Precision Aerospace Machining: Exploring Carbide, Ceramic, and PCBN Inserts
Delve into the world of precision aerospace machining in this insightful blog. Explore the benefits of Carbide, Ceramic, and PCBN inserts for achieving unparalleled efficiency and precision in manufacturing.In the dynamic realm of aerospace manufacturing, precision and efficiency are not just desirable attributes but absolute necessities. As the industry continues to evolve and embrace new technologies, the choice of cutting-tool inserts plays a pivotal role in determining the success of machining operations.
In this comprehensive guide, we embark on a journey through the innovative landscape of Carbide, Ceramic, and PCBN inserts, exploring their unique characteristics, applications, and contributions to precision engineering in the aerospace sector.
At the foundation of precision machining lies carbide inserts, celebrated for their unparalleled versatility and reliability. Engineered from a composite of tungsten carbide particles, alloying elements, a binding agent and often a coating, carbide inserts offer remarkable hardness and wear resistance, making them indispensable for a wide range of machining tasks. From roughing to finishing operations, carbide inserts excel in delivering consistent performance and cost-effectiveness across various aerospace components.
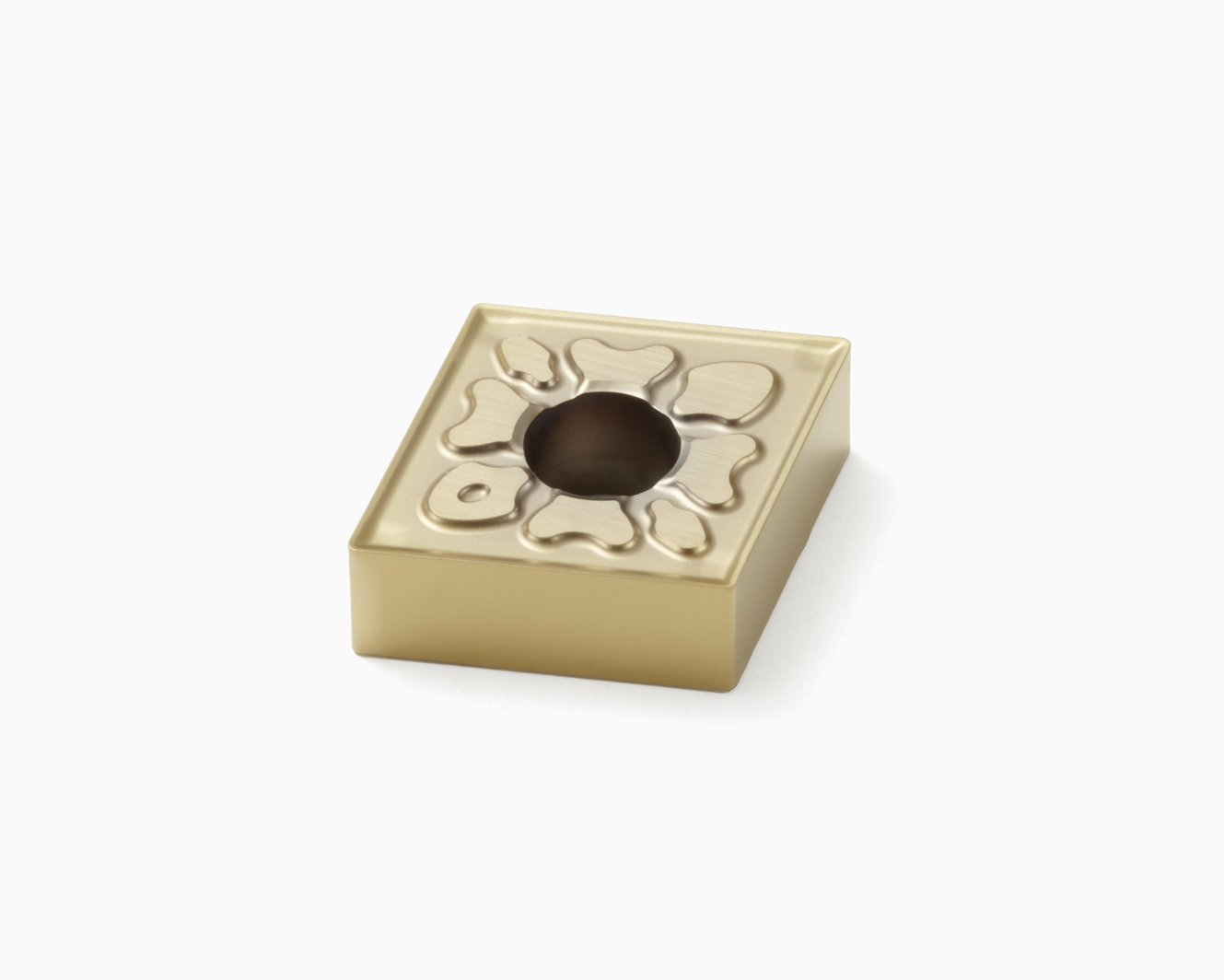
The versatility of carbide inserts extends to their adaptability to different machining conditions and materials. Whether machining aluminum alloys, titanium, or high-temperature nickel-based superalloys like the Inconel-class, carbide inserts demonstrate remarkable stability and efficiency.
