Gearing up with robots
If you want to avoid mistakes, let robots do the work. That's the philosophy of German gear-manufacturer Stelter Zahnfabrik.THE ADMINISTRATIVE BUILDING for gear manufacturer Stelter in the north German town of Bassum may look old- fashioned, but it’s home to a business that’s at the cutting edge of its field.
The company’s Production Director, Christian Stelter, explains, “We have an exceptional level of automation, with several robots linked together in a single process.”
This highly automated arrangement allows for a dull, grey blank to be put on a conveyor belt and emerge shining at the other end, following a whole series of turning, milling, and grinding procedures. The company likes to say that its products are “made by magic hands”, a reference to the work of its industrial robots.
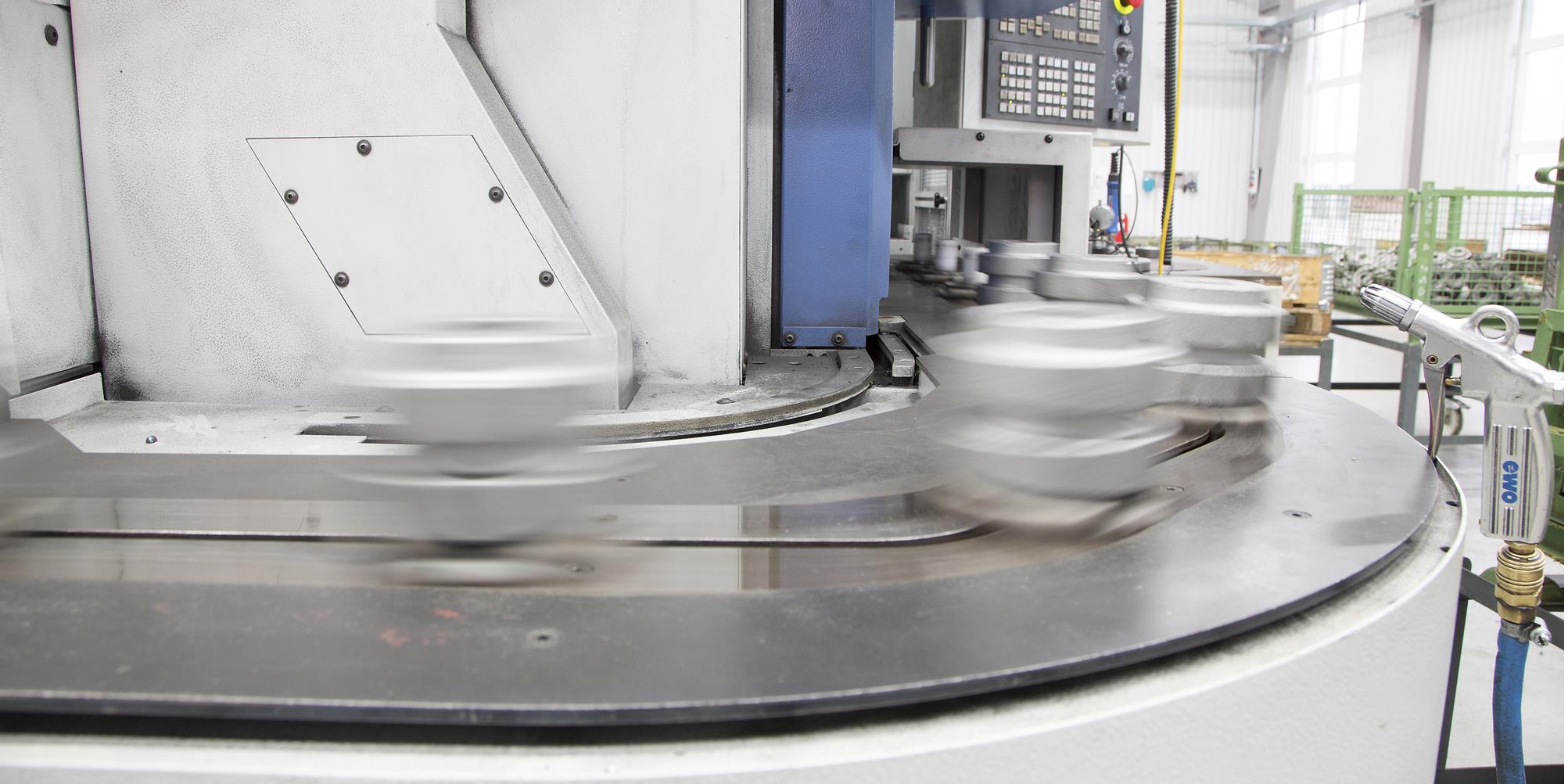
Stelter Zahnradfabrik specializes in making and finishing all kinds of gears. Automotive makes up to 60 percent of production, with major German car manufacturers among the company's customers.
STELTER ZAHNRADFABRIK’S newest production hall, built in 2014, features a number of machines that make the various gears required for a new duplex clutch gearbox for a major German automaker.
At each workplace, a computer screen reminds operators to carry out various checks at predetermined intervals. Is the inner diameter still within tolerances? How deep is this or that groove? Every few minutes, the screen flashes up a new parameter for checking. “We decide what needs to be checked, and we can see in the office if the checks have been done and what values they show,” explains Stelter. This combination of operator and machine is one that Stelter and company Technical Director Karl-Heinz Wilkens believe will characterize the industry for some time to come.
“A human being is always in charge,” says Wilkens. “A person controls the control processes and programs the programs. But people should be mostly involved with quality issues. Filling the oil tank can only be a sideline.”
Stelter says it’s a matter of getting rid of the human element as a source of errors. By using robotic equipment managed by workers, who in turn are helped by computer systems, he has put his staff in charge of quality. “We started using this system ten years ago, and we have improved quality enormously,” he says.
Quality is the key. According to Stelter, his company is one of the top three in the field, and he puts this down to quality, flexibility and, of course, price. And that means absolute reliability in the 24-hour-a-day production process.
As Wilkens puts it, “We have an automatic line, so we need insert operating life times that are reliable. If we have to break the process, we lose production. And that’s where Seco Tools has helped.”