Solid Support for Additive Manufacturing
Manufacturers can rely on Seco for expert advice based on extensive experience with Additive Manufacturing. Innovative research and tool designs support customers who want to optimize their use of AM.Additive manufacturing offers unparalleled design freedom, material efficiency and production flexibility that revolutionize various industries. The technology continues to evolve and plays an increasingly important role in manufacturing, enabling new possibilities for innovation and efficiency. However, the incorporation of additive or 3D metal printing processes into production operations requires planning and expertise.
Most shops will consider incorporating AM to generate a component initially machine from solid material or produced via casting. To ensure the process truly adds cost effectiveness, Seco advises manufacturers to expand their thinking when they produce parts with AM.
Upstream and downstream processes such as secondary machining or finishing operations must benefit from AM. If 3D metal printing will reduce costs for those operations as well, then it is worth the investment even if the process might not save time in the actual part production/build stage.
Instead of trying to replace all its conventional machining with AM, a shop should blend 3D metal printing in with those processes. AM also allows for the generation of 3D metal printed features onto machined parts. Melding the two processes helps optimize overall part production.
Part tolerances influence the use of AM. Manufacturers must realize that the process behaves differently in terms of the tolerances it can hold. 3D metal printing typically achieves tolerances in the ±0.25mm range, so if a part requires tolerances tighter than that, conventional subtractive processes need to be considered.
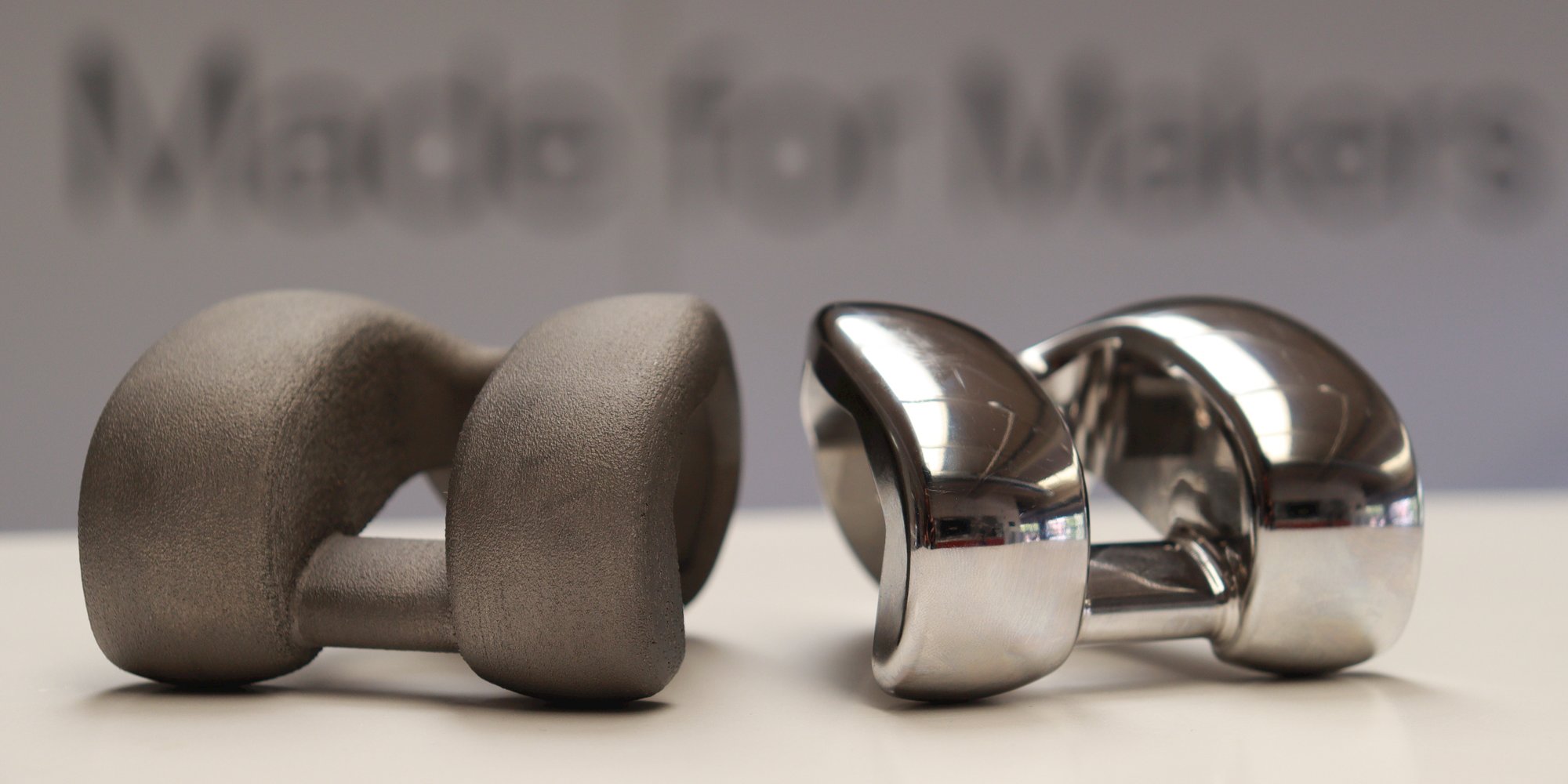
With these tolerances in mind, additive manufacturers need to rethink the process instead of replicating how a part was produced previously. This is especially true when building parts or adding features that will not be machined. For example, medical implant manufacturers use 3D metal printing to create free-form surface features and textures that are either impossible to machine or that must not be machined to avoid contamination with chips and coolant. In these instances, AM’s achievable tolerance capability definitely factor into the equation.
