How to select stainless steel cutting tools
Selecting the optimal cutting data for stainless steel: cutting speed, feed rate, depth of cut, and tool type — is crucial to balance productivity, tool life, and surface quality.
When I work with stainless steel, I am always careful to prioritize achieving optimal cutting data. Cutting speed, feed rate and depth of cut are all key to ensuring efficient machining.
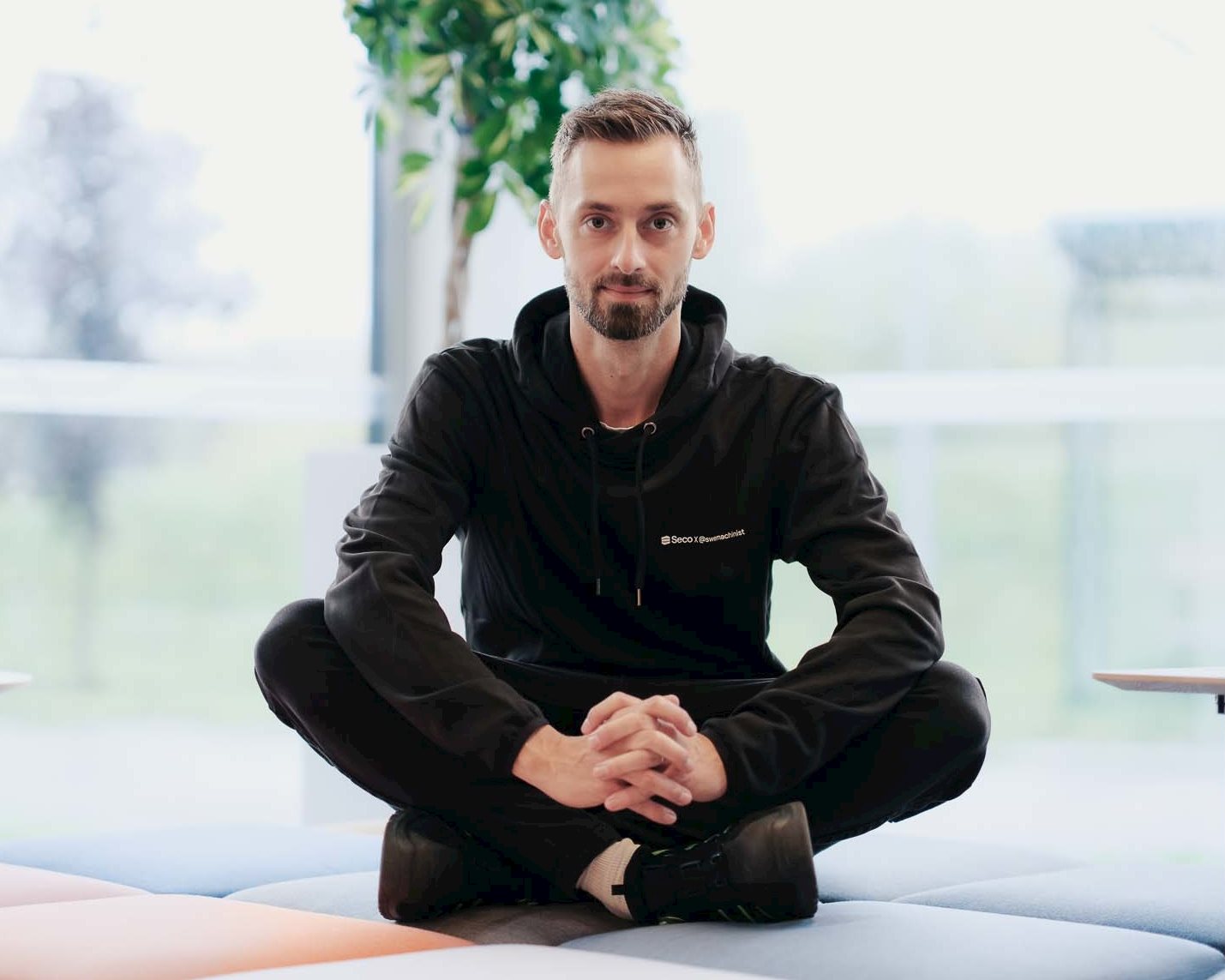
Finding the optimal cutting data involves adjusting parameters like speeds and feeds based on the set-up and material properties, to avoid issues like work hardening and tool wear.
