The cutting edge of precision: Innovations in laser machining
This article highlights Optek's advancements in laser micro machining, including fiber and ultrafast lasers, and their impact on various sectors. It also covers the THERMACH project for machining metal matrix composites.In the heart of the UK’s technological landscape, just a stone’s throw from The River Thames in Oxfordshire, a small company named Optek has been quietly revolutionizing the world of laser micro machining. Founded in 2000 by three visionary engineers from the UK Atomic Energy Authority, Optek has grown into a global leader in precision engineering, with facilities spanning the UK, China, and the USA. Their journey took a significant turn in 2019 when they were acquired by Humanetics, a move that has only accelerated their innovation and reach.
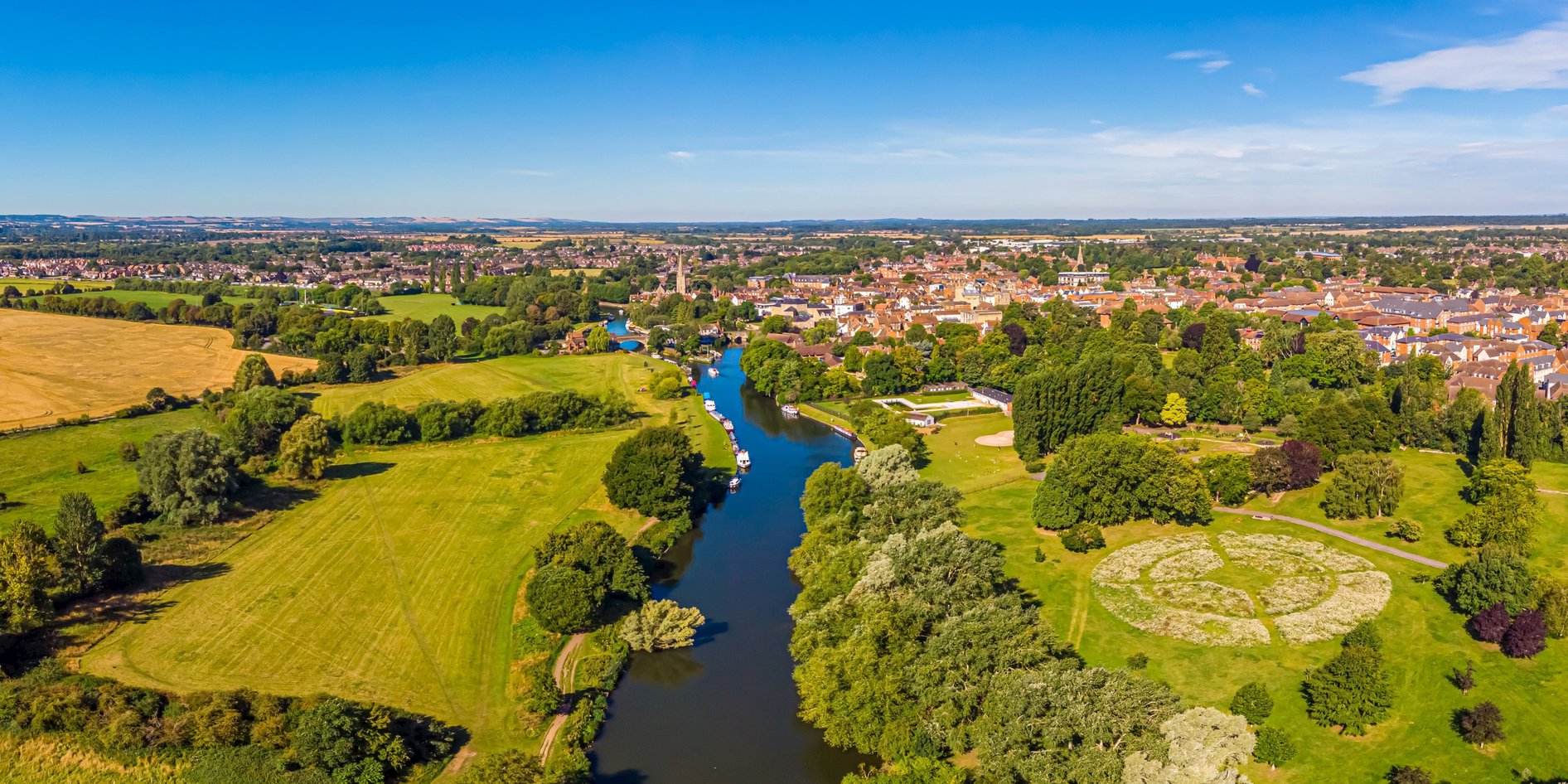
Optek’s story is one of relentless pursuit of excellence. “We started with a simple goal: to push the boundaries of what laser micro machining could achieve,” says Chris Randon, Business Development Manager at Optek. Over the years, the company has garnered accolades, including two Queen’s Awards for export, a testament to their impact on the global stage.
