Brake Disc
For stopping wheel rotation, brake discs or rotors are usually made of grey cast iron, but in some instances are produced from composites such as reinforced carbon or ceramic matrix composites. As a safety component, brake discs require specific surface finishes, radii, flatness and parallelism. Most often, custom tooling such as combination turning heads and drills are used in machining processes. The casting, ferrite content and ageing can all affect brake disc machinability.
YOUR MANUFACTURING CHALLENGES
- Increasing productivity by roughing many surfaces with the same tool.
- Optimising productivity and reliability when roughing the cast skin on the outer diameter.
- Finishing the bore and setting surfaces with minimal tool changes.
- Maintaining efficiency and reliability when finishing the braking surfaces.
- Maximising productivity when balancing the ventilated brake disc.
- Drilling numerous holes with minimal cost and time.
- Drilling numerous holes with low cycle times, high quality and reliability.
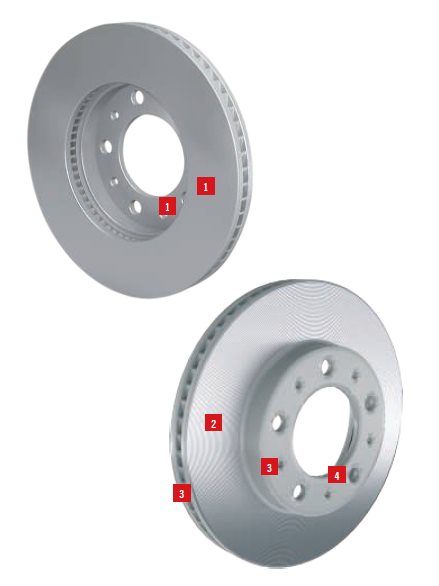
1 - Increasing productivity
Your Challenge: | | Increasing productivity by roughing many surfaces with the same tool. |
Our Solution: | | The Seco-Capto custom turning head system will reduce the number of turret revolutions and can be error-proof modified for mass production applications. Offering highly rigid and accurate performance, the system also enables full automation of presetting by adding electronic data chips to the toolholders. Additionally, CBN300 provides outstanding toughness and heat evacuation, achieving excellent roughing with high cutting parameters. Your benefits include reliable accuracy and increased efficiency. |
Product: | | Seco-CaptoTM Tool with PCBN Insert |
2-3 - Optimising productivity and reliability
Your Challenge: | | Optimising productivity and reliability when roughing the cast skin on the outer diameter. |
Our Solution: | | The flexible Seco-Capto quick change turning head system reduces tool change times and can be error-proof modified for mass production applications. Offering highly rigid and accurate performance, the system also enables full automation of presetting by adding electronic data chips to the toolholders. Additionally, CBN300 provides outstanding toughness and heat evacuation, achieving excellent roughing with high cutting parameters. Your benefits include reliable accuracy and increased efficiency |
Product: | | Seco-CaptoTM PCBN Turning Tool |
4 - Finishing the bore and setting surfaces
Your Challenge: | | Finishing the bore and setting surfaces with minimal tool changes. |
Our Solution: | | The Seco-Capto combined turning head system will reduce the number of turret revolutions and can be error-proof modified for mass production applications. Offering highly rigid and accurate performance, the system also enables full automation of presetting by adding electronic data chips to the toolholders. Additionally, CBN400C achieves toughness and machining accuracy, making it ideal for finishing with high cutting parameters. Your benefits include reliable accuracy and increased efficiency. |
Product: | | Seco-CaptoTM Tool with PCBN Insert |
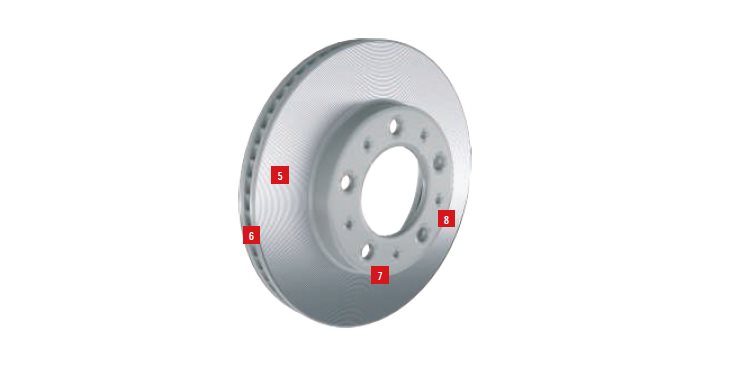
5 - Maintaining efficiency and reliability
Your Challenge: | | Maintaining efficiency and reliability when finishing the braking surfaces. |
Our Solution: | | The flexible Seco-Capto quick change turning head system reduces tool change times and can be error-proof modified for mass production applications. Offering highly rigid and accurate performance, the system also enables full automation of presetting by adding electronic data chips to the toolholders. Additionally, CBN400C achieves toughness and machining accuracy, making it ideal for finishing with high cutting parameters. Your benefits include reliable accuracy and increased efficiency. |
Product: | | Seco-Capto™ PCBN Turning Tool |
6 - Maximising productivity
Your Challenge: | | Maximising productivity when balancing the ventilated brake disc. |
Our Solution: | | Seco’s family of R335 disc milling cutters feature robust bodies for high tool life and incorporate a variety of features designed to optimize machining of cast iron. Positive rake angles reduce cutting forces and vibration to optimize accuracy and energy consumption, and the use of a constant rake angle over the radius maximizes chip evacuation. Your benefits include highly productive performance with extended tool life. |
Product: | | R335.19 Disc Milling Cutter |
7 - Drilling numerous holes
Your Challenge: | | Drilling numerous holes with minimal cost and time. |
Our Solution: | | By offering the ability to chamfer a hole by plunging after drilling, the custom Perfomax Chamfer Drill combines operations to increase productivity. A unique flute design optimizes chip removal, and the use of Perfomax drilling inserts allows for a very cost-effective process. Your benefits include reducing costs while maintaining high process stability. |
Product: | | Perfomax® Chamfer Drill |
8 - Drilling numerous holes
Your Challenge: | | Drilling numerous holes with low cycle times, high quality and reliability. |
Our Solution: | | Providing high performance the Seco Feedmax Chamfer Drill utilises the light-cutting geometry and a special edge preparation to increase process security and tool life. The tool also incorporates a low-friction coating. Your benefits include maintaining productivity in challenging, high-tolerance holes. |
Product: | | Seco FeedmaxTM Chamfer Drill |