5 Additive Manufacturing Trends Enhancing Production and Tooling
Additive manufacturing enhances many aspects of workpiece and tooling production. 5 trends show how it can revolutionize the manufacturing industry.Additive manufacturing (AM) has advanced exponentially from its origins as a clever technology with limited practical applications on the production floor. Today, nearly 10 versions of AM exist, each useful in different ways. AM can repair aerospace parts, produce individualized medical implants, create fixturing and workholding solutions, and improve tool production, especially in the development of customized solutions. As capabilities increase and costs drop, even smaller shops can find many ways to make use of 3D metal printing.
AM is revolutionizing the production of medical implants and devices. Some smaller implants, such as those used in dentistry, may function properly as standardized forms/products. Larger orthopedic implants such as hip and knee prosthetics work better when they fit the individual patient more precisely. Pre-surgical scans provide the data to produce individualized implants with 3D metal printing. The customizable nature of 3D printed parts also makes them ideal for creation of medical and surgical tools.
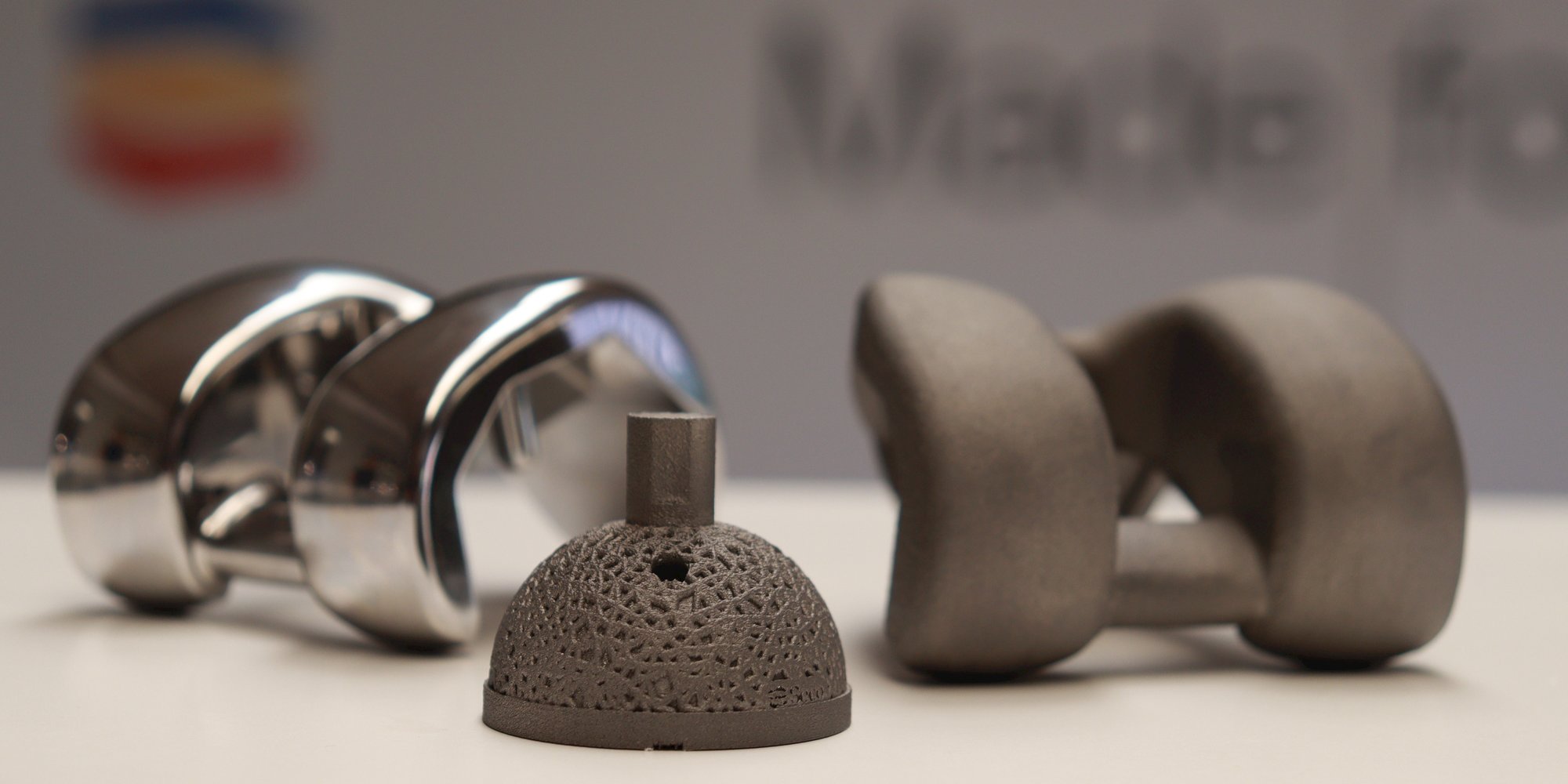
Additionally, 3D printing makes it easy to fabricate medical implants from titanium, which the human body easily fuses into bone through osseointegration. Unlike cobalt-chromium alloys, titanium does not tolerate grinding operations. But AM enables the creation of lightweight, strong titanium implants that match the patient's anatomy.