With a diverse range of shapes, sizes, and cutting geometries, carbide inserts empower aerospace manufacturers to achieve precise dimensional accuracy and surface finishes, essential for meeting stringent industry standards.
However, despite their versatility, carbide inserts do have a limitation – they cannot operate at the same high cutting speeds as PCBN or ceramics, which becomes decisive if productivity is the main factor.
As aerospace manufacturing ventures into realms of higher temperatures and exotic materials, ceramic inserts emerge as pioneers in heat-resistant machining. Crafted from advanced materials such as alumina or silicon nitride, ceramic inserts exhibit exceptional hardness, thermal stability, and chemical resistance, making them ideal for challenging machining environments.
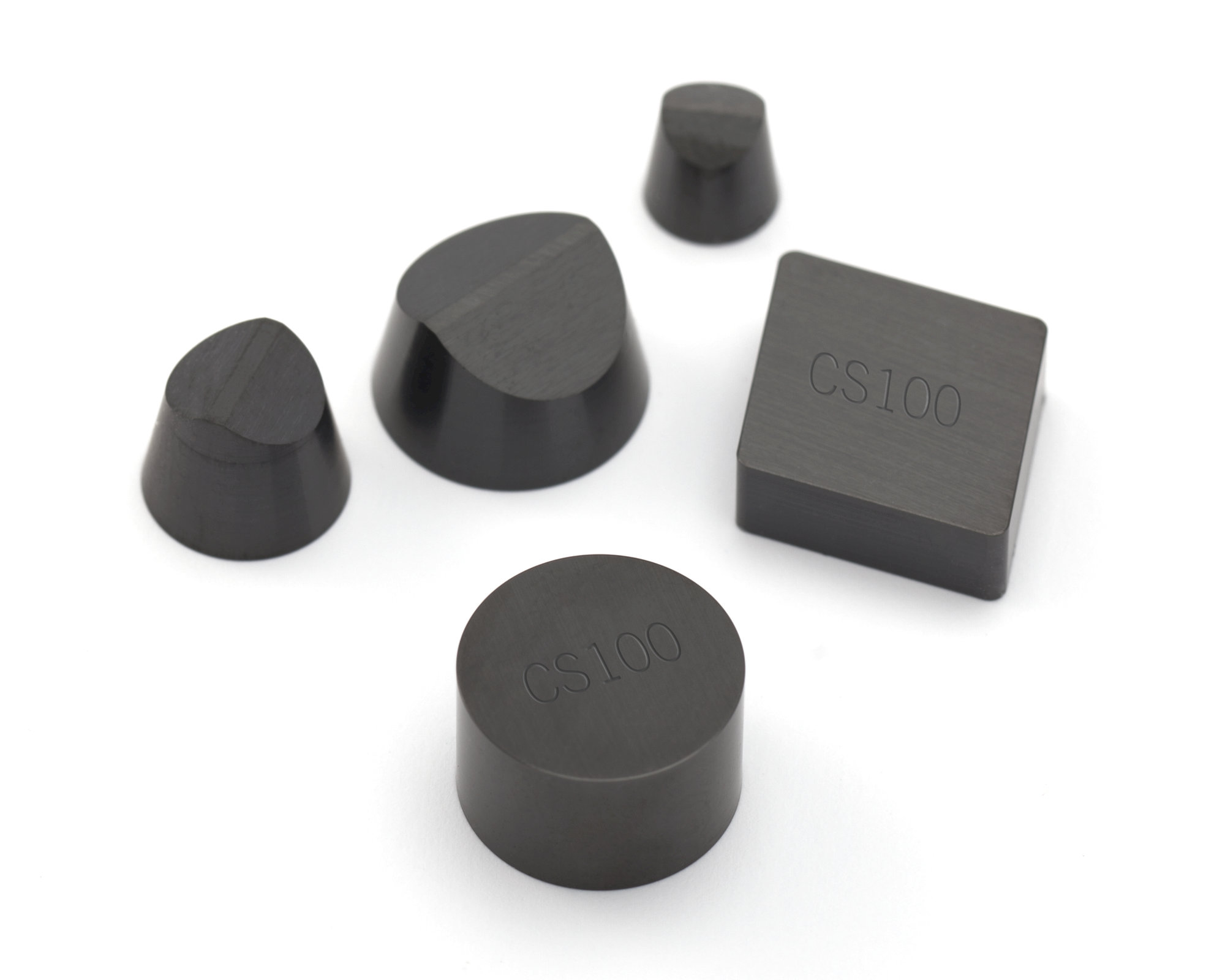
One of the primary advantages of ceramic inserts lies in their ability to withstand elevated temperatures without compromising on performance. In high-speed machining of aerospace alloys, ceramics maintain their cutting-edge integrity, minimizing tool wear and extending tool life.
Furthermore, their inherent resistance to chemical reactions ensures compatibility with a wide range of workpiece materials, reducing the risk of insert degradation or material contamination.
However, the brittleness of ceramic inserts presents a notable challenge, particularly in applications involving interrupted cuts or sudden load variations. Careful selection of cutting parameters and toolpath strategies is essential to mitigate the risk of insert chipping or fracture. Additionally, achieving desired surface finishes and chip control may require specialized cutting geometries and edge preparation tailored to ceramic insert materials.
