From Concept to Creation: How Additive Manufacturing is Shaping Machining
Explore how additive manufacturing is transforming the machining industry by enhancing efficiency, reducing costs, and enabling innovative designs across various sectors.Traditional manufacturing methods, while tried and tested, often encounter hurdles in meeting the demands of modern workpiece production.
Production managers, in particular, grapple with the complexities of producing parts with intricate geometries, which can lead to extended lead times, increased tooling costs, and higher scrap rates. For application engineers, the limitations of subtractive manufacturing can hinder their ability to fully realize innovative designs. The constraints imposed by machining processes often require design compromises, limiting product performance and functionality.
That is where additive manufacturing (AM) comes to the stage. AM, often referred to as 3D printing, is a process where a three-dimensional object is created by successively adding material layer upon layer. This method is opposed to the traditional manufacturing ones that involve removing material from a larger block to create the desired shape.
Once a niche technology, AM is now gaining traction across various sectors, from aerospace and automotive to healthcare and tooling. Its potential to create complex geometries and optimize material usage has captured the attention of manufacturers worldwide, resolving challenges across various industries:
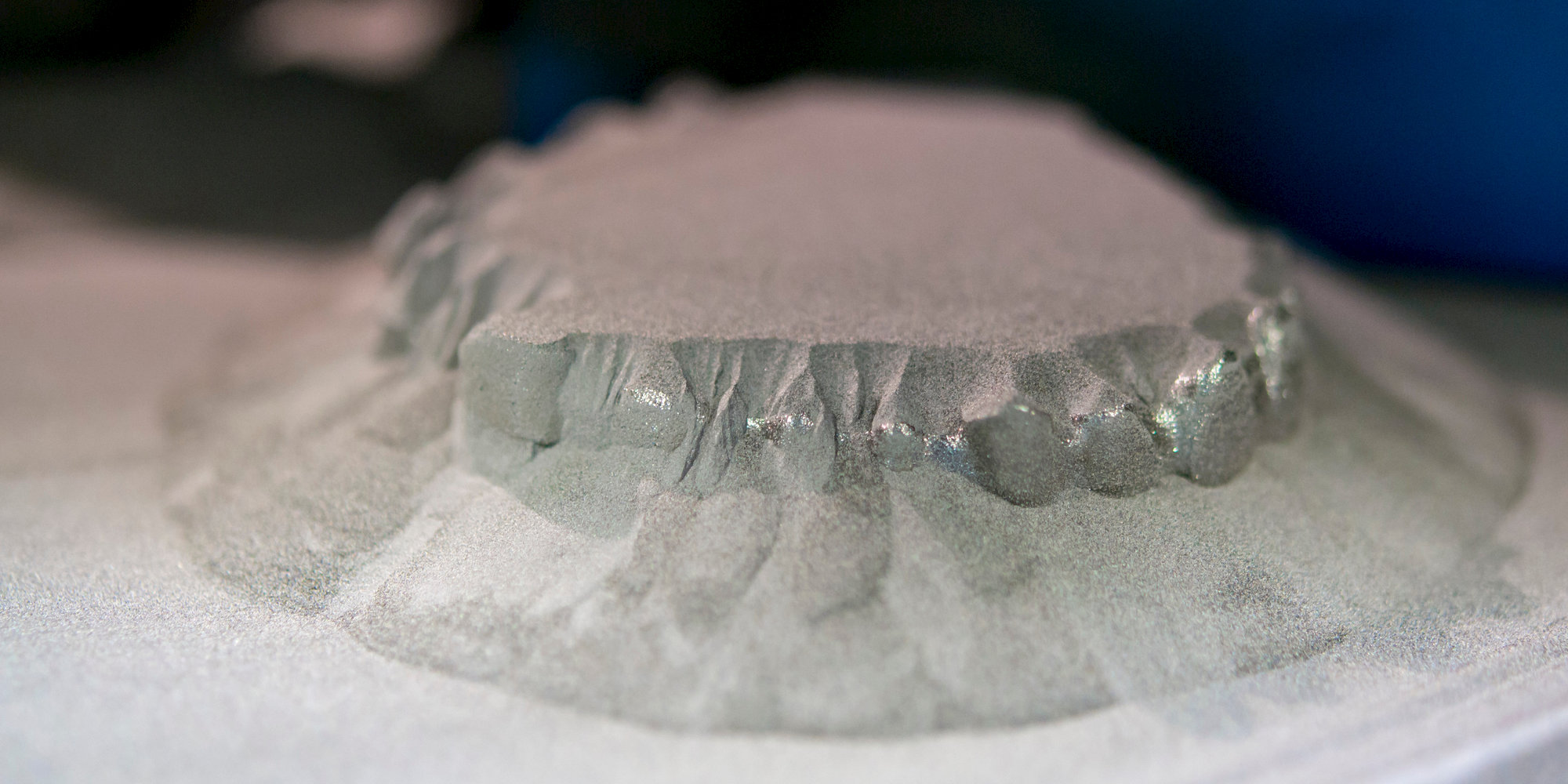
For example
In the automotive industry: Producing components with complex internal channels for cooling or structural reinforcement can be extremely time-consuming and expensive using traditional methods. This not only impacts production costs but also delays time-to-market. For instance, a study by McKinsey & Company found that tooling-related issues can account for up to 40% of production delays in the automotive industry, hindering time-to-market and reducing overall profitability.
