Versatility and flexibility in application and materials
Discover an indexable face milling cutting tool designed for exceptional versatility and a broad working range. The new generation Octomill transcends traditional face milling, offering unparalleled flexibility across diverse applications and materials. Its innovative multi-insert pocket design accommodates three distinct insert types
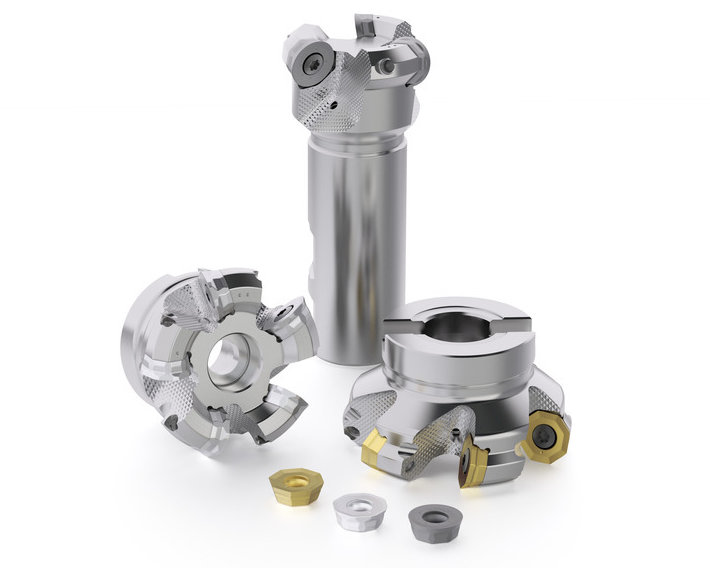
Beside the core face milling insert range the cutter can be equipped with round 16 mm (about 0.63 in) as well as moderate high feed insert option. One indexable cutter system that can perform face and copy milling tasks as well as ramping, helical interpolation and profiling. This results in higher flexibility and a broader working range.