In the pursuit of machining excellence, PCBN inserts emerge as the epitome of precision engineering, especially when facing hardened materials prevalent in aerospace components. Composed of polycrystalline cubic boron nitride, PCBN inserts exhibit exceptional hardness, thermal conductivity, and wear resistance, surpassing traditional insert materials in demanding machining applications.
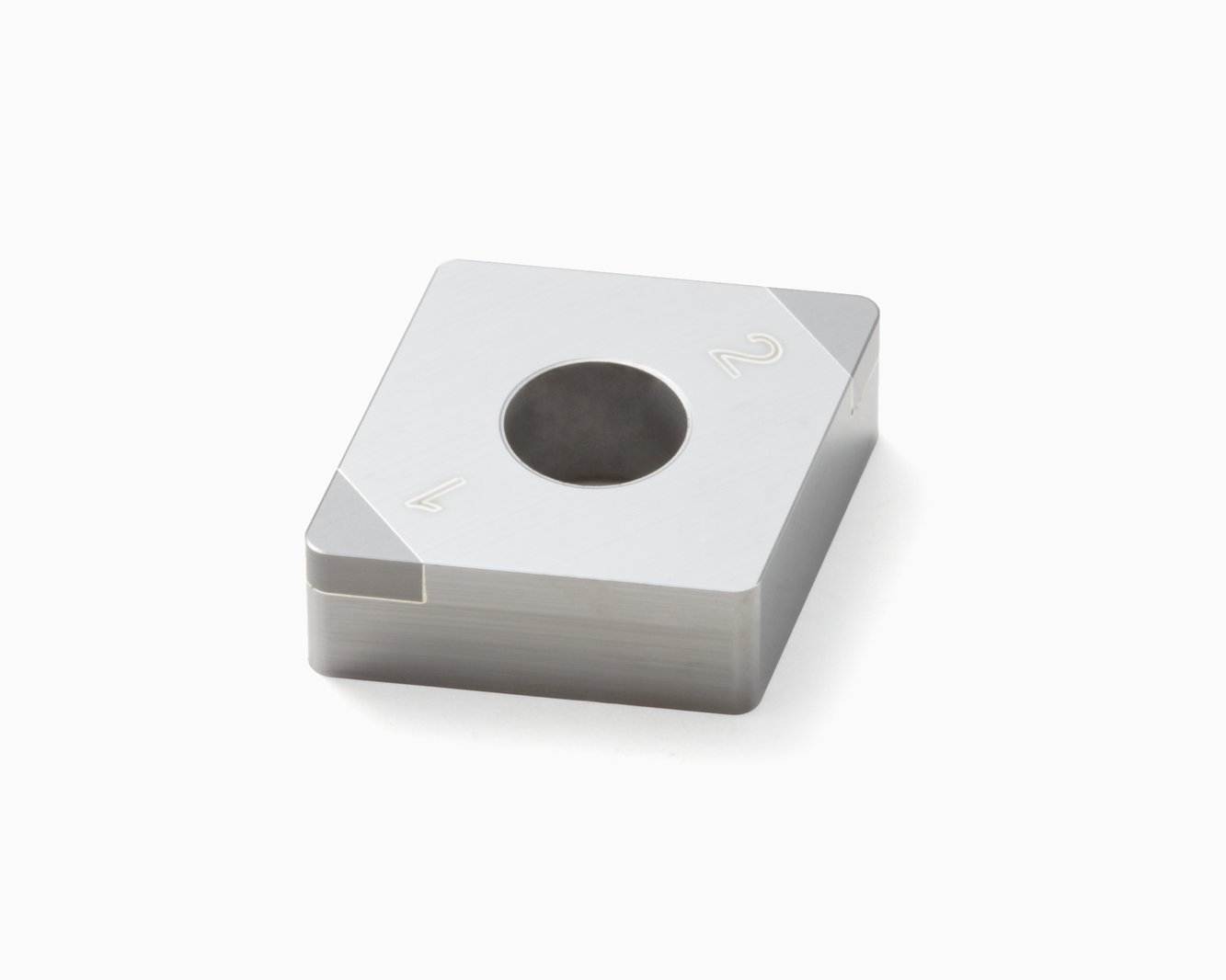
The primary advantage of PCBN inserts lies in their ability to machine hardened materials with unparalleled precision and efficiency. Whether machining turbine discs, spools, shafts or casings, PCBN inserts deliver superior surface finishes, dimensional accuracy, and tool longevity, essential for meeting the exacting requirements of aerospace manufacturing.
Additionally, PCBN inserts excel in high-speed machining environments, where elevated cutting temperatures and forces are common. Their superior thermal conductivity ensures efficient heat dissipation, minimizing the risk of insert deformation or thermal damage to workpiece materials. Moreover, PCBN inserts exhibit excellent chemical stability, reducing the risk of built-up edge formation or material adhesion during machining.
However, the initial investment cost of PCBN inserts may pose a deterrent for some aerospace manufacturers, particularly those operating on tight budgets or with limited machining requirements. Furthermore, the inherent brittleness of PCBN inserts necessitates careful handling and machining practices to prevent insert breakage or premature wear.