- In the aerospace industry: Creating lightweight yet structurally sound components with intricate lattice structures or internal coolant channels is often impractical with traditional manufacturing. This restricts design optimization and increases production time. A study by NASA found that additive manufacturing could reduce the weight of aircraft components by up to 40%, leading to significant fuel savings. The RAMPT project at NASA’s Marshall Space Flight Center has delivered composite materials demonstrating a 40% weight savings over conventional bimetallic combustion chambers.
Inline Content - Gridded Links
Tags: 'blog_aerospace_material_of_the_future'
Max links: 1
- In the medical segment: Manufacturing customized implants or surgical tools with precise contours and porous surfaces for tissue integration is challenging and costly using conventional methods. This can limit care and increase procedure complexity. However, additive manufacturing can contribute to a more sustainable and environmentally friendly approach to manufacturing in the biomedical and healthcare sector.
Inline Content - Gridded Links
Tags: 'additive_manufacturing_five_trends'
Max links: 1
- In the general engineering sector: Producing complex tooling or molds with undercuts or complex coolant channels can be time-consuming and expensive. This impacts production efficiency and product quality. With AM, engineers are no longer restricted by machinability constraints and can explore new shapes and functionalities. This opens opportunities for lightweighting, increased strength, and improved performance.
AM offers a transformative approach to production, presenting numerous advantages over traditional methods. Its ability to create complex geometries with precision and without the constraints of tooling is a notable change for industries demanding intricate components. Nonetheless, this manufacturing method comes with its own set of challenges.
In the medical field, AM shines in producing overly complex parts with unique properties, such as porous implants for bone integration or components requiring internal structures. In aerospace, manufacturers can produce components with internal coolant channels or lattice structures, previously unattainable through conventional machining. However, these benefits come at a high cost, making it essential to evaluate the specific requirements of each project to determine if AM is the most suitable strategy.
While AM can deliver complex forms and customized solutions, build times can be longer compared to traditional methods, making it less suitable for high-volume applications. This trade-off between complexity and efficiency must be carefully considered to find the right balance between the requirements of your project and the capabilities of the method.
AM can work with a variety of materials, including polymers, metals, ceramics, foams, gels, and even biomaterials. However, the range is still limited compared to traditional manufacturing processes. Certain materials may not be suitable for AM due to their melting points, chemical properties, or physical characteristics. Additionally, the properties of the final product, such as its strength, durability, and surface finish, can be affected by the choice of material. While materials like Inconel, titanium, and cobalt chrome can offer desirable properties in specific cases, their cost can impact overall production expenses.
