Choosing the right Face Milling Cutter
Seco offers a wide range of face milling products for roughing, semi-finishing, and finishing, addressing diverse machining challenges.Face milling is one of the most common operations on each component. It can be performed with a wide range of different tools that are not necessarily dedicated face milling solutions. Cutters with a lead angle of 40° - 45° are most frequently used, but square shoulder, round and high feed mills are also used depending on the application conditions and demands.
Today, we offer a wide range of face milling products to meet roughing, semi-finishing and finishing needs and to overcome a variety of machining challenges. Face milling operations can be divided into 5 main usage areas:
Seco’s core general face milling range exists out of 5 systems. Each system holds inherent characteristics and strength to support certain applications and usage demand. The core range is supported by ISO insert shapes as SEKR and SPKR as well as additional niche systems for heavy duty machining and dedicated finishing solutions.
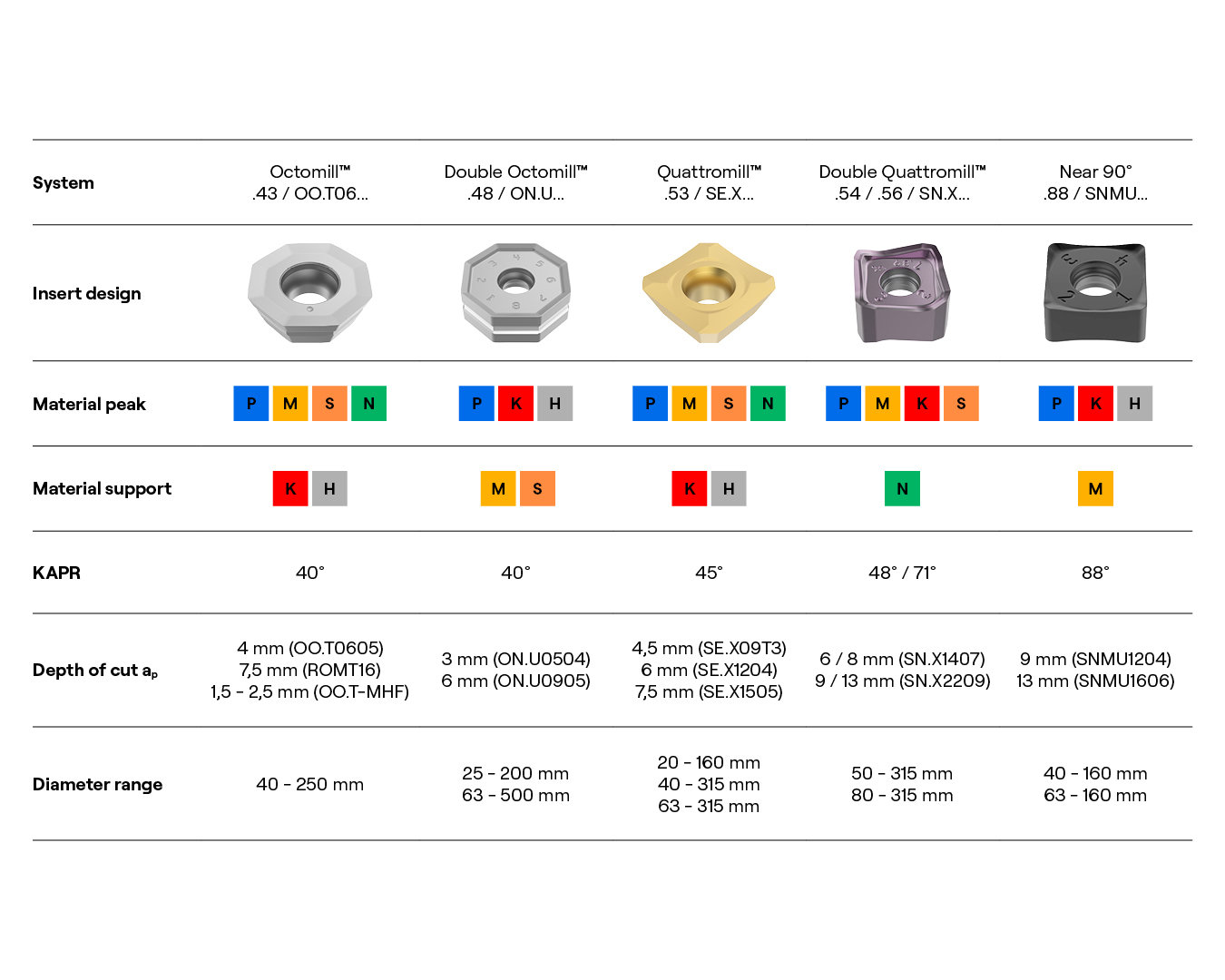
This information provides an overview of our face milling systems, highlighting the key characteristics of each item. This comparison offers initial guidance for selecting the optimal solution for your specific needs.
