Balancing key factors in stainless steel machining
Stainless steel is strong and resists heat and corrosion. To machine it, balance tool properties and geometries with aggressive cutting parameters.Stainless steel is a versatile workpiece material that combines strength with heat and corrosion resistance. Those exceptional structural properties make it more difficult to machine. Shops need a careful balance of cutting tool properties and geometries plus aggressive cutting parameters for productive stainless-steel machining. With the right setup and settings, stainless steel becomes less challenging and more rewarding to turn.

Stainless steels come in five family groups: ferritic, martensitic, austenitic, duplex and precipitation hardening. Each group's unique properties and applications present different machining challenges.
Learn more about the material group
Basic stainless-steel alloys are ferritic or martensitic. Ferritic alloys include 10%-12% chromium and can't be hardened. Martensitic alloys add more chromium and carbon, along with manganese and silicon, and harden via thermal treatment. Today, ferritic and martensitic stainless alloys show up in household items such as kitchen or garden tools. They're no longer the first choice for industrial environments. Stainless steel alloys evolved for greater mechanical strength and corrosion resistance.
For strength, metallurgists added nickel to create iron/chromium/nickel alloys, or austenitic stainless steels. These alloys are common in petrochemical processing, to meet hygiene requirements in the food industry and to produce general machinery for harsh environments.
With greater performance capabilities come greater manufacturing challenges. Ferritic and martensitic stainless-steel alloys are not much more difficult to machine than plain steels because their corrosion resistance is a chemical property. However, the same elements that increase hardness, toughness, deformation resistance and thermal properties of austenitic stainless steels also decrease their machinability.
Until recently, machinists assumed that the strength of austenitic alloys required higher mechanical cutting forces, stronger negative-geometry tools and reduced cutting parameters. That approach hasn't been successful. It produces short tool life, long chips, frequent burrs, unsatisfactory surface roughness and unwanted vibrations.
Austenitic stainless steel doesn't require much higher mechanical cutting forces than traditional steels do. The primary challenge of austenitic stainless steels lies in their thermal properties, which require more energy for machining.
But metal cutting fundamentally is a deformation process, and austenitic stainless steels work harden during deformation. Austenitic stainless steels combine low thermal conductivity with high deformation resistance, so machining them generates excessive heat. It's essential to evacuate that heat from the cutting zone. Unlike plain-steel chips, austenitic stainless-steel chips can't absorb and carry away much heat. Instead, it remains in the cutting zone, which shortens tool life.
Toolmakers engineer carbide substrates so they can withstand the heat generated while machining stainless steel. Cutting edge sharpness is as important as substrate composition. A sharper tool cuts rather than deforms stainless steel, which reduces heat generation.
Although stainless steel's poor thermal conductivity limits chips' heat absorption, greater volumes of larger chips pull away more heat. To evacuate heat from the cutting zone effectively, use the largest-possible depths of cut and feed rates to maximize the heat carried away in chips. Larger depths of cut also reduce the number of cutting passes required to complete a part. Austenitic stainless steel tends to work harden when machined, so fewer cutting passes minimize these damaging risks.
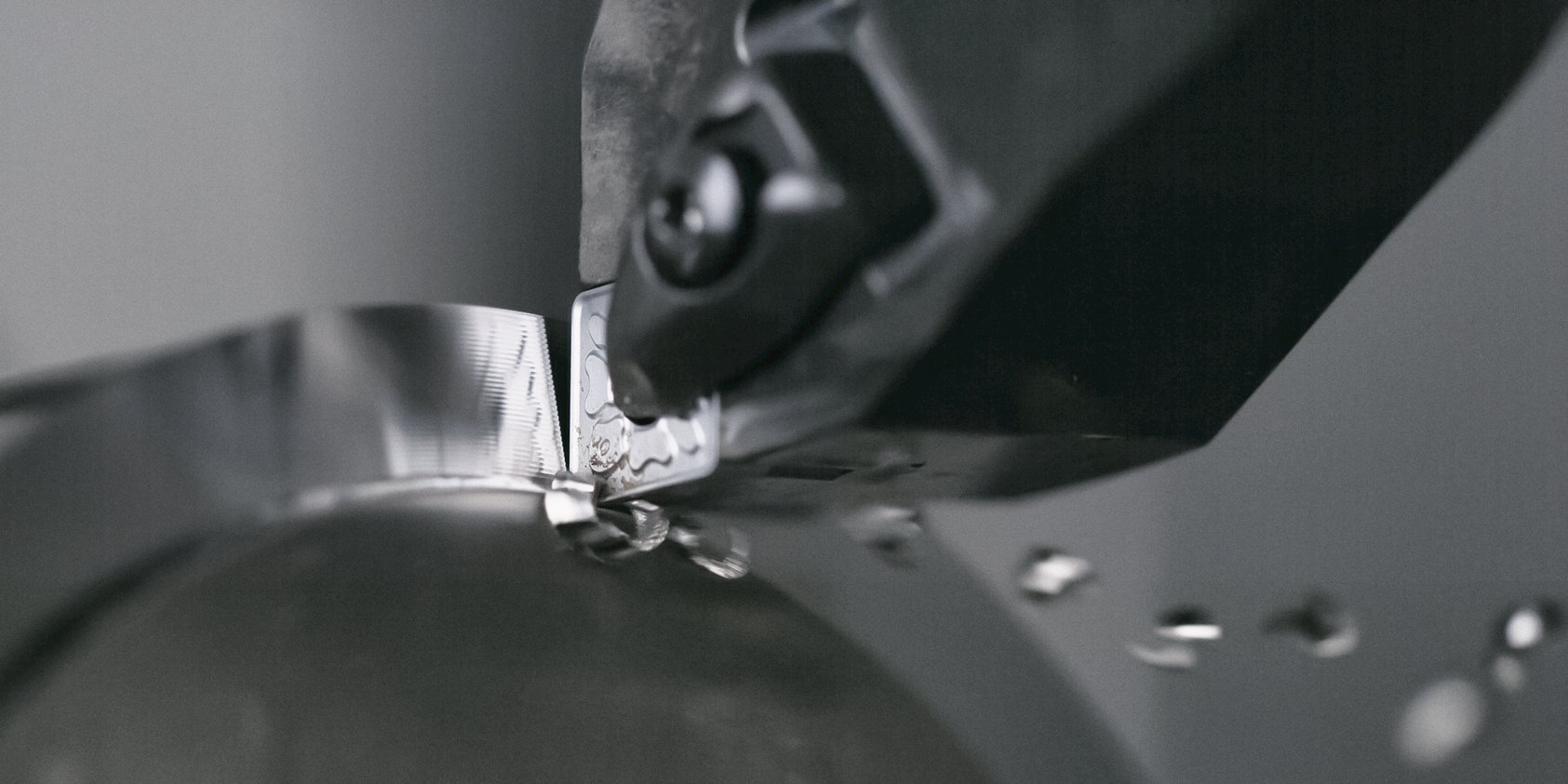
These aggressive machining tactics have practical limitations. For example, surface finish requirements restrict maximum feed rates. Machine tool power, as well as cutting-tool and workpiece rigidity, also limits machining parameters.
