Tougher than most
Seco helps Comsteel keep the wagons rolling in one of the most inhospitable places on earth.Rather than being held back by its nearly 100-year history, Australian railway wheel manufacturer Comsteel, embraces it. Combining its heritage with modern technology allows the company to create world-leading products.
No location on the planet is tougher on railway rolling stock than the Pilbara region of Western Australia. Mining trains in this remote part of the world regularly pull loads of iron ore weighing more than 33,000 tons, with each axle forced to bear 45 ton loads. Temperatures can approach 50 degrees Celcius and the nearest major city is more than 933 miles away.
The job of producing rail wheels tough enough to cope with such demanding conditions is one that fits well with Comsteel, a manufacturer located on the other side of the continent in Waratah, a suburb of the city of Newcastle, New South Wales.
With roots stretching back nearly 100 years, Comsteel relies on both strong traditions and cutting-edge tech-nology to produce railway wheels with world-leading standards of toughness and durability.
Operations Superintendent for Railway Products at the Comsteel plant, Kevin Roberts, says with enormous mining customers depending on the company’s wheels to keep their operations productive, there’s a huge emphasis on quality, high degrees of hardness and toughness, and safety. “The trains used in the Pilbara are so big that if an incident does occur, there’s going to be major damage and a loss of production,” he says. “Our customers use our wheels because they know they won’t have those kinds of issues.”
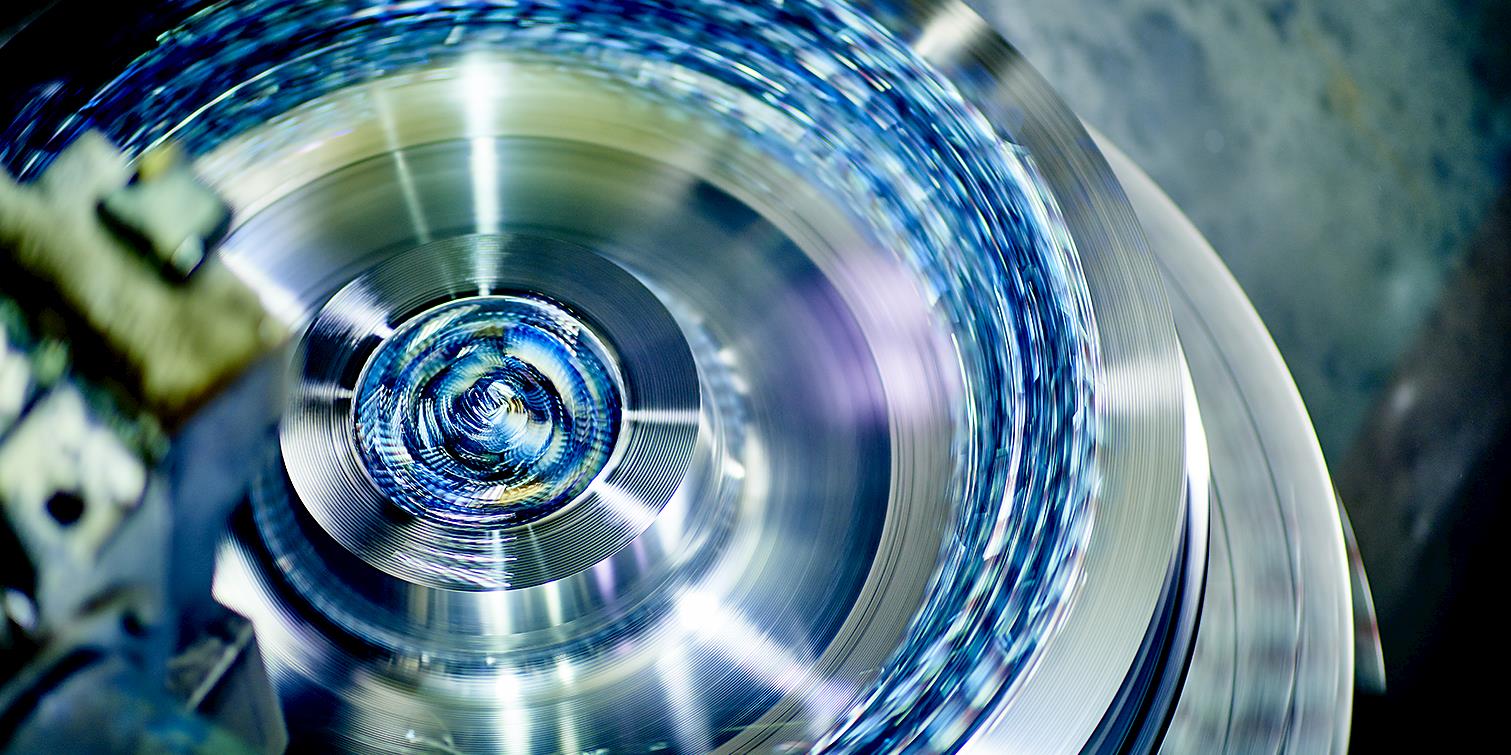
FOUNDED IN 1918 as The Commonwealth Steel Company, Comsteel is now part of the glob-al steel products company, Moly-Cop. In addition to over 150 different types of wheel, Comsteel manufactures railway axles and wheel sets, as well as grinding media used by the mining industry to crush ore.
Comsteel Business Development Manager Andrew Hemsworth explains that while wheels for use in hauling freight make up the bulk of the company’s sales, Comsteel also supplies wheels to every Australian rail authority for use in locomotives and passenger trains.
THE COMPANY’S EXPORT MARKETS, meanwhile, include South Africa, New Zealand, the United States, and, notably, China. “We supply wheels for wagons that are built in China and they are then sent to Australia,” he says. “The wagon manufacturers know our product works for high-end applications with high axle-loads and they can’t put just any wheel into that environment.”
The biggest selling point for Comsteel wheels is their high hardness and toughness. Hemsworth explains the company’s heavy haul freight wheels are made of micro-alloy steel produced using an on-site electric arc furnace.
Micro-alloy steel ingots are sawn into cheeses before being forged and rolled. They are then heat treated, tested, and machined before being subjected to non-destructive, visual, and dimensional testing.
Comsteel Wheels have been certified both by the Association of American Railways, Europe’s EN standards and international Quality Management standard ISO 9001.
Kevin Roberts says tight procedures, quality systems and a respect for the experi-ence of employees are key to the company’s success. Also vital is the culture of continu-ous improvement and the adoption of new technology, which ensures a quality product that meets customer needs.
ROBERTS SAYS WORKING with high-quality suppli-ers is also crucial. Comsteel has deepened its cooperation with Seco in recent years, with Seco now the Tier 1 tooling supplier for the company. “Seco’s tooling works very well on our wheels,” he says. “The performance of the carbide insert we use is very high and leads the way when machining our high hardness micro alloy wheels.”
Seco inserts are used to machine the web of the wheel and the extremely hard wheel treads. Roberts says after trialing dozens of inserts over many years, he is yet to find an insert that performs better on the micro alloy wheels than Seco’s product. “Tooling is a high consumable cost and the Seco prod-uct performance works well with keeping our costs down,” he says.
Another plus is Seco’s service. With Com-steel continually developing the strength of both its steels and wheel products, Seco is on hand to offer tooling advice and help machine prototypes.
Area Business Manager for Seco Austral-ia, Harold Phipps, says he and his colleagues strive to make themselves available when-ever Comsteel needs help, and have worked long hours on weekends to solve problems. “We have helped bring down Comsteel’s tooling costs and improved their bottom line,” he says “It’s a true partnership with benefits for both Comsteel and Seco.”