solution: | | This custom tool contains an optimum number of teeth for roughing a crank bore by plunging and secures inserts via a center-lock clamping system. The tool’s positive geometry reduces cutting forces and minimizes machine power requirements, while through coolant holes improve tool life. Your benefits include increasing productivity and reducing costs. |
Product: | | Plunge Milling Cutter |
3 - Face milling irregular stock, cast skin and impure surfaces
Your Challenge: | | Maintaining productivity and reliability while face milling irregular stock, cast skin and impure surfaces. |
Our Solution: | | With sixteen cutting edges per indexable insert, Double Octomill significantly reduces the cost of obtaining high quality results. The tool provides surface finishes with maximum security, achieves tremendous cutter body life and can be used for both roughing and finishing. Your benefits include cost reduction while maintaining top performance. |
Product: | | Double Octomill Face Milling Cutter |
3 - Productively finishing main faces
Your Challenge: | | Meeting surface finish and flatness requirements while productively finishing main faces. |
Our Solution: | | A super positive geometry with up to a 35-degree effective rake angle makes Quattromill an ideal choice for challenging face milling applications. A robust cutter body with a protective coating houses strong inserts with integrated anvils that protect the pocket seats. Your benefits include maintaining impeccable surface finishes while increasing the productivity and flexibility of your milling operations. |
Product: | | Quattromill Face Milling Cutter |
4 - Combining seal location ad chamfer into one operation
Your Challenge: | | Maximising productivity by combining seal location and chamfer into one operation. |
Our Solution: | | Combining contouring and chamfering operations, this custom step milling cutter uses a positive geometry to minimize cutting forces and reduce machine power requirements. The