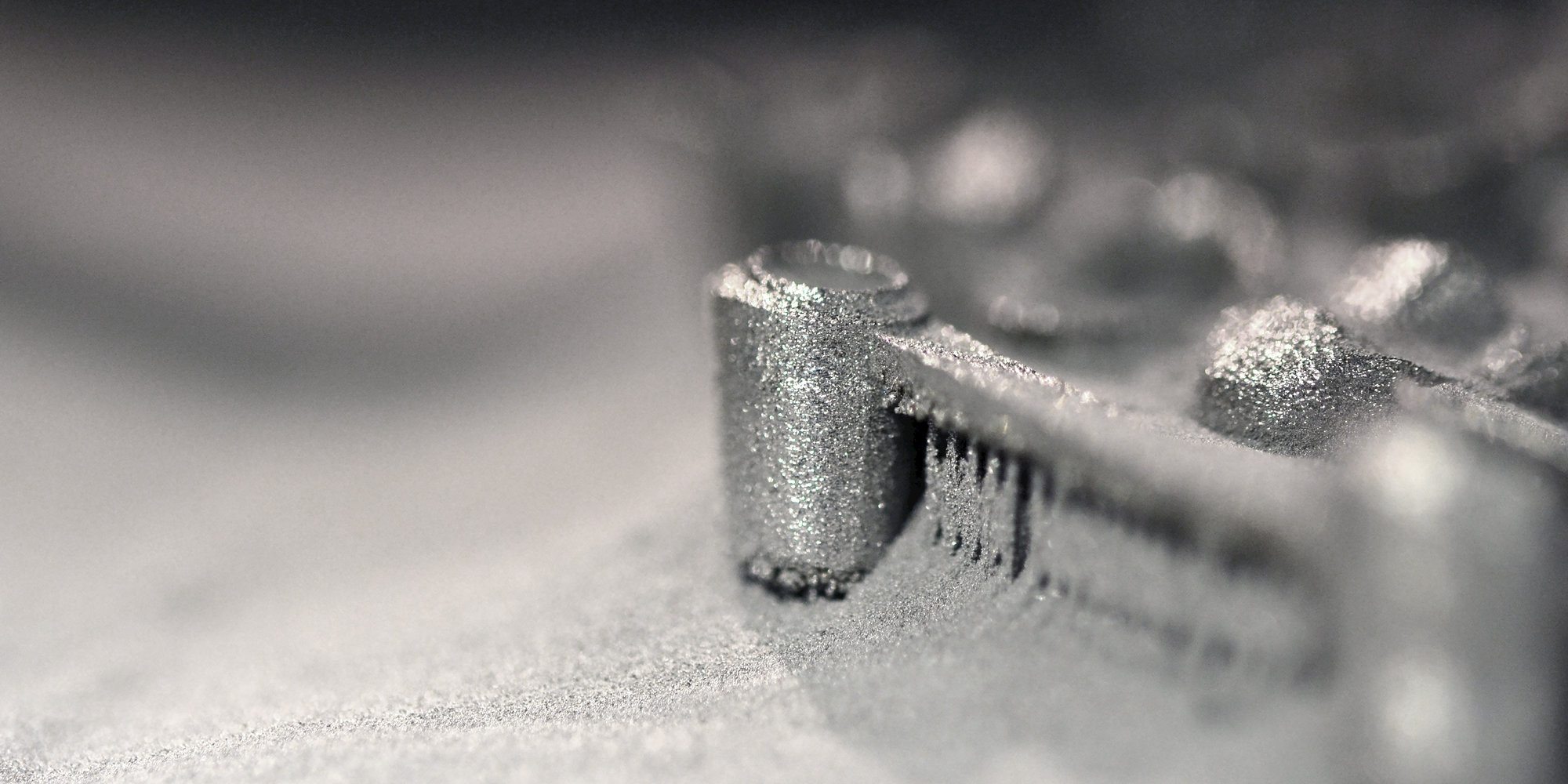
When considering the use of AM for a project, it’s important to assess several key factors:
- Design Complexity: AM enables the production of complex and intricate designs that may not be feasible with traditional manufacturing methods. If your project requires complex geometries, internal structures, or custom designs, AM could be a beneficial choice.
- Production Volume: AM is typically more cost-effective for low-volume production runs. This is because it doesn’t require the expensive tooling and setup that traditional manufacturing methods do. However, for high-volume production, traditional methods may be more efficient and cost-effective.
- Material Requirements: AM can utilize a wide range of materials, including plastics, metals, and ceramics. It’s important to consider the material requirements of your project, as not all materials may be suitable for additive manufacturing.
- Lead Time: While AM can speed up the prototyping process significantly, the build time can be longer than traditional methods, especially for high-volume applications.
- Cost Considerations: The initial investment in AM equipment could be high while the cost per unit is also generally higher than with traditional machining, particularly for high-volume production.
As Additive Manufacturing technology continues to advance and material science expands, we can expect to see even more groundbreaking applications and innovations.
Despite its promise, AM still faces challenges that need to be addressed for widespread adoption. Therefore, collaborations between manufacturers and suppliers like Seco will be essential to unlock the full potential of the additive manufacturing process.
We invite you to explore the possibilities of AM alongside Seco. By working together, we can unlock the full potential of this transformative technology and shape the future of manufacturing.
Ready to learn more? Contact us today to discuss your specific needs and explore how we can help you leverage the power of AM.
Contact Us
Inline Content - Survey
Current code - 5fce8e61489f3034e74adc64