One of the cornerstones of Optek’s success has been their pioneering work with fiber lasers. Unlike traditional lasers that rely on crystals, fiber lasers use Optical fibers as the gain medium. This innovation has led to lasers that are not only more reliable but also require less maintenance. “Fiber lasers have transformed our approach to precision machining,” Randon explains. “Their ability to operate in dusty and liquid-rich environments, like those found in CNC machines, has been a game-changer.”
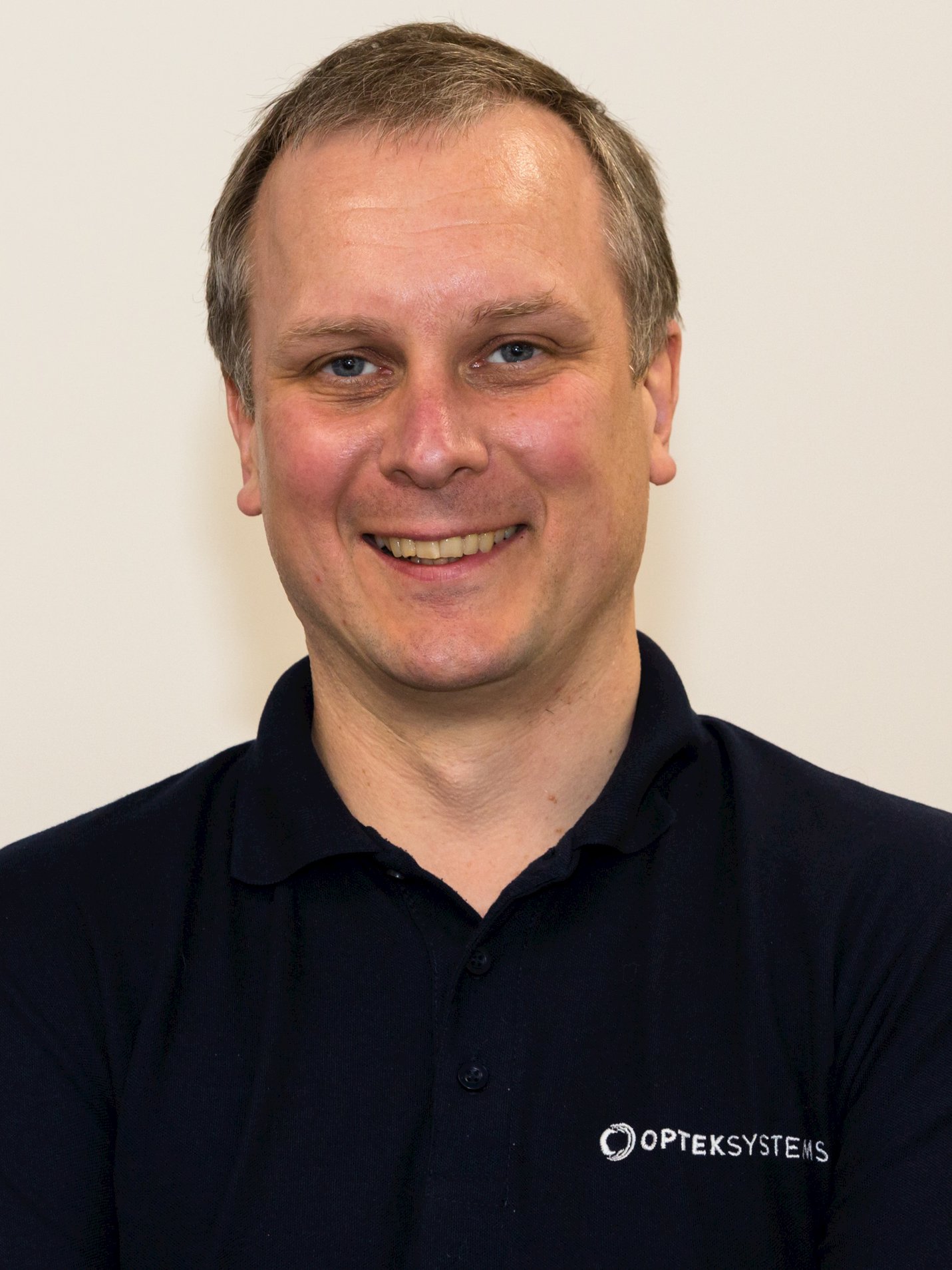
The evolution from nanosecond to ultrafast lasers, including picosecond laser and femtosecond lasers, marks another leap forward. These lasers emit incredibly short pulses, allowing for precise material processing with minimal thermal impact. “Ultrafast lasers enable us to achieve cleaner cuts and reduce material damage,” says Randon. This technology is particularly valuable in applications involving heat-sensitive materials, ensuring high-quality results without compromising the integrity of the workpiece.
