Aerospace Blisks
Improve blisk production with custom tools. Take advantage of Seco industry expertise to optimize machining, programming, paths and strategies.Blisk manufacturing combines challenging part geometry, materials, processes and stringent quality control. Suppliers struggle to meet tight tolerances and satisfy customer demands for greater efficiency and lower costs. As engine designs evolve and fuel efficiency becomes an increasing industry focus, super alloys for high-temperature applications and weight-saving light materials continue the trend toward hard-to-machine aerospace parts.
Turbine blisks highlight these challenging trends. All engine blisks perform the same functions, but every blisk design is unique. To achieve part quality throughout machining and finishing operations in manufacturing, suppliers need optimized strategies that combine the right tooling, programming and approaches. From barrel cutters and mechanized edge processing (MEP) to custom-produced, additive-manufactured tools, suppliers look for solutions that reduce setups and tool counts, eliminate burrs and cut out secondary processing.
Optimization helps avoid costly scrap of high-value parts. Reliable, repeatable processes enhance unattended production to reduce bottlenecks and increase high-quality output. A tooling manufacturer with in-depth expertise in aerospace applications can provide suppliers with complete packages of consulting advice, customized tooling and machining approaches to tackle these complex parts successfully. Tooling-manufacturer support also can help decrease cycle time, eliminate manual intervention and secondary paths.
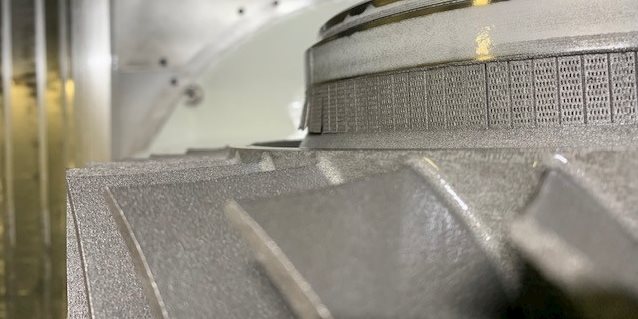
Aerospace customers extract cost concessions and expect high quality from part suppliers. As sustainability calls for development of new regionalized aircraft and engine designs that improve fuel economy on increasingly shorter routes, new designs result in smaller, more-efficient aircraft with improved performance and fuel efficiency from new lightweight and heat-resistant materials. By definition, materials for high-temperature applications and for weight reduction present greater challenges for manufacturers throughout production, especially on complex parts such as turbine blisks.
Customer pressures and production complications leave external suppliers and in-house OEM production facilities looking for new approaches to blisk manufacturing. These facilities strive for longer tool life, fewer tools, more production automation, fewer setups and reduced energy requirements for machining, all in the name of cycle-time and cost reduction. Increasingly, suppliers seek to cut cycle times and improve blisk quality with customized tools that eliminate burrs and minimize post processing.
Blisk designs vary uniquely from aircraft to aircraft, but all of them include a specific list of features. In particular, blades and seal fins demand high quality operations – and offer opportunities to streamline production with greater production efficiency. Stabilizing the part for machining becomes more and more difficult as part features become thinner with each successive operation, which can cause damaging vibration during machining. Difficult-to-reach part features demand special tools for best results. As production progresses, the part rises in value because of the accumulation of processes, which heightens the importance of stability, repeatability and reliability to eliminate expensive scrap. A greater focus on unattended machining prompts the quest for stable, repeatable processes without post-finishing operations.
Many production lines use more than one tool for this critical task. Machining individual fins separately can result in burrs, which require manual intervention that raises machining costs. To produce highly accurate, very sharp part features and reduce or eliminate burrs, secondary tool paths and manual intervention, customized tools – some manufactured through 3D printing – can machine these fins in one motion. Jetstream Tooling® holders assist in providing stability and reducing cycle times.

Among finishing operations in manufacturing, blisk blades provide some of the biggest challenges that manufacturers face. To achieve part geometry and optimal surface finish without deflecting the shape or position of the blades, manufacturers must keep these thin, vibration-prone parts stable. Barrel cutters with larger stepovers help shorten cycle times by up to 90% on semifinishing and finishing operations. In some cases, the geometry of blade surfaces and the narrow widths of blisk bays make it difficult to use the latest barrel tools for blade finishing because of tool-shank collisions at extreme tool tilt angles. In those cases, taper ball nose (TBN) tools step in to take care of the task.
Beyond tooling itself, collaborative strategies and innovations help increase stability and improve surface quality. Programming optimization includes optimized cutting paths as well as processes that overcome the limitations of machining software to optimize use of barrel cutters.
To improve product quality, shorten machining time and reduce setups during surface finishing operations, part rigidity helps optimize the process. Specialized tools with optimized programming and cutting strategies match the unique shape of an individual blisk for better results. Mechanized edge processing (MEP) helps reduce and even eliminate edge burrs. As with all operations on a tight-tolerance, high-value part, finishing operations benefit from the ability to maintain rigidity during machining.
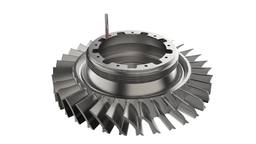
Blisk manufacturers quickly itemize their short list of production goals, all of which center around faster cycle times, fewer processes and higher-quality results. Seco Tools has amassed the expertise and experience to eliminate manual intervention and secondary paths, reduce tool requirements and improve tooling designs for machining. In addition to tooling solutions, Seco provides holistic solutions that address the critical needs of the entire production process.
From programming recommendations to custom 3D-printed tools and optimized machining strategies to efficient approaches, Seco constantly strives to help blisk manufacturers increase product quality, reduce cutting time and tooling costs. To meet production demands for greater efficiency, quicker output and lower tooling costs, manufacturers can partner with Seco to boost their profitability as well as their productivity.
Contact Seco today to find out how we support every aspect of your production with so much more than tools.
Contact us here