But there is also a bit of experience involved.
I would always consider and analyze what kind of job I’m doing. This is the main thing along with the nature of the specific material, but I would say experience can be very handy here because sometimes with the speed and feed calculators it can be very hard to define the set-up.
But experience is something you get from working with the material or through talking to colleagues.
Here are some of my insights into optimizing cutting data when machining stainless steel:
It all starts with the right tool. Using carbide tools with a positive rake angle and sharp edges can reduce cutting forces. It’s best to select coatings that provide heat resistance and wear protection, particularly for austenitic grades.
If you get the proper tooling first, you can get the correct cutting data for them because with the right tools, you can do anything.
So, if you have a very expensive part with super tight tolerance, for example, I think specialized tools will come in handy.
You also learn from experience, so I generally go with tools that I prefer myself. It’s also worth noting that Seco has the Secolor color coding system where you can see the material and if it’s good for roughing. I tend to go for a roughing insert with a roughing cutter.
So, I can see it on the list and then I can go for the finishings as well from that. You can choose tooling quite a lot that way.
For stainless steel, it’s vital to keep the cutting speed moderate due to its hardness and tendency to work-harden. For finishing feed rates can be in the range of 0.02 to 0.1 mm/rev, depending on the desired surface finish.
But for roughing operations a moderate to high feed rate is recommended. A typical range for stainless steel cutting is 0.05 to 0.3 mm/rev.
The main issue here is work hardening of the part, without a doubt. You need to make sure you undercut the hardening that you just made from the previous pass, basically.
That’s why we recommend more aggressive data for roughing. In general steel you usually go lower because things will last better usually but in this case in stainless steel it can be the opposite to that. You often have to adjust upwards.
Maybe lower the feed but increase the speed to avoid this hardening happening because this will also shorten the tool life quite a lot. That’s why the speed and feed calculator is very good to have. You can have it as a good reference point as well.
If you’re playing a record and your needle is worn out, the music will sound distorted. You’ll take the record off the turntable right away! In a way, it’s not so dissimilar to machining on stainless steel:
You always need a good, stable set-up because if not you can get machine chatter. Then you need to adjust the speeds and feeds even more, using the speed and feed calculator. Maybe you will lower the speed but increase the feed even more.
I think a lot comes down to how it sounds when it cuts. I guess a lot of this comes down to experience as well, but I need to be able to hear that it cuts smoothly. You can adjust it enough so you can hear that it doesn’t instantly want to start destroying the plate or chatter.
If it’s not cutting smoothly, in turning for example, you get this ‘mumble’ in the part, these very deep grooves. Chatter is a huge issue and if you get chatter the tool will also chatter so everything needs to really work together here.