Coolant almost always is crucial to successful machining of austenitic stainless-steel alloys. Use high-quality oil/water emulsion with at least eight or nine percent oil content. By contrast, typical machining operations use only three or four percent oil content. Higher pressure delivery to the cutting zone also improves coolant performance. Specialized high-pressure delivery systems such as Seco Jetstream Tooling® are even more effective.
A hard tool-surface coating reinforces hot hardness and improves tool life in high-temperature environments. Thick coatings that insulate the substrate from heat do not adhere well to very sharp geometries. Instead, cutting tool makers engineer thin coatings that provide a good heat barrier. Some austenitic stainless-steel alloys contain abrasive hard inclusions. A hard coating that increases cutting tool’s abrasion resistance can increase tool life.
Austenitic stainless steels are highly ductile and tend to stick to the cutting tool. Adhesion wear occurs when cut material sticks to and builds up on the tool. These adhesions may pull away sections of the cutting edge, which leads to poor surface finish and tool failure. Coatings can provide lubricity that inhibits adhesion wear. Higher cutting speeds also help minimize adhesion wear.
Notch wear is a highly localized, extreme form of friction wear that results from work hardening during machining. Varied depths of cut spread the wear areas across the cutting edge. Along with appropriate coatings, this strategy helps mitigate notch wear in austenitic stainless steels.
Toolmakers balance tool properties for optimal performance in specific workpiece materials. Carbide grade research looks to balance hardness and toughness. This yields a tool that is hard enough to resist deformation but not so hard that it fractures. Similarly, sharp cutting-edge geometry is not as strong as a rounded edge. Toolmakers aim to create tools that balance sharpness and strength.
Toolmakers revisit their tool application guidelines during tool development. Most machining parameter recommendations are based on the toughness and hardness of traditional steels. These recommendations do not consider the thermal factors involved in machining austenitic stainless steels and other high-performance alloys. In collaboration with academic researchers, toolmakers have begun to revise tool testing procedures in light of these materials’ thermal characteristics.
New testing guidelines reflect the creation of new reference materials. Traditional machinability standards used one steel alloy and the mechanical loads produced while machining it. Now, toolmakers have established a separate reference material for austenitic stainless steels with appropriate baseline values for speeds, feeds and depth of cut. To achieve optimal productivity in materials with various machining characteristics, toolmakers apply balancing or calibrating factors relative to that reference material.
Many cutting tools offer highly acceptable performance in various materials under numerous cutting conditions and machining parameters. These tools can provide moderate, cost-effective productivity and workpiece quality for one-time jobs.
For top productivity and process reliability in specific workpiece materials, however, toolmakers continually manipulate and balance a wide variety of tool elements. The basic elements of a tool include its substrate, coating and geometry. Each is important. In the best tools, they operate as a system to produce results that exceed the sum of their parts.
Some parts of a tool, including tool geometry, play an active role. Geometry can change heat generation and removal, chip formation and achievable surface finish. Conversely, substrates and coatings play passive roles. They are engineered to balance hardness and toughness, withstand high temperatures, and resist chemical, adhesion and abrasive wear.
Traditional M3 and M5 turning geometry inserts from Seco offer basic examples of performance-altering differences in geometry. Both feature negative (0˚ clearance angle) cutting edge geometries and T-lands between the cutting edge and the tool rake face. The versatile medium-rough M3 geometry provides good tool life and chip breaking in a wide range of workpiece materials. M5 geometries take on demanding, high-feed roughing applications. They combine high edge strength with comparatively low cutting forces.
Despite their versatility, the M3 and M5 geometries are strong but not fully sharp. In austenitic stainless steel, they generate considerable heat via deformation. Instead, the Seco MF4 and MF5 geometries feature sharp, positive geometries. Their narrower positive T-lands help maintain sharpness while they provide support behind a sharp edge. These open, free-cutting geometries facilitate medium to finishing operations in steels and stainless steels. The MF5 geometry is especially effective in high-feed applications.
To achieve the right results, machinists need tool designs that suit the materials they use. In complex, demanding materials such as austenitic stainless steels, that means using the correct tools and machining approaches to offset the behavior of the metals themselves. New tool designs embody the optimal response to versatile but challenging workpiece materials.