Advantages of Shorter Tooling for Multi-Tasking Machines
Discover the benefits of shorter tooling used on multi-tasking machining centers to improve efficiency, output, and the finish you desire.Because several types of Multi-Tasking Machines are equipped with dual spindles, twin turrets and B-axis milling spindles, there are a lot of machine components moving around which limit the machining work envelope. While this is advantageous in terms of part processing capabilities, it increases the risk of tool interference when an operation is using standard-length tooling.
Shorter tooling delivers an operator with more maneuverability, resulting in a machining work envelope that is better optimized for programmed tool paths and anticipated outcomes. Shorter tool designs tend to be stronger, allowing the machining process to run at a higher output. But simply making tools shorter in length is not as easy as it sounds. Learn how it requires tooling suppliers with the experience and ingenuity to do so without compromising tool or machine performance.
Multi-Tasking Machine tool technology plays a critical role in manufacturing part processing. Besides the gains in productivity, multi-tasking technology has elevated shops, especially smaller ones, to levels where they can easily machine the most complex parts cost-effectively.
Multi-Tasking Machines can mill, turn and drill part features with a high degree of accuracy and precision while also significantly reducing job setup time because they can perform most, if not all of a workpiece’s required machining in one cycle. Additionally, combining operations in one machine dramatically lessens inaccuracies that can occur when workpieces travel across multiple workstations. It also eliminates work-in-process inventory that might otherwise wait between single-process standalone machine tools.
Without the need to transfer workpieces from one machine to the next, Multi-Tasking Machines require minimal human intervention and operate mostly unattended. They allow manufacturers to accomplish more with fewer machine tools on their factory floors. While providing this increased output, the machines save valuable floor space, help reduce overall capital equipment investment costs and contribute to sustainability.
Multi-Tasking Machine configurations are packed with a variety of components and capabilities.
- Twin turning spindles
- Multiple tool turrets (upper and lower) with rotary tool stations
- Y-axis off-centerline capability
- Tilt/rotary B-axis milling spindles
- Tilt/rotary worktables
In full operation, there are several components moving simultaneously within the Multi-Tasking Machine work envelope. For example, lower turrets can work simultaneously with upper turrets on the same workpiece. Or, lower turrets can work in combination with a machine’s milling spindle that can be applied to either side of the machine’s headstock. All this simultaneous activity further heightens the risk for tool interference issues inside a machine where workspace is already limited.
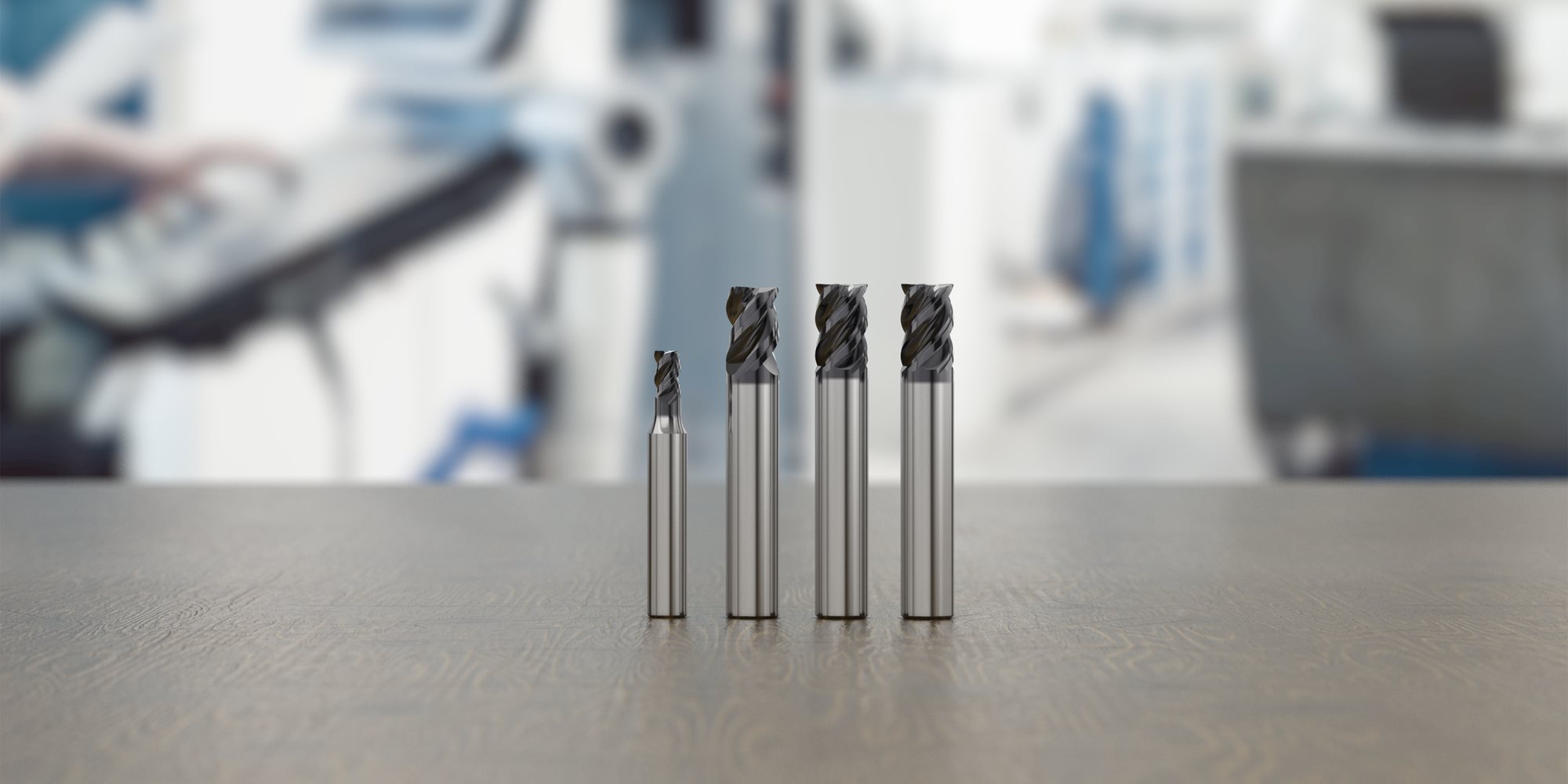
