Tibial Tray
Learn to optimize medical-implant production, cut costs and create high-quality surface finishes with tools that match your material and parts.To become part of the human body, medical implants require ultra-high accuracy and surface finishes. Medical device manufacturers face constant pressure to boost output and cut costs while they maintain precision. To do so, they must find ways to avoid secondary processes that solve problems but increase production time.
The complete knee assembly is a perfect example. All three of its components must minimize friction and mimic surgically removed bone to provide pain-free comfort and a full range of motion. The tibial tray begins as a solid billet or near net shape, typically cobalt chrome or titanium. Both are hard to machine, place enormous stress on cutting tools and can require costly special tooling. After milling, bead blasting and manual polishing remove tool marks. If manufacturers reduce milling speeds to minimize these marks, part production slows and tool life can be unreliable.
For tibial trays, Seco offers tool ranges that provide excellent performance. A tool designed specifically for side finishing can minimize feed marks from peripheral finishing. To reduce costs, a combination tool pairs the JH710 series with mechanized edge processing (MEP) to help eliminate burrs. The JH770 series provides good general finishing tools.
Tooling manufacturers must offer a full range of long-lasting, high-quality tools. With an understanding of industry challenges, a tooling manufacturer can help customers optimize production and increase output quality as well as volume.
Tibial trays begin as forged, cast or solid cobalt chrome or titanium. Throughout production, manufacturers want to produce perfect surface finishes, conform to exacting specifications for geometry and topography, and minimize secondary processing. Beyond perfect parts, the goals of production include increasing output and minimizing costs as much as possible, both in response to customer pressures. Of course, the ultimate challenge to cost containment comes in the form of scrapped parts, so manufacturers must attempt to avoid any step or process that does not contribute directly to the ideal production outcome.
This production phase requires low-cost, reliable, dependable processing that can run with minimal intervention. Successful roughing sets up subsequent processes for equal success, and tooling must match up with the workpiece. Although many manufacturers specify cobalt chrome knee replacement implants for cost containment, increasingly titanium is the material of choice for a tibial tray. The riser feature on this part is left over from the casting process and can vary hugely depending on their processing ready for use. Ensuring a reliable process which can accommodate height and material variances is key to success. Gate roughing is also another feature which demands reliability and the tools used for this step will ultimately determine how successful the following processes are and the impact on cost per part.
For dynamic milling, the JH770 roughing tool series with four flutes matches well with the task of processing tibial trays from solid material. The five or six-flute versions of this tool series enable manufacturers to apply optimized roughing to the near net shapes of forged or cast workpieces. In addition, the helix, rake, angular relief and short flute lengths of the JH770 series combine to produce a strong roughing tool that handles slotting, side roughing and dynamic milling techniques, all of which contribute to the roughing process for this component of the complete knee assembly.
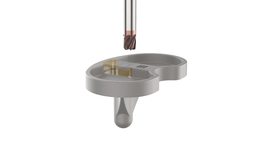
Tibial Tray - Tibial Gate Roughing
Tibial Tray - Riser
Because of the importance of surface finish perfection, it's essential to minimize tool path marks that can require sand blasting and manual polishing to remove. Minimizing these secondary processes helps increase part output and reduce cost per part. Polishing with fiber tools raises manufacturing costs and increases production time.
Surface finish and topography must remain at high-quality levels on the tibial tray component because both are essential to proper function of the knee assembly. The part must conform exactly to all design specifications.
The JH740 series machines cobalt chrome and titanium effectively. Its large frontal wiper geometry features superior tool life, helps produce proper surface topography and minimizes tool path marks that otherwise require secondary polishing. Adding the JH710 on the inner walls and outer surfaces of the tibial tray, peripheral finishing gives the part an excellent surface finish that conforms to specified tolerances. In combination the JH710 and JH740 series' ensure customers who require all part surfaces be free of tool path marks can eliminate the need for manual polishing altogether, cutting production time and cost.
Tibial Tray - Tray Wall Finishing
Tibial Tray - Floor Finishing
The locking mechanism feature is hugely important due to the security required to lock the bearing insert into the tibial tray. The bearing insert absorbs all the patient’s weight and needs to remain securely connected to the tibial implant. A common method to connect these two components is to produce male and female locking areas on the implant by way of a t-slot. The JH790 is designed to produce this feature balancing out the cutting forces without impacting and subsequently ruining any other surfaces of the implant. It's designed with common dimensions to accommodate standard industry widths and depths typically found in a tibial tray implant.
Tibial Tray - Locking Mechanism
Medical implants and in particular tibial trays have to be manufactured with no sharp edges this is crucial for aesthetics and patient and surgeon safety. To complete the finishing of the tibial tray our solutions include the JS509 (90°) or JS506 (60°) chamfer tools and the concave radius V31 families.
Implant features as unique as you are? The medical industry doesn't apply typical corner radii or have an adhered to standard like you would find in Aerospace for example meaning the standard offer might not quite suit your component. We can accommodate changes to diameters or corner radii on standard tools in the range easily by building your tool on MyDesign. The medical series of tools are all available and it is just a case of requesting your tool with an answer and drawing in seconds.
For those slightly more challenging requests we have a team of tool experts who can apply the trusted features the medical series demonstrate but combine with other innovations such as offering a JH710 wall finishing design with a MEP deburring top-edge geometry thereby combining two tools into one and releasing all the productivity benefits this combination provides. Another example might be adjusting JH790 t-slot cutter geometry to accommodate a dovetail shape. We can even combine a JH790 t-slot or dovetail with the floor wiper JH740 for unrivalled surface finish even in those hard-to-reach areas on the implant reducing the need for costly manual polishing.
Amortize your setup costs and lower your cost per tool with the Seco Tools Global Reconditioning service.
Manage your tools effectively and avoid wasting material while increasing your corporate sustainability footprint.
Seco Tools will recondition your tools to the original quality and close to new performance. With a good tool maintenance program and process controls, you can expect 2-3 regrinds. By applying Seco reconditioning tool cost savings per component can be as high as 40%.
Few production tasks truly represent one-of-a-kind challenges for medical device manufacturers, and the tibial tray is no exception. To help manufacturers optimize their production processes and attain both the output and the finish quality levels that their customers demand, Seco offers the benefits of our long experience in dealing with medical implants, including these complex knee assembly components.
You expect Seco to offer you more than great cutting tools. We provide a broad roster of services to support your productivity.
We offer custom products, tool reconditioning and recycling, targeted learning opportunities and services to help you improve efficiency. Everything we do upholds sustainable machining practices.
Contact Seco today to find out how we support every aspect of your production with so much more than tools.
Contact our experts here