Reduce Chatter for Better Machining
Machinists have been chasing the causes of chatter in machining and learning how to avoid chatter in machining for more than a century. CNC chatter is self-exciting vibration that can be traced to the cutting tool or the workpiece. When chatter causes poor surface finishes and/or excessive tool wear to the point that tool life is compromised, tool chatter troubleshooting becomes necessary.Chatter, a form of unwanted vibration, is present in virtually all forms of machining and common when milling corners. In his 1906 article to the American Society of Mechanical Engineers, Frederick Taylor called chatter “the most obscure and delicate of all problems facing the machinist.” Despite quantum advances in technology, the manufacturing industry continues to chase this obscure and delicate problem.
Though vibration in machining comes in many forms, it is resonate vibration that occurs when one component vibrates at or near another part’s natural vibration frequency and amplifies it. In many cases, cutting forces set up a vibration at the cutting edge that is at or near the resonate frequency of the cutting tool. The resulting “self-exciting” vibration is known as chatter that is traced to the cutting tool or at the workpiece.
There are several potential causes of chatter. Slender cutting tools, thin-walled workpieces, cutting forces that are too high, incorrect tool geometries and wrong cutting parameters or machining strategies can all cause or contribute to chatter. Initial indications of chatter are high-pitched noises emitting from the machine and a scalloped, wavy or rough surface finish appearance.
Chatter comes with significant economic impact. The unacceptable surface finish (previously mentioned as a chatter indicator) requires secondary processes to meet specifications. In addition, chatter can translate into excessive tool wear which drives up inventory cost and creates downtime through frequent changeovers. Further, chatter can damage the spindle and machine tool.
Chatter, by itself, is not always an issue in the machining process. However, when it causes poor surface finishes and/or excessive tool wear to the point that tool life is compromised, tool chatter troubleshooting becomes necessary.
To minimize chatter, always use the most rigid tools and toolholders available. The same principle applies to workholding and fixturing. Shorten tool overhangs as much as possible and reduce vibration by using antivibration bars. Ensure that tools are sharp, and that the appropriate cutting data is being used. If adjustments are required, consider reducing depths of cut and cutting forces. In terms of the entire machine tool, explore alternative spindle speeds that might reduce overall harmonics in the system.
In the latest installments of #SecoTechTalk, Seco Product Manager Jay Ball shows you how to calculate the minimum corner radius for any solid end mill product to avoid jamming the tool hard into a corner. Allowing the machine tool time to strike an arc eliminates the chatter and improves tool life and surface finishes.
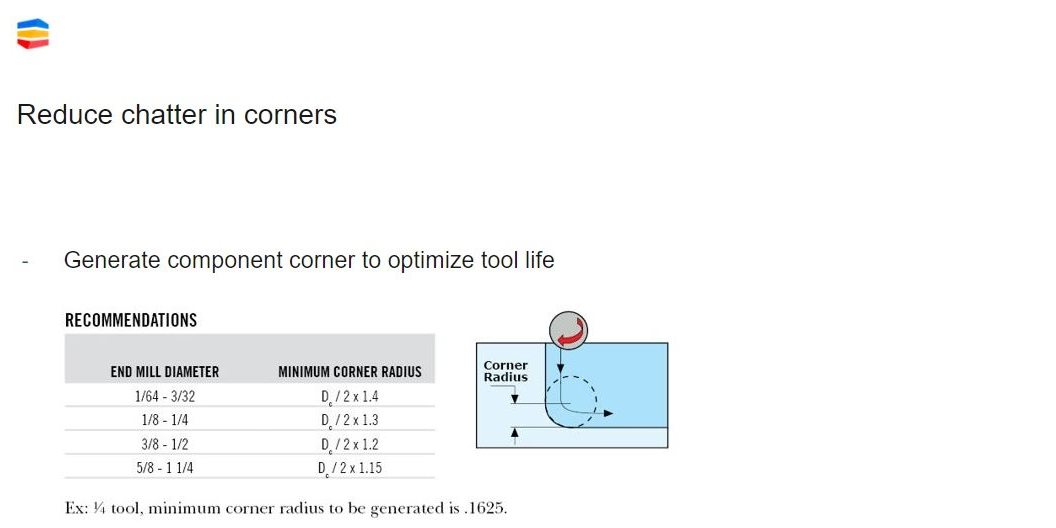
For tips on getting the most from your machining operations, catch more episodes of Jay’s #SecoTechTalk on Seco’s Instagram. You’ll find practical advice that makes your machining more efficient and sustainable. Leave a comment to let him know what you want to hear about next.
Inline Content - Survey
Current code - 5fce8e61489f3034e74adc64