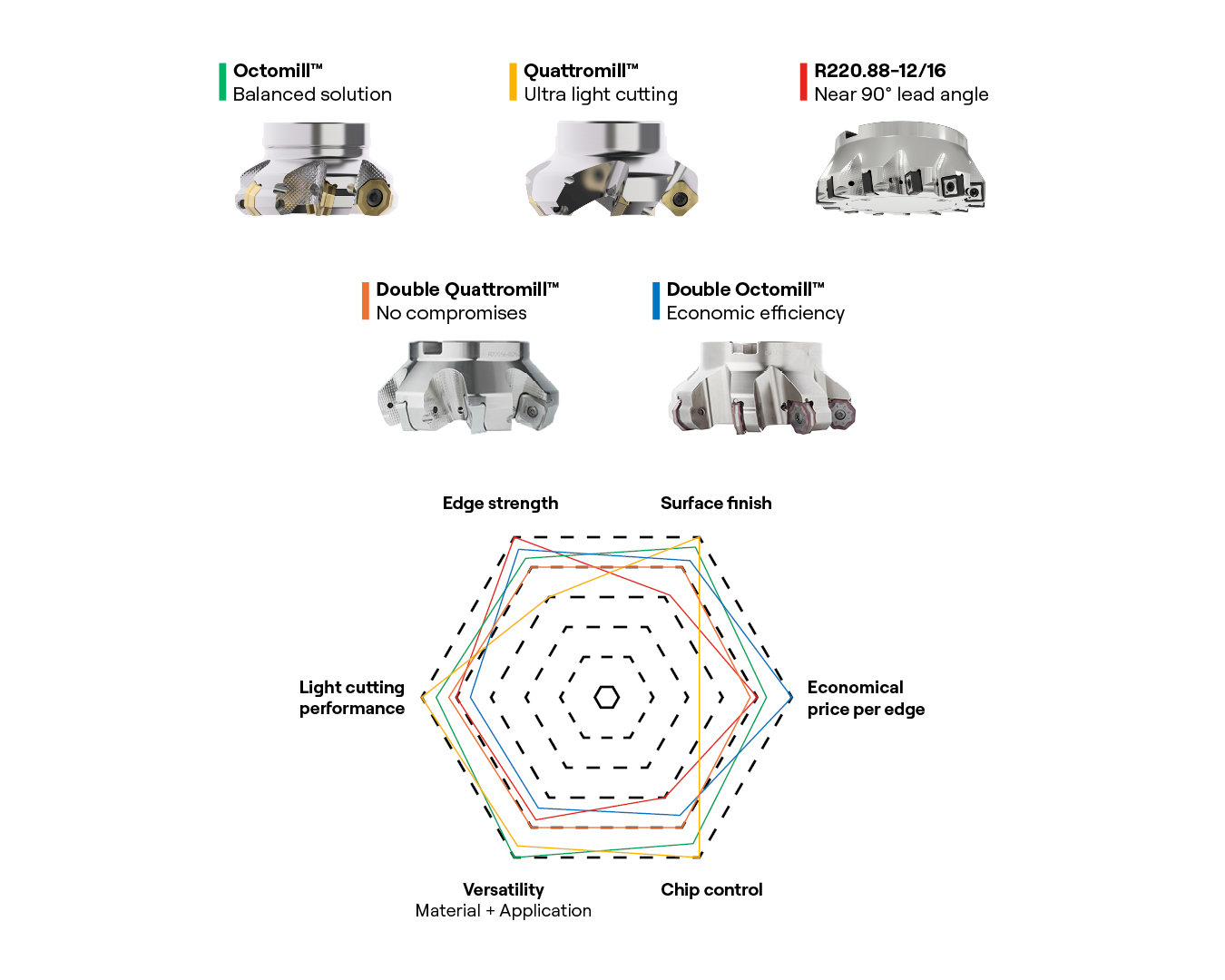
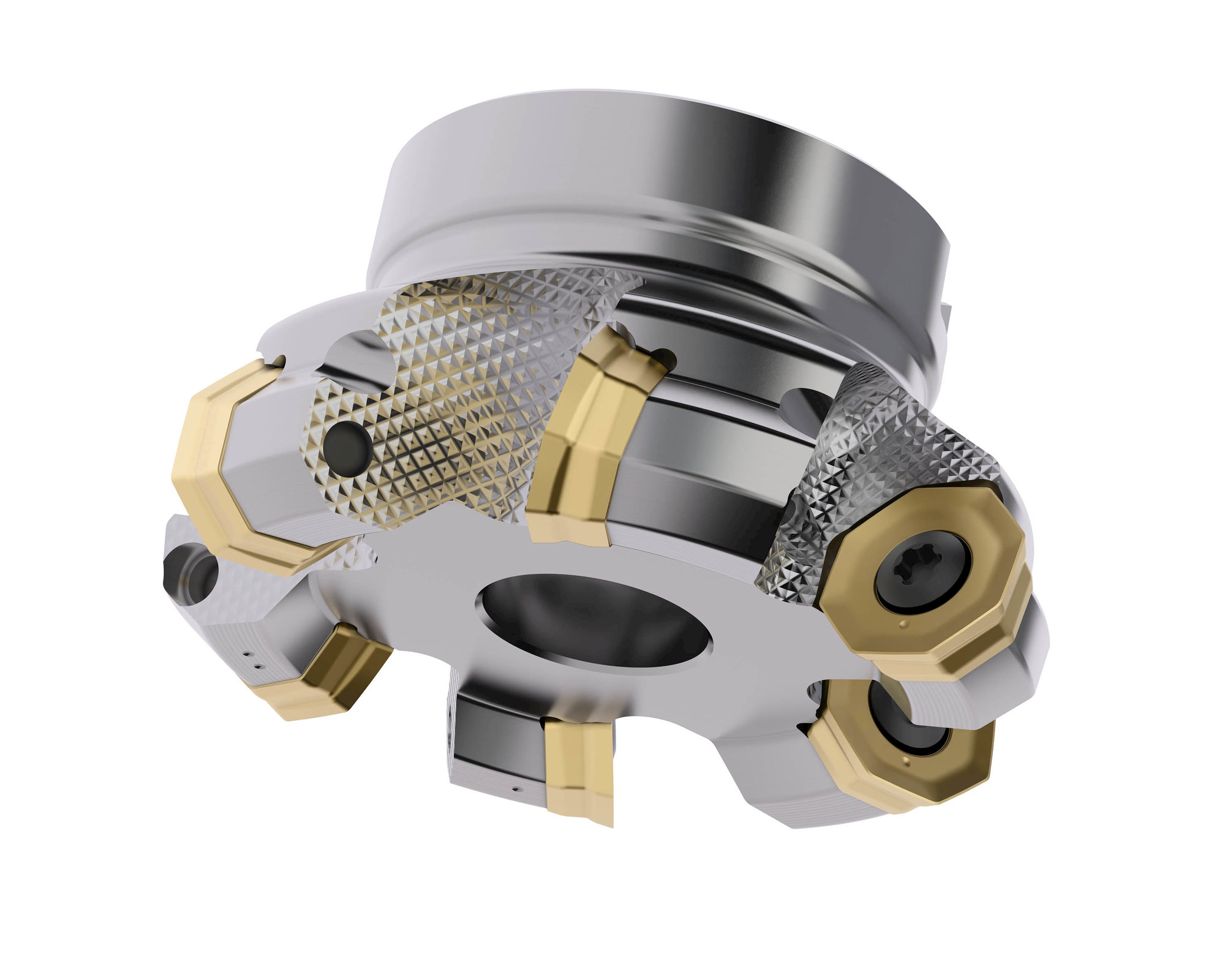
Octomill™ size 06 is a new generation and evolution of Seco’s Octomill™ size 05 and 07 building upon the strengths of previous generations. This innovative system combines the light cutting action and material versatility of OF.R/N/T inserts with the robust cutting edge and system stability of OD.T-style solutions.
A key advantage of Octomill™ size 06 is its unique cutter-insert interface. This design simplifies the handling of single-sided inserts, replicating the secure feel of a double-sided system. Octomill™ size 06 is more than just a face mill. The multi-insert pocket design accommodates three different insert types, including round 16 inserts and moderate high-feed options, providing exceptional flexibility and a broad working range.