In the ever-evolving landscape of aerospace manufacturing, strategic considerations guide the selection and utilization of cutting-tool inserts. Material compatibility, machining requirements, cost considerations, and performance expectations are paramount factors in determining the optimal insert solution for a given application.
For those seeking deeper insights into the intricacies of aerospace machining and advanced insert technology, our comprehensive whitepaper offers invaluable resources and expertise. Delving into the nuanced details of carbide, ceramic, and PCBN inserts, the whitepaper provides actionable insights and best practices for achieving precision engineering excellence in aerospace manufacturing.
Inline Content - Gridded Links
Tags: 'wp_insert_pcbn_carbide_ceramic'
Max links: 1
As aerospace manufacturers navigate the complexities of precision machining, Seco stands as a trusted partner, offering a visionary array of cutting-tool solutions tailored to the demands of modern aerospace manufacturing. With our commitment to innovation, expertise, and customer-centric approach, we empower aerospace manufacturers to push the boundaries of precision and efficiency, driving progress in the aerospace industry.
Discover our Innovation Hubs
Innovations in aerospace machining are redefining the boundaries of precision engineering, fueled by advancements in cutting-tool technology and materials science. By harnessing the capabilities of carbide, ceramic, and PCBN inserts, aerospace manufacturers can achieve unparalleled levels of precision, efficiency, and quality in their machining operations. As the industry continues to evolve, strategic partnerships with industry leaders like Seco pave the way for groundbreaking advancements and transformative solutions.
Inline Content - Survey
Current code - 5fce8e61489f3034e74adc64