In the fast-paced world of industrial manufacturing, speed and efficiency are paramount. Optek has embraced high-power pulsed lasers to meet these demands. By increasing the average power of these lasers, they can process materials at twice the speed without a proportional increase in cost. “High-power pulsed lasers have significantly boosted our productivity,” Randon notes. This advancement is crucial for industries like automotive and electronics, where high throughput is essential.
For applications requiring intricate designs, such as medical devices, Optek has turned to five-axis galvanometers. These advanced systems offer unparalleled beam manipulation capabilities, enabling the creation of complex features like inverse taper holes. “The five-axis galvanometer allows us to push the boundaries of what’s possible in medical device manufacturing,” Randon explains. This precision is vital for products like thrombectomy catheters, which demand exacting standards.
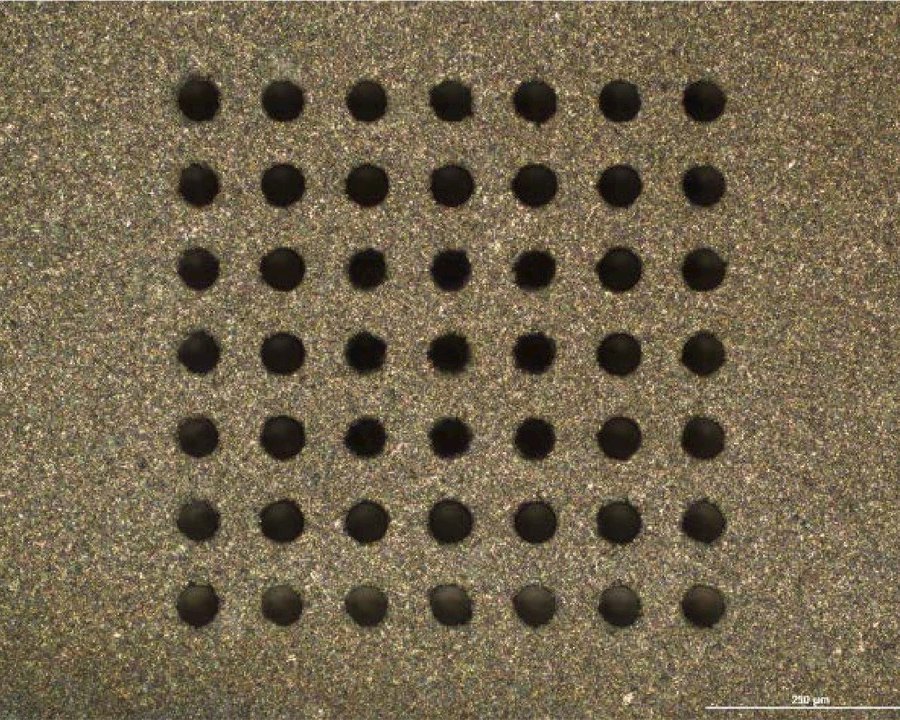
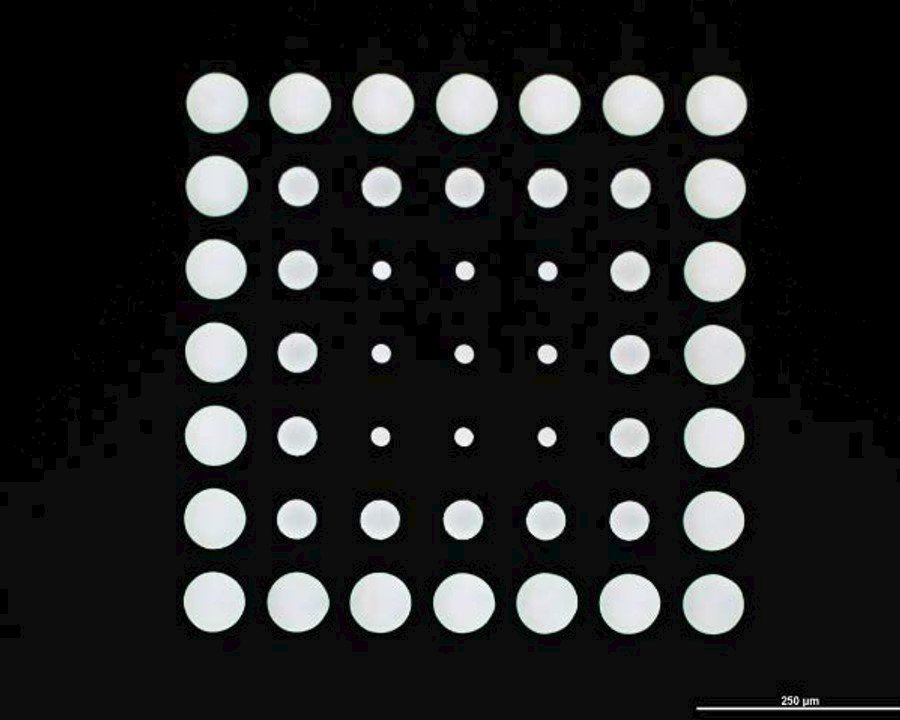
Originally developed for astrophysics, adaptive Optics technology has found a new home in laser micro machining. By correcting wavefront distortions, adaptive Optics enables precise focusing of laser beams, even in transparent materials. “This technology allows us to achieve remarkable accuracy in materials like glass and polymers,” says Randon. The ability to create detailed features in such materials opens up new possibilities in many industries.
Combining galvanometers with CNC stages and advanced software, Optek’s infinite field of view systems can process large areas with high precision. This innovation is particularly useful for applications like creating molds for face masks. “Infinite field of view technology has streamlined our processes, reducing the need for multiple setups,” Randon notes. This efficiency translates to faster production times and lower costs.
The integration of artificial intelligence into vision systems is transforming laser micro machining. AI algorithms can analyze material properties, detect defects, and optimize processing parameters in real-time. “AI has revolutionized our quality control processes,” Randon says. “It reduces human error and ensures consistent product quality.” This automation is crucial for maintaining high standards in industries like aerospace and medical device manufacturing.