Its superior runout and wiper flat alignment, coupled with balanced cutting forces, enhance finishing performance, even in challenging setups. This makes the new generation Octomill a valuable addition for demanding finishing applications, alongside Quattromill and Square 6.
Easy to choose / easy to use: your new 1st choice in face milling
Well-balanced solution between price-performance-ratio, light cut behavior and handling
High flexibility and versatility in various materials and applications
More than just a face mill thanks to the multi-insert pocket design for face, moderate feed and round 16 inserts
Easy and reliable insert handling particularly for single-sided solution
Superb system for finishing application
High performance in challenging materials as SMG M and S
Insert design protects the pocket seat in case of edge or insert breakage
Save cost through higher edge utilization based on unique insert cutter interface design
Go to the product
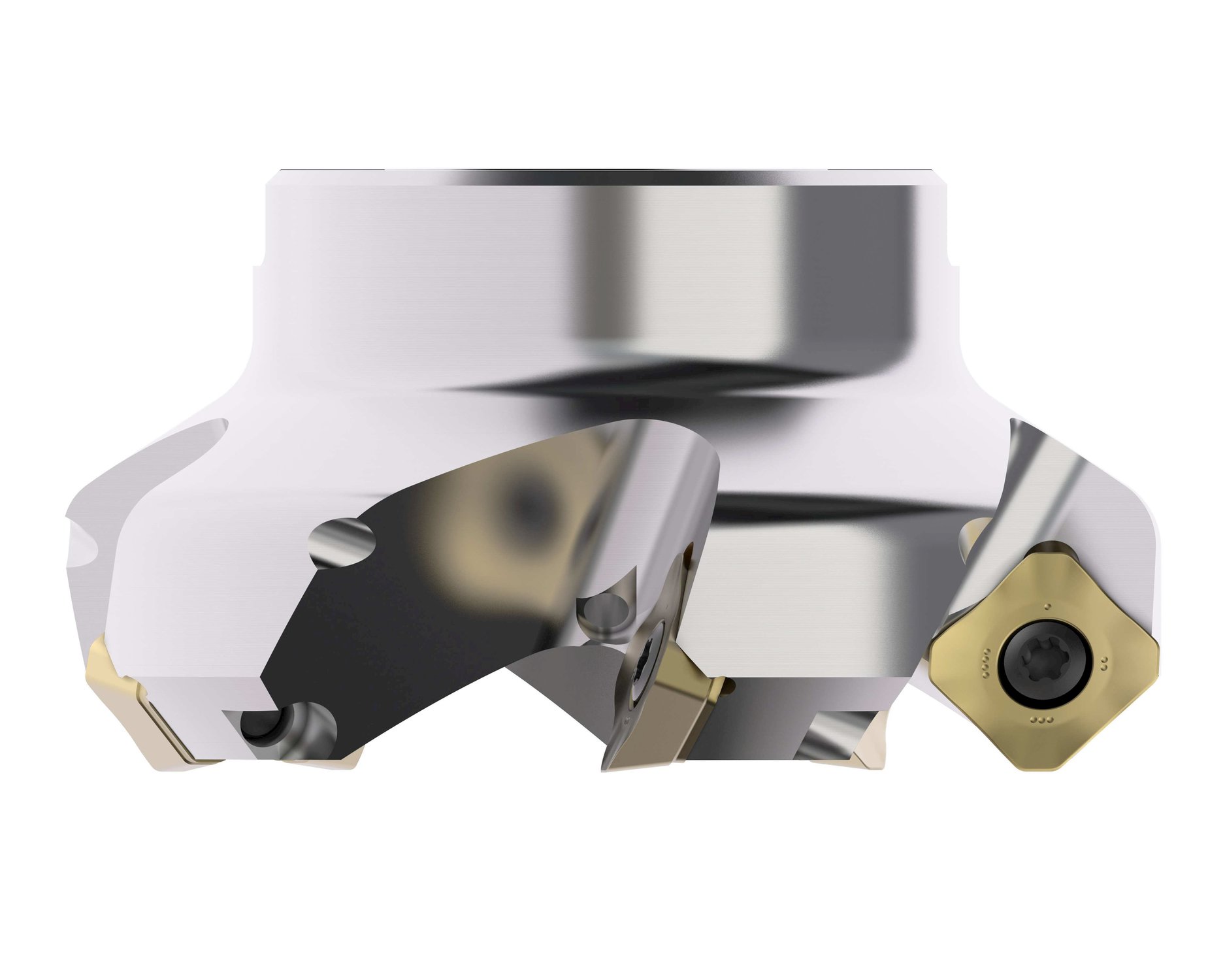
