Overcome Jet Turbine Disc Milling Challenges
Specialized tooling designed around overcoming the unique challenges and strict tolerance needs when manufacturing jet turbine discs and associated components.
Machining a turbine disk – we showcase advanced skiving and fir tree features using Wire Arc Additive Manufacturing.
To watch the demo, fill in this form now and instantly get 5 additional machining demos
Inline Content - Sugar Form
Sugar Form url - https://info.secotools.com/acton/fs/blocks/showLandingPage/a/45194/p/p-00dc/t/page/fm/0
Frame height - 650 px
The key machining operations involved in producing aerospace jet engine turbine disks include pre-milling dovetails and fir trees, broaching dovetail slots, gear skiving splines, edge profiling, rough turning and finish turning. All operations require holding extremely tight tolerances and generating specified surface finishes while avoiding heat generation that can affect base material integrity. As these sequential machining operations progress, the investment of time and effort significantly increases part value, so anytime you can improve the speed and efficiency of each operation, you shorten delivery time and boost profitability.
Turbine blade disks can require between 45 and 135 dovetails/fir trees with machining time dependent on disk thickness. The female profiles of disk dovetails and fir trees match the male profiles of turbine, compressor and fan blades. In pre-milling disks, advanced Seco high-performance and solid-carbide end mill cutters, along with special-profile cutters for dovetails and fir trees, enable you to balance time, cost and risk. The tools provide high-material removal rates to shorten cycle times without imparting stress on disk base material. While doing so, they also reduce the risk of tool breakage, part damage and scrap. For added cost savings and longer working life, Seco offers reconditioning and recycling programs for dovetail tooling.
Although several aerospace manufacturers have switched to milling disk dovetail slots, many are locked into roughing and semi-finishing them with the broaching method.
