Bearing Inserts
Learn to optimize medical-implant production, cut costs and create high-quality surface finishes with tools that match your material and parts.The sophistication of today's complete knee assemblies increases the complexity of medical device manufacturing. Now that digital scans can capture the precise structural configuration of a patient's knee and 3D printing can replicate it in a knee assembly, some implants become one-off parts produced through high-mix, low-volume output, although mass production remains typical.
Within the complete knee assembly, three components pose different sets of manufacturing challenges, including the ultra-high molecular weight polyethylene (UHMWPE) plastic bearing insert. Its soft surfaces require ideal topography and surface finishes of Ra 0.2-0.4 to make the knee assembly truly functional. The bearing insert must match the contours of two metal parts with high precision.
Manufacturers can cut cycle times and boost quality with tools that optimize production and withstand long stretches of unattended machining. For the bearing insert, Seco offers the Premier Finish carbide cutter, which reduces cycle times from 20-50 minutes to 10-15 seconds. Unlike ball nose end mills, this reconditionable custom tool finishes a bearing insert in a single pass.
Ideally, tooling manufacturers draw on knowledge of their customers' industries to produce and recommend the ideal tools for each process. This service helps customers optimize production, increase quality and boost output. As a trusted adviser and partner, the tooling manufacturer demonstrates the value of choosing the right supplier.
In a complete knee assembly, the bearing insert cushions opposing metal parts, simulating the function of cartilage in the natural knee joint. Made from ultra-high molecular weight polyethylene (UHMWPE) plastic, the bearing insert acts as a shock absorber for weight-bearing stress and eliminates metal-on-metal contact. The part must mate perfectly with the flat surface of the tibial tray and the complex curves of the femoral condyles, with surface precision between Ra 0.2-0.4.
Constant customer pressures force manufacturers to increase output and reduce per-part costs, particularly through unattended production. Successful lights-out manufacturing depends on the ability to maintain the shortest-possible cycle times and minimize or eliminate secondary processes. At the same time, the process must reach the specified standards for geometry and surface finish.
The top surface of the bearing insert matches the double-dish shape of the femoral condyles. Surface quality requirements increase the complexity of this part. Successful machining of the condyle surfaces of a bearing insert depends on chatter-free cuts for reliable, uninterrupted operations. Production optimization must reduce bottlenecks, improve surface finishes, eliminate burrs, and minimize manual secondary processes. Above all, manufacturers seek to eliminate the prospect of scrapped parts.
A custom tool offers the optimal choices for this production task. Low-stepover scans of the surface of a bearing insert with a ball nose end mill – such as the JH450 series – can provide excellent results, but can yield cycle times of 20-50 minutes. Instead, manufacturers can opt for the Premier Finish solid-carbide condyle tool. This ultra-sharp form cutter can reduce cycle times to 10-15 seconds. For small features and finishing, the J93/J99 series of uncoated sharp end mills offer excellent performance.
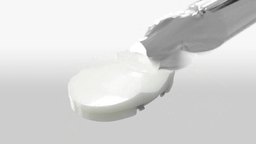
The Premier Finish carbide cutter produces ideal surface finishes at high production speed, meeting manufacturers' needs for output volume and part quality. Because this tool is reconditionable, manufacturers can amortize costs further.
Ideally, a tool supplier offers more than just great tools with long tool life. Throughout years of experience, Seco has amassed a large volume of expertise that refines the approach to medical implant manufacturing. We help our customers optimize their production processes, reduce cycle times and achieve the surface finishes they need.
Contact our experts here