A lathe like no other
A unique, custom-made lathe, the Petra lll particle accelerator and successful cooperation with Sweden's Linköping University all played a roll in making Seco the first company in the world to be able to undertake real-time, atomic level studies of how material is affected during metal cutting.HAVING THE ABILITY TO STUDY CHANGES IN THE CUTTING ZONE OF INSERTS DURING METAL CUTTING HAS BEEN AN ELUSIVE GOAL FOR BOTH INDUSTRY AND ACADEMIA FOR MORE THAN A DECADE.
Perhaps the biggest challenge has been constructing a cutting rig that is suitable for use in the Petra III particle accelerator, the device used for testing at the DESY research center in Hamburg, Germany. The required lathe needed to be small and light enough to carry out normal turning operations in the accelerator, while also being sufficiently stable, rigid and heat-resistant.
The high-energy X-rays generated in the Petra III are thinner than a stand of hair, but emit energy that affects the objects they penetrate. These objects must remain stable so that the precisely aimed beam can generate accurate readings. Only one person has succeeded in building a machine that meets the demands required for use in this kind of experiment and that person is Janne Eriksson from Seco in Fagersta.
From Sweden’s down-to-earth Dalarna region, Eriksson has a solid background as a technician, as well as a strong general interest in technology – all good characteristics for being able to solve such a unique construction challenge. But despite Eriksson’s suitability to the task, lots of others had tried to accomplish the same thing, and he admits that he had a few sleepless nights as the deadline for the project “came hurtling forward”. The crucial idea for how to construct the structural framework – the heart of the lathe – came from a seemingly unlikely source.
“I read up on the subject, thought about it, read even more about sustainable construction, and began to wonder if I was stuck. Then one day, I sat down in the workshop and let my thoughts wander. My gaze fell on the fire hydrant and I suddenly realized that it was resting on an H-beam that was supporting the whole roof. And in that instant I got the idea from which the framework was developed.”
Eriksson succeeded in making the idea a reality by working closely with his colleagues at the Seco Tools Technical Center in Fagersta. Once test runs were completed, further challenges cropped up when the lathe was installed on-site in one of the particle accelerator’s beam-lines. Among other things, modifications were required to adapt the lathe to this new setting. At this stage Eriksson still had concerns about the project.
Eriksson says, “I thought, ‘Okay, the machine’s now in the accelerator and is spinning a 30-kilogram lump of metal and is completely vibration free. But how long will it keep on going so well? A few minutes?’. But all my reservations quickly evaporated and now it has run for days at a time. Over the last year, we have been on-site in Petra III to both assemble and take apart the lathe for each test. The lathe has worked just as well each time.”
The development of the lathe was part of Project X-Cut, a consortium between the German research institute HZG Geesthacht, Seco Tools, and Linköping University. Seco’s manager for the cooperative effort is Mats Johansson Jõesaar, an R&D Expert within Seco’s Materials and Technology Development division.
JOHANSSON JÕESAAR is proud and pleased – both as a researcher and as a Seco employee – of the success achieved by the unique lathe and the opportunities it presents for growing knowledge around how materials react during the cutting process. While there is already existing knowledge around the cutting process, the new opportunities now available to study materials at the atomic level will be of major significance for the development of coatings and materials.
“As we get to understand more about how the material is affected, we’re gaining completely new possibilities to tailor its properties such as extending tool life and reducing wear on products,” says Johansson Jõesaar. “Thanks to this increased understanding, Seco will be able to make more efficient products with higher levels of reproducibility. This atomic-level knowledge about materials during metal cutting is laying the groundwork for the next generation of materials and products. Seco is the first metal-working company in the world that’s doing it, and we now have a unique head start.”
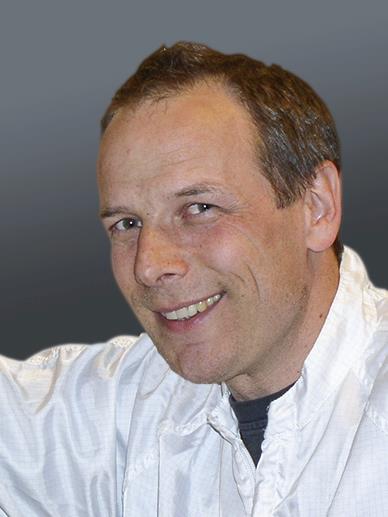
SECO TOOLS AND LINKÖPING UNIVERSITY have worked together since 2010. PhD students have worked real-time with X-ray-technology studies of Seco’s coatings.
Why does your institution work together with industry?
“Simply put, we are streamlining material process in order to better understand materials. It’s important that our research is close to reality, and so it’s only natural to pick up issues and problems from industry. As we produce the answers required, new knowledge often arises, which generates new questions and new ideas for new materials. It’s a really fun way to work.”
What challenges are you taking on with Seco Tools?
“We have worked together for a long time, among other things on real-time studies of the effects of pressure, temperature and other variables that affect the characteristics of the layers when they are used. We look at a few layers at a time to better understand each layer’s characteristics and to be able to interpret the results that we see. The intensity of Petra III’s X-rays offers unique opportunities in this area in terms of the number of measuring points and the amount of data. Just one second in Petra III gives more information than several days of measurements in our own X-ray equipment.”
How would you describe the lathe that Seco has developed?
“It’s a unique research tool with all the precision demanded for advanced real-time studies.”
What further work will you undertake with the results from Petra III?
“The results will provide us with new knowledge of how layers are affected during use. This means we can now go a few steps further by, for example, looking at how the workpiece, the chip, and the insert are influenced by each other in real time during turning. This opens up exciting new research fields for us.”