Quattromill™ is the ultimate general-purpose face mill, designed to excel in any application. Its exceptionally light cutting action makes it a problem-solver for diverse materials and setups, from small machines and weak setups to high-performance machining on robust equipment.
Quattromill™ delivers process reliability and stability, making it a safe and easy choice for general engineering tasks. The high helix angle minimizes notch wear, a common challenge when machining stainless steel and superalloys, including titanium. This design also promotes a smooth, peeling cut, effectively suppressing vibrations and harmonics.
Furthermore, Quattromill™ offers superb chip formation and evacuation, reducing the risk of chip scratches on the workpiece surface. This facilitates easier and faster cleaning of components and machines, while also minimizing chip volume thanks to the compact and consistent chip shapes produced across all materials.
Roughing and finishing in extremely unstable set ups
High productivity even in unstable and challenging set ups
Easy to use and reliable cutting action thanks to forgiving machining characteristic
Optimal chip control even in long chipping materials and big cutter diameters
Single sided square insert in 3 insert sizes 09, 12 and 15
Most light cutting face mill with low power consumption
45° lead angle can be also used for chamfering
Broad material coverage from SMGP-M-K-N-S-H
CBN and PCD insert options available
Go to the product
Unlike traditional double-sided insert systems, Double Quattromill™ excels by reducing cutting forces and machine power consumption, ensuring superior workpiece stability. The high helix angle of the inserts not only provides a free-cutting action but also extends tool life and increases versatility across a broader range of materials.
