Is this the future of orthopaedics?
The development of smart implants for use in orthopaedic surgery has the potential for making dramatic improvements to patient diagnostics. The global market for orthopaedic devices is booming. It’s currently valued at US $60.2 billion and is projected to be worth $81.4 billion by 2027 1, though when it comes to a better quality of life, the value for patients who are fitted with implants such as prosthetic knees, hips or elbows is priceless.The development of smart implants for use in orthopaedic surgery has the potential for making dramatic improvements to patient diagnostics. Dominic Connor, Seco Tools’ Global Medical Application Engineer, explains more about this new technology.
The global market for orthopaedic devices is booming. It’s currently valued at US $60.2 billion and is projected to be worth $81.4 billion by 2027 1, though when it comes to a better quality of life, the value for patients who are fitted with implants such as prosthetic knees, hips or elbows is priceless.
The sophistication of implants is also growing. The latest frontier for the technology is ‘smart implants’. In August 2021, industry giant Zimmer Biomet and medtech company Canary Medical announced the launch of Persona IQ ®, the world’s first ‘smart knee’, cleared by the US Food and Drug Administration for use in knee replacement surgery.
The ‘smart knee’ combines the proven technology of Zimmer Biomet’s prosthetic knee with Canary Medical’s implantable reporting processor (CHIRP). The processing chip is implanted inside the tibial extension segment of the knee, which is actually anchored to the patient’s tibia.
“The chip monitors the patient’s outcome after being fitted with the knee implant,” explains Dominic Connor. As Global Medical Application Engineer for Seco Tools, Connor keeps a close eye on new developments within orthopaedics and the wider medicare industry.
“Today, the doctor normally gives post-surgical recommendations to the patient of, say, three hours of exercise and 10,000 steps a day, so that the knee implant will have the best chance of working properly and giving you the right medical outcomes.
“But to a great extent doctors are relying on medical markers of progress, such as muscle build-up, and trusting the patient’s word that they are following the exercise recommendations to the letter.
“What this smart implant technology does is take patient recollection of their own rehabilitation out of the equation because the chip monitors the patient’s movement via the implant and sends that information to the cloud. It’s early intervention through real-time monitoring and ensures that the doctor and patient can work together to achieve the best outcome for the patient.”
It’s a technology whose application has the potential to transform orthopaedic patient care, and the ‘smart knee’ is expected to soon be joined by similar smart implants. But it also brings certain challenges. In particular, the manufacturing and machining of such devices.
“This is just the first instance of putting chips into a component,” explains Connor.
“In this instance it’s complementary components combining to make a smart implant, but in some instances you might not be able to put a chip into a separate component and build that into the implant assembly, meaning that the chip will physically have to go into the implant. This creates a challenge from a manufacturing point of view: a reasonably complex component is going to become a lot more complex because you’ll need to decide where you put the chip, the implant and battery in what is a finite space.
“As an example, wall thicknesses of the implant might decrease with the need to accommodate all the new parts. Machining thin walls and controlling the process to stay within component tolerances is a familiar challenge; will you end up with a reliable process to manufacture that feature economically and ensure that it’s sufficiently durable?”
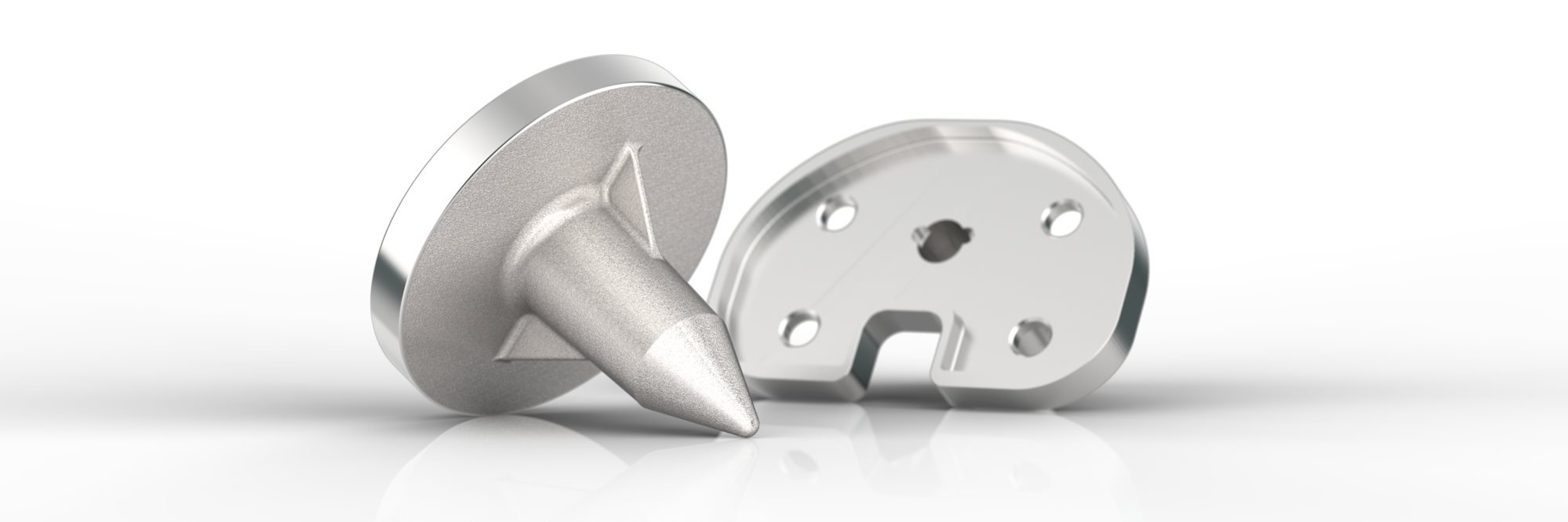
In this respect, the role of a metal-cutting solutions manufacturer such as Seco Tools can have a vital role to play. The more complex nature of a smart implant could require its designers to consult with toolmakers much earlier on in the development phase, to ensure that what they come up is producible from the moment it’s given to the manufacturing team, potentially saving a lot of time and money.
“We sometimes see a real disconnect between development and engineering teams and their production colleagues. Making a few components in a test or proving environment is different to establishing a process which needs to be robust enough to reliably produce 700,000 of these parts a year,” says Dominic Connor.
“A crucial success factor is to have more collaboration at the beginning in co-developing processes and strategies with the correct tools. We know that the earlier we can get involved in that process, the better the process outcome will be.
As smart technology takes hold and material choices become more advanced and diverse, it’s clear that the world of implants is entering a period of immense change. There are many moving parts to this equation and collaboration across industries and disciplines – be it regards to smart technology or smart tools to make it -- will be crucial.
“Where we need to be is our customers saying to us - ‘we’re developing the next-gen knee that’s going to be released in the next five to ten years. What do you as a cutting tool partner need from us to enable you to support us producing that knee in the future?’,” says Connor.
“There’s an old African proverb that applies here,” he adds. “If you want to go fast, go alone, but if you want to go far, go together’”.