Optek’s innovations are not just theoretical—they have practical applications that are making a difference in the real world. For instance, black marking, which involves creating microstructures on metal surfaces to trap light, resulting in durable, high-contrast marks. This process is essential for biomedical devices that require autoclave-resistant markings. “Black marking ensures that our medical instruments remain identifiable even after repeated sterilization cycles,” Randon explains.
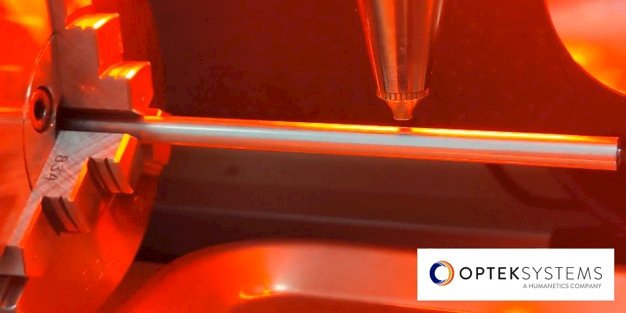
Another application is the creation of hydrophobic and hydrophilic surfaces using laser-induced periodic surface structures (LIPSS). Hydrophobic surfaces repel water, while hydrophilic surfaces attract it, both of which have various industrial uses. “LIPSS technology allows us to tailor surface properties to specific needs,” says Randon.
In the aerospace industry, laser micro machining is used for drilling, cutting, and surface structuring. Applications include creating filters for fuel cells, micro grooves for air bearings, and processing metal matrix composites (MMC’s). “The precision and reliability of our laser systems enhance the performance and safety of aerospace components,” Randon notes.
One of the most notable collaborations in Optek’s portfolio is their work on the THERMACH (Thermal Machining) Project involving Seco, the University of Nottingham, advanced materials company TISICS, and Attenborough Medical. This UK-based research program has focused on the processing of MMC’s, which are notoriously difficult to machine due to their hardness and abrasive nature.
“Traditionally, machining MMC’s would result in significant tool wear and damage,” Randon explains. “However, by integrating laser machining with Seco’s cutting tools, we’ve been able to overcome these challenges.”
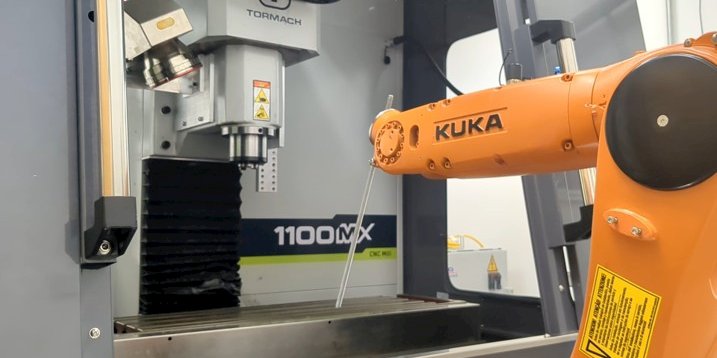
The success of this collaboration has opened up new possibilities for machining hard and brittle materials. “Our work with Seco demonstrates the potential of combining laser technology with traditional machining methods,” Randon notes. “It’s a perfect example of how innovation can solve complex manufacturing challenges.”
The future of laser micro machining is bright, with exciting developments on the horizon. The integration with IoT and Industry 4.0 technologies promises to optimize production processes through real-time data analysis and machine learning. “Smart factories equipped with interconnected laser systems will revolutionize manufacturing,” Randon predicts.
Advancements in laser technology, such as artificial intelligence and new types of ultrafast lasers, will expand the capabilities of laser micro machining. The technology is also expected to penetrate new industries like biotechnology, renewable energy, and nanotechnology. “We’re excited about the potential of laser micro machining to drive innovation across various fields,” Randon says.
Optek’s journey from a small startup to a global leader in laser micro machining is a testament to the power of innovation and dedication. With cutting-edge technologies and a commitment to excellence, they are poised to continue shaping the future of precision engineering. As Chris Randon aptly puts it, “We’re just getting started.”
Inline Content - Survey
Current code - 5fce8e61489f3034e74adc64