For Multi-Tasking Machines, shorter tooling is better as the machining processes entail complicated toolpaths and multiple tool changes when using standard-length or long-reach tools. In most instances, only the very ends of these tools are in the cut, so large portions of their cutting edges go unused. Plus, longer tools tend to lack stability, which can shorten tool life.
Conversely, shorter cutting tool lengths are perfect for premium real estate in the machine work envelope. They allow for more maneuverability around the workpiece, and manufacturers reduce waste by using the entire tool not just half its cutting edge length. Plus, shorter tools require less carbide to produce and are more cost-effective.
For optimum performance and stability, Seco designed its JS550 Stub Series endmill geometries with an SIRA coating and its industry-proven JS754 geometry Stub Series with the unique HXT coating. The tools are made for use in second spindles or live rotary milling turrets of Multi-Tasking Machines and developed by Seco specifically for ISO-P, M and S materials. The combination of geometry, coating and shorter protrusion length increases tool life by 20% to 40% when compared to conventional size tools.
For 45° B-axis turning on Multi-Tasking Machines, specially designed toolholders provide greater reach and less overhang while reducing the risks of collisions and ensuring greater productivity. For those machines with dual turning spindles, these toolholders allow shops to use one set of tooling/inserts for 45° B-axis turning applications on both spindles instead of right and left hand tooling. At the same time, they reduce cutting tool vibration and chatter for better parts and surface finishes.
One such holder designed for 45° B-axis turning is the Seco-Capto MTM JETI Toolholder for general ISO turning. The holder features a unique 3D-printed coolant clamp that secures with one screw for quick setup and insert indexing. With Jetstream Tooling® technology, the toolholder delivers high-speed cutting fluid directly to the cut for efficient chip management and extended tool life – even at higher speeds and feeds – to improve surface finishes and part quality. Multiple clamping sizes accommodate various materials and depths of cut, from standard machining to extreme roughing.
As automated part production becomes more common in manufacturing, single-setup machining with dual-spindle or spindle-turret multi-tasking equipment allows shops to keep pace with customer demands. However, space is limited in the work envelopes of these machines, which can constrain the use of conventional-length tools, require extra tool changes and spindle movement and increase the risk of collisions. With versatile, shorter-length tools such as the Seco JS550 and JS754 Stub Series, it’s easy to apply everything from side milling to full slotting strategies at high-performance volume rates, even in the tightest machining envelopes.
For unmanned Multi-Tasking Machine operations, shorter tools provide efficient use of tooling, ensure process stability and help eliminate the time and money wasted changing out tools damaged during a collision. All of which contributes to increased manufacturing sustainability.
Inline Content - Survey
Current code - 5fce8e61489f3034e74adc64