In these instances, the combination of high-quality tailor made tools and inserts, such as single-tooth broaching bars, along with advanced broaching CNC programming strategies from Seco, enable you to achieve extremely tight tolerances and stringent surface finishes much faster in less overall processing time.
To generate a turbine disk gear spline, aerospace manufacturers either use dedicated gear machines or opt for gear skiving on multi-tasking mill-turn machining centers. When splining on dedicated gear machines, Seco gear-milling solutions can shorten cycle times significantly critical for large-batch production. However, such specialty machines involve higher initial capital investments and the inevitable production bottlenecks of installation. They also add another machine to the overall turbine disk manufacturing process, increasing the risk of setup errors while consuming valuable production time.
Gear skiving can be good news for jet turbine disk manufacturers as Seco’s gear skiving tools boost part processing flexibility and eliminate the time-consuming setups required for multiple machine operations. With fewer setups, you also significantly lower the risk of errors and stacked tolerances.
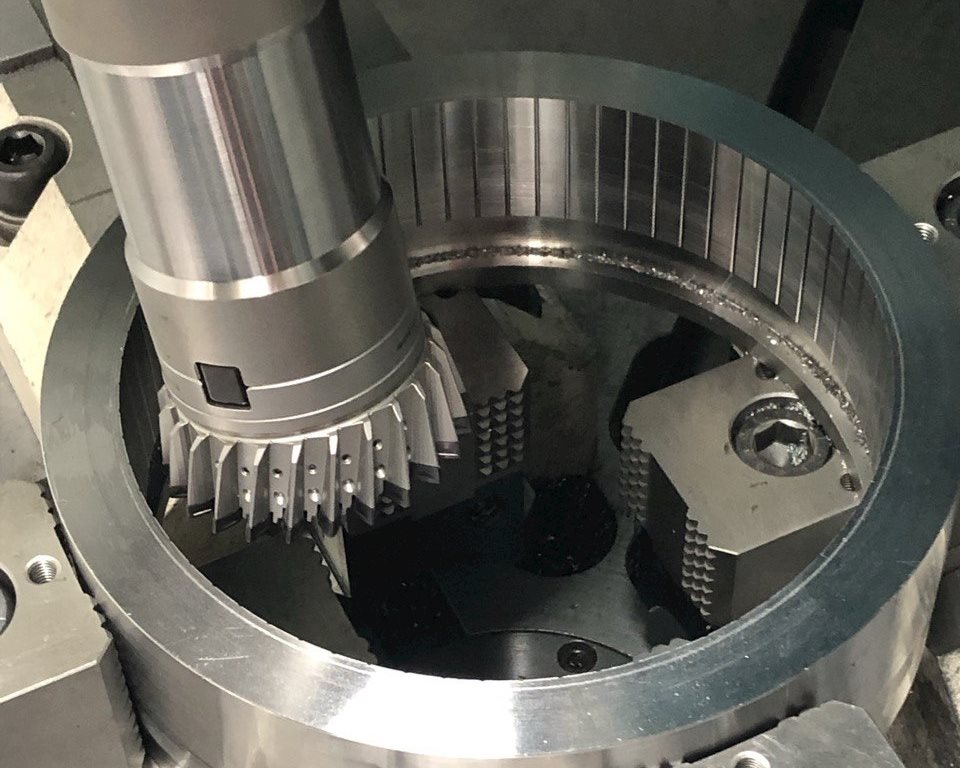
Any inconsistencies in deburring/edge profiling turbine disks can lead to part failure and catastrophic outcomes. Accordingly, you can perform the task as a mechanized CNC-controlled operation with Seco engineered edge profile tooling. Unlike time-consuming, inconsistent manual deburring that is harmful to workers, MEP removes humans from the equation and takes place in an enclosed machine. The part remains clamped after previous operations to maintain reference points, ensure reliability and high quality while maintaining the health and safety of operators.
The investments of equipment and time involved with manual deburring then shift to tooling for existing equipment. With Seco MEP tooling, you gain complete part feature accessibility – from the top, bottom or along varying radii – so no edge is missed.
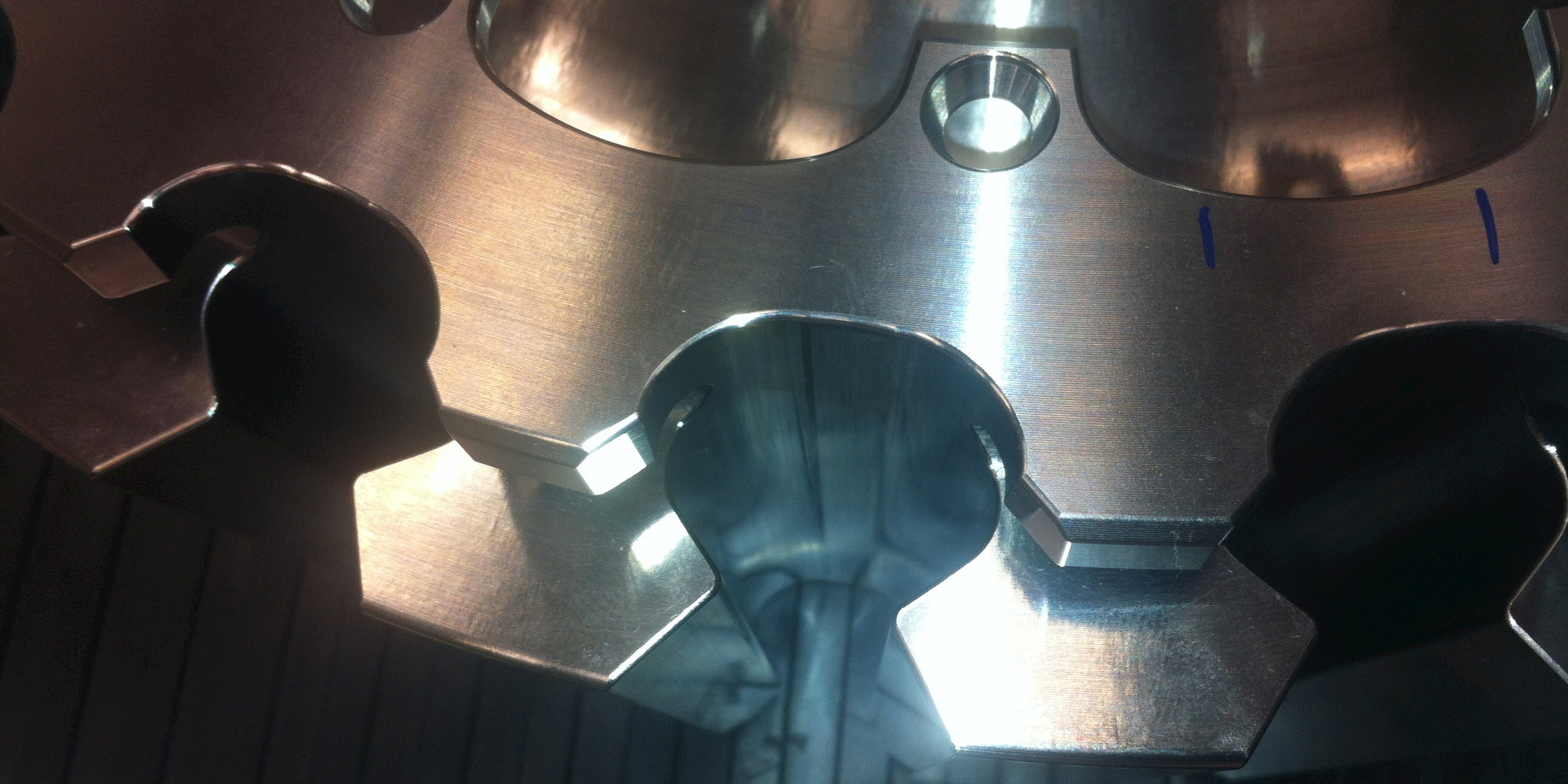
Depending on workpiece material, aerospace manufacturers use either ceramic or carbide inserts to rough turn disks. In either case, chip flow control is mandatory to maximize productivity. The combination of high-pressure coolant plus properly programmed Seco ceramic and carbide inserts can achieve effective chip management. So you experience less edge chipping and insert breakage, which minimizes process intervention and maximizes process security.