AND DON’T FORGET TO…
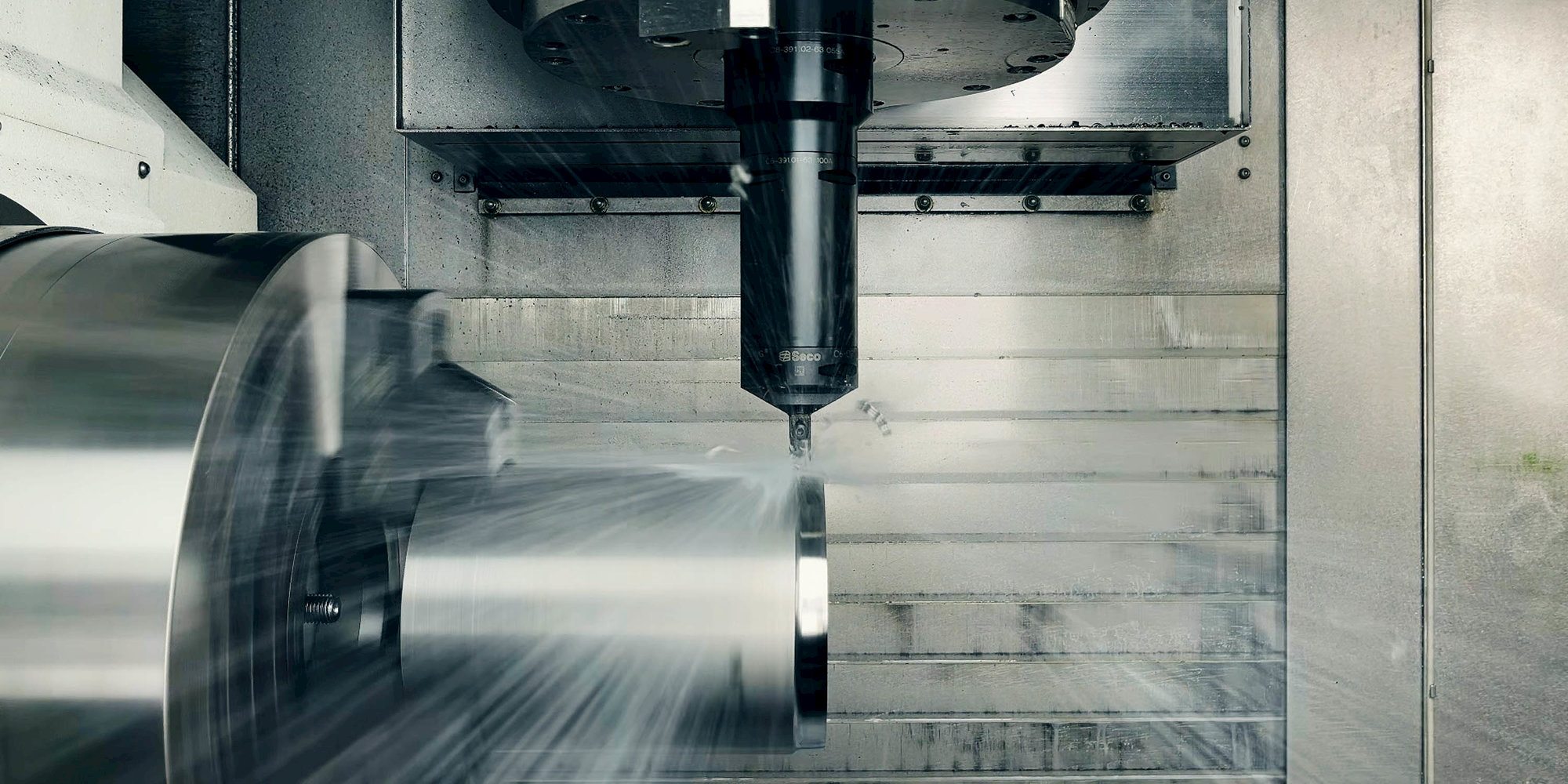
A cool head is necessary for working with a challenging material such as stainless steel, and the need for adjustments comes with the territory. But coolant is also vital, so as to manage heat and prevent thermal damage to the tool and workpiece.
You need to be constantly asking yourself: is the coolant enough? Because you want to keep the part cool as well.
If the parts start to get too warm it will start to build up these tensions and this will make the part warp, especially when it comes to the bigger parts like a long shaft. You should flood it with coolant to help keep the temperatures under control.
If you keep these considerations in mind and accept that it might not go perfectly right away and adjust, it all helps.
If you want to dive deeper into the topic, download the whitepaper.
Inline Content - Gridded Links
Tags: 'wp_guide_stainless_steel'
Max links: 1
Inline Content - Survey
Current code - 5fce8e61489f3034e74adc64