Produce better steering knuckles with fewer tools
Optimized combination tools that accept off-the-shelf inserts make it easy to improve steering-knuckle manufacturing with fewer tools.Steering knuckles contain wheel hubs or spindles, and attach to the suspension components of a vehicle. Made from nodular cast iron, forged steel and aluminium, the components are critical to front suspension safety, so quality surface finishes, precision radii and perfect machined flatness are required.
As new automotive brands and technologies come to market, connect-to-ground manufacturers face material shortages, regulatory requirements and a lack of skilled labor. To make sure they can produce enough steering knuckles to meet consumer demand for new vehicles, they automate their production processes and look for ways to simplify tooling. At the same time, their customers expect them to make more parts faster and reduce cost per part.
The move to hybrid, electric and hydrogen vehicles makes many automotive parts obsolete and adds new ones to the production line. Steering knuckles remain part of the production mix, regardless of vehicle type. Their complexity – and the need to closely meet specifications and geometry – requires repeatable precision.
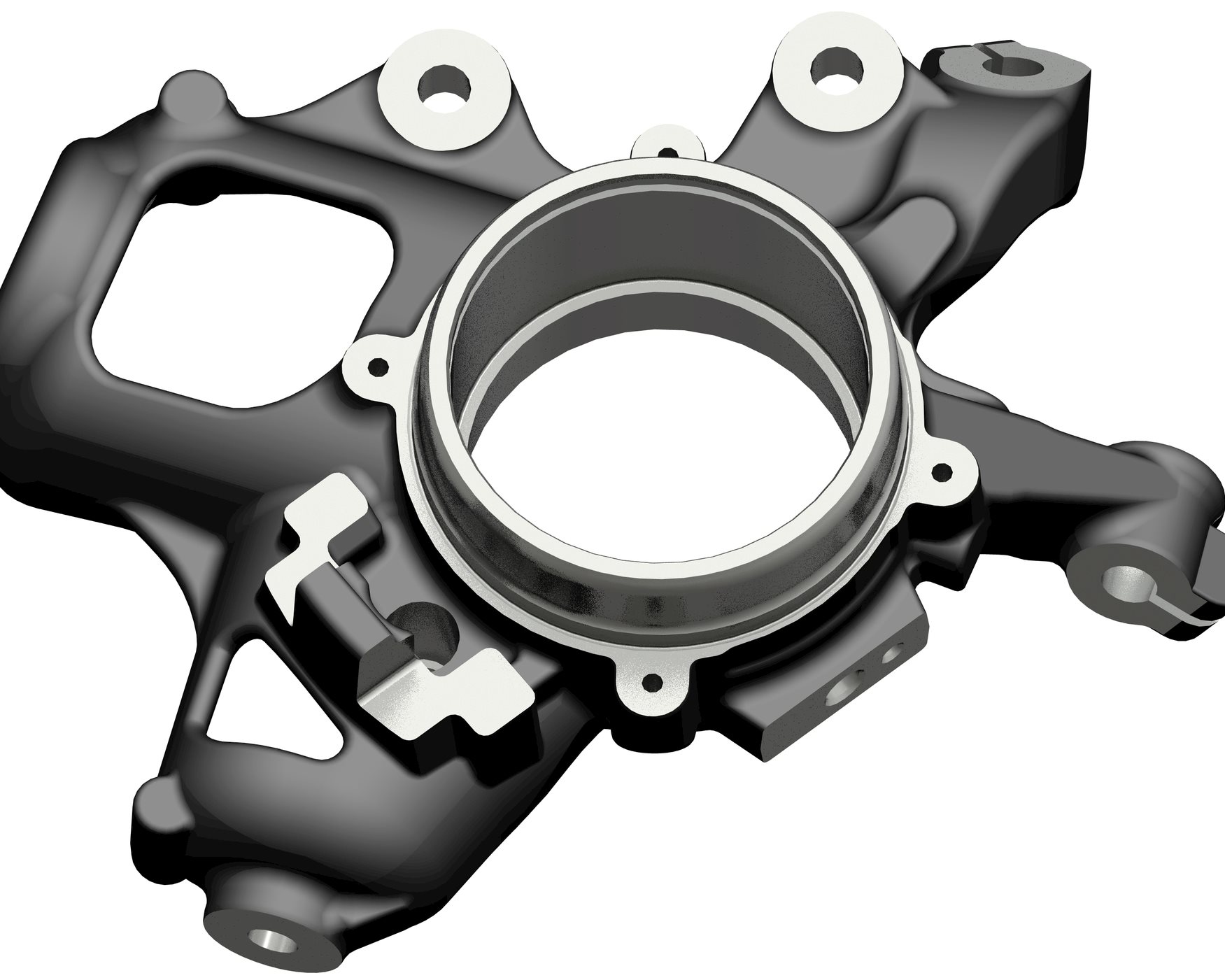
Steering knuckle designs look radically different from one vehicle model to the next, but they all involve specific types of production processes. Seco provides all the milling, drilling, grooving, reaming and finishing tools for these operations. These include standard tools and inserts as well as specialized designs. All of them minimize vibration, maximize surface finish quality, optimize chip control, provide process security and offer easy setup.
To meet the high technical standards for these parts without using large, heavy tools that slow production, Seco offers combination tools that simplify operations. Additionally, manufacturers can access more than 80 years of Seco machining knowhow to help them train less-experienced operators and remove bottlenecks in the machining process.