CAD/CAM packages need specific capabilities for 3D metal printing. Additive manufacturers must have the ability to design complex 3D metal printed parts, perform feature-based programming and create programs for secondary machining operations. CAM also benefits from full simulation capability as well as built-in probing and machine verification.
Near-net part shapes created with AM may pose problems in terms of fixturing for secondary subtractive machining operations. AM parts use less material, so if secondary machining is needed, the 3D metal printed part will most likely be less stable and offer fewer areas for clamping in secondary finishing operations.
To overcome this, additive engineers design parts with workholding in mind and include tabs or other features specifically to secure 3D metal printed parts during secondary machining operations. These engineers also take additive engineering a step further and generate more efficient part designs. For instance, these designs would involve less material, include added support features only where necessary and/or reduce the amount of secondary subtractive machining operations.
Part probing takes on a more critical role in AM. Once a 3D metal printed part is produced and needs secondary machining processes, probing allows additive manufacturers to determine the locations of surfaces and features on a near-net shaped part. However, such probing capability often requires the use of a multi-axis machine tool to access all those shapes and features with the probe.
Obviously additive manufacturing (AM) requires specialized resources. Manufacturers often look to their own R&D departments for the incorporation of additive manufacturing, but it requires time and resources that are beyond that department’s scope.
In these instances, strategic partnerships with suppliers who have extensive experience in additive engineering are critical when incorporating 3D metal printing into part processing operations. For optimal solutions and techniques, Seco knows AM technology and its impact – and how to maximize process results.
The company is well versed in both additive and subtractive manufacturing processes. This experience stems from the fact that for a long time, Seco has used 3D metal printing extensively in its own production operations.
Additive manufacturers can take advantage of insights, workflow configuration, application resources and tooling from Seco. Research in the company’s Innovation Hubs and among its R&D teams has produced a range of finishing tools designed with additive machining in mind, while the company’s Engineering Services help eliminate problems to ensure additive manufacturing success.
The Engineering team will define the 3D metal printing process and its required CAM programming for increased productivity. For optimized cycle times, the team centers its process around the additive manufacturing application and feature-based methods. During the process, the team determines exactly how 3D metal printing will provide manufacturers a competitive advantage and will guide them along a path to efficiency and maximized results.
Through its Innovation Hubs, Seco creates a collaborative environment that brings in industry partners to design and develop best-in-class machining processes and tooling innovations. Simultaneously, the company continues its commitment to technical training and education through its Seco Technical Education Program (STEP), both for employees and for customers.
The Seco R&D department continuously improves the use of AM technology for the development and manufacture of new and existing products. The company always looks for ways to improve its products and make the best use of AM technology.
Because Seco is well entrenched in the current additive manufacturing market, the company knows how to support customers and solve their AM problems. Typically, Seco gets involved at the new product integration (NPI) level/stage. The customer supplies a print of a part that was most likely produced from solid material. This is an ideal time to seek out advice from Seco on how and where to implement AM.
Seco consults with a customer’s designers to determine the best use of AM and where it will improve part production, both in upstream and downstream processes. Those manufacturers considering the incorporation of additive manufacturing should reach out to Seco who can help them understand part yields, volumes and cycle times, validation methods, inspection, consumable costs, and designs for manufacturing.
Looking for advice from our side?
Contact Us
Inline Content - Survey
Current code - 5fce8e61489f3034e74adc64