Available in two lead angle options, Double Quattromill™ offers optimized performance for different applications. The 48-degree version combines lower cutting forces, reduced power consumption, higher feed rates. The 71-degree version is ideal for milling at greater depths of cut, particularly when working close to walls or part fixtures. This lead angle is the perfect balance between conventional face mills and square shoulder mills in terms of cutting forces and depth of cut capabilities.
Two insert sizes further enhance the system's adaptability. The SN.X1407 insert is a cost-effective, general-purpose choice for small to medium-sized machines, delivering excellent performance in both weak and rigid setups. The SNMX2209 insert is designed for powerful machines and demanding, cost-efficient roughing operations. Both insert sizes feature thick cross-sections, enabling the system to handle high feed rates and depths of cut, even during extended machining times.
Economical face mill with large depth of cut capability (up to ap = 13 mm)
Double sided square insert in 2 insert sizes 14 and 22 with thick cross sections
Light cutting thanks to high positive helix angle especially for double sided solution
Cutter version .54 / SN.X….A is a conventional face mill approach with 48° lead angle
Cutter version .56 / SN.X….Z has a lead angle of 71° for higher depth of cut capabilities and less interference risk to side walls or fixturing
Internal coolant up to DC = 315 mm
Cassette cutter option available
Go to the product
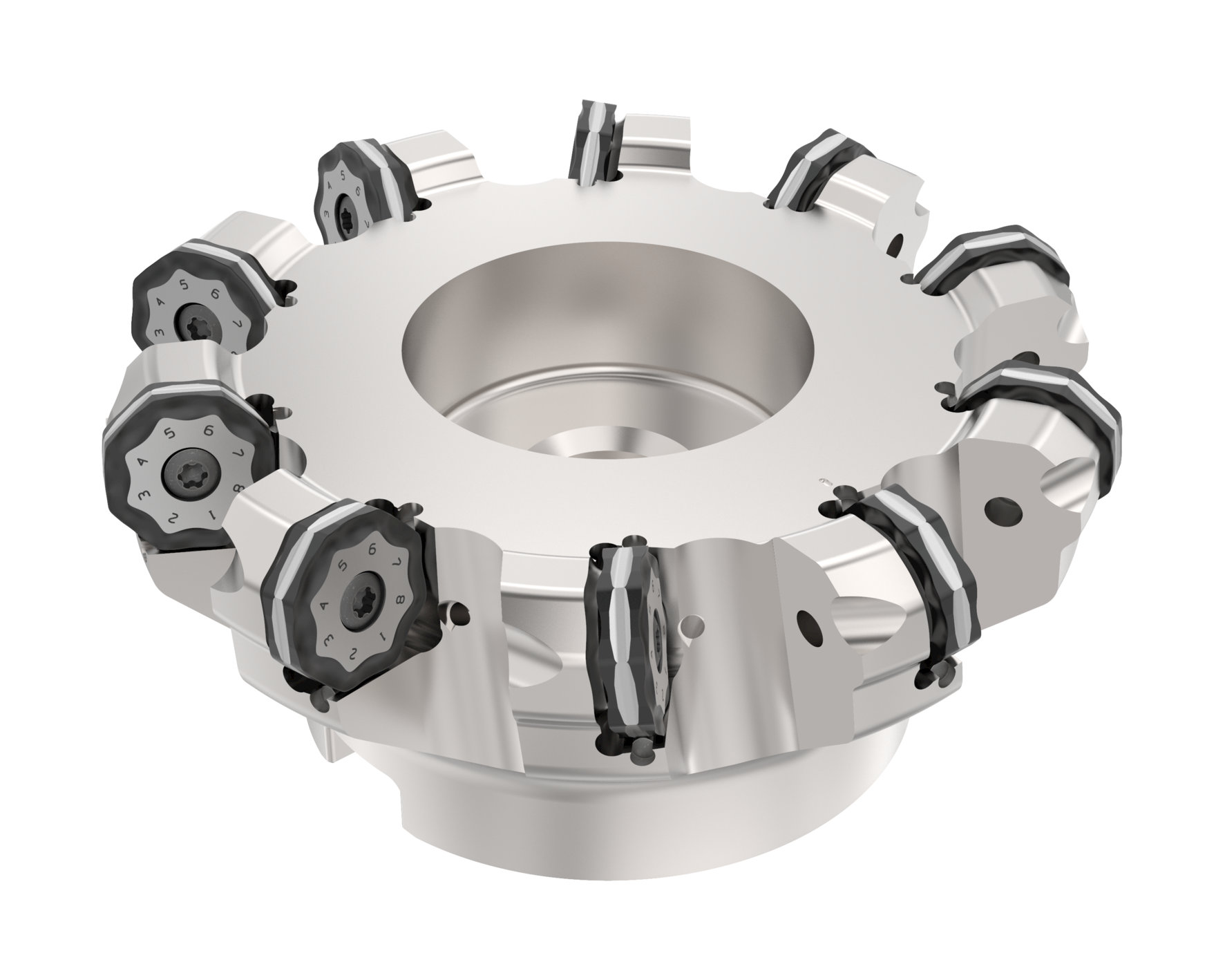
Double Octomill™ face milling cutters deliver exceptional economy thanks to 16 cutting edges per double-sided insert. This system seamlessly blends easy handling, robust performance, and cost-effective operation for both roughing and finishing. Originally designed for steel and cast iron, Double Octomill™ has expanded its capabilities with dedicated geometries and grades for ISO M and ISO S materials.
A patented cutter-insert interface, featuring hardened pins for precise insert seating and ground grooves on the insert, ensures easy and secure indexing, minimizes runout, and enhances system durability and robustness. These features are particularly crucial for mass production environments.
