Easy, fast and secure insert handling of Cutter-Insert Interface
The new generation of Seco’s face mill Octomill 06 offers easy, fast and secure insert handling especially for a single sided insert solution.
It mimics the cutter-insert interface design of Double Octomill and disconnects the cutting-edge from the support surface areas. This creates freedom in the design and leads to multiple benefits.
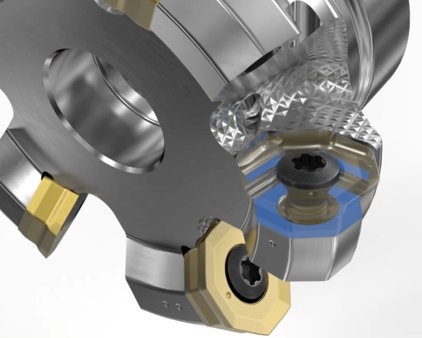
The cutter support surface has a quite flat angle of +5° in comparison to the high positive relief angle of +18° around the cutting edge.
This allows the face milling insert to more easily slip down into the pocket seat during indexing, reducing the risk of a gap in the bottom seating face.
The result: no faulty insert mounting and positioning.
The insert rests correctly in a defined and strong position in the pocket seat.
Leading to no insert movement, well aligned wiper flats and higher run out precision, all important aspects for a higher process stability and less workpiece rework or scrap.
Furthermore, handling of the face milling inserts is improved by compact outer proportions, an insert thickness of 5.56 mm (about 0.22 in) as well as the same large insert screw as the Double Octomill 09 - M5 with T20P. These dimensional aspects make the insert processing more comfortable. The insert screw length is chosen to enable the indexing of the insert within the pocket seat without being removed. This means less risk of losing a screw or insert during the processing especially in the machine or beside the machine.
Additionally, the indexing support surfaces stay intact when overrunning the tool wear down to the relief or even in case of edge breakage. The cutter-insert interface allows a higher utilization of cutting as well as less pocket seat damage when indexing onto a used cutting edge segment.
The interface acts as a defined limitation or breakage point to protect the cutter pocket seat in unfavorable conditions/situations. Leading to cost savings and again a higher process stability.