Any imperfections in the finished surfaces of jet engine turbine blade disks can escalate into dangerous fractures and part failure. When finish turning, you must meet exacting tolerances and produce perfect surface finishes without generating heat or adding exorbitant amounts of time to the overall production process. To overcome these challenges, Seco provides advanced PCBN and carbide tooling engineered for the machining strategies you can use to achieve imperfection-free disk surfaces with high levels of integrity.
As an aerospace manufacturer, you look to your tooling suppliers as partners as well as a source of productive tools. Additional services from Seco further enhance the quality of that relationship and its value to you. Seco services include tool reconditioning for better amortization of costs, consulting expertise that assists in process optimization and a reliable supply of the necessary tools. A tooling supplier must offer a holistic approach to parameters, machines, fixtures and programming to help manufacturers optimize their entire process and gain maximum value.
The essential machining operations for producing aerospace turbine discs include power skiving, fir tree machining with form cutters, coupling machining, seal fin turning and mechanized edge profiling. All those operations demand exceptionally tight tolerances and the generation of specific surface finishes, while minimizing heat generation that affects the integrity of the base material.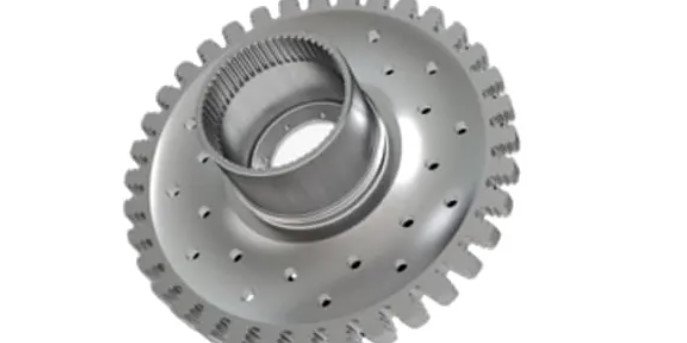
In this demo, watch how we tackle the challenge of machining difficult materials using the latest strategies and Seco tooling. Our 5-axis mill-turn machine boasts capabilities in power skiving and multi-axis turning.
The work holding system has been meticulously designed to safeguard critical features like the seal fins and incorporate an expanding mandrel with external splines that perfectly match and securely grip the internal splines on the component, ensuring extreme stability throughout the machining process.

Collaborative Partners:
- Siemens
- Grob
- Craftsman
- Blum
- AMRC
Contact us here