balanced tool includes through coolant holes to increase tool life. Your benefits include increased efficiency by combining cutting applications. |
Product: | | Milling Cutter |
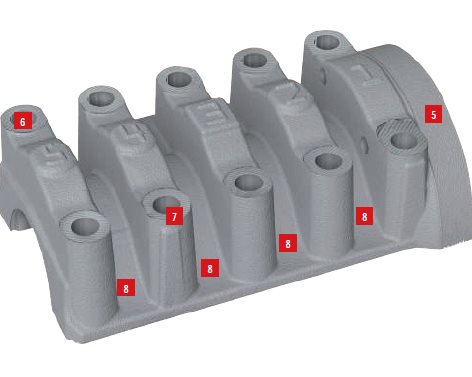
5 - Roughing the outer diameter
Your Challenge: | | Reducing cycle times for roughing the outer diameter. |
Our Solution: | | This custom tool features an integrated HSK-A attachment to reduce weight and overhang, enabling it to be used with a high feed. Positive geometry minimizes cutting forces and demands on the machine, and use of ISO/ANSI Duratomic® TK2001 inserts will maximize metal removal rates. Your benefits include boosting productivity and attaining optimal performance from your equipment. |
Product: | | OD Machining Tool |
6 - Producing spot faces
Your Challenge: | | Producing spot faces with maximum productivity and reliability. |