Just more than a face mill!
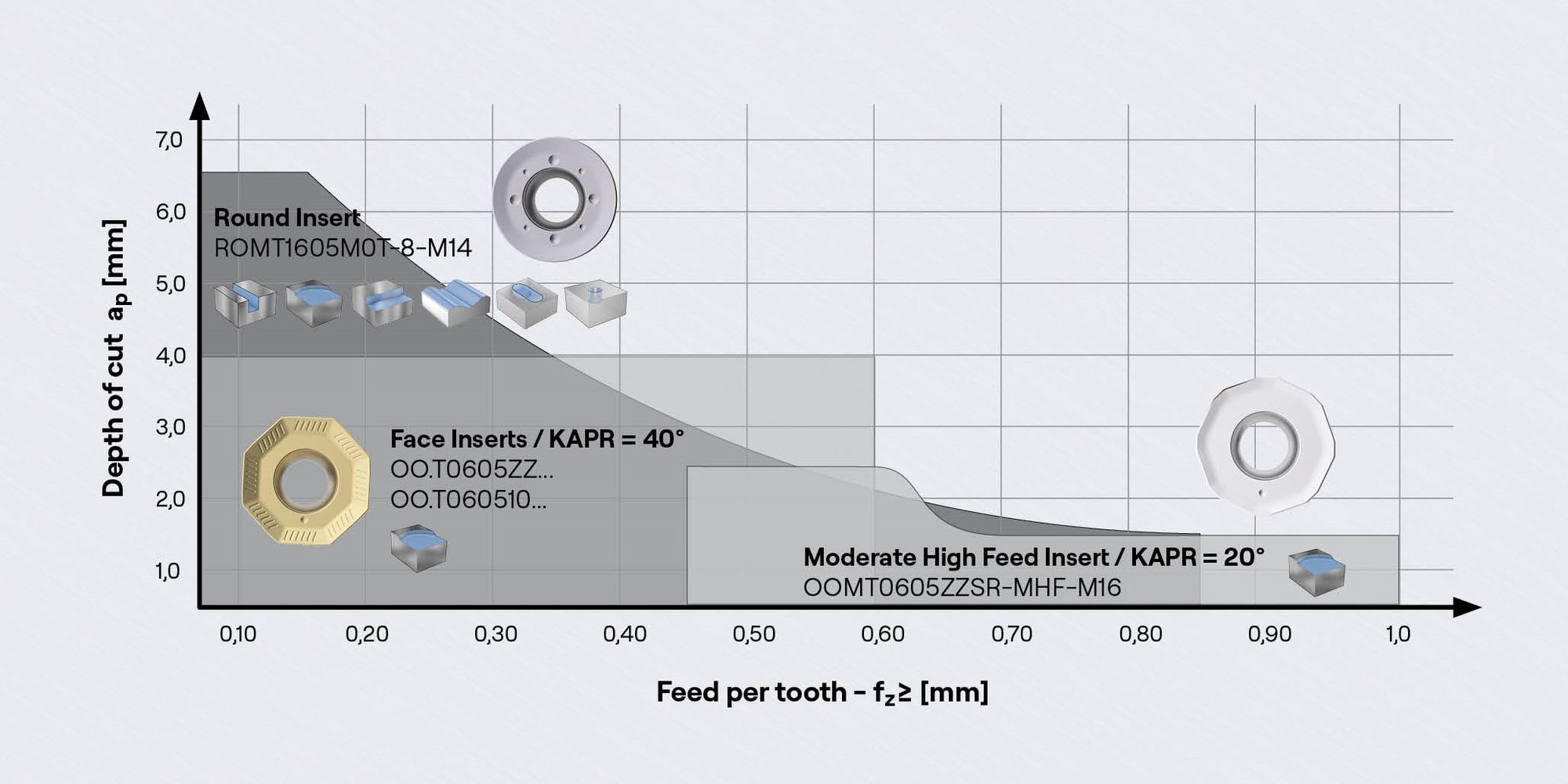
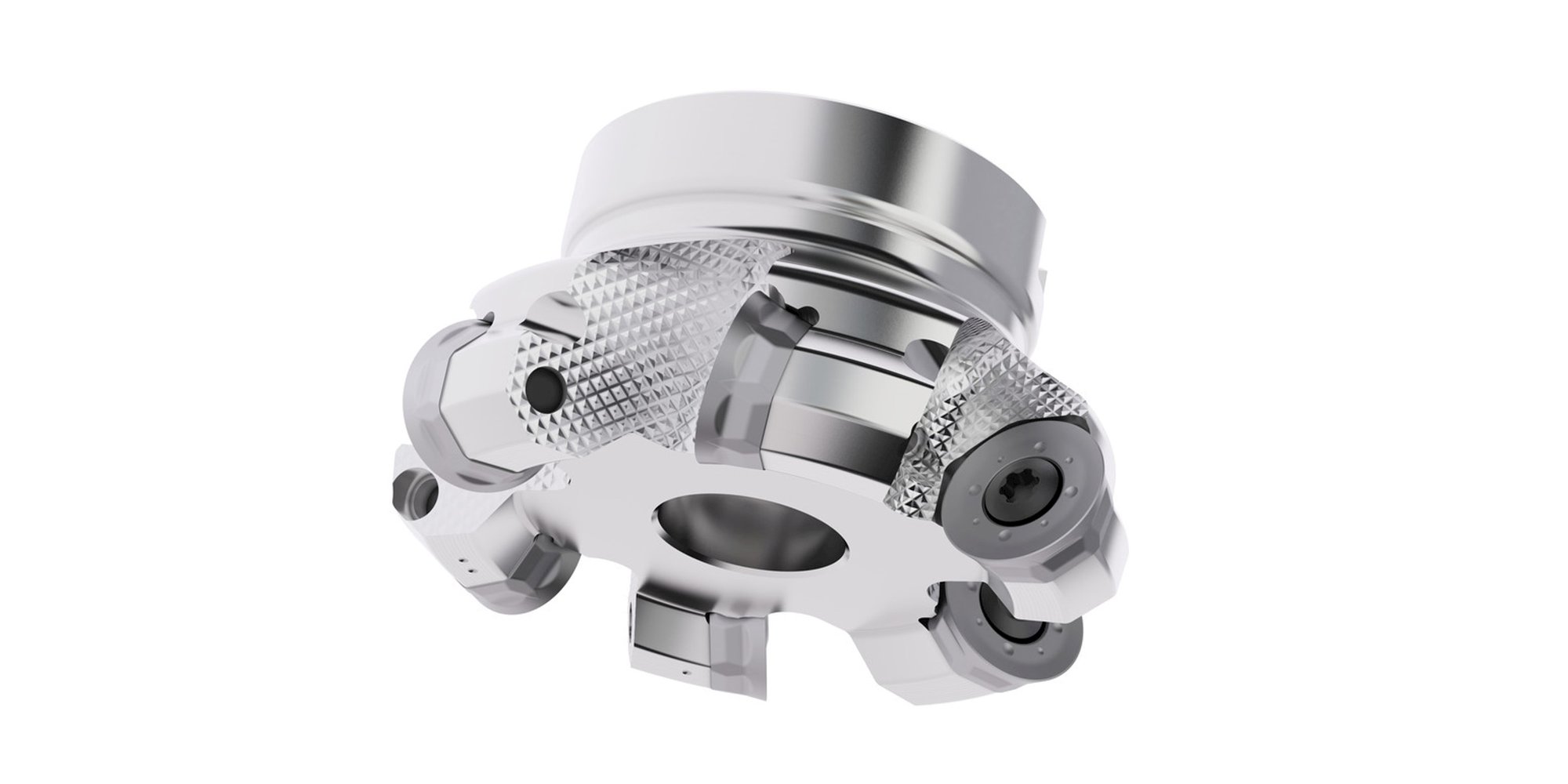
Seco’s Octomill size16 mm round insert (ROMT1605M0T-8-M14) provides a lighter cutting behavior due to the more positive axial cutter setting angle compared to the existing R217/220.29I / RP.T1605 range. This leads to a smoother cutter entry and exit and is especially beneficial for weak set ups to utilize the potential tool performance. Still the existing R217/220.29I range has a stronger cutting edge particularly at depth of cut above 4.0 mm (about 0.16 in) in comparison to this alternative choice.