The Double Octomill™ family includes two insert sizes to address diverse machining needs. The ON.U0504 insert is perfect for smaller machines and less rigid setups, enabling smaller cutter diameters and depths of cut up to 3.0 mm. The ON.U09 insert, designed for more powerful machines and rigid setups, handles depths of cut up to 6.0 mm. Double Octomill™ provides tailored solutions for every challenge. Coarse-pitched cutters excel in weak setups and long-chipping materials, while super close-pitch wedge clamp cutters maximize performance in materials like cast iron.
Most economical face mill option with 16 cutting edges per insert
Double sided octagonal insert in 2 insert sizes 05 and 09
Broad cutter range including Capto and CAP back ends as well as left handed cutters
Comprehensive range of inserts to meet most challenges
Easiest insert handling and reliable positioning due to unique insert cutter interface
Go to the product
The .88 cutter family is a face milling cutter with square shoulder milling characteristics. The near 90° lead angle generate a high depth-of-cut capability and allows machining operations close to sidewalls of a workpiece or close to fixture clamping due to the reduced risk of interference. Common demands when machining cast iron components since the variable casting allowance cause undefined depth of cut conditions during the first cut.
Square shoulder or near 90° cutters are also often preferred on cast iron components because of side walls and fixturing being close to the required machined surfaces. The high lead angle generates less axial cutting forces in comparison to a common face of high feed milling system which is a great benefit in thin or axially weak supported workpieces.
The SNMU12/16 inserts offer economical eight cutting edges per insert and are made for robust cutting action that can occur when machining tough skins and sand inclusions. Beside cast iron the system can also be used with great performance in common steels. This system can be applied as a more cost-efficient alternative against dedicated square shoulder milling cutters with maximum 4 – 6 cutting edges per insert.
Near 90° concept offers high depth of cut and less interference risk to side walls or fixturing
Made for cast iron machining with variable and unforeseen stock variations
Double sided square insert in 2 insert sizes 12 and 16
Cost efficient alternative to dedicated square shoulder milling cutters thanks to 8 cutting edges
Robust insert options made for heavy cuts and challenging cutting conditions as inclusions
Go to the product
Discover more on Octomill 06