Reduce Vibrations in Roughing Unstable Setups with Octomill 06
Struggling with roughing in unstable setups? Octomill 06 delivers high performance, less vibration, and extended tool life – even on weaker machines
Seco’s Octomill 06 has a much higher positive helix angle in comparison to common OD-solutions (e.g., ODMT0504 or ODHT0605). This generates many benefits as:
The positive / negative instead of a positive / positive setting approach as well as thicker insert design compared to OF-solutions (e.g., OFMR0704 or OFET05T3) create a more stable cutting edge that can handle higher feed rates and challenging cutting conditions which might case cutting edge chipping.
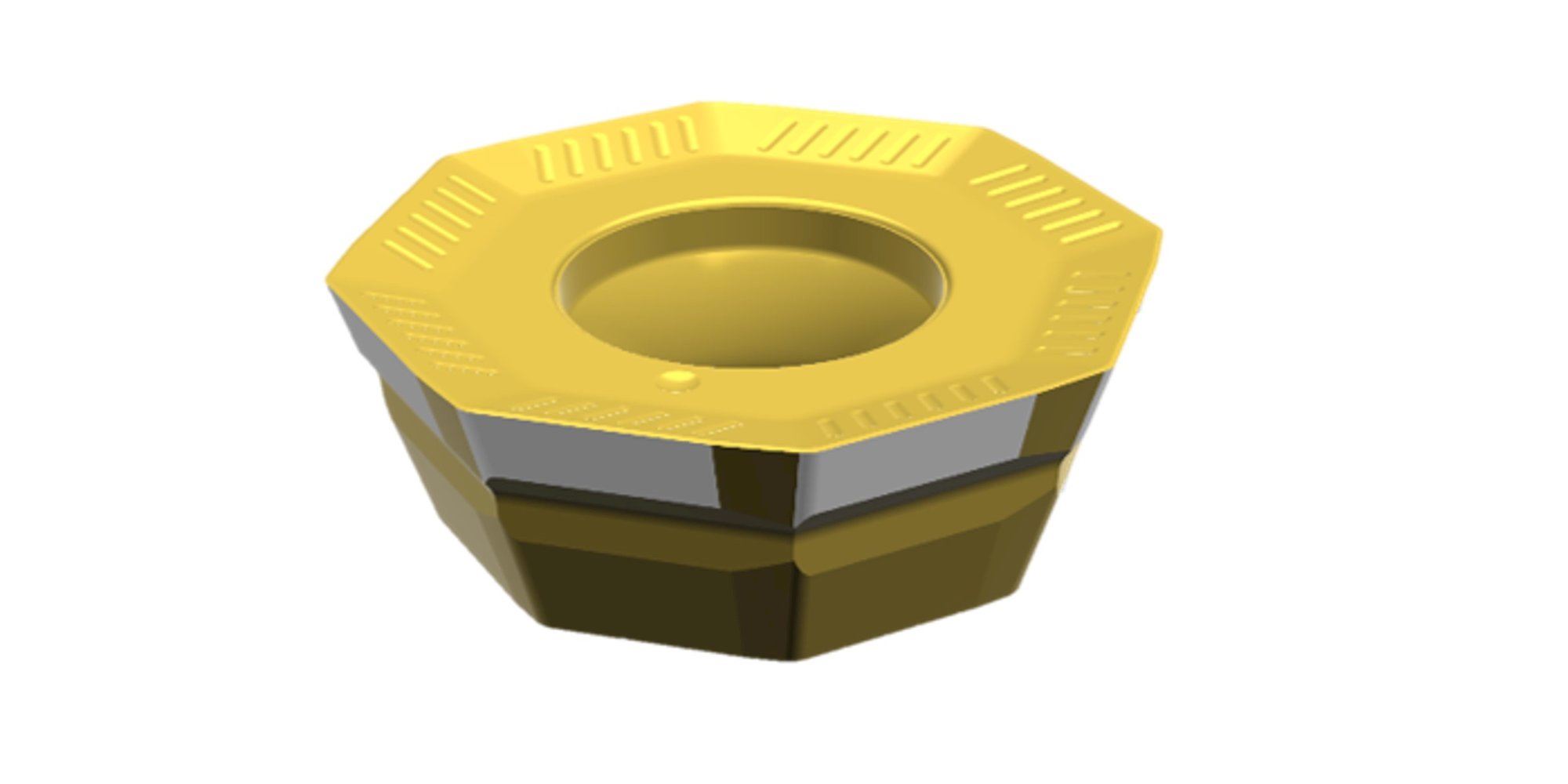
Conventional designs integrate a right and a left-handed wiper flat, which limits certain design aspects and machining characteristics. Seco’ new Octomill has a straight cutting edge design and a pure right-handed design. This enables a higher axial angle setting angle as well as an improved and more consistent chip formation already at low depth of cut. The straight edge line increases the edge strength and stability and leads to a more consistent wear pattern all along the cutting edge.
Common difficulty of cuter systems with octagonal inserts is the clearance to the workpiece on the minor cutting edge. Insufficient bottom clearance can lead to back cutting marks and effect the surface finish appearance. This can be especially seen on set ups that tent to bend back as thin walled or low supported workpieces. NG Octomill 06 has a clearance of 5° on the minor cutting edge in comparison to traditional lower clearances of just 2°. This extra clearance protects the minor edge from initial and undefined wear before being used as a main cutting edge. This design feature leads to better surface finish as well as higher process stability and tool life.
All these aspects support high performance roughing especially under unstable and challenging conditions.