The design features a rigid anti-rotation interface that prevents the movement during machining due to strong 90° face contact between insert and pocket seat. The insert can be indexed by 4 or 8 edges depending on the required dept of cut. This insert option enables the this indexable face milling system to perform besides facing also proper ramping, helical interpolation and profiling.
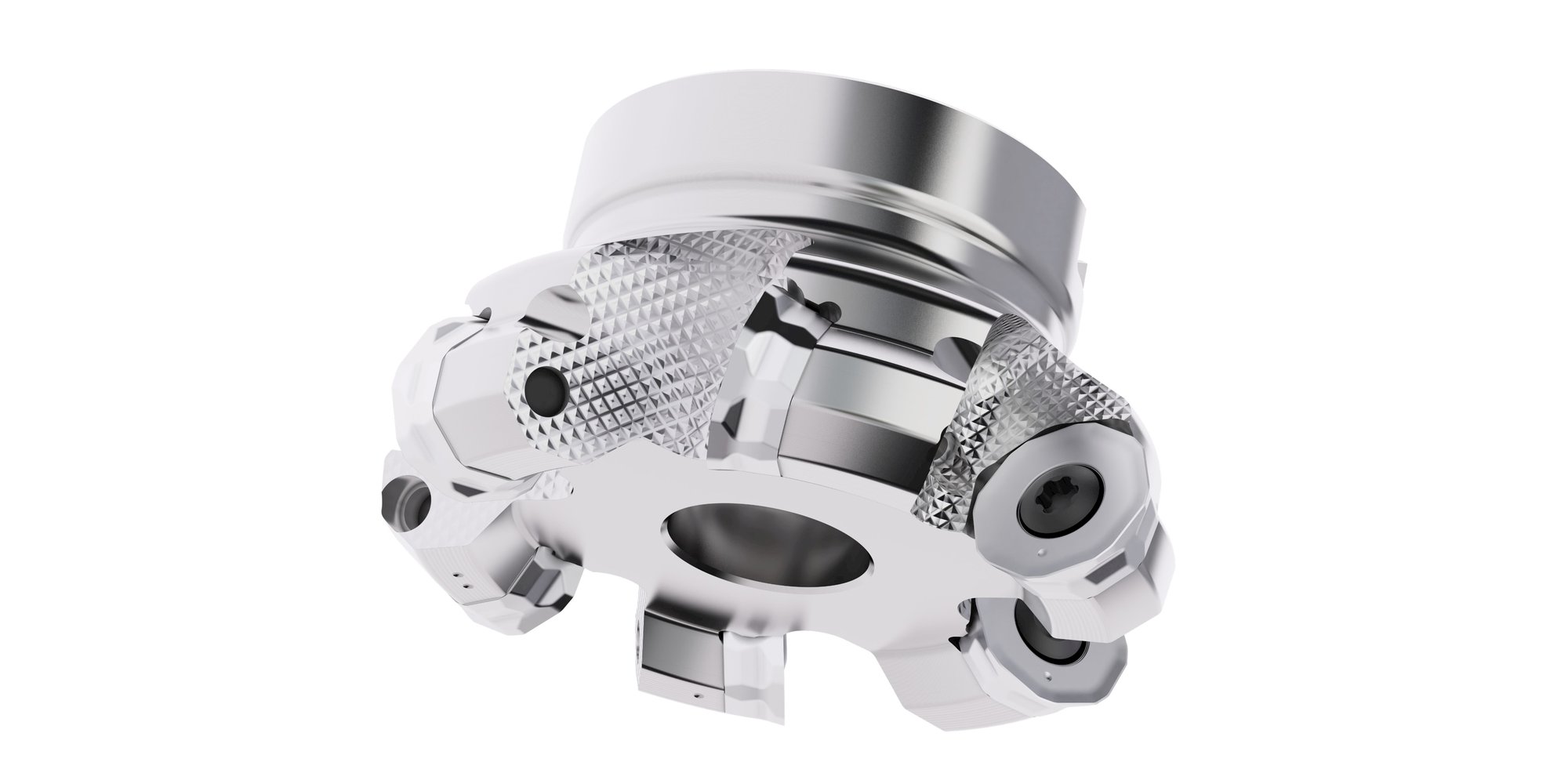
The moderate high feed insert option (OOMT0605ZZSR-MHF-M16) insert can be seen as a faster face milling option, also called moderate high feed milling. This is ideal for application with limited depth of cut demand ap < 1,5 mm (about 0.59 in) since the lower lead angle of 20° instead of 40° allows higher feed per tooth.
The insert has an integrated wiper flat that creates an acceptable surface finish appearance even at higher feed rates which is a great benefit versus round or common high feed cutters.
A common trouble with dedicated high feed solutions is the uneven stock allowance on the first cut. The edge line design of this MHF insert handle stock variation (a common issue for dedicated high feed systems) above ap = 1,5 – 2,6 mm (about 1.02 in) with an increased lead angle of 45°. This brings extra process security and confidence when facing open surfaces.