‘No longer just a buzzword’: How 3D Printing is Making its Mark in Medical
Additive Manufacturing isn’t a buzzword anymore: it’s standard practice. Discover the drivers of 3D printing in the medical segment.In less than a decade, Additive Manufacturing (AM) has gone from a hot topic at medical industry conferences to the production line. Leading orthopedic manufacturers now use 3D metal printing to produce hundreds of thousands of prosthetic hips annually, enabling complex shapes previously impossible to create.
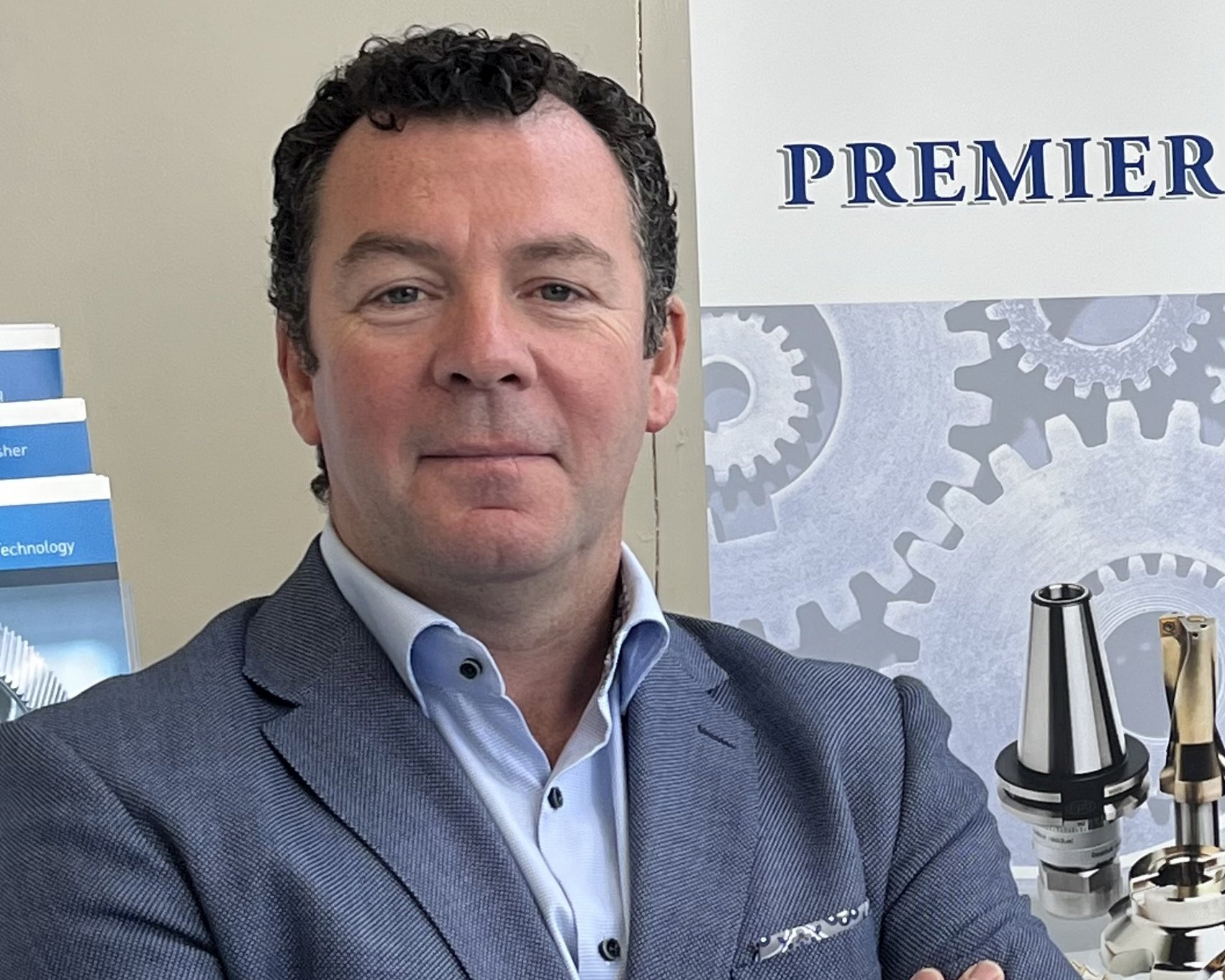
Others are producing tailor-made replacement bones for victims of serious accidents or bone cancer. Even producers that use traditional techniques for actual manufacture are using AM to accelerate product development.
"Ten years ago, we were talking about this, five years ago we were playing with it, but now we're using it for mass production," said Ciaran Dillane, the Managing Director of Premier Machine Tools, a Seco subsidiary that is a major supplier to Ireland's medical industry.
"I don't think it's a buzzword anymore: it's standard practice."
The main technique being used for 3D metal printing in the medical industry is Laser Powder Bed Fusion (LPBF), where layers of metal powder just microns thick are brushed over the growing component on a bed and fused using lasers.
3D metal printing is becoming the orthopedic industry's standard method for manufacturing replacement components for joints like hips, knees, and shoulders, or meshes to repair skull damage, as it allows the production of complex sponge or lattice structures impossible with traditional forging or milling.
The lattice is placed where the titanium meets the bone, which then finds its way through the lattice and stops growing when it hits a hard surface. This 'bone ingrowth' technique creates a better bond between bone and component than the former 'bone ongrowth' technique and removes the need for bone cement, reducing the risk of infection.
"All of the orthopedic manufacturers have their own versions of this technology, and it has scaled hugely over the past five years," Dillane said.
