Reduce Tool Deflection with a Short Reach
Tool deflection is a form of vibration that occurs when the dynamic cutting forces of machining cause the cutter to yield to the resistant force of the work piece. Discover the several ways to address tool deflection in milling.Tool deflection occurs when the dynamic cutting forces of machining cause the cutter to yield to the resistant force of the work piece. In other words, the tool bends due to the mechanical loads of cutting.
Tool deflection is a form of vibration and vibration in machining is always a challenge that must be solved. Vibration comes in many forms, but the solution virtually always centers on stability of the machine tool or its cutting tool. Tool deflection can cause chatter, which, when sufficiently high, endangers the quality of the machining process.
Tool deflection and its attendant vibration patterns during machining cause a variety of problems that include:
- Uncontrollable and unpredictable extra wear on cutting edges that negatively impacts process reliability and decreases tool life;
- Inferior surface finishes and increased scrapped or reworked parts;
- Severe lack of dimensional accuracy.
As a result of those individual adverse effects caused by tool deflection, manufacturing economics are also impacted. Undue vibration uses and wastes energy, challenges operators to devote time to solving the problem and leads to inordinate tool wear, breakage, scrap and downtime that make for inefficient and unsustainable machining.
There are several ways to address tool deflection in milling. Using CAM systems, for instance, is one way to optimize tool paths. Other approaches include:
- Using milling cutters with a coarse pitch and clamping them with the shortest possible overhang;
- Selecting tools with positive geometries;
- Employing carbide grades with thin coatings;
- Improving clamping system stability with tapered tool holding and the largest possible connection size.
However, to solve the challenge of tool deflection, overall tool rigidity is critical. Bending is a function of overhang length and tool diameter. The more tool reach incorporated into a setup, the less rigid and stable the process becomes. For optimum tool life, there should be less than 0.001” of tool deflection – and even less when the process uses small tools.
In this #SecoTechTalk installment, Seco Product Manager Jay Ball says solving end mill tool deflection is like telling a good story: keep it short. Limiting tool projection/overhang will keep deflection in check. Choking down on the end mill with the tool holder is the easiest way to reduce tool deflection. Make sure the end mill is inserted into the holder to a length of two to three times the outer diameter of its shank.
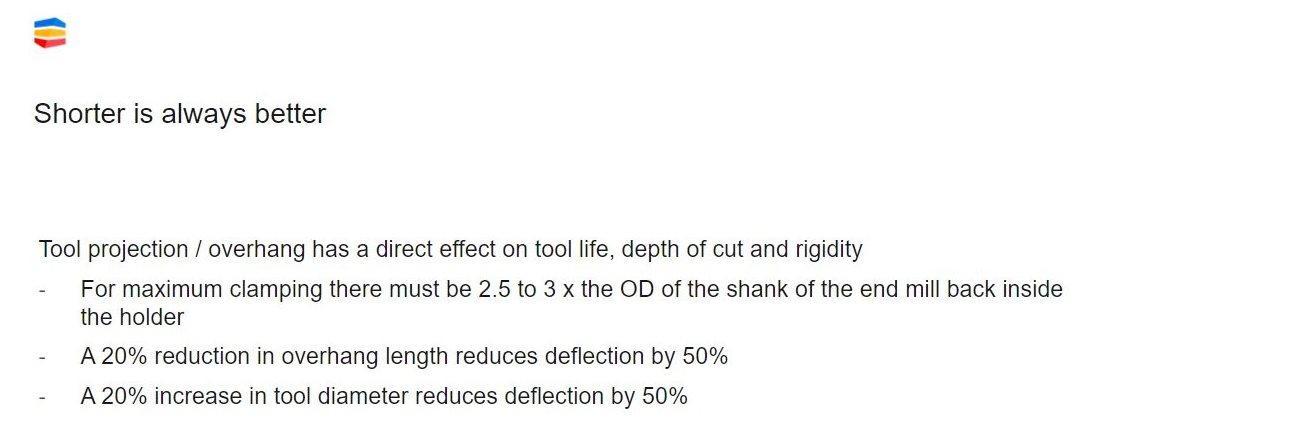
Reducing a tool’s overhang will have a significant impact on resisting deflection. In fact, a 20% reduction in overhang length will reduce deflection by 50%. Check out Jay’s #SecoTechTalk to learn more about how to solve the challenge of tool deflection.
For more tips on getting the most from your machining operations, catch more episodes of Jay’s #SecoTechTalk on Seco Instagram. There you’ll find practical advice that makes your machining more efficient and sustainable. Be sure to let him know what you want to hear about next.
Inline Content - Survey
Current code - 5fce8e61489f3034e74adc64