For high-quality results without the production slowdowns that large, heavy tools can cause, steering-knuckle manufacturers look for combination tools and specialized options that any operator can use easily. Seco provides a full selection of milling, drilling, grooving, reaming and finishing tools for this specialized set of production processes, including many that accept off-the-shelf inserts.
Now steering-knuckle manufacturers can eliminate vibration, improve surface finishes and tool life, and boost their production output – with fewer tools. Along with optimal tooling, Seco also offers the benefits of more than 80 years of machining expertise. We help steering-knuckle manufacturers remove production bottlenecks and improve workforce training for success in a competitive industry.
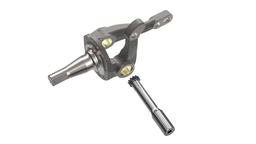
- Eliminate poor chip control that can compromise surface finishes and part quality.
- Produce parts that meet demanding specifications for steering knuckle manufacturing.
- Simplify machine tool setup.
- Achieve bore concentricity.
- Reduce tool index compared to table index.
- Combine semi-finishing operations to reduce tool requirements and steering-knuckle cycle times.
- Avoid risk of surface finish damage.
- Maintain good chip breaking.
- Implement advanced table indexing.
- Maintain stock allowance for drilling and semi-finishing to control chips.
- Ream from one side for greater concentricity.
- Optimize tooling design with cermet.
Face mills
Drills
Reamers
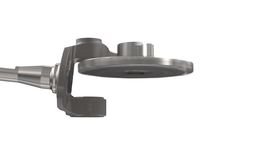
- Eliminate machining vibration.
- Optimize use of machine torque.
- Improve surface finishes and tool life.
- Create fixturing that can handle part complexity with stability.
- Limit the challenges of long tool overhangs
- Uncontrolled vibration limits part quality and results.
- Operations need to make optimal use of available machine torque.
- Improper setup and tooling lead to poor surface finishes and short tool life.
- Complex steering-knuckle part designs complicate fixturing.
- Long tool overhangs can cause vibration.
- Bottom radius machining with big nose radii complicates finishing operations.
- Taper hole machining is difficult with bore lengths greater than 80 mm.
- Optimize tooling for steering-knuckle manufacturing.
- Positive geometry enables reduced cutting force.
- Reduced tool weight.
- Disc mills with dampening pads.
- Coarse-pitch cutters.
- Implement push or pull machining.
- Use tangentially mounted fixed insert pockets.
- Implement dry cutting.
Square shoulder mills
Drills
Reamers
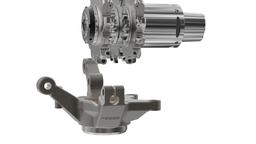
- Reduce production cost and time per part.
- Achieve required steering-knuckle manufacturing quality.
- Limit tool changes to as few as possible.
- Reduce excessive power consumption.
- Manage a high risk of vibration.
- Balance productivity and cost to ensure maximum profitability.
- Achieve the surface finishes required for steering-knuckle manufacturing quality.
- Combination tool designs reduce the number of tools in the tool storage magazine and the number of changes.
- Balance outer disc mills to avoid excessive power consumption from simultaneous cutting.
- Adapt fixturing to reduce vibration with support under the feature.
Outer cutters
Outer inserts
Inner cutters
Inner inserts
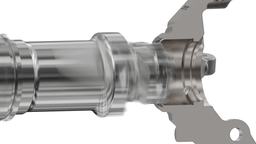
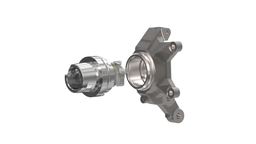

- Meet demanding specifications for part dimensions and quality.
- Limit the need for skilled labor in steering-knuckle manufacturing.
- Reduce cycles times.
- Minimize tool changes to reduce cycle times in steering-knuckle manufacturing.
- Implement automation to achieve low-cost, high-volume steering-knuckle manufacturing with minimal intervention.
- Provide the process security required for dimensional accuracy.
- Limit the need for skilled operators to set or adjust tools.
- Avoid use of large and heavy tools to achieve multi-purpose tooling and combined operations.
- Minimize vibration and maximize surface finishes.
- Achieve concentricity between transmission and bearing diameters.
- Custom multi-step boring bar roughs, semi-finishes and chamfers.
- Grooving tools use double-sided ISO/ANSI inserts.
Grooving tools
Customized monoblock rough/semi-finish tools
Customized reamers
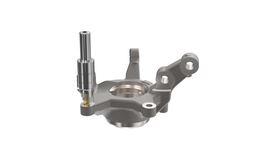
- Combine processes and minimize tool changes.
- Achieve part stability during steering-knuckle manufacturing.
- Avoid the use of long overhang tools.
- Combine face milling, chamfering and drilling to minimize tool changes.
- Limit the number of required positions in the tool magazine.
- Stabilize the fixture and part setup with little direct support for the workpiece.
- Overcome the machining limitations of long overhang tools.
- Multi-process tool designs increase productivity with fewer tool changes.
- Achieve faster steering-knuckle cycle times without sacrificing product quality or cost effectiveness.
Combination drill and spot-face tool with positive geometry
If you would like to reach out to one of our automotive experts please contact us here