Most use titanium powder, which has an elasticity similar to bone and, unlike chromium or alloys including iron, is fully biocompatible. Seco's owner Sandvik offers more than 2,000 metal powders, of which a growing number – close to 50 at present – are for additive manufacturing.
Additive manufacturing is also starting to be used for spinal implants, where 3D metal printed titanium is replacing polymer for spinal cages. It is used to make specialized surgical instruments, which are tailored for a particular patient or operation.
"I think dental is shifting a lot more quickly: it has smaller components, which are not as critical with tolerances," explained Andrew Fielding, Global Business Development Manager (Medical) at Seco. "It'll be at 50-60 percent [of the market] in the next couple of years."
According to Ingemar Bite, R&D Manager for Seco's Additive Manufacturing department, in all these cases components need to be machined after they have been printed, both to reach their exact final shape and to achieve the right surface finish.
"Directly after the process, we have a surface full of natural porosity, which is why we need to machine all surfaces that are either subjected to high tensile stresses or have requirements on geometrical tolerances or surface finish," he explained.
This means that even at the computer-aided-design stage, the shape of the component needs to be drawn up with machining in mind, for which manufacturers can benefit from the expert help Seco can provide.
At Seco's facility in Fagersta, 175km northwest of Stockholm, Sweden, Bite's team have been researching additive engineering since Seco acquired its first LPBF machine in 2018.
"So far, it's been in development, with evaluation and field tests, both at our customers and internally. Now we feel that the process is so stable, and we have enough knowledge to start going out to customers with this technology," Bite said.
The company had worked with AM earlier, however, collaborating with the Additive Manufacturing Centre in Sandviken on its first AM product – a coolant clamp.
This clamp, which has been available to customers since 2017, can direct coolant to a specific part of the cutting edge through a curved channel impossible with conventionally machined tools.
Earlier this year, Seco moved both AM production and R&D into the facility rebuilt for its needs in the beginning of this year.
“This is a big advantage for us, as I see it: there is still a lot to learn and evaluate with AM and having both R&D and production working close to each other under the same roof gives a lot of benefits.” Bite said. “It also gives us increased flexibility with equipment and better control over the process.”
Seco aims to use AM to produce custom tools for traditional machining, particularly where the customer needs a better solution that can be achieved only with this method.
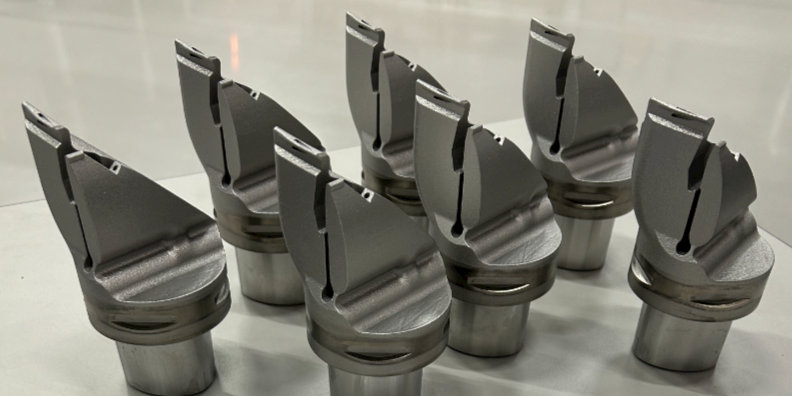
The company is also developing hybrid tools where the front-end of the tool, featuring a unique pocket, feature, or coolant outlet, is 3D-printed directly onto a conventionally machined back-end.
This allows Seco to use inserts and/or other tools in very challenging applications, bringing access to a feature or making it possible to machine materials that would otherwise be very difficult.
AM tools have other advantages. As much as 20 percent of total weight can in most cases be removed without affecting performance of the tool. 3D-printing onto a conventionally machined back-end can reduce production time.
Reduced weight can also improve tool performance, particularly in cases where the tool has long overhangs, where lower weight tool can increase the effect of passive dynamic damping in the bar.
While some manufacturers are using the technique for serial production, it really comes into its own when customization is required, with implants, prosthetics, and surgical guides design based on patient-specific anatomical data.
Dillane expects this to become the standard practice for producing components for victims of serious accidents or bone cancer. "They'll do a CT scan of you in the hospital, they'll understand what state your bone is in, and then they will send that to one of the orthopedic manufacturers in the form of a scan. They will reverse engineer it overnight and they'll put it on a 3D printer and print it within 24 hours. And you will probably walk out of the hospital in 36 to 48 hours." This rapid turnaround time, which patients are used to when getting dental implants, will cut the amount of time patients have to wait in hospital for prosthetics.
In other industries, a short turnaround time can speed up product development. Seco recently managed to help one global orthopedic manufacturer to go from the first designs to a fully machined femoral component in just six weeks. Even though the final component will be forged and milled in a traditional way, using additive manufacturing to build prototypes cut the development time by more than half.
In the coming decade, additive manufacturing seems certain to overtake traditional techniques in the orthopedic and dental segments, with bespoke parts tailored to individual patients becoming more common, and turnaround times ever faster. The technique is also likely to enable new, more complex mechanical components, such as spinal cages and artificial knees for children that can grow as they do, and also to enable easier chip embedment. Finally, new machines are emerging that can alternate between additive manufacturing and traditional milling techniques.
"We don't talk about machining anymore. We talk about component shaping," Dillane explained. "Because for us, additive manufacturing and subtractive manufacturing are joined at the hip."
Interested in learning more about the benefits and challenges of additive manufacturing in the medical segment?
Find more answers in our latest e-book!
Inline Content - Survey
Current code - 5fce8e61489f3034e74adc64