Our Solution: | | Using a square positive insert with a dedicated geometry for low cutting speeds, this custom tool provides an optimal method for milling spot faces of the fastening holes. The balanced custom cutter offers smooth cutting action and features a center-lock insert clamping system to ensure stability. Your benefits include a cost-effective solution that reduces wear on spindle bearings. |
Product: | | R417.19 Spot Face Milling Cutter |
7 - Drilling numerous holes
Your Challenge: | | Drilling numerous holes with low cycle times, high quality and reliability. |
Our Solution: | | Providing high performance when dealing with angled exits or intersecting holes, the Seco Feedmax Chamfer Drill utilises the light-cutting geometry and a special edge preparation to increase process security and tool life. The tool also incorporates a low-friction coating, and uses four land margins to increase stability. Your benefits include maintaining productivity in challenging, high-tolerance holes. |
Product: | | Seco FeedmaxTM Chamfer Drill |
8 - Bearing splitting operations
Your Challenge: | | Minimising setting and adjusting time in bearing splitting operations. |
Our Solution: | | Created specifically for the splitting operation, the Gang Disc Milling Cutter uses fixed pockets and positive insert geometries to reduce cutting forces and minimize machine power requirements. The high number of teeth and incorporation of MK2050 grade precision ground carbide inserts provide optimal performance in cast iron. Your benefits include a fast, economical solution for your splitting application. |
Product: | | Gang Disc Milling Cutter |
HOMERelated content
Case Studies: Bearing Cap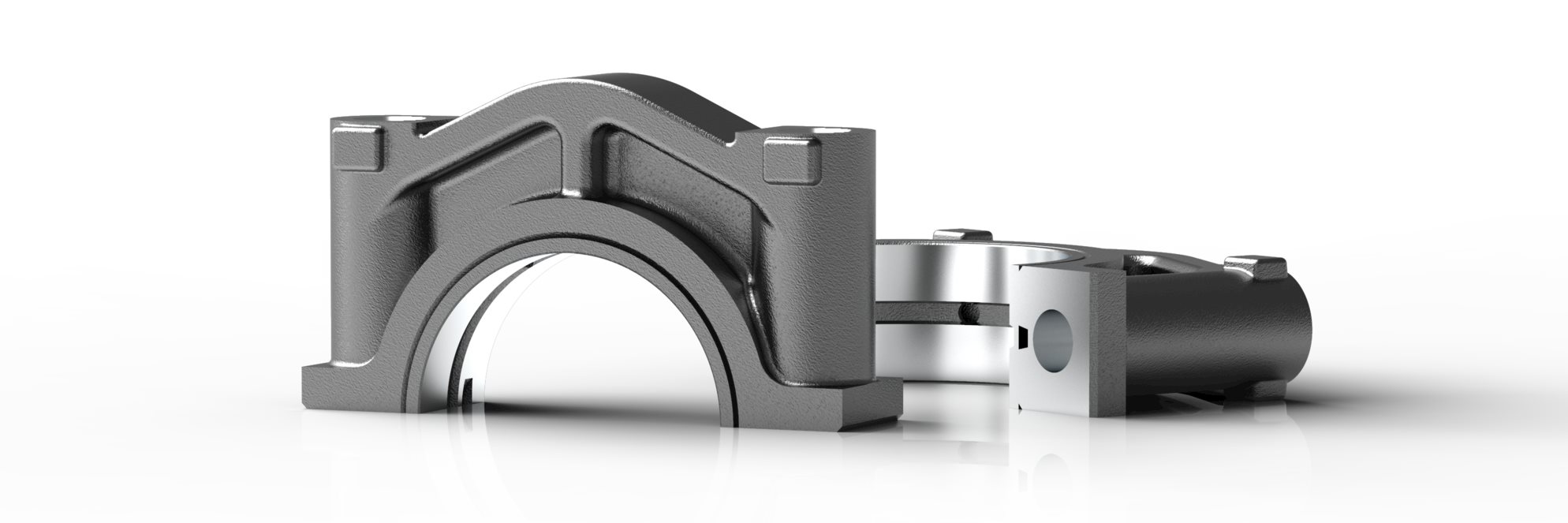
Turbocharger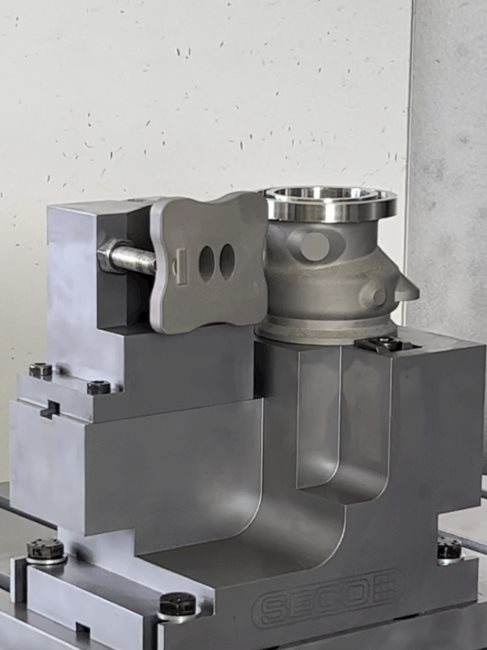
Truck Engine Block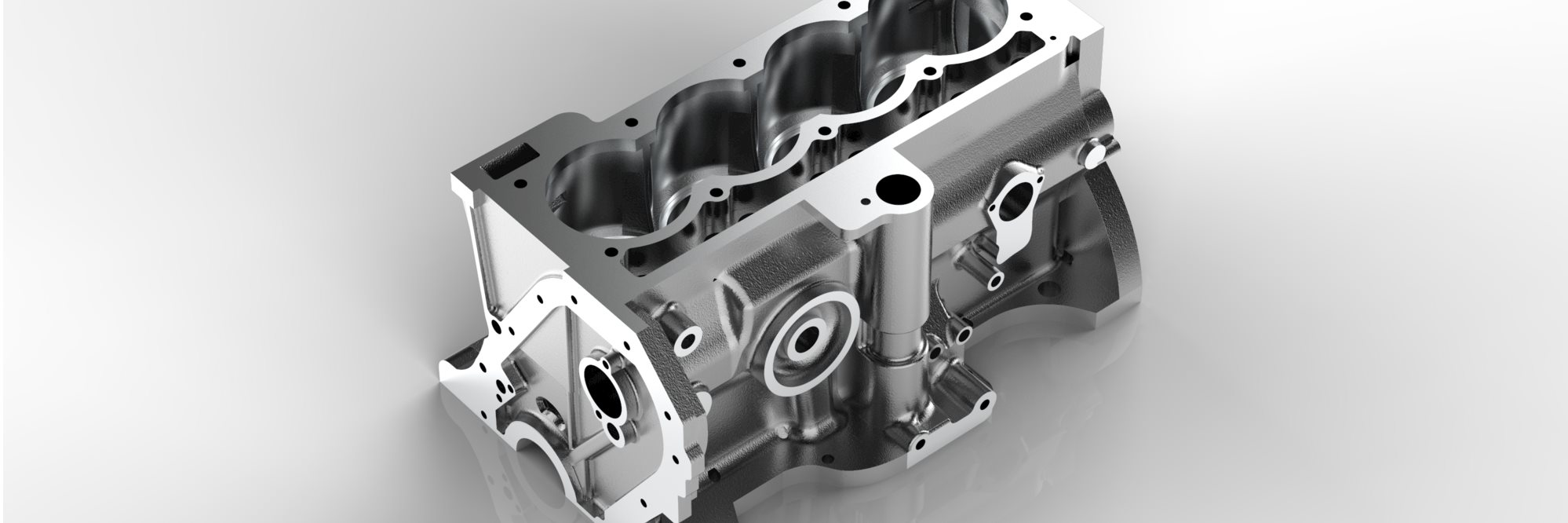
Video: 5 solutions to the main engine block challenges | Seco Tools
Crankshaft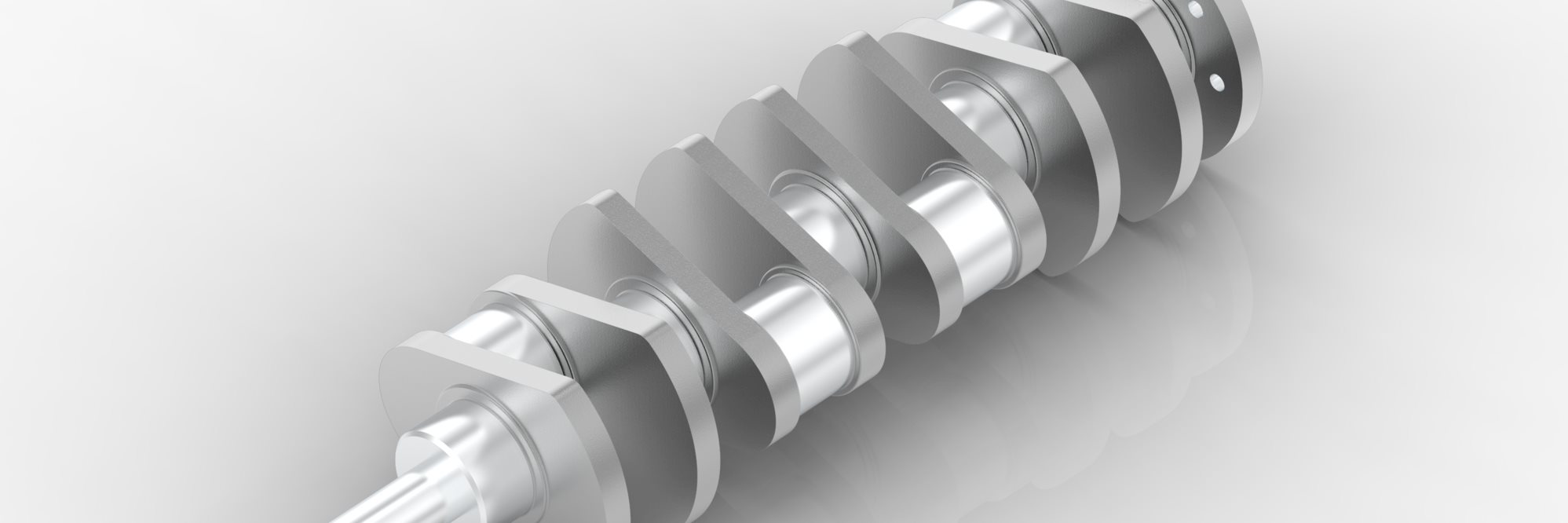
Piston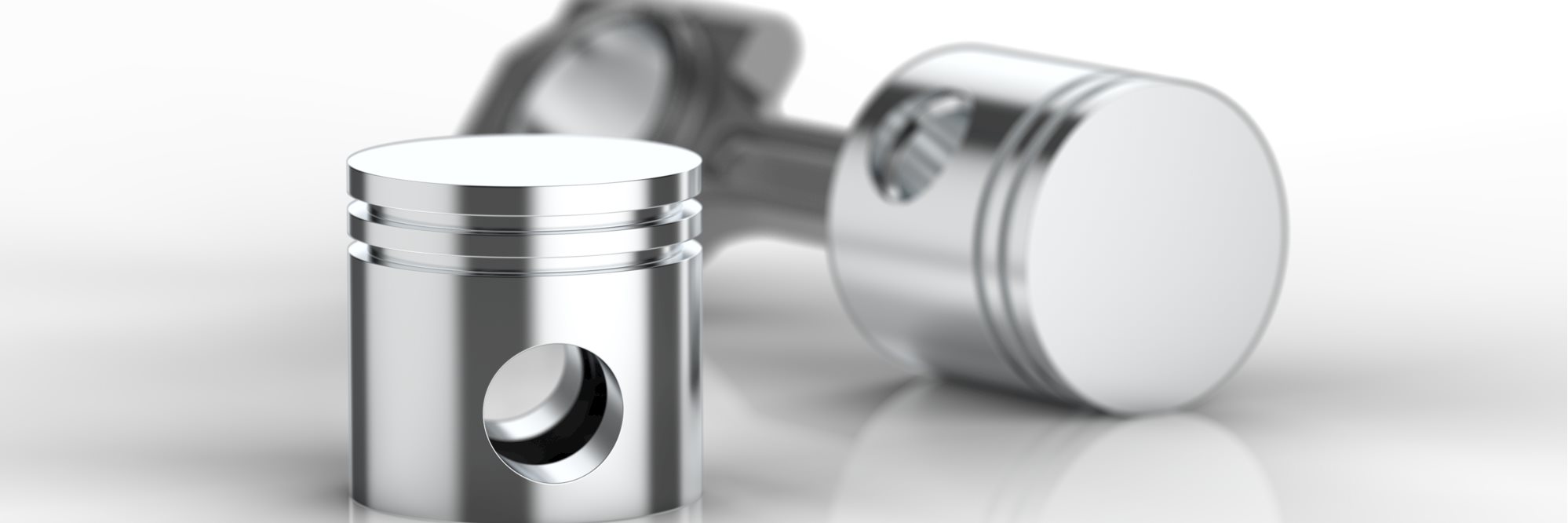
Cylinder Head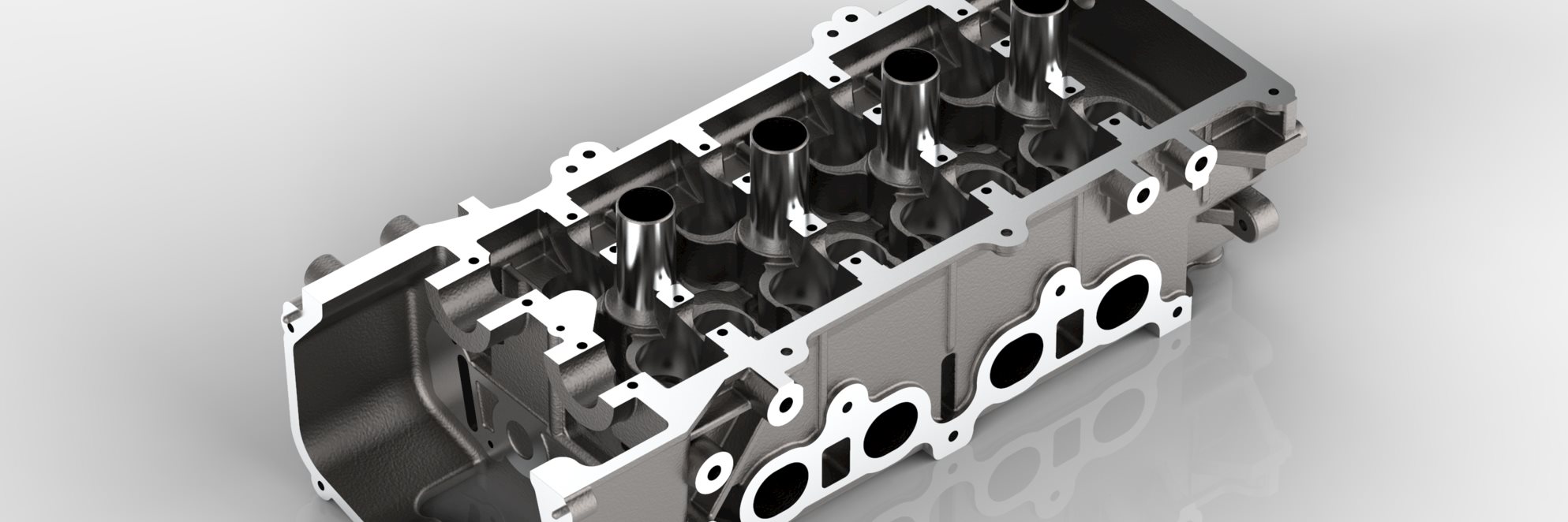
Connecting Rod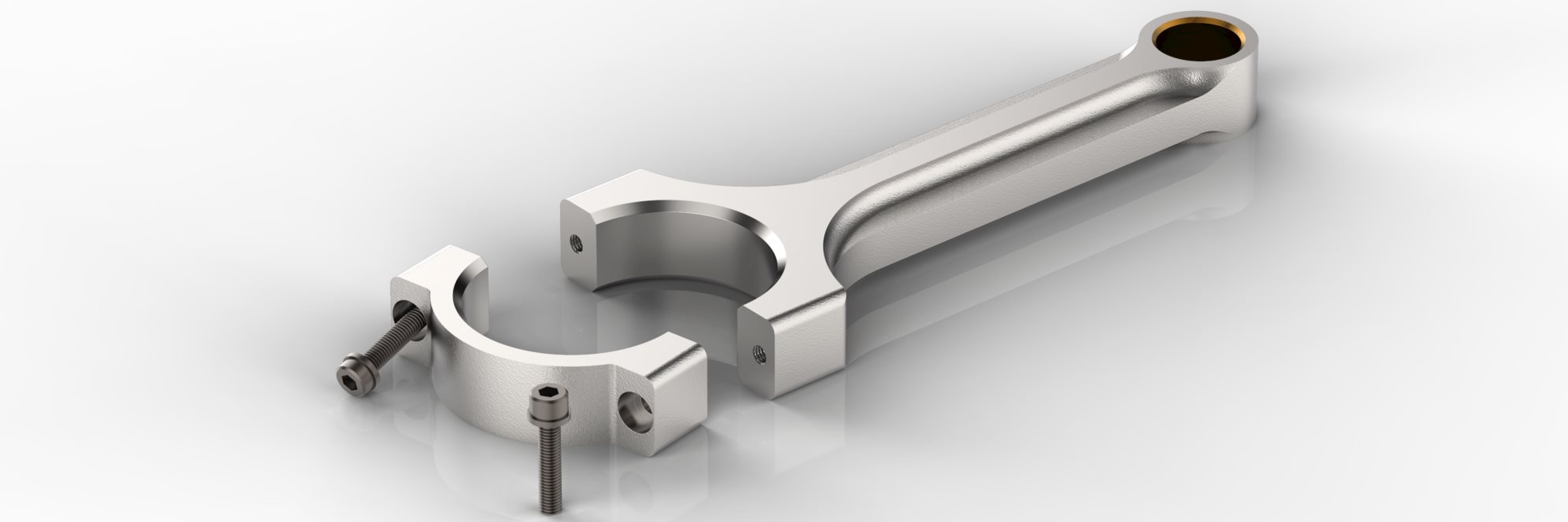