Medical implants must be free of contaminants to function correctly inside the human body. Printed medical parts limit exposure to coolant and chip residue during manufacturing. AM parts require little machining after they are printed, but shops can and must control polishing operations tightly. Automated polishing of AM parts reduces cycle times and component costs compared to manual operations, which apply the same finish all over the part. Automation enables manufacturers to match specifications with different finishing standards on different areas of a part.
Shops that do not produce medical products may look to 3D printing initially for fixtures and workholding. They may fabricate some of these devices from highly dense plastic to fixture workpieces on a coordinate measuring machine (CMM). This approach can provide a cost-sensitive, vertically integrated alternative to purchasing metal fixtures and waiting for them to arrive.
Other shops integrate additive manufacturing as a supplementary process in tandem with subtractive machining. This enables them to add features onto machined workpieces without sending parts out to other vendors. Shops that make aerospace parts already use weld additive manufacturing to repair large, irregularly shaped high-value parts.
Along with all of AM's obvious advantages, it also presents some disadvantages. Some workpieces cost more to produce through AM than through subtractive machining. Where price is a primary consideration, AM may not be the ideal choice. Although AM easily creates many otherwise "impossible" part shapes, some features require supports that make production more complex.
As manufacturers have begun to find innovative ways to use additive manufacturing for production work, however, five trends lead AM into new applications and showcase its strengths.
Toolmakers look to additive manufacturing to add through coolant with better results than machining can achieve.
The machined technique produces a sharp edge that forces coolant to swirl rather than form a forceful stream.
The two-hole approach to coolant channels is unnecessary with 3D metal printing.
Tools built through additive manufacturing incorporate a single coolant channel, a structure that machining cannot produce.
Printed channels direct coolant to the cutting edge efficiently and reach areas that otherwise would escape the flow.
Coolant channels aren't the only tooling and part features that benefit from additive manufacturing. Some of these features are easier to build with 3D metal printing than through machining. Others simply can't be produced with subtractive techniques.
AM simplifies the production of complex molds, including interior cavities that machining can't reach. Honeycomb structures replace solid metal for lightweight strength. AM can build the support structures for a tool in the same process that builds the tool itself. Like many other 3D-printed items, these supports need not be solid, so they require less material.
AM also helps make manufacturing sustainable. Additive processes don't create piles of chips to recycle, and any residual metal powder is either reusable or recyclable. Printed tools typically weigh less than their machined equivalents, which enables shops to use less energy to make parts.
Future developments will make even further use of CAD/CAM capabilities in additive manufacturing. Eventually, toolmakers should be able to program in the parameters of a part and generate the tool to produce those features. Even today, additive manufacturing can help manufacturers determine whether they can produce a specific part – and define the customized tooling their job will require. AM production requires only a small amount of machining to transition from near-net shape to finished configuration.
Traditional manufacturing of customized tools can require up to eight weeks, including iterative design to optimize shape, strength, and features. AM can reduce that time to two weeks or less. On one build plate, 3D metal printing can produce four individual nested items in one eight-hour cycle. In some cases, tool designs require the combination of AM and sintering – and the results function just as well as subtractively milled tools.
Learn more about the benefits and challenges of additive manufacturing on our latest ebook
Additive manufacturing can generate near-net shapes that come extremely close to final part dimensions. Finish passes on these workpieces require exacting fixtures and highly accurate machining. Accurate probing and best-fit alignment also are essential to proper results. Compared to milled parts, 3D printed workpieces have less tolerance for slight variations in shape. This makes attention to detail even more important in production, finishing and inspection.
With that said additive manufacturing holds enormous promise for workpiece and tool production. It creates better options for coolant flow than machining can produce.
It excels at building complex shapes. AM accommodates high-value materials that don't tolerate some subtractive techniques, reduces chip volumes, and enhances sustainability. Its capabilities have begun to revolutionize tool design and customization.
But success in manufacturing often relies on more than technology. Optimal solutions and techniques benefit from strategic partnerships.
With deep experience in additive manufacturing, Seco knows AM technology and its impact – and how to achieve optimal results with it. As our customers grapple with its potential, we understand how they strive to implement it and how to make it work for them. With many decades of manufacturing expertise, we're ready to take additive manufacturing into the future and help apply its strengths.
Inline Content - Survey
Current code